BMW Group: Thinking big about outbound
Alongside pictures of her family, Anita Pieper’s office is full of visual charts and signposts: value-stream maps, PDA circles for scheduling and a 3PS board outlining various projects and targets her teams are working on, from quality statistics to network studies or a plant launch years ahead.
In the middle of the board is a simple circle surrounding the most important task for the week. It could be a system audit, a financial target, a tender deadline. The signs help Pieper focus, she says, with a view of both the ‘important’ and the ‘urgent’ across multiple timelines.
“I like to have these boards for structure. They remind me what my team is doing, as well as [highlighting] our targets. What are the big things to improve? Where are we in a timeline of progress? What’s the next thing to do?”
[in_this_story align="right" border="yes"]Although she has been working at BMW’s global headquarters in Munich leading the carmaker’s global vehicle distribution since last September, the boards are the same Pieper used when she led logistics and the production system at BMW’s massive Steyr engine plant in Austria. They are also similar to tools from other plant and material logistics roles she has held across the automotive and other sectors, including at drive and automation specialist Bosch Rexroth, Terex Cranes and earlier at several German plants for Ford.
The tasks on display for outbound may differ from those of a plant but the management processes are the same, she says. Both plants and vehicle logistics require careful monitoring and data collection, even if such visibility in the outbound supply chain has typically been less precise; plants and vehicle logistics also follow processes across different working areas, all of them highly connected and interdependent.
Pieper wants to bring more of the discipline and structure of a plant into outbound logistics, but that does not necessarily mean introducing 45-second takt times per handling or 15-minute delivery windows (although there is room to make outbound delivery more robust, she says). Rather, her emphasis is on process stability, data analysis and continuous improvement. From her plant days, Pieper has also learned the importance of empowering employees, and has thus created various project groups with team leaders to concentrate on network improvements and technology adaptation.
Pieper is new to outbound but her varied background does not let her see it as an isolated business once assembly line workers hand over vehicles to the plant dispatch area – the so-called ‘F2’ in BMW parlance, the official point at which vehicle logistics takes responsibility. Rather, she emphasises links between earlier stages in production and inbound logistics, as well as product planning and engineering.
[sta_anchor id="1"]“Outbound logistics is always something special, but part of our task is to link it with other processes,” she says. “That includes the fact that the plant needs to provide us with a stable ‘F2’ so that I can follow through with seamless delivery. But in outbound logistics, we also need stronger data and knowledge of other parts of the chain.”
Pieper points to inbound planning logistics’ close involvement with future models, including establishing supplier quality standards, delivery processes and packaging years before a launch, information that she says can also be valuable for outbound logistics. For example, finished vehicles require various interior or exterior protection, while vehicle dimensions need to be considered for outbound equipment.
“If I don’t get such information in the right time, then we may fail to budget accordingly in a vehicle launch for the protection or equipment that we need,” she says.
[sta_anchor id="2"]Pieper also believes there are areas where logistics functions can work together or even share purchasing and equipment. An example is protection wraps used on parts from delivery to factories, during assembly and through vehicle distribution. “When we work more closely together with inbound logistics and assembly, we can plan for the right requirements and do things in a more standard way across the supply chain,” she says.
Coordinating outbound innovation Pieper nurtures these connections across the supply chain in several ways. Monthly meetings with the leaders of each logistics department, for example, encourage discussions on projects and challenges, from the ongoing network design of BMW’s upcoming plant in San Luis Potosí, Mexico, to potential mitigation strategies for Brexit. They are also opportunities to share information and processes.
For Pieper, an important cross-group topic has been how to manage innovation. “It is not so much a question of capacity or transport tools,” she says. “Rather, it is a chance to see how other departments use data or new technology such as augmented reality, all of which we can learn from.”
Across its supply chain, led by senior vice-president for logistics Jürgen Maidl, the BMW Group is studying connected technology and equipment, from self-navigating materials handling to the use of smart glasses or virtual reality. Outbound logistics has links to these projects, most notably the ‘Connected Supply Chain’, a global transport management initiative that aims to increase visibility of material and products to as close to real time as possible, combining it with optimisation tools and sensor-based tracking.
"Logistics isn’t the specialist for connected cars or autonomous vehicles, but we need to think about them, and we need specialists in our team to consider our requirements, adjust and develop new rules." - Anita Pieper, BMW Group
For example, the carmaker’s pioneering ‘Connected Distribution’ project, which has trialled in-vehicle telematics and connected car features to track location and status, will take a critical next step in March 2018 when the BMW Group will ‘go live’ using the features as part of a standard distribution system for a new model launch.
Likewise, a multi-year project to update BMW’s order and allocation system, called Pro-Flex, includes critical features for vehicle logistics, including the ability to prioritise sold vehicles and expedite them through transport and accessory-installation.
Sustainability is another key area for the supply chain, with outbound logistics playing an important role in reducing emissions, for example through multimodal transport lanes or exploring alternative fuels and electrification in logistics.
However, Pieper felt that there was a disconnect between the various outbound-related projects. For example, within vehicle distribution is an initiative to improve data links, including a survey of 50 logistics providers to better understand how they need and use data from the BMW Group, and how information could be shared more quickly from both sides. The project was handled in a separate area to Connected Distribution, although both are relevant to each other.
Pieper wanted stronger connections in such areas. She notes that BMW’s inbound logistics already has a dedicated innovation team, however there has been nothing so specific for vehicle logistics – until now.
From this July, BMW is combining its Connected Distribution programme, Pro-Flex, and a number of other data and IT projects into a dedicated innovation division called ‘Vehicle Distribution 2020-2025’. By January 2018 the sustainability team will also join this group.
“These functions belong together because between them we have a lot information about transport modes, sustainability data and logistics systems; only by combining and sharing that can we gain the true benefits,” says Pieper.
BMW has created an integrated outbound innovation team, Vehicle Distribution 2020-2025, to cover a range of new technology, data and sustainability topics
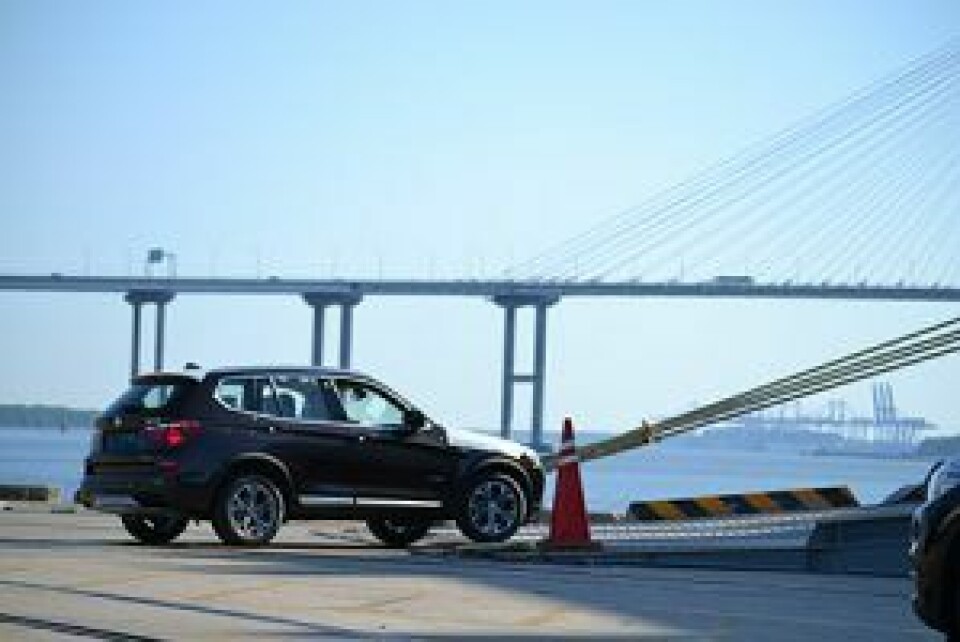
Working alongside the innovation team will also be a doctoral candidate – Promotion, in German – who, starting in October, will begin a research thesis on outbound logistics and BMW’s Connected Distribution. The research will focus in part on developing logistics-based rules to guide the process of using connected car and autonomous-driving technology in distribution, from considering cellular frequencies to determining handling checkpoints. It will involve coordinating with departments from inbound and purchasing to R&D and engineering, as well as suppliers and even other OEMs to develop standards. The Promotion will, in essence, help to increase vehicle logistics’ influence in the supply chain and in broader technology development.
“Logistics isn’t the specialist for connected cars or autonomous vehicles, but we need to think about them, and we need specialists in our team to consider our requirements, adjust and develop new rules.”
[sta_anchor id="3"]The doctoral candidate is from outside vehicle logistics, with a background in mechanical engineering and international supply chain systems projects. Pieper considers such new perspectives essential for outbound logistics to evolve. She admits it is a challenge to operate an enormous network and simultaneously develop new processes and technology. “You can’t always do it with the same people,” she says.
Umbrella networksWhile Anita Pieper stresses its links to plants, inbound and supply chain planning, she is aware of how specialised vehicle distribution is. She emphasises the entrepreneurs who invest in dedicated logistics equipment and the importance of long-term relationships. She takes none of this for granted, and spent much of her early months in the role visiting facilities globally to see operations and meet suppliers face to face.
[mpu_ad]Pieper also recognises distinctions about outbound that offer unique opportunities. For one thing, the scope of the distribution department is vast, including plant yard operations, transport and handling, network management, quality control, vehicle distribution centres (VDCs), compounds, accessory installation and contracting, to name a few. At plants there are also many different functions, but most fall under different areas of oversight.
“The complexity of each task in vehicle logistics may not be so high, but as there are so many contacts and tasks that fall under this department, the range is much bigger,” she says.
Needless to say, vehicle logistics’ global perspective is also different to individual plants, not only for production and delivery locations, but also BMW’s network of VDCs across Europe, South Africa, Asia and North America.
This scope excites Pieper with the opportunity to “think big”. “In outbound, we are always in a network, never just a plant, and so our team members need to think beyond any one location, both to understand impacts across the world, and also to have bigger objectives,” she says.
That is why Pieper has combined her plant-like approach in dividing the group into various project teams, but given them the widest scope possible. She calls this an “umbrella strategy”, where skills, data and objectives are put together in defined structures and charged with ambitious targets.
[sta_anchor id="4"]This is evident even in the titles Pieper gives such groups, such as ‘Vehicle Distribution 2020-2025’. Similar umbrella groups have also been established in major regions. For example, there are now ‘Network Strategy’ teams dedicated to the US and China, each with project leaders tasked with considering operational improvements, network design and upcoming tenders.

Anita Pieper wants outbound project groups to look deep as well as wide across the supply chain. One example under review is in damage protection, notably the interior and exterior components and panels that require foils or wraps during vehicle transport to avoid scratches.
Currently, such parts may have a wrap applied to them at plants prior to the assembly process, which is then removed once the vehicle is built. When it reaches the plant dispatch area, logistics teams apply a new UV-protection wrap or foil, which will again be taken off prior to customer handover.
“This cannot be the most effective way to manage such protection,” says Pieper. “If we could find and agree a foil that could be applied at the supplier after the part is completed, and which could then be used throughout inbound transport, assembly and distribution, the process would be far more efficient.”
The difficulty, admits Pieper, is that there is no integrated responsibility to work across the different logistics and production areas. Under her initiative, BMW has established project groups for packaging, assembly and distribution to pursue a pilot. The objective is to trial the approach with two parts; if successful, Pieper will make the case for a wider rollout.
Pieper would have liked to try putting horizontal protection onto vehicles directly after the paintshop, but there were issues over the necessary drying time for paint. Therefore, the project is set to start with interior parts on the vehicle’s B-pillar (the support section that divides the front side window from the rear and central windows), which often has a brilliant surface that is susceptible to scratches.
Pieper does not suggest such activities are new under her management so much as the combination of people and tasks to encourage transparency. “It is not rocket science. But the strategy is to identify projects, put them under an umbrella, and make the teams part of a bigger event. That is also why we give them bigger names, such as Network Strategy, to encourage employees to go beyond any single consideration.”
In the US, for example, there are studies for a potential new VDC in northern California. The team is also considering adding a new type of accessory installation centre close to its plant in Spartanburg, South Carolina, which would offer customers more opportunities to personalise X-series vehicles built in the US. Currently, such installations are done at dealers or third parties; creating a separate space for them could generate more revenue, but avoid adding extra work across standard operations in the plant or dispatch area.
“The accessory installation centre would be different to a VDC, with no paintshop, and should be close to the plant so vehicles could move on their own wheels and then require only one transport to dealers,” says Pieper.
There are also close studies looking at import routes and combinations for vehicles built in San Luis Potosí, whether through new entry points like Galveston, Texas, BMW’s east coast hubs or rail transport.
In China, where the BMW Group’s logistics is responsible for imported vehicles through to dealers, Pieper wants the Network Strategy team to explore closer ties with its local joint venture, BMW Brilliance Automotive (BBA). Both groups already share a distribution centre in Chengdu, in south-western China, with combined storage, shared transport to dealers and a single provider (with separate contracts). Pieper wants the team to consider similar locations, especially as BBA is setting up countrywide distribution centres as part of a China-wide multimodal strategy.
Pieper insists that the strategy team should think beyond replicating existing projects, and look closely at network impacts and potential. In Mexico, for example, there are [sta_anchor id="5"]project teams investigating quality issues, such as the risk of damage in specific locations from environmental conditions like hail or highly salinized air in ports. “We have to make sure that we link critical data in our network,” says Pieper.
The route from now to 2025Few umbrella groups have been tasked with as wide a scope as Vehicle Distribution 2020-2025, which aims to transform processes across the outbound chain. However, while the name correctly implies a long-term perspective, the innovation team is also working on current and imminent projects. For example, Pro-Flex has already replaced legacy systems in several markets, including rollouts this year in Japan and Canada. Pieper says that BMW is seeing positive impacts on lead times where it can identify critical vehicles in transport.
For sustainability, the BMW Group has made significant progress, including reducing overall carbon emissions by 120,000 tonnes across inbound and outbound logistics between 2014 and 2015, despite volume increases. Meanwhile, after years in which the share of vehicles leaving plants by rail fell, BMW’s global ratio has risen to around 63%. In Europe, BMW has a remarkably balanced split between road, rail and short-sea shipping.
In tenders, the BMW Group now calls on providers to offer transport solutions that include alternative fuels, such as compressed and liquefied natural gas (CNG and LNG), which more carriers are using, as well as electrification.

However, Pieper wants to go further. BMW has commissioned a research institute to investigate the feasibility of transporting cars on ships powered by wind energy. The carmaker is also considering how it can support carriers to introduce electric-powered trucks – which BMW already uses for inbound logistics to its Munich plant – including providing charging infrastructure at plant yards or VDCs.
Perhaps few areas touch as much of both the future and the present as does Connected Distribution, which has made significant progress over the past two years. What started as a pilot to track locations for a few vehicles – initially the i-series electric vehicle built in Leipzig – will soon be included in serial production, combined with an app.
Connected Distribution begins next March with a new model from the Munich plant, in which the functions for tracking will be included in the electronic control unit, and so become part of a car’s “backbone”, says Pieper. This will allow it to send data to BMW using the so-called ‘last state call’.
The system will be available for data during the assembly process, or ‘F1’, once the control unit is installed. “This will allow the assembly team to see exactly where a vehicle is in the plant or yard via an app,” she says. “For example, if there is a vehicle that requires more tests or has a quality issue, they can immediately identify it.”
Vehicle logistics will have a screen available in the app that shows locations, along with status on things such as battery charge. The vehicle logistics team is currently determining a set of rules for exactly how and when they will monitor flows, especially to pick up on exceptions in the process.
For example, BMW has defined geofenced areas at its plants and VDCs, as well as port terminals or compounds run by logistics providers. If a vehicle is outside of the geofence when it should be within it, BMW can follow up as to why.
"The strategy is to… make the teams part of a bigger event. That is also why we give them bigger names, such as Network Strategy, to encourage employees to go beyond any single consideration." - Anita Pieper, BMW Group
Pieper does not envision telematics as a replacement for manual scanning of vehicles at VDCs or compounds, not least since such scans also confirm booking for ocean shipments. However, BMW will able to quality-control how logistics providers scan vehicles, including the delay between a vehicle arriving at a port or compound and when it is actually booked into BMW’s transport system. If providers are waiting a day or more to book the vehicles, it could impact onward transport and delivery times, for example.
Likewise, by checking the state of charge or if there are irregularities, such as lights left on or windows open, BMW can better monitor its providers and quality handling.
“By building a more robust set of data on exceptions or delays to bookings, we will be able to explore ways to encourage improvements with our colleagues and providers,” says Pieper.
The app will initially track the model from Munich globally, with plans to include more cars over time. However, this tracking is limited to vehicles that have connected technology features. While the number is growing – and will increase following regulatory requirements for satellite connections in the EU and possibly the US in coming years – tracking a portion of vehicles makes telematics somewhat less valuable as a data-gathering tool.
[sta_anchor id="6"]“That is why we are currently exploring a potential interim solution for several years, such as putting a dongle on vehicles to track those without connected technology,” says Pieper.
Writing new rulesConnected Distribution has already linked outbound to many departments at the BMW Group, from logistics and assembly to engineering, research and development. For example, issues such as accounting for different cellular networks between the EU, China and US require different frequencies for messages, something vehicle logistics managers have to work with programmers to address.

The China-Europe railway has garnered significant interest among carmakers. Like some other premium European brands, the BMW Group is already a regular user of it to ship expedited parts to its joint venture plants in China, for example. Currently, BMW moves about 2,500 containers by rail to China each year, volume that would otherwise probably move by aeroplane.
Outbound flows of vehicles are somewhat less common, though Volvo Cars began this past June to export vehicles from its plant in northern China to Europe.
BMW Group logistics has trialled the service for vehicles to China. According to Anita Pieper, it worked “really well”, including reliable transport times. However, given BMW’s high export volume to China – it ships in excess of 200,000 cars per year to the country – she suggests that rail is likely to make most sense as a supplement to ro-ro shipping.
Pieper says that the carmaker is exploring how the rail mode could be a viable alternative for some Chinese regions, such as central and western provinces. Thanks to China’s ‘One Belt, One Road’ initiative, these regions have financial incentives to encourage companies like BMW to use rail for delivery. However, Pieper is reluctant to become dependent on these provinces and subsidies.
“The operational tests are a green light but we need to explore to what proportion we will use it,” Pieper says. “I see the opportunity for some small, specific volumes.”
Establishing rules and standards for such operations is partly why Pieper has sought to build closer links between her outbound department and R&D engineers. “We need the competency and the vision in vehicle logistics to know and understand the possibilities, and share that with research and development,” she says. “If we don’t have that vision, the engineering department won’t think of it for us.”
This interaction will only get more important as cars gain more autonomous driving features, and could include vehicle logistics tasks such as loading, unloading or transport between parking and workshops in VDCs. Bringing together such considerations will be exactly the purview of the doctoral candidate starting in October.
“We need steering methods that can establish the information that we can use from the vehicles, combine them with logistical rules and establish how the information flows to other systems as well,” she says. “It is a critical operation and I think it’s essential that we expand our competencies.”
The researcher will also have an important job in interacting with logistics providers and other carmakers. BMW Group logistics already participates in cross-industry groups on tracking, including in an outbound logistics group under the auspices of the German Automotive Association (VDA), as well as a working group dedicated to establishing standards for telematics at the Association of European Vehicle Logistics.
“We think it is important to work with other manufacturers to establish the right standards and processes,” Pieper says. “However, we will be in a much better position to participate in such industry groups once the Promotion is on board.
“We’re building a real team and new competencies for Connected Distribution and once that’s done, we can share a lot more with the industry.”
Looking to the future, handling the nowAnita Pieper is not short of vision, and wants her team motivated to work in forward-looking projects. However, she admits that it is not easy to look ahead while dealing with the operational issues of the “now”. That is especially the case currently, with European markets enjoying relatively strong growth and plant production running high, but with logistics space in yards and terminals no bigger than before.
“Operational steering of the network is currently the most time-consuming task for vehicle logistics. We face quality holds from plants and limited space, while any weather or other network disruptions have knock-on effects,” says Pieper.
In late June, for example, strong storms in the north of Germany prevented two trains destined for the north German port of Bremerhaven from leaving the BMW Group plant in Dingolfing, causing even more congestion at the plant yard. Meanwhile, high volumes across the industry are slowing vehicle throughput at major export and handling centres. There are similar issues at locations in the US and China.
There are opportunities where investment in new facilities will relieve bottlenecks and expansion projects are underway. In the UK, for example, BMW has contracted terminal provider Able UK to develop a new VDC in Killingholme, in the Humber Estuary, to handle vehicles imported through the port of Grimsby. The VDC will open later this year and start full operations in January, run by logistics provider GBA. It will complement the carmaker’s other UK VDC in Southampton, which also handles BMW Mini exports.
The Killingholme VDC, which will have a paintshop and accessory workshop, will replace a current inland facility in Thorne, in South Yorkshire, where new imported cars are handled alongside used ones and motorcycles.
“That was too much. The new VDC will free up space in Thorne, which will still handle used vehicles and motorcycles,” says Pieper. “As the new VDC is next to the port, we won’t require additional transport to it.”
Last year in the US, BMW opened a new VDC in Galveston, Texas, with terminal provider and shipping line WWL for vehicle distribution in the Gulf and central US. On the west coast, meanwhile, it is expanding its VDC in Oxnard, north of Los Angeles, at the port of Hueneme.
“Oxnard was originally built to handle 60,000 vehicles per year, while currently we ship around 200,000 there,” says Pieper.
With the strength of west coast markets, BMW also believes it would benefit from a second entry point in the northern part of California. “The biggest hurdle is the environmental risk from an earthquake. We want a safe area to store our vehicles, and we are currently reviewing options,” she says.
In late June, BMW also announced a further $600m infrastructure investment at its Spartanburg plant, which will support production of the X-series there.
In China, BMW will in July re-open its VDC in the port of Tianjin, in the north-east, which had been shut following the port explosion in the summer of 2015. Since then, the carmaker has used a temporary space, however without a paintshop or automatic washing facilities, both of which have been restored in Tianjin.
"By building a more robust set of data on exceptions or delays to bookings, we will be able to explore ways to encourage improvements with our colleagues and providers." - Anita Pieper, BMW Group
At its Shanghai VDC, meanwhile, BMW has recently installed a paintshop, part of a trend towards upgrading Chinese port facilities – all of which are run by providers – to allow more extensive customisation and accessory work.
While Pieper says BMW will expand or improve its network wherever it makes sense – current tenders for the US east coast and Europe are considering new options and combinations, for example – she emphasises that there is room to improve existing operations. For example, overcrowded yards are exposing gaps in handling processes.
“I’m spending a lot of time trying to see where vehicles are, why they might be standing somewhere, and what contract is behind the vehicles,” she says. “For example, if a car has been stood for two days, is that because there is a problem, or because the carrier contract stipulates that he can pick it up 48 hours after the dispatch order?
“We have a strong, efficient operation, moving around 2.4m cars per year in good quality, but we do not always handle deviations in a standard way,” she adds. “That means we don’t always have full transparency of each move, when we in fact need to understand every time so we can learn and improve.”
[related_topics align="right" border="yes"]Projects like Connected Distribution and Pro-Flex will increase visibility of inventory and processes over time. But Pieper admits that she only has so much resource and budget, and clearly vehicles need to move, whether using the latest technology or legacy systems. Sacrifices are necessary and innovation is sometimes put on hold.
“For example, one of our team members had the idea to use all the data that we obtain about future vehicles to carry out virtual load testing, where we can simulate handling rather than waiting to do it physically,” Pieper explains. “It is a great idea, but the question is, do we invest in virtual reality now or wait a bit longer to see how the technology will develop? It is always a challenge to balance resources.”
To maintain priorities on innovation, however, Pieper wants to simplify current processes. She thinks, for example, there may be room to cut some of the many key performance indicator reports and checks the carmaker runs.
[sta_anchor id="7"]“Do we need all of them? We are looking carefully at where we can free up capacity and use it for other things, like new technology,” she says. “This is what we need to do to stay ahead but also continue to manage a huge network.”
Taking ownership and responsibilityAnita Pieper has put a lot of focus on BMW’s internal research and projects. But she also understands the critical role that logistics providers will play in developing BMW’s future distribution processes and equipment.
To that end, she wants BMW’s logistics providers to be more proactive in adapting their equipment and processes to the carmaker’s changing requirements. She repeats calls made by her predecessors who emphasised that, as vehicles have grown larger in recent years, logistics providers need to consider such dimensions in rail, truck and yard investments. But she also wants companies to prepare for the rise in autonomy and green technology, including with more flexible equipment.
“Perhaps soon, trucks will be autonomous and electric, so what will that mean to carrying and handling vehicles?”
To support providers in these decisions, the BMW Group is running supplier days and workshops to share its technology and expectations. “However, we expect logistics companies to be experts in their own equipment and they need to take responsibility for it,” says Pieper. “They also need to be proactive and find out what we want and need, rather than waiting for us to ask them for it.”

Sustainability is a topic in which Pieper thinks providers must do more. While BMW is pursuing wind-powered ships, alternative fuels and electric trucks, she is surprised that carriers have relatively little to offer beyond charging higher prices to use green energy sources. She is worried it will end up being carmakers like BMW that invest in new equipment, when she believes it should be providers.
“I understand that some of this has higher costs but it should be a shared commitment to improve the environment and meet targets,” she says. “I would like to see logistics companies take more ownership of these things.”
For Pieper, when managing a vehicle distribution chain that involves so many parties, handovers, equipment types and systems, not to mention geographies, individual responsibility is often as important as the collective effort. After all, whether in applying new locations, technology or concepts, the chain is jeopardised by its weakest link, and she is determined that outbound, and its providers, will be among the strongest.