Another second chance in Detroit
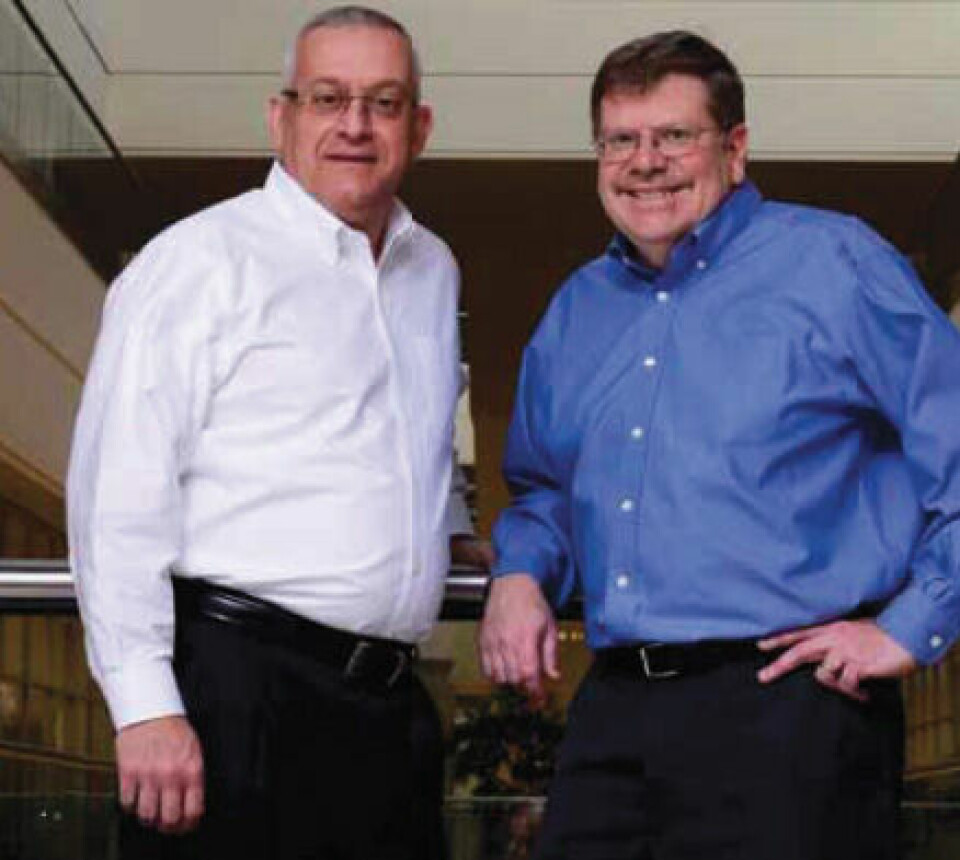
With fast growing volume in North America, and surprisingly strong exports, the Chrysler Group’s resurgence under Fiat’s control has been one of the industry’s best tales of turnaround. Efficient, global and combined vehicle logistics networks are helping to support Chrysler’s rise and help it grow globally, writes Anthony Coia
If you’re lucky enough to get a second chance, you need to make the most of it. Perhaps few organisations understand this better than the Chrysler Group, which, although it has probably had more than its share of fresh starts, is thriving as though its facing its last. With the dark days of the economic downturn now in its rear-view mirror, the Auburn Hills, Michigan-based Chrysler Group is driving its operations with a renewed speed and efficiency that has enabled it to become both lean and profitable. This turnaround has been helped in large part by the change in ownership control that continued when Fiat increased its share in Chrysler from 53.5% to 58.5% in January, thus meeting the final target set by the United States’ government following its bailout of the carmaker and agreement to grant Fiat control.
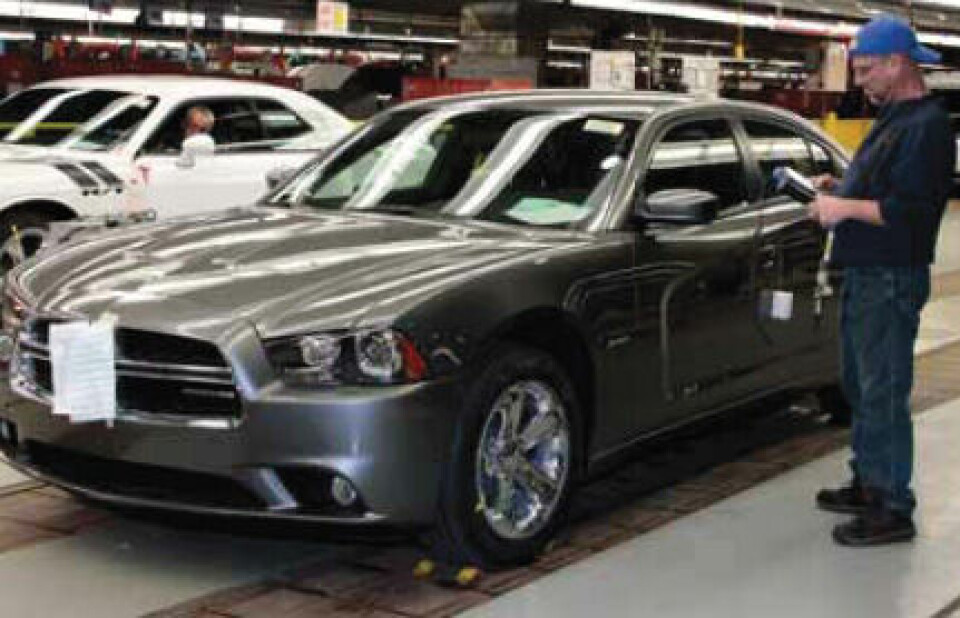
Last year, the Chrysler Group reported a profit of $183m– its first annual profit as an independent company since 1997– as sales in the US rose 26% compared to 2011. Exports more than doubled, albeit from a small base. With sales in the first two months of the year up 40%, Chrysler predicts revenue of $65 billion this year, which would be an increase of $10 billion compared to 2011. The company expects worldwide shipped vehicles to increase more than 20% to 2.4m vehicles in 2012. What is evident behind the numbers is that, at the new look Chrysler, logistics continues to play a vital role. Chrysler now shares its responsibilities for vehicle distribution with Fiat, thus establishing a network that takes advantage of the supply chain expertise and global networks of both carmakers. The results have been positive, particularly with Chrysler seeing strong growth in Europe well above a stagnant market. The carmakers are also making efforts to use common processes and systems, while adapting best practices from one another. For example, William Cook, head of worldwide logistics and customs at Chrysler, reveals that the carmaker now has plans to follow Fiat’s example in Italy and start operating its own, in-house fleet of car carriers. In future there could also be significant potential for shared tenders, for example to contract global ocean volumes. While such measures have yet to be put in place, Chrysler’s growth in both North America and around the world should provide more opportunities.
Expanding the distribution network
Cook credits part of Chrysler’s recent improvement in logistics to its organisational structure. Replicating what is in place at Fiat, the hierarchy of the Chrysler organisation is designed to give supply chain management a higher priority. The Supply Chain Management Group, of which Cook and his team are a part, is a relatively new industrial division that was created when Chrysler emerged from bankruptcy protection in June 2009. It is led by Michael Keegan, senior vice president of supply chain management, who reports directly to Sergio Marchionne, CEO of both Fiat and the Chrysler Group. While organisationally similar, a key overlap in the supply chain between Fiat and Chrysler currently is in finished vehicle logistics, with Chrysler responsible for distributing Fiat’s vehicles in North America and Fiat responsible for distributing Chrysler’s vehicles in Europe. It is a system that enables each company to take full advantage of its geographical expertise, sales and service networks. For example, among the benefits in Europe is that Fiat has been expanding vehicle logistics networks for Chrysler’s Jeep brand. Chrysler’s vehicle distribution operations are based mainly in the US and its logistics network is approximately 90% focused on North America. Its production network on the continent consists of ten vehicle assembly plants, with eight clustered around the upper Midwest and in Ontario, Canada. There are three in Michigan–Detroit, Warren, and Sterling Heights–two across the border at Brampton and Windsor, one in Belvidere, Illinois and two in Toledo, Ohio. Finally, there are two in Mexico at Saltillo and Toluca. Its logistics facilities consist of 51 rail ramps and 11 vehicle-mixing centres– primarily in the United States–for rail or truck transport. Rail carrier CSX manages the mixing centres, which handle multiple vehicle manufacturers.
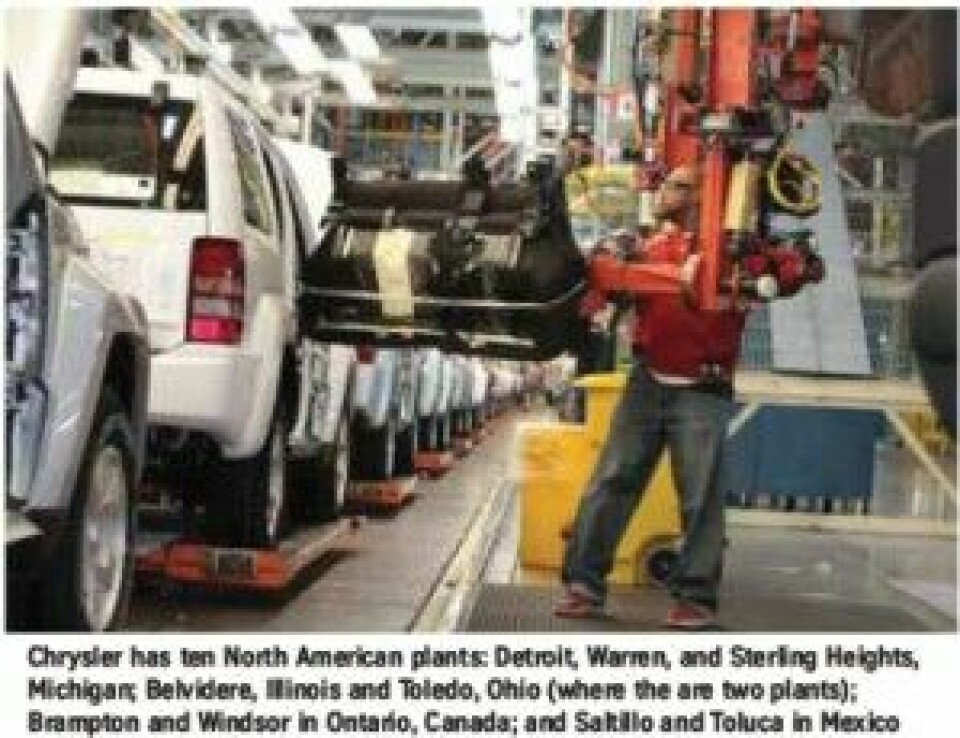
Export growth
Chrysler, always a North America-focused carmaker, has nevertheless seen a surge in exports from North America recently, particularly to Western Europe, China, Brazil, and other parts of South America. “Europe is our biggest market, but others are also growing, such as China,” says Cook. This growth has been evident in the volume Chrysler has sent through its primary ports of exit on the continent. Chrysler uses three main ports for its vehicle exports: Baltimore, Maryland; Gray’s Harbor, Washington; and Veracruz, Mexico, which account for approximately 80% of its North American exports, according to Steven Tripp, head of worldwide vehicle transportation. Beside these ports, Chrysler also ships from other North American gateways to a lesser extent, such as Jacksonville and Miami, Florida, and Lazaro Cardenas, located on Mexico’s Pacific Coast. While Fiat’s expansion plans for its brands in North America could eventually lead to more cross-shipping and imports from global Fiat production, it would seem as though the current alliance has–and will continue to–benefit Chrysler’s exports most. Export growth has outperformed most markets, even in the struggling European economy. Jeep sales in the EU and EFTA countries rose nearly 62% in 2011, for example, in a market that was otherwise flat. Tripp credits this growth in part to better distribution, including that of Fiat’s network in Europe and South America. Furthermore, Chrysler’s export growth to other emerging markets has also increased. “We are planning to grow to 2.4m units this year, which would be a 20% increase over 2011 in the number of shipped vehicles,” he says. Chrysler’s import network is still fairly limited in North America because of the carmaker’s continental focus. There are no imports into the US by sea, for example, notes Tripp, although Chrysler does import a small volume of Fiat vehicles from Europe into Mexico through the port of Veracruz (Fiat already had a presence in Mexico before the alliance and Chrysler took over finished vehicle distribution). The strong growth internationally has led to an increase in demand for export vehicle logistics services as well as to a reorganisation of Chrysler’s supply chain structure towards a more global enterprise. Since September, Chrysler’s organisation has been categorised into four geographic regions: NAFTA, EMEA (Europe, Middle East, and Africa), LATAM (Latin America), and APAC (Asia Pacific). To help facilitate its finished vehicle logistics efficiency, Cook says that Chrysler has a good relationship with customs; it provides benchmarking and is an early adopter of customs protocols. Outside of North America, Chrysler uses a number of destination ports worldwide for importing its vehicles, including Livorno, Italy–the largest Italian vehicle port and a major export gateway for Fiat. In South America, the port of Rio de Janeiro, Brazil serves Chrysler and Fiat. In China, Chrysler uses the port of Xingang (Tianjin), which is the largest port in northern China and the main maritime gateway to Beijing. It also uses the port of Shanghai on China’s central coast.
Find ways to collaborate
Among Chrysler’s main objectives is to reduce cost and improve its order-to-delivery cycle time for finished vehicles. In doing so, Chrysler evaluates its total supply chain by calculating the cost and cycle time elements of vehicle distribution, which includes how it might load together with competing carmakers. “A means of achieving [improvement] is through collaboration with other vehicle manufacturers, which involves co-loading on rail transportation and possibly truck transport,” says Cook. “We have already done a limited amount of co-loading successfully.” For truck co-loading of finished vehicles, Chrysler envisions greater opportunities, but there are currently a number of obstacles, according to Tripp. “We need to work out a structure that makes sense.
Due to the complexities involved, there is a lot of system work to do in our highly dynamic network,” he explains. Chrysler produces the Fiat 500 at its plant in Toluca, Mexico, which is located approximately 40 miles (65km) southwest of Mexico City. As well as taking advantage of free trade agreements within NAFTA, the Mexican production also benefits from a free trade agreement with Brazil. On the whole, Fiat distribution has fit very well into Chrysler’s operations. “Chrysler’s distribution of the Fiat 500 fits seamlessly with the rest of our network,” says Tripp. “The Fiat vehicles move on the same carriers and through the same distribution centres as our other vehicles.” The Toluca plant exports the Fiat 500 to the United States, Canada, Brazil and to China. Cook says that in North America, full integration is progressing well between Chrysler’s and Fiat’s vehicle networks. “The information technology infrastructure between Chrysler and Fiat still needs to be integrated,” he admits. But while more opportunity to gain logistics efficiencies may come through integrating vehicle distribution with Fiat (more than 200 Chrysler dealerships now also include Fiat studios), current Fiat volumes in the US are still small (fewer than 20,000 were sold in 2011). There may be more potential in benchmarking and adopting best practice and IT systems than in physically moving vehicles together. “We are benchmarking with Fiat in the area of information technology,” says Tripp.
“This involves evaluating combination and integration opportunities and looking at how Fiat controls its IT infrastructure.” Cook sees possibilities in a mutual exchange of best practices between both carmakers, as well as possible efficiencies in adopting common systems. “Our objective is to combine quality protocols and commonise processes from Chrysler and Fiat,” he says. He points out, for example, that Fiat has its own car carrier fleet in Europe–iFast Automotive Logistics–an approach that Chrysler thinks would also be a good idea for North America. Cook now reveals plans to start an in-house carrier in the US. “Chrysler is setting up a small haul-away company for vehicle transportation,” says Cook. “We plan to administer a pilot project during the second quarter of this year, and we expect to be operational by the end of the year,” reveals Cook. The trucking company would serve Chrysler in the upper Midwest, which is the manufacturer’s primary vehicle production base. While Chrysler does not say as much, it may well be making such a move to avoid the sort of disruption to its vehicle logistics that followed a strike last year by Allied, the largest carrier in the US. Chrysler now appears more interested to control its own destiny in this regard.
Ocean capacity–a move towards global tenders?
Chrysler manages its logistics at a high level. Cook says that the system is stable, but he is looking for ways to improve communication, something in which third party logistics providers (3PL) play a role. The 3PLs currently handle documentation and administer some operational control, while Chrysler relies on its freight forwarders and transport suppliers to provide its required capacity. “For information technology services such as tracking and tracing we use 3PLs, as well as for scheduling loads, ordering railcars, and operating the off-site yard,” says Tripp. Adds Cook, “Chrysler is looking for similar operating metrics throughout its finished vehicle logistics system. We want a better measure to keep track and manage order-todelivery stability from the plant to the destination country or dealership.” Tripp says that for Chrysler’s deep-sea shipments, it has increased capacity and vessel frequency. It has also added a new carrier to its Middle East trade. “However, we still need to do more,” he says. Cook agrees and sees further scope for working with Fiat on a global scale as a means to secure ocean capacity as well as to lower freight rates: “As our volumes increase, we are also experiencing growing demand for ocean carrier ro-ro capacity.” Although co-tendering with Fiat on ocean shipments could improve Chrysler’s logistics efficiency, the details are not yet in place. “Both Chrysler and Fiat have long-term contacts with their carriers, but we are still collaborating,” says Tripp. “We currently collaborate with Fiat on our use of ports and on vessel frequency and we will also collaborate on ocean shipping. However, at this point, it is not clear how that will work.”
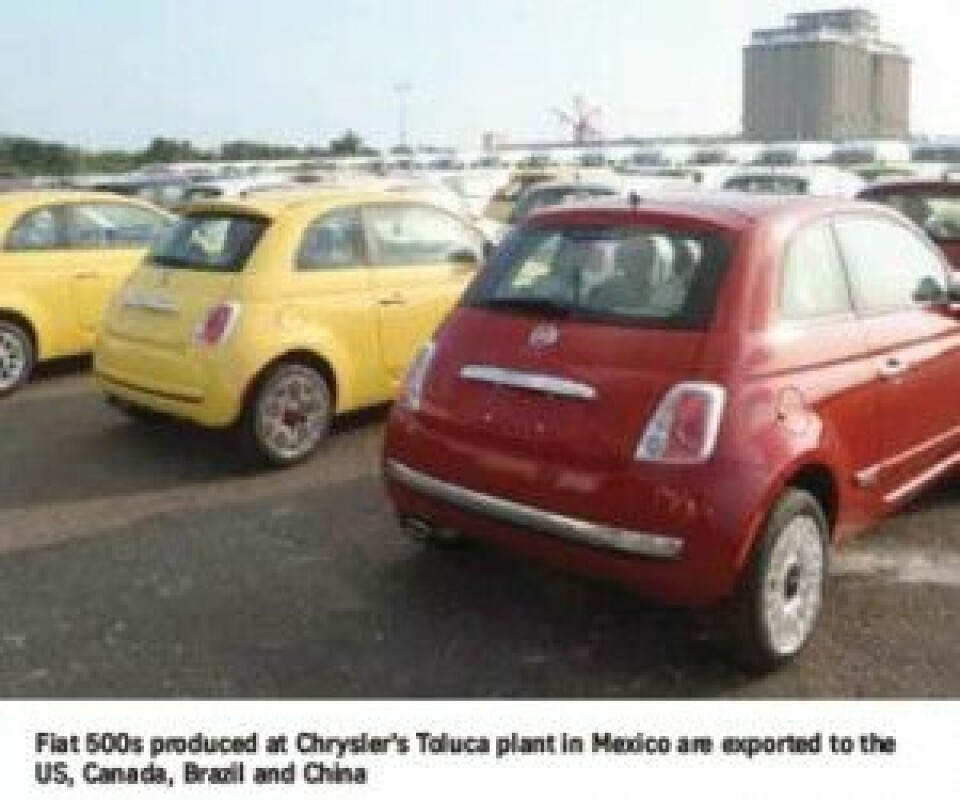
Rail wagon shortages
Regarding inland transport, rail is the dominant transport mode for moving finished vehicles between the United States and Mexico. Tripp says that the supply of tri-level wagons (known as railcars in North America) is Chrysler’s single greatest concern for vehicle logistics at this time as the industry is experiencing a shortage of the equipment. “Although plans are in place to build more railcars, not enough are on schedule for production this year and almost none will be built until late in the year,” Tripp says. In the interim, Chrysler and many other carmakers often have no option other than to ship on bi-level wagons, which is wasteful because it uses a greater number of wagons to ship the same number of vehicles. Because of this inefficiency, it is also more costly to transport vehicles by rail and the situation leads to bi-level shortages as well. “We are very concerned that the railcar shortage will be a constraint on our ability to keep up with the demand for our vehicles in NAFTA region and around the world,” says Tripp. “Almost all of our export vehicles move by rail to the ports of exit and we need railcars to move them to these ports. “In addition, the tri-level railcar fleet is very old and some of those cars probably need to be withdrawn from circulation soon,” continues Tripp. “Unfortunately, the railroad industry has not invested sufficiently in this equipment to support volumes planned for this year and the coming years.”
Doing well on the road
For truck transport, gaining more accurate forecasting is the main issue for Chrysler in making its finished vehicle network run faster and smoother. The goal is to provide Chrysler’s car carriers with more pipeline visibility of what vehicles are coming to them so that they can plan their equipment appropriately. But Chrysler is, on the whole, reasonably satisfied with its truck network. While at various times in 2010 and early 2011 there were concerns about truck capacity and availability, Chrysler is no longer as concerned about an impending lack of capacity, despite its interest in pursuing its own fleet. “We believe the trucking industry is doing a good job of adding capacity to support our increasing volumes,” comments Tripp. Tripp also says that recent regulatory changes regarding truck transport have not affected Chrysler’s logistics efficiency at this point.
The Federal Motor Carrier Safety Administration, a division of the US Department of Transportation, recently issued an updated Hours of Service of Drivers, which became effective in late February. The latest regulations reduce the maximum number of hours that a truck driver can work within a week from 82 to 70 hours. This reduction will require scheduling changes within trucking companies, increased labour requirements and other adjustments. How–or whether–these new regulations will impact on the wider automotive industry and Chrysler’s truck transport network is not yet known. In reality, some of the regulations appear to be helping the company track elements of performance. Cook says that new reporting changes issued by the Compliance, Safety, and Accountability (CSA) programme have provided Chrysler with a more comprehensive tool with which to measure carrier safety. “We track our carriers’ safety performance using these new measures and work with [them] to encourage them to improve their performance in these areas,” he says. Another area of concern for Chrysler, as well as other vehicle manufacturers, is the increasing cost of fuel. “Rising fuel prices translate rather quickly to increased freight costs. We have fuel surcharge programmes for all transport modes, through which these costs are passed on to Chrysler,” says Cook. As it looks at possible collaboration opportunities with Fiat, Chrysler has made its own gains in finished vehicle logistics efficiency. Among its improvements has been the order management cycle, according to Cook. He says that the Supply Chain Management division balances production and inventory with product at its dealerships. “We are not pushing inventory out,” he says.
Another of Chrysler’s recent gains in logistics efficiency is in damage reduction. “Damage has dropped by 10% within the past year,” says Tripp. He credits this to communication with its carriers and to obtaining feedback from them, which has been essential to do quickly. The company is also working with a third party provider to handle claims and insurance. Last year, Chrysler established an on-site repair shop at one location in Detroit, which helped to minimise the movement of vehicles and reduce the number of handling transfers. This concept is being expanded, according to Tripp.
As part of its overall logistics system, Chrysler’s World Class Manufacturing (WCM) is a common manufacturing operating system originating from Fiat. The WCM philosophy for how a plant is organised and how its employees approach their jobs is geared toward maximising productivity and minimising waste. This process was also integral to Fiat’s turnaround strategy several years ago. According to Cook, the principles of WCM are now being spread from inbound logistics to outbound. “As part of WCM, we are looking at inbound logistics. WCM looks at everything. First, it focused on the logistics process inside the plant and then on supplies to the plant. Now there is more focus on outbound logistics, for which we are administering a pilot programme.”
With the US economy appearing to be moving forward more decisively, Chrysler and its logistics providers have reason to be optimistic for continued volume increases. Emerging markets are shaping up as even stronger growth opportunities for Chrysler and Fiat. Although challenges are still evident–such as the rising cost of fuel, the European economy, the need for greater transport capacity in some areas and the need for deeper integration with Fiat–the prospects are overwhelmingly encouraging.