Can one size ever fit all?
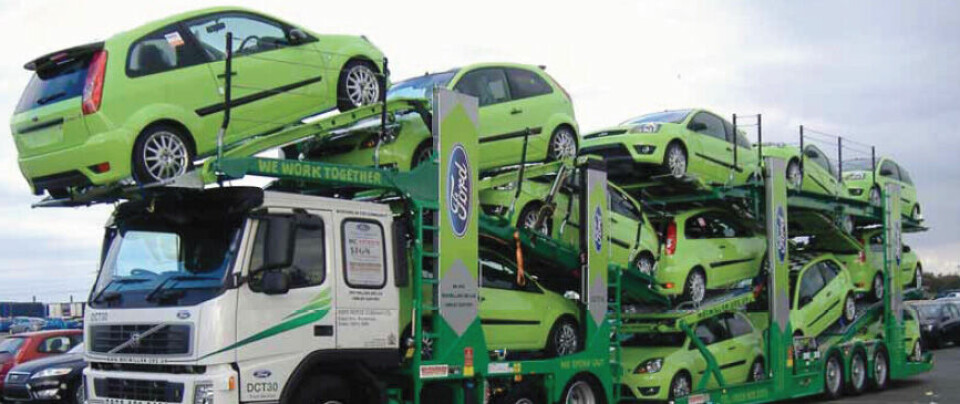
Carmakers are gravitating towards similar standards and technology for road carriers, but the recession has made investment tougher than ever. Carrier builders and customers speak about how much cutting-edge technology and processes count
The purchase of new vehicle transporters has followed the downward trend of car sales. Carrier builders are trying to keep their edge with design improvements and increased flexibility, including diesel-fuel technology and replaceable panels. Soft tie-downs are also becoming essential and automated deck features are speeding up the loading and unloading. A long-standing but fundamental problem transporter manufacturers face is accommodating an expanding range of vehicle sizes on a single carrier. “Flexibility is essential to handle the variety of car and light commercial van designs while maximising capacity,” says Richard Lawson, who owns Spirit Autologistics, based in the UK. He has noticed that whereas some new designs have increased van carrying capacity, they can restrict car capacity.
Ford in the UK wants a carrier that accommodates a diverse model mix of vehicles from the Fiesta small car to the longwheel base, high roof Transit van, according to Kevin Knight, a senior supervisor for outbound logistics. Ford uses transporters that carry the maximum vehicles for UK roads, which requires a three-deck configuration rather than two-decks as used elsewhere in Europe.
For Austrian-based transporter manufacturer Kassebohrer, the main challenge is to produce a body that can carry passenger cars and commercial vehicles with easy handling and fuel saving superstructures, reveals CEO Günther Percht.
Flexible and adjustable equipment stands out
Flexible capacity is also important to BLG Auto Transport, which operates more than 500 trucks in Germany, Poland, and Ukraine. Wolfgang Stoever, sales and marketing director of parent company BLG Automobile Logistics, says that it uses manufacturers Lohr and Kassebohrer for its trailers and Mercedes-Benz, Renault, and MAN for its trucks. Recently, BLG Auto Transport ordered 80 new trucks from Mercedes- Benz and MAN. “For our customer Daimler, car carriers must be able to carry smart cars with a load factor of 12 as well as M-Class SUVs with a load factor of four to five,” says Stoever. Increasingly car transporters must accommodate vehicles with low loading angles and lower ground effects. “The undercarriage cannot scrape the ground and the loading angle cannot be so steep as to hit the front nose on the deck,” says Keith Fritzsching, national sales manager at transporter manufacturer Delavan Industries, based in West Seneca, New York. Along with lower loading angles, the changing designs of new cars with higher roof profiles have made it more difficult to move at full capacity, points out Lawson.
Designing the perfect car carrier
To achieve such flexibility, the major vehicle logistics players cooperate on different levels in designing car transporters. “We have a high degree of influence in the design of our car carriers,” explains Stoever. “It involves a dialogue with the manufacturers of trucks and trailers; there is also close cooperation between truck and trailer manufacturers.” Because of growth in the volume and size of commercial vehicles, manufacturers are redesigning their products to increase loads. Lawson says that transporter manufacturers work closely with carmakers to respond to technology and design requirements. Transporter Engineering jointly designed a car transporter called Maxicom, which it introduced in September. Although the initial intent was to maximise loads on panel vans, it also wanted to carry cars, explains Jim Pearson, managing director. Transporter Engineering works with PSA and Ford, with which it shares CAD drawings that enable it to view the size of their upcoming vans. Compromises on carrier design may not necessarily benefit the customer. “Vehicle manufacturers in the UK say that they want the highest quality transport, but it usually comes down to the price of moving the car,” says Pearson. “That means the highest load factor and reliability at the lowest price, which may stifle potential improvements. For example, a trailer with a particular axle weight may be fine now, but in ten years, it may not be sufficient. We could increase the axle weight, which would increase the capacity. Vehicles manufacturers are on board for technology changes, but not for incurring any costs associated with it.”
BLG uses twin axles to increase the load factor to the weight limit. “There is a serious discussion about whether or not trucks can get longer and heavier. Of course, there is the risk of damaging the road with too much weight, but if you do not increase capacity, you will not be as efficient in fuel, wages, tolls and diesel taxes,” says Stoever.
A divided Europe
As transporter manufacturers and users work to maximise capacity on their vehicles, government restrictions could limit those efforts. Says Kassebohrer’s Percht, “In Europe, the maximum dimensions for truck and trailer height, weight, width, and length vary by country. There is no harmonisation in sight. Everyone thinks about the need [to harmonise] for intermodal shifting, but in a political sense, harmonisation is not on top of the list.”
Whereas the overall length restriction in the UK is 18.75 metres, less than other European countries, the only height restriction is approximately 4.88 metres, compared to 4-4.2 metres elsewhere in Europe. Thus, Transporter Engineering’s trailers carry 11 vehicles instead of 8-10. There is a 20.75- metre length restriction in two-thirds of the countries, and in some countries, transporters can operate up to a length of 22.75 metres. There is also varying amounts of overhang permitted by cars on the back of trailers, which can mean the difference between being able to load another car, or not. Although capacity limits are a practical part of the business, increases are still occurring. Last June, Kassebohrer, reduced the net weight of its newest trailer, the Intago, which enables the addition of 1.5 tonnes more capacity, according to Percht. It can hold ten Volkswagen Golf cars. The Intago also has a new lifting system that can use the entire width of the upper platform for holding vehicles. “There is no offset bar in the way, so commercial vehicles or SUVs that exceed the width can now fit,” says Percht.
What to tell your carriers
As cost pressures dominate, carriers have become more demanding about the reliability of their equipment, according to Pearson. About two years ago, Transporter Engineering made a change to its design that involved bolting pieces of the frame rather than welding them. “If a car transporter sustains damage, we or the carrier can unbolt a section and re-bolt it within a couple of hours,” he says.
At VW Mexico, logistics manager Luis Carlos Olivares says that all modifications to its car transporters must be quantified in terms of efficiency, quality, and speed of vehicle distribution. He says that VW Mexico is meeting the demand for its commercial vehicles by using specialised flat-bed trucks with modifications for vehicle lashing. VW Mexico began using these trucks through two logistics providers in March 2009 for imports through Veracruz and for domestic deliveries. The trucks hold two vehicles on average, and as many as three. “This is a good option due to the size of our commercial vehicles and it provides an additional measure to ensure the efficiency of haul-away transport,” says Olivares.
For American Honda, the two main components that determine transporter efficiency are speed and cost, according to Scott Crail, manager, logistics operations. He explains that Honda has set no standards and issued no dictats on the technical aspects of carrier equipment. “We have left it up to our car hauler partners to determine how they can best deliver on their commitment. The industry’s move to strap trucks shows its commitment to quality delivery, and Honda supports this equipment shift. Almost half of our carriers probably use straps, including all of the new ones,” says Crail. Carmakers have recently embraced the use of soft tiedowns, which are wheel straps that allow vehicles to ride on their own suspension. They are designed to reduce damage and driver injury by replacing chains that attach the vehicle’s undercarriage to the trailer.
Delavan’s Fritzsching says that beginning in January, no new General Motors’ vehicles in the US will have the ability to use chains, and all OEMs will follow suit by 2010. Toyota already uses soft ties, but made its use of them official in 2009. All of Delavan’s new equipment contains the soft tie, also known as the ‘ground strap’ design that requires each deck to be lowered to ground level so that the driver can remain on the ground instead of climbing on the side of the truck, which improves the driver’s safety and productivity.
Delavan also uses hydraulic technology with self-locking cylinders in all of its new designs. “With the older technology, when raising the deck, you needed a support post to pin the deck when it was in the air. With the self-locking cylinder, it locks automatically, eliminating the need for an extra post. This saves weight in the trailer, improves driver productivity, and helps reduce damage to the vehicle when loading or unloading,” says Fritzsching.
More of Honda’s carriers are using straps, along with new deck designs that lower the decks to ground level. “Straps and new deck designs are lowering the cost to carriers through reduced driver injury. Truckers say that they will gain a larger pool of drivers with hydraulic deck technology, which is safer and easier,” he says.
American Honda anticipates that the shift to strap rigs will lower damage. However, Crail says that it is difficult to show a direct relationship between equipment changes and cost. “If improvements have reduced the carrier’s cost, we have not seen it. We anticipate future benefit in lower, or at least controlled, rates as carriers pass some savings to us,” says Crail. He admits that the carmaker does not see as much damage now and that straps could be the reason because chains are not dropping on the cars. However a large percentage of damage is on the bumper and straps do not affect that