Arriving at the moment of truth in North America
After years of anticipation about growth in North American production and potential logistics bottlenecks in Mexico, this is the year when hopes – and possibly fears – will become reality.
Since the end of 2013, when Nissan opened a $2 billion plant in Aguascalientes, both Mazda and Honda have also gone live with new plants in Mexico, fuelling a long-expected boom in North American production. Other carmakers expanding capacity include the Volkswagen Group at its existing plant in Puebla and with the development of a new factory for Audi slated for 2016.
Production of light vehicles in Mexico last year hit a record 2.93m units, of which 2.42m were exported (1.7m to the US). Production is expected to grow to 4m units in the coming years. Mexico is not the only market in the region that is growing. Although the year got off to a slow start, with some economists blaming poor weather for flat sales in January and February, analysts and industry participants are still expecting US light vehicle sales to approach 16m units in 2014, with sales for Canada and Mexico adding another 2.8m or so. Carmakers are planning launch campaigns that will see a record number of new models entering the market.
“Aided by moderating fuel prices, demand for pickup trucks and sport utility vehicles has gained momentum. The growth rate of the automotive industry has outpaced that of the overall [US] economy,” notes Linda Brandl, vice-president and general manager for automotive at Union Pacific Railroad.
Carmakers are busy re-organising their outbound logistics networks to meet the market’s changing needs. At Honda, for example, the new plant will mean only around 2% of the brand’s sales in North America are met by imports. Mercedes-Benz, which will begin production of the C-Class sedan this September at its factory in Vance, Alabama, is also expecting to see fewer imports – although exports are expected to rise above the 150,000 that the plant already ships. Mercedes is also rumoured to be planning to build vehicles in Mexico with Nissan, although this is yet to be confirmed.
With exports from the US and Mexico on the rise, OEMs are upgrading yard facilities and seeking new transport flows. Shipping lines and port operators are looking at increasing services at sea as well as introducing new terminal locations. North American railways are investing heavily in equipment and infrastructure.
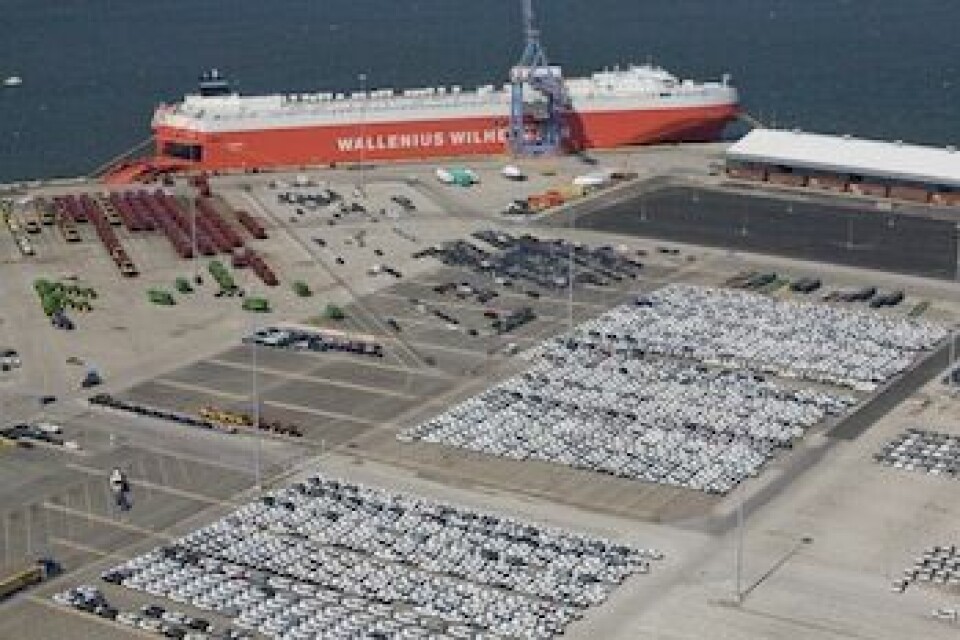
At the same time, industry experts say that logistics capacity constraints are likely to become more prevalent, including shortages of trucks, rail wagons and railhead capacity. Short-sea shipping, although used by a variety of carmakers in the region, could indeed become a more viable option for transporting vehicles and high-and-heavy equipment between the US and Mexico. However, such routes largely remain spot services or stops on longer, trans-continental routes, rather than specific point-to-point ‘shuttles’. That could mean carmakers won’t see the frequency or capacity at sea in anywhere the scale they will for rail.
With this churn in the North American market, there is also a growing interest among OEMs in better integrating services. American Honda has copied its yard management and IT systems from the US to Mexico, for example. Likewise, the Volkswagen Group is studying how it might better coordinate vehicle and material flows across its existing and future production in the US and Mexico, as well as for imports and exports.
Honda’s export plan goes into action
This time last year in Finished Vehicle Logistics, American Honda unveiled its combined rail and short-sea export logistics strategy from Mexico to the US. Now the plan has come into effect with the start of production at Honda’s 200,000-unit plant in Celaya, central Mexico. According to Dennis Manns, vice-president of sales and logistics planning at American Honda, the Celaya plant will ship 80% of its production to the US and Canada and a small amount to Europe and South America. With this plant, 98% of Honda’s North American sales will be produced on the continent – up from 85% just a few years ago.

Honda has been readjusting its logistics network with the start of Celaya production and the decline in Asian imports. From Mexico, Honda ships one-third of exports from Celaya by short sea from the port of Lázaro Cárdenas to San Diego and Richmond, California and Portland, Oregon; another third moves by short sea from the port of Veracruz to Brunswick, Georgia; Baltimore, Maryland; and Davisville, Rhode Island. The rest goes by rail through Texas.
Manns adds that all units from Honda’s existing plant in Guadalajara move by rail, although it may consider short sea. “The railcar supply in Mexico is the biggest question at this point,” he states.
The Celaya plant has dual railway access – Ferromex (FXE), on the plant’s north end, crosses the US-Mexico border through Eagle Pass, where it connects to Burlington Santa Fe (BNSF); Kansas City Southern de Mexico (KCSM), on the plant’s south end, enters the US through Laredo and connects to the railway’s American sister, KCS.
Manns says that Honda’s Mexican logistics system is completely integrated with the US. “We brought our operations system from the US and duplicated it in Mexico,” he says. “Within the past 12 to 18 months, track and trace has improved, including more accurate estimated arrival times.”
Short-sea interest
Honda is not alone in its decision to add short-sea shipping into its export mix from Mexico. Indeed, with shipping lines adding more services between the US and Mexico, it may well have spurred on an accelerating trend (although rail is set to remain the dominant mode for Mexican exports to the north).
Richard Heintzelman, executive vice-president and head of commercial at Wallenius Wilhelmsen Logistics Americas, says that given the uncertainty of rail capacity to meet vehicle production volumes in Mexico, WWL has enhanced its ocean services from Mexico, as well as US Gulf ports. Last year, the company expanded its Mexico-US service by adding calls from Veracruz and Altamira to Galveston, Texas; Jacksonville, Florida; Brunswick; and Baltimore. Additionally, these services provide connectivity to not only the USA from Mexico, but link WWL’s global ocean network as well to this important sourcing location
Stan Gabara, executive vice-president of Pasha Automotive Services, agrees that concerns over future rail capacity have made short sea more of an alternative. He estimates that about 5% of Mexico’s vehicle production currently moves by short sea to the US, but predicts that this share will increase to as much as 10% by 2016.
For the past ten months, Pasha and Siem Car Carriers have been handling shipments for General Motors at the ports of Lázaro Cárdenas and Grays Harbour, Washington. Siem calls at Lázaro Cárdenas, San Diego, and Grays Harbour before departing for Asia. Gabara says that Pasha has reduced its transit time from Mexico, with a lead time of five-and-a-half days from plant to the port of San Diego and eight days to Grays Harbour.
"[Reloading AutoMax wagons for southbound return journeys] optimises asset utilisation and minimises empty miles on the units. It also enables KCS to move more vehicles with fewer assets" - Kelley Anderson, Kansas City Southern
Pasha is also developing a new port facility at Port Manatee, Florida, located near Tampa Bay, which will have a sailing time of just two-and-half days from Veracruz, as well as four days to Jacksonville and six days to Baltimore. It will have a two-berth capacity for US exports to Mexico and Central America. The port will have on-dock rail capacity from CSX as well as storage and blocking outside of the terminal. Gabara says operations in Port Manatee should be running by the third quarter.
Terminal operator Amports has also announced plans to develop a vehicle terminal at the port of Tampa, which is expected to start operations this year.
Export flows
Gabara adds that Pasha is experiencing strong growth in the export of US-produced vehicles. The company currently operates at the ports of Grays Harbour, San Diego, and Baltimore. Its shipments include 90,000 Chrysler units from Grays Harbour to markets including China, South Korea, and Russia.
Mercedes-Benz exports some vehicles from its plant in Vance to Mexico. “We used to ship our vehicles by rail and truck to Mexico. Within the past two years, we began using short sea from Brunswick to Veracruz for our ‘M’ and ‘GL’ series,” reveals James Kasamis, manager for national import and domestic logistics at Mercedes-Benz USA. “All vehicles move by short sea because of improved logistics efficiency, cost savings, and it frees up rail capacity within the US.”

Along with vehicles, there has also been a reasonable trade in high-and-heavy equipment between the US and Mexico, including most of the cargo that K Line America moves from Galveston to Veracruz, for example. Butch Crane, assistant vice-president for the company’s North America car carrier division, says its volumes have been growing at the ports of Veracruz, Jacksonville, and Brunswick, as well as the west coast. He adds, however, that the Mexico to US trade is a spot market. “We are a deep-sea carrier and not designed for short-sea due to environmental restrictions,” he says. “However, there is interest in supplementing our business with short-sea services,” he says.
While sea transport may gain volume for exports out of Mexico, as well as for more US exports, the North American railway industry is investing heavily to make sure it meets demands for automotive production.
Among the cross-border rail carriers, Union Pacific Railroad offers direct access to Mexico’s six major rail gateways: Calexico, Nogales, El Paso, Eagle Pass, Laredo and Brownsville, where it interchanges with Mexico’s two largest railroads, FXE and KCSM. For example, Union Pacific’s new intermodal service between Laredo and Memphis, Tennessee, connects vehicle manufacturers in the southeastern United States and Mexico, says Brandl.

Union Pacific plans capital investments of $3.9 billion in 2014, according to Brandl, who says that continued investment in freight wagon rebuilds and new AutoFlex wagons will provide capacity to handle the projected sales growth. AutoFlex is a 90ft (27.5-metre) long convertible multilevel wagon that is adjustable to accommodate bi-level or tri-level vehicle transport using the same rack structure. In 2012 and 2013, Union Pacific added 600 AutoFlex wagons to its fleet.
According to Kelley Anderson, vice-president of sales and marketing for automotive, KCS’s strongest demand for finished vehicle logistics services is coming from the Celaya area, where Honda’s new plant is located. KCS continues to focus its efforts on balanced programmes for finished vehicles shipped in AutoMax equipment – another longer and adjustable wagon – to and from Lázaro Cárdenas. These wagons carry northbound shipments to domestic destinations in Mexico where they unload before being repositioned to another loading point within Mexico and reloaded southbound to Lázaro Cárdenas.
“This optimises asset utilisation and minimises empty miles on the units. It also enables KCS to move more vehicles with fewer assets,” says Anderson. “The Honda and Mazda facilities will both ship southbound to Lázáro Cardenas, providing another point that balances the southbound flow of vehicle shipments with the northbound ones.”
KCS is also investing in capacity expansion projects, such as a line of road infrastructure upgrades along its international corridor and the Caltzontzin district, north of Lázaro Cárdenas. This includes a new 10,000ft siding at Cranell, Texas, centralised traffic control on the Laredo and Brownsville subdivisions, and siding extensions on the Beaumont subdivision and the Tula and Caltzontzin districts. “We are also focusing on border operations, including a secure border initiative to improve velocity, as well as additional multi-level cars to support on-going growth,” says Anderson.
He adds that KCS is seeing difficulties in improving switching capacity at Sanchez yard in northern Mexico. There is also a lack of capacity on the international corridor between Laredo, Texas and Shreveport, Louisiana.
While there is considerable investment in Mexican rail, a current unknown in the sector is a reform bill that has already passed the country’s lower house of Congress in February. The bill would open up Mexico’s rail freight sector to investment and competition beyond Ferromex and KSC de Mexico, which currently hold exclusive concessions. Lawmakers in Mexico say the country’s infrastructure would benefit from increased investment and interconnections by rail, while costs would likely be lower.
Ferromex and KSC have publically denounced the bill, citing that their contracts contain exclusivity clauses for another 14 years. The bill would still need to be approved by Mexico’s Senate, but both railways have indicated that they would consider legal action to quash the bill.

One of the most significant manufacturers and exporters from Mexico is the Volkswagen Group, which has been ahead of the game in terms of mixed modal distribution to the US. Logistics director Roman Müller says the carmaker currently sends about 45% of US-bound vehicles by short sea and 55% by rail; for Canada, it expects to move all volume by rail.
Mexico is a global export hub for Volkswagen. From the port of Veracruz, it exports to Europe, the US, and South America, and from Acapulco it ships to China, Japan, South Korea, and Australia. Müller anticipates exports of nearly 419,000 units this year, of which 40% will move by rail to the US and Canada, and 60% by sea to the US, Europe, Asia and Latin America. Müller says that within the past year, the OEM’s biggest export growth from Mexico has actually been to Europe.
Volkswagen Mexico also imports vehicles from Spain, Brazil, Argentina, and India. From Europe, all of its imports arrive through the port of Veracruz. Domestic distribution within Mexico is by truck, says Müller. Around 15% of its imports move directly from Veracruz to the dealership, while most of the rest move via Volkswagen’s plant in Puebla where they are combined with domestic production for dealer delivery.
Volkswagen has recently expanded Puebla with new central yard operations.
“Last year, we increased our use of rail to the port of Veracruz from 20% to 40%,” Müller says. “The biggest challenge has been the existing infrastructure, but by working with the government and the port, we achieved this goal. Overall, we reduced our logistics costs significantly.” Müller adds that the company has also improved cost and performance with a new IT system, which allows Volkswagen to adjust its route planning every day. With the help of the system, the carmaker plans to increase its truckload factor, which will contribute to a goal of decreasing its CO2 emissions in logistics by 25% by 2018.
Capacity strains
The growth of vehicle production in North America has put more pressure on logistics resources in other areas too. Although Mercedes-Benz is not currently building any passenger cars in Mexico, for example, Kasamis says increased production in the country impacts it indirectly because the carmaker relies on the same rail wagon pool as other carmakers.
He also notes that the car haulier driver shortage is worsening in the US, with the average age of drivers now around 55 years. The latest federal Hours of Service Regulations, which went into effect last summer, have also impacted capacity. The law requires drivers to have more down time than previously, thus creating the need for more drivers as well as the realignment of delivery schedules.
Manufacturers and logistics providers are looking at ways to stretch their available capacity. Mercedes-Benz favours expanding after-hours deliveries at dealerships. “As we try to persuade our dealerships to expand their hours of operation, we are experiencing some positive results,” says Kasamis. “Most of them have after-hours delivery and inspection, and some have 24-hour drop-off access within gated areas.”
Sharing pipeline plans with truck and rail providers to help improve their load building and scheduling is also important, notes Kasamis. For example, even if the trucker knows generally when the train will arrive, if he picks up only two or three cars, he would still have to wait for the next train, leading to delays in delivery.
It helps when carriers have good IT systems, Kasamis says. making a distinction between companies that own their own fleets and can control the standard of systems, and owner-operators, which are less likely to have advanced systems.
Mercedes-Benz has made a number of other changes to improve its logistics efficiency, including ro-ro contracts that now last for five years and provide incentives for arrival at particular ports by certain dates.
"Most of [our dealerships] have after-hours delivery and inspection, and some have 24-hour drop-off access within gated areas" - James Kasamis, Mercedes-Benz USA
Elsewhere, Pasha recently began providing accessorisation for logistics provider Glovis America and its customer, Hyundai, in San Diego. Previously, Glovis had been shipping vehicles by rail from San Diego to Alliance, Texas for accessorisation. Now, Pasha provides this service before moving vehicles by rail to Texas, Oklahoma and New Mexico. By grouping the vehicles geographically, it improves velocity to the dealerships. Stan Gabara says Glovis is able to gain greater quality control because all processing occurs at the first point of rest. To improve efficiency at the port of San Diego, Pasha is expanding its terminal capacity, while at Grays Harbour, Pasha and the port have invested $28m in infrastructure improvements.
The North American production landscape continues to develop. There is expansion particularly in Mexico, but rising output and exports from the US are also impacting logistics. The challenge is to create a timely and balanced flow of vehicles within a growing, but still limited outbound network. Further changes are likely, whether it’s more short-sea shipping routes, rail corridors or port entry and exit points.
There are uncertainties ahead – such as whether the current blip in sales is truly the fault of weather or another sign of economic weakness – but with aggressive production plans and new model launches, the next few years will be crucial for North American vehicle logistics.
Additional reporting by Christopher Ludwig.