Aiming for end-to-end control at Opel/Vauxhall
Michael Scholl, Opel/Vauxhall’s director of supply chain, discusses parallel planning, in-plant logistics customisation and complexity with Automotive Logistics
When carmakers make changes, be it launching a new model, adding or shifting a supplier location, or selling in a new market, they reverberate across the supply chain, either as ripples or shockwaves that require their own logistics response. Whether it is new packaging to transport a small part, the redesign of a plant’s parts supermarkets, or even new suppliers altogether, such decisions rarely touch any part of the supply chain in isolation.
The best operations arise when OEMs plan far in advance, whether in cost modelling supplier decisions, or testing the delivery efficiency of part designs. It also helps when there is a strong, central supply chain function with responsibility from customer order input to meeting final delivery promises.
This ‘end-to-end’ focus, from model development through to outbound logistics, is precisely the remit of Opel/Vauxhall’s supply chain department, led since 2008 by director Michael Scholl, a 23-year General Motors veteran who has held various production, material and planning roles. His responsibilities run the gamut, including material and vehicle order management, production scheduling, packaging development, in-plant logistics, inbound and outbound logistics, and network planning, to name a few.
Supply chain is among the most cross-functional teams in GM’s organisation, working across manufacturing, engineering, product development, sales and purchasing. And while the carmaker has been pushing a ‘total enterprise cost’ approach to its sourcing and manufacturing for a decade, including consideration for capital costs like plant and supplier tooling and packaging, and expenses like material, customs and logistics, among others, Scholl says the process has been refined and strengthened over the last three years.
Read these other stories that form part of this exclusive coverage of Opel/Vauxhall's supply chain management:
In particular, advanced planning, or ‘frontloading’, in the supply chain has come more strongly to the fore. The supply chain team conducts more studies of manufacturing footprints, parts design and assembly and delivery concepts during the vehicle development phase. Important examples can be found for packaging design. “As soon as the first technical drawing of a part is available and quality, handling and ergonomic requirements are determined, we start with the packaging design using CAD technology for those parts requiring special racks and containers,” Scholl says. “We are focusing on large, bulky and difficult to transport parts, like fuel tanks, brake and fuel pipes, struts, etc.”
Opel/Vauxhall has also integrated its vehicle order management with production and material planning, helped by a suite of software solutions that consider material availability across an order pipeline that runs 11 months in advance (see 'order slotting' story). For the first time, Opel has brought together those who manage orders, material follow up and logistics, leading to a better understanding of potential supply bottlenecks, and how to react to them.
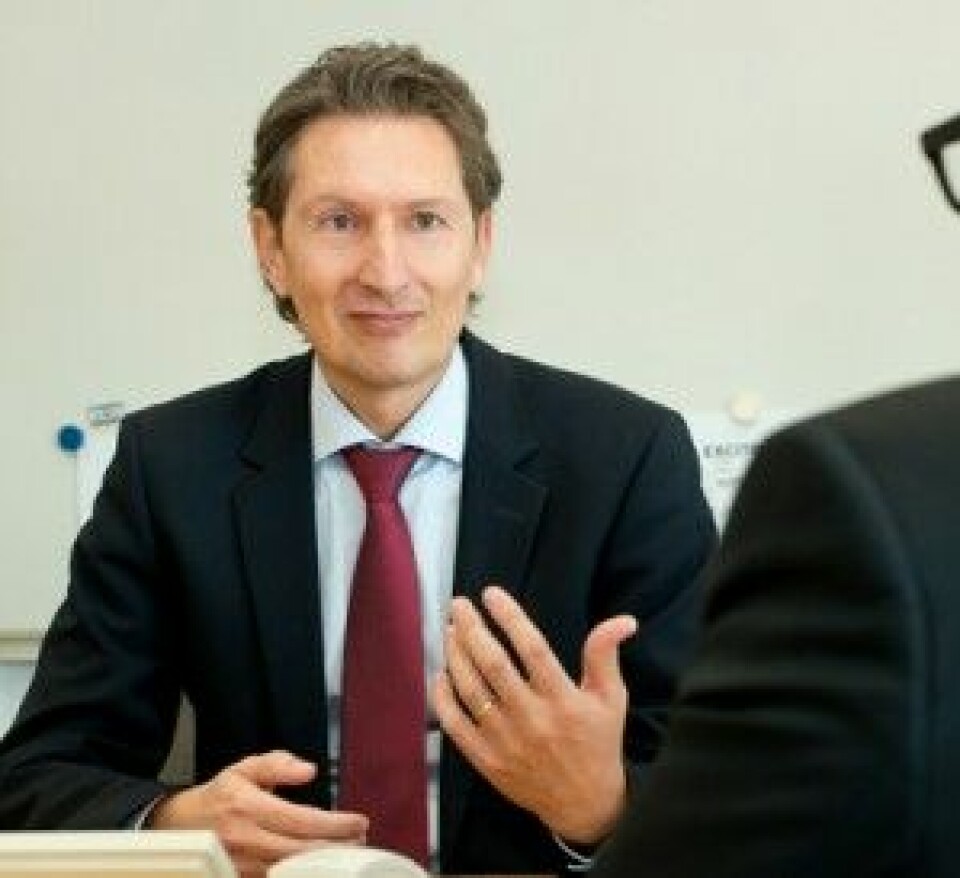
Scholl says that logistics considerations, as well as Opel’s active supply chain engineering, have helped shape the supply base, including more localisation. While he admits that there is no “one-size-fits all” supply chain, his department has more influence on manufacturing and supplier footprint decisions, including on keeping certain parts and products in Europe.
“We absolutely have more influence than we had in the past. The function has evolved from having an operational focus to a being a designer for a sustainable value chain,” he says. “Our role at GM has also developed from a function that executed decisions made by other functions to an even partner.”
Supply chain management will be even more important as Opel enters a period of great change. The carmaker will close a plant in Bochum, Germany this year which will cause supplier shifts as models are consolidated across other factories. At the same time, it will invest €4 billion ($5.5 billion) to fund 23 new models and 13 engine ranges, while sales of Chevrolet are set to end in west and central Europe by 2016. Complete supply chain consideration will be crucial to ensuring uninterrupted production and deliveries during this phase, as well as in helping to improve future costs.
Frontloading the supply chain
Ludwig: How far in advance does Opel plan supply chain operations?
"Scholl: We start very early in the vehicle development process, even prior to the final decision to begin a product programme. This can be 4-5 years before the start of production."
What are Opel’s biggest challenges for advanced planning?
"We need to ensure that the total enterprise cost (TEC) mindset is considered in all the decisions that we make. This requires that this way of working is institutionalised across the functions and not dependent on single individuals driving it."
Do you consider material handling in the vehicle development stage?
"Yes, indeed, we consider supply chain handling concepts and associated costs. When it comes to choosing the right delivery method, part proliferation and complexity are the main drivers, and can result in non-value-added activities like repacking or sequencing. Our frontloading activities are thus focused on reducing complexity at the early stage to avoid non-value add activities."
What role does supply chain play in determining production and sourcing locations for GM?
"We are an even partner in the decision-making process. Supply chain and logistics are operational considerations that can be expressed in cost. Bottom line, the decision needs to make sense from an enterprise perspective, with supply chain playing a major role. In this respect our costs can tip a decision for a certain manufacturing or supplier location in a certain direction."
Is there scope to localise more parts and tooling in Europe?
"Yes, localisation of suppliers is desirable from a supply chain perspective. The question is whether you can justify the potential investment required or higher labour cost with other reduced on-going expenses. In light of increased intercontinental logistics costs, double tooling and supplier localisation is a more and more attractive alternative."
How possible is it to shift supplier locations in a mature market like Europe without disrupting suppliers’ economies of scale?
"Where you would lose scale on a single part, you might counteract this by applying bundling strategies, where you give suppliers a broader scope of parts within a commodity, or the volume for the same parts for multiple products to generate scale. These are strategies in our toolbox, but they are not exclusive and not a rule. Every case is special. Beside obvious short-term benefits, it is more important than ever that GM and its suppliers are aligned. Alignment with business and cultural priorities is necessary to help GM and suppliers achieve scale and drive mutual growth and success. This alignment will also help to build strong, strategic, long-lasting relationships based on trust and transparency which will eventually drive better business performance for GM and its suppliers."
Designing the logistics network
Ludwig: How often do you engineer logistics networks?
"Scholl: The optimisation of our logistics network is a constant and multi-layered process. With every introduction of a new product, the overall network is re-assessed and optimised on a macro level. Every introduction of a new supplier location requires integration. We are optimising single routes as volume changes even on a weekly and daily basis. We are also taking a more strategic approach and challenging the variables of any given plant network from a TEC perspective for improvements across the network."
With the end of car production in Bochum, have you had to redesign network flows?
"Every change in the manufacturing or supplier footprint that impacts the volumes of material flows results in a redesign of the affected part of the network. This might lead to to new locations for consolidation facilities or changes in the direct, milkrun and crossdocking mix. These shifts are part of our strategic network analysis."

GM Europe now uses Gefco as a fourth party logistics provider. Is the network engineering and planning handled by Gefco rather than GM?
"Beside other tasks, Gefco plans and engineers the most efficient network for inbound and outbound transportation. Based on a bigger book of business, Gefco can generate significant volume leverage and optimisation for us. In combination with our in-house competence, this generates a powerful planning and cost management capability."
What would you point to as the big trends or changes that will shape the next phase of your network engineering?
"Beside the traditional factors of cost, speed and responsiveness, ‘green logistics’ will become more important. In this respect we are looking into extending our rail usage and intermodal traffic where it makes sense."
Looking to standard packaging
Ludwig: Have you been able to increase the use of returnable packaging in your plants?
"Scholl: The percentage of returnable packaging in our plants is historically very high and a key strategy. However, for certain parts and supplier locations, returnables cannot be justified from a cost perspective, as the length of the loop would require too high an investment and freight cost for empty returns. For that reason, a significant amount of overseas parts arrive with expendable packaging."

Have you made any improvements in standardising racking?
"The development of packaging is centralised and therefore racking is standardised across all plants if part dimensions and configurations allow it. Just as our vehicle engineers are working on de-proliferation of our products, the supply chain team is trying to de-proliferate our packaging portfolio.
Thus, we are reducing the use of special racks and replacing more and more with standard containers. Wherever special racks are still required, we try to re-use existing ones. Needless to say, we are working with a modular design that not only supports re-use but also allows us to optimise the utilisation of truck and container space."
Upstream and downstream links
Ludwig: Outside the order slotting project, are there gaps in creating buildable schedules based on the total supply chain?
"Scholl: With the order slotting capability we made a huge step forward. However, the transparency of supplier capacities is definitely an area where we still can improve."
Do you want more visibility in the lower tier pipeline?
"Our contact partners are tier ones. We expect them to manage their supply base as we do with them, except in very complex situations such as the Fukushima crisis in Japan or flooding in Thailand. If our tier one suppliers ask for support, we will get involved in managing the lower tiers."
Do you track the accuracy of your forecasted vehicle delivery dates?
"Delivery date reliability is a key cross-functional metric. Over the last few years we have implemented several initiatives, such as sequence stability in our processes. Order slotting is the most recent one and we will continue to focus on this subject as we are convinced it is important for customers to get vehicles when they were promised."
Does Opel optimise its build schedule by vehicle destination?
"Indeed, we are optimising our production schedules according to outbound needs. For example, we batch production of vehicles for certain markets or delivery destinations to support a quicker pick-up by carriers. In combination with our production sequence stability, this has positive effects on delivery time as well as on total cost since a reduction of tied-up capital is imaginable. This has significant potential, especially for markets with lower volume."

Managing the everyday supply chain
Ludwig: Are you facing any chronic material shortages?
"Scholl: We are not currently confronted with chronic bottlenecks such as during the Fukushima crisis, but there are always commodities that require full attention and priority, such as for high-demand products or those from financially stressed suppliers. To cope, GM has a global risk management organisation that aims to identify potential risks as early as possible before they hit operations, and to develop and implement solutions if a risk has materialised. As there is no perfect world, problems will happen. I can only ask for full transparency and early warnings if there is a potential risk. GM also supports the MMOG/LE (Materials Management Operations Guideline /Logistics Evaluation) initiative. We ask our suppliers to conduct this self-assessment to identify potential shortfalls within their internal processes."
How well is the logistics network able to respond to sudden changes?
"Logistics must be a multi-stage process that takes sudden changes into the equation and still optimises those impacts within any given set of variables. That might mean having more smart inventories as a part of a more tactical weekly and daily operating plan. We already have a high level of cube utilisation across transportation modes at all receiving areas, while we monitor the major consolidation facilities prior to shipment to allow for any necessary corrective measures."
How synchronised is Opel’s production with tier suppliers?
"Synchronisation of the value stream requires that you provide certain stability in your internal processes. Production sequence stability has the highest priority in our plants and is measured by different KPIs. Based on this stability, we have coupled several suppliers directly to our production programme, having them produce and deliver in line sequence.
This isn’t limited to suppliers adjacent to our plants, but includes remote suppliers, such as customised wiring harness suppliers in Romania delivering to German assembly plants. We encourage our suppliers to use this sequence stability to also synchronise their tier supplier base."
Finally, what changes do you see most affecting day-to-day operations?
"It will continue to be balancing flexibility for sales versus stability of schedules for the supply side. Managing this in light of a growing proliferation of product and parts will be the biggest challenge.
Even more important is to recognise that the supply chain function should manage its destiny by better driving the design of the value stream early in the process. All of this must occur under the umbrella of total enterprise cost, which requires transparency and the right mindset across the entire General Motors organisation."