Cutting out the paper trail
Digital information is faster, more accurate and more useful, so why is there still so much paper in the automotive supply chain?
Almost all companies now have some kind of digital infrastructure underpinning their processes, but can any automotive logistics operations be said to be truly paperless?
Perhaps the most notable recent example of a company moving away from paper has been Chrysler, which since 2014 has mandated that its dealer deliveries use electronic proof of delivery (ePOD), leading carriers to adopt a number of paperless solutions. Volkswagen Group companies including Audi and Skoda, too, have been using mobile truck check-in at some plants, allowing drivers to enter a yard without having to stop at the gate.
Nevertheless, the automotive supply chain remains filled with stacks of paper, but is this just an unwelcome remnant of out-dated processes, or are there good reasons to retain the simplicity and accessibility of straightforward paper documents in some instances? We followed the paper trail to find out.
In this story...
- A history on paper
- Counting the cost
- In-plant applications
- Structural inclusivity
- Recycling the benefits
Historical precedent is a strong driver for paper use, says Alistair Newton, director of supply chain and logistics services at UK-based IT specialist Sovereign Business Integration Group. Sovereign’s Event Management Logistics (EML) product is a cloud-based solution tailored for the vehicle supply chain, among other sectors. “It’s very rare for a company to adopt a ‘Big Bang’ approach to eliminating paper from their processes,” he says. “Usually they take baby steps. For example, they might start with an electronic document management and workflow system to scan and store paper records provided by their customers or suppliers, then gradually evolve to cut out the paper middle man and give customers direct access to their systems.”
According to Newton, the steps towards paperless typically start in an organisation’s back office with finance and billing processes, before spreading out to other operations. Perhaps that’s one reason why paper persists at the fringes, in dispatch notes and delivery documentation, but there are reasons why it has been harder to remove paper from some areas than others. “For legal and contractual reasons companies need to ensure the integrity of their records,” he says. “In automotive, for example, that’s very important in the management of damage claims documentation.”
Moving to electronic storage of those kinds of documents requires companies to develop secure auditable systems that can assure the integrity of the information they hold. “You need systems set up so that, even if a document is changed or edited, you can always drill back to the source data if you need to,” Newton explains.
In several parts of the supply chain, the law actually requires the use of paper documentation. “In today’s fast-paced environment all planning and execution by LSPs and carriers is paperless,” says Dave Belter, vice-president of global transportation management at Ryder. “But that data often exists in a secondary form on paper, notably in the bills of lading used by carriers.”
Traditional paper bills of lading still have an important role to play, he continues, especially as a means for truck drivers to explain their contents of the vehicles to police and other authorities.
So far, efforts to remove the need for paper bills of lading are the exception rather than the norm. Matthias Berlit, vice-president of manufacturing logistics at supply chain IT provider Inform describes one such project at the sequencing facility of a German OEM customer: “This company runs a crossdock and consolidation facility a few kilometres from their main plant. Around 300 trucks per day travel between the two locations and the company has reached a special agreement with the local police force that allows them to use the in-cab display unit rather than a physical bill of lading to show what they are carrying.”
"In today’s fast-paced environment all planning and execution by LSPs and carriers is paperless. But that data often exists in a secondary form on paper, notably in the bills of lading used by carriers" – Dave Belter, Ryder
Inform has developed a special screen for the in-cab terminals that provides the police with the load information in an appropriate format, he adds.
However, such legal barriers can be particularly stubborn at international borders. While many countries are pushing shippers towards digital notification of cargoes, others, like Brazil, still require ‘blue ink’ documents with original signatures to accompany international shipments, notes David Parker, global director of operations, process and IT at supply chain management company UTi Worldwide.
It isn’t just legal and contractual ties binding companies to paper; there are financial issues, too. The cost of storing large quantities of data – and of being able to access that data fast enough – has been a key historical consideration, especially for smaller companies, says Sovereign’s Newton. But he suggests that many of these problems have been reduced significantly through a combination of falling infrastructure costs and smarter design. An explosion in the availability of low cost, network-connected devices also makes it easier to collect and share data in environments like truck cabs or yards. “You can now get real-time proof of delivery on non- specialist devices like a tablet or a mobile phone,” he notes.
The equipment isn’t the only cost to companies moving to fully digital processes – there’s also the expertise needed to implement, run and maintain sophisticated software systems. “The cost of creating a connection to a customer or supplier’s system is important, especially in countries where labour is relatively cheap,” say UTi’s David Parker. “But the ability to have the same data from beginning to end is key to uniting the supplier, customer and the forwarder.”
This a challenge that remains real today for smaller companies in high labour cost countries too, despite advances in technology. Many smaller players in the supply chain still have relatively unsophisticated internal IT infrastructures. It is a situation that is “a bit more widespread than you’d think,” says Tom Kozenski, vice-president of industry strategy, at software company JDA.
David Stain, Europe, Middle East and Africa marketing lead for manufacturing and field mobility at tracking technology company Zebra, agrees that the shift to real-time digital information can be daunting for companies used to manual systems. “I remember how much of a shock it was to suppliers when the car companies started to ask for data as a flat file, rather than on paper. These new systems will be similarly challenging,” he suggests.
In the factory environment, the last vestiges of paper are falling to a variety of different approaches. Kanban cards, once an emblem of the Toyota Production System’s robust simplicity, are now being replaced by e-kanbans that use barcodes, computer screens or other triggers to send a replenishment signal to manufacturing control systems.
At Zebra, Stain describes on-going work to replace another lean manufacturing stalwart – the printed standard operating procedure – with an electronic equivalent. “In warehouses, it is already common to guide operatives with voice or video cues,” he says. “Now we are looking at similar technologies on the assembly line, where the operator has real-time access to a digital checklist that they tick off as they complete each task.”
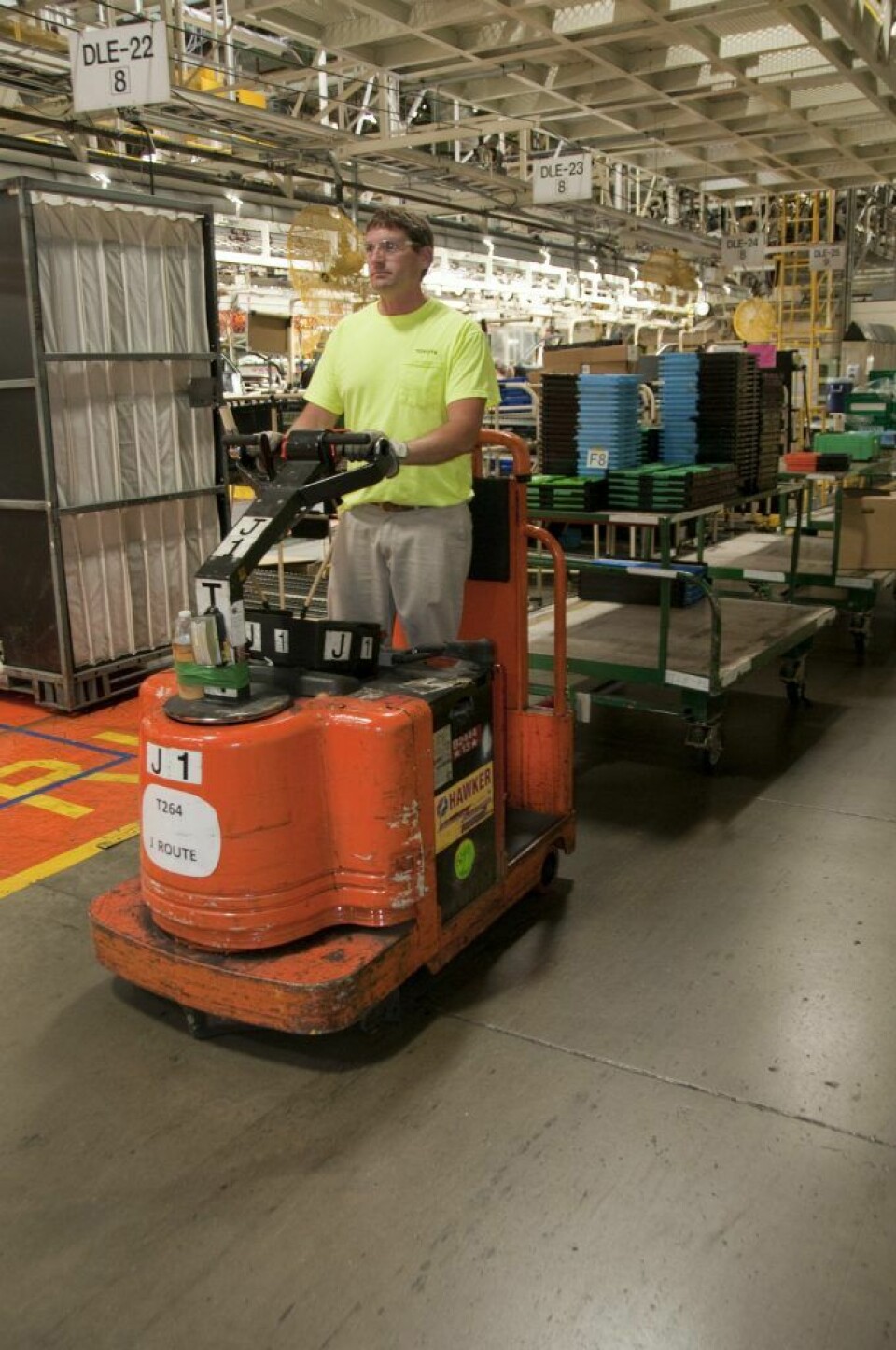
Matthias Berlit says the labels used to identify parts and containers in the supply chain are another stubborn source of wasted paper. “Often, production material receives a new label at every step in the supply chain,” he says. “That means the same part could have ten different labels in its journey from the supplier to the final assembly line.”
Inform is working with several OEM and tier one suppliers on global transport labels – a single label applied by the original supplier and used to identify the parts throughout the logistics chain. As with other efficiency improvement efforts, he notes, it is often the smallest suppliers that have the most difficulty adapting their systems to cope with such changes.
On a similar theme, Stain describes efforts by Zebra to improve the durability and versatility of barcode labelling systems so that parts can be labelled in a machine-readable manner at every stage in the production process. These efforts include heat-resistant labels and adhesives that allow barcodes to be applied to freshly made ingots of steel as they emerge from the mill.
Just making the transition from paper to electronic communication and storage is only part of the story, notes Jens Möller, senior vice-president for automotive at UTi. If that information needs extensive manual intervention or re-keying between one system and another, it will still be delayed and error-prone. “Handling information is just like handling parts, you should aim to touch it on as few occasions as possible,” he says.
In fact, the structure of many large companies means they may need to pass data through many interfaces inside their own computer systems, which are often formed from a diverse collection of different programmes and platforms. In an attempt to overcome such internal inefficiencies, UTi now has a single platform to control all its operations worldwide, something that Möller insists is still rare in the industry.
Many large organisations have tackled the issue of small suppliers who are unable to link directly to their systems via EDI or other automated messaging technologies by offering access to their own systems via internet-based portals. This approach helps to reduce the burden at the customer, but it comes with significant costs for the supplier as such systems rely on a lot of manual data entry by operators, with the inevitable productivity penalty and risk of errors.
"Often, production material receives a new label at every step in the supply chain. That means the same part could have ten different labels in its journey from the supplier to the final assembly line" – Matthias Berlit, Inform
The use of multiple portals can create complexity problems, too. “We’ve seen situations where small companies have to access the line of business systems of ten or a dozen different customer contracts,” says Sovereign’s Alistair Newton. “That means they need people with an in-depth understanding of each of those systems – it is quite a burden.”
The alternative at this point, he suggests, is for companies to invest in a secure feed from their own company system to each of their clients’ systems to share the tracking of processes and data.
As OEMs, partners and suppliers gradually overcome the barriers to fully integrated digital information flows across their supply chains, what benefits can they expect to capture? There are productivity gains to be had, of course, as fewer people are forced to spend their time pushing paper around, or manually re-keying and reformatting data between systems. Quality should improve too, with fewer errors resulting from lost documents or typing errors, but these advantages are merely the tip of the iceberg.
As systems become better integrated, increasing the speed of information exchange across the supply chain is a key benefit. JDA’s Collaborative Supply Execution system is used by a number of large OEMs to share planning and operational data with thousands of suppliers. According to Puneet Saxena, vice-president of industry strategy for manufacturing at JDA, by communicating their production plans as far in advance as they can, and crucially, communicating any changes to those plans as soon as they happen, companies can greatly reduce their ‘bull whip’ effect, whereby communication delays the impact of demand changes, which are then amplified through the supply chain.
Matthias Berlit points out that a critical advantage of electronic communication is that every stakeholder can be sure they are working with the most up-to-date information. “With real-time information everyone can respond much more effectively to last minute changes,” he says. “For example, if a driver is taking a vehicle to a particular storage location in a yard and the system identifies an issue with the vehicle or the slot, they can be redirected on route.”
Zebra’s David Stain suggests that a key benefit for companies aiming to run fully digital real-time systems is an improved ability to respond when things go wrong. “When everything is running smoothly, these systems are simple. It gets tricky when you have a quality issue and you suddenly have to put parts into quarantine, and trace the problem back up the supply chain.”

At Ryder, Dave Belter makes a similar point for logistics networks. “It’s all about managing exceptions,” he says. “And you want to be alerted when an exception is imminent, rather than once it has happened.” GPS and cellular phone tracking technologies play an important role here for Ryder, he notes, along with “predictive analytics that can identify whether a conveyance is likely to arrive on time, allowing you to take action early and find a solution if it is not.”
Sovereign’s Alistair Newton adds that a well-designed digital infrastructure also helps when things go really wrong. “Well-designed systems have built-in disaster recovery capabilities, so if a fire or other catastrophic event closes a facility, you still have access to your records to help keep the business running.”
The benefits of fully digital information go far beyond the purely operational. Detailed digital records of past supply chain performance also give manufacturers and logistics suppliers access to powerful new management tools. “From a strategic perspective, these systems give you a wealth of data on the performance of your networks,” says Belter. “You can see which of your suppliers are not meeting expectations, and you can identify the opportunities for performance improvements.”
At UTi, Jens Möller points out that a key advantage of the company’s new, fully unified system is the way it helps to enforce standard processes right across the organisation, greatly reducing the management overhead that was previously required to do that. Möller’s colleague David Parker, meanwhile, suggests that the freight forwarding sector can look to the express parcels industry for a glimpse of what fully integrated information flows will eventually deliver.
“We are aiming for a situation where the supplier just needs to scan a part as it comes off the end of their line to create the appropriate delivery order – eliminating the remaining faxes, emails or phone calls that still take place today in this part of the process,” Parker states.
Ultimately, says Zebra’s David Stain, real-time data exchange will accelerate the entire supply chain, as the time windows that manufacturers use to schedule the delivery of parts to the assembly line shrink “from days to hours, or even minutes.”
Exactly when that will happen though is not yet clear. “Going paperless throughout your organisation requires a cultural change,” concludes Alistair Newton. “I’ve seen many organisations get rid of a lot of paper from their processes, but I’ve never seen one get rid of all of it.”