Bosch urges the use of digital twins on shared data platforms
Tier one supplier Bosch has been using digital technology to overcome data silos with the aim of reducing costs and managing supply chain complexity. Dr Birgit Boss, Bosch’s senior expert on digital twins, explains how the rest of the automotive industry can benefit from it too
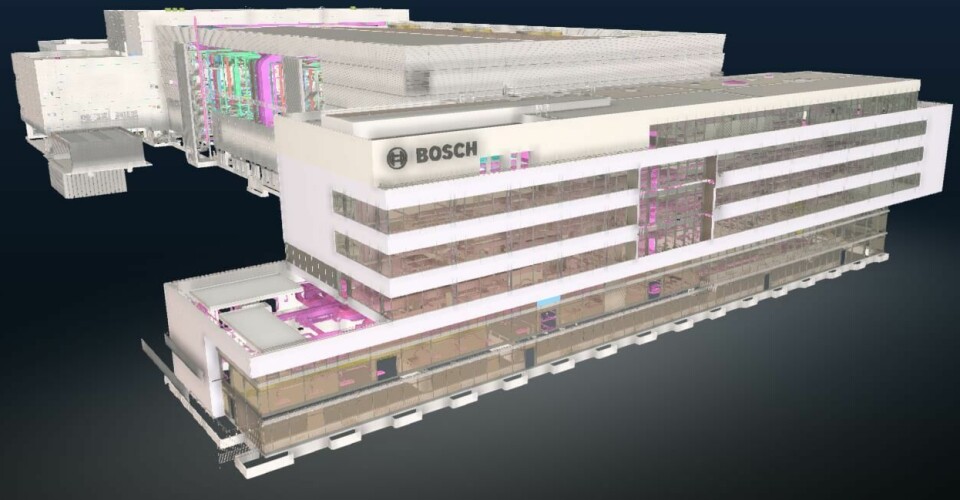
The use of digital twins – the digital reproduction of a machine, production line or supply chain operation – has been highly anticipated within automotive logistics for years, particularly to plan, quality check and monitor logistics flows. Despite many manufacturing and warehouse operations already using them to manage material flow, efficiency and quality, however, it has taken slightly longer for them to catch on within the logistics supply chain more widely.
Even as automotive logistics increases its digitalisation, there are still barriers for many OEMs and suppliers that are preventing the use of digital twins. Dr Birgit Boss, senior expert on digital twins and standardisation at Robert Bosch, believes that this is because of a lack of certainty in companies as to when exactly they should invest and join the train. There is also a hesitancy to share data in general and, most importantly, a lack of understanding of its benefits.
Starting small to get the ball rolling
As a basic definition, digital twins offer data for a specific asset. These assets can be asset types, for example a specific type of battery, or asset instances, for example a singular battery with a defined serial number. The digital twins are sets of different submodels, with each submodel representing a different aspect of the product, such as submodels for the material composition of a battery or just documentation. By being able to access these chunks of information based on smaller submodels the digital twin offers, it makes it easier to track and measure parts and products throughout their lifespan.

Boss explains that to fully reap the benefits of digital twins, you need to be clear on your use case – or what you want to gain from using the technology. This could be an end goal such as measuring the carbon footprint of a part to then improve sustainability, or using digital twins to measure and track parts, and how they are moved as part of the logistics flow, with the aim of improving efficiency and quality.
In Bosch’s case, the company has several projects with different use cases because of its multiple business units and divisions. Boss says that the industrial technology sector of Bosch is very advanced. There are over 200m digital twins in place for different product groups, such as tightening systems or industry hydraulics, powered by the Bosch Semantic Stack. However, she says it’s important to think of just one use case and one product group, and eventually build from there, rather than trying to implement all possible use cases at once, as the technology of digital twins is modular and scaleable. More data for additional and new use cases can be added at any time to an existing digital twin. Use cases in logistics rely on several companies working together to share information.
Learning to share
While companies are often eager to push for more collaboration in the automotive industry, it becomes more difficult to follow through on that ideal when it comes to sharing your own firm’s data. Boss says that getting partners onboard to collaborate is key, but this can be difficult as it is not the norm in such a competitive industry.
This is one of the reasons that Catena-X was formed in 2021 by the German Federal Ministry of Economic Affairs and Energy, and the German Association of the Automotive Industry. Catena-X is a European-wide initiative to create an open data-sharing platform designed to increase visibility in the automotive supply chain and improve the flow of parts and materials. It creates uniform standards for data and information exchange and is managed on a peer-to-peer system to ensure security in the exchange of supply chain data. Catena-X has three pillars to it; a consortium, an association and the first operating company known as Cofinity-X. There are currently around 170 members working on the platform, including Bosch, which holds spots on the management board and the advisory council, and carmakers such as BMW, Ford, Mercedes-Benz, Renault, Stellantis, Volvo and Volkswagen.
![There needs to be a standardised API that allows everyone to access all data and communicate it in a standardised way [pic: Bosch] sofc_salzgitter_kh-erkelenz](https://image.automotivelogistics.media/178833.webp?imageId=178833&width=960&height=642&format=jpg)
To ensure that different companies feel comfortable sharing data, there needs to be open communication between everyone involved, with agreed definitions and boundaries set early in discussions. “It is not enough to provide data, you also need to provide information,” Boss says. “The first thing to do is to agree on the semantics of the data. This is closely coupled to agreeing on which data should be exchanged and why.”
Boss explains that this is exactly what was is done in Catena-X: defining which data needs to be exchanged to implement the use cases identified. The standards library of Catena-X documents the semantic models all stakeholders agreed on.
“Not all data will be shared with all partners. There will be specific usage policies defining who is allowed to do what with the data”
Dr Birgit Boss, Bosch
Data sharing is not sharing without knowing what others plan to do with it. “Without agreed use cases that are beneficial for all involved parties there will be no data sharing,” Boss says. “Not all data will be shared with all partners. There will be specific usage policies defining who is allowed to do what with the data.”
She says there also needs to be a standardised application programming interface (API), which allows everyone to access all data and communicate data in a standardised way across various industrial applications and machines end-to-end. “This is why I’m also active in the Industrial Digital Twin Association (IDTA),” Boss says, “to drive these digital twin specifications that a programmer can implement and afterwards [make] interoperable with twins from other companies. Without a standardised API, every supplier would implement its own, or each OEM would request another API from its suppliers, which would be very cost-intensive.”
The legal bit
Of course, in any business, when data sharing is involved it needs to be treated carefully. This is where these usage policies come into play.
“You should be aware of what you’re sharing, and that you don’t request something that nobody can share,” Boss says. “These usage policies and access policies are important, as they define who is allowed to access the data and the way another party should handle it. Some data is uncritical, like documentation that you could download from the internet anyway, but some data is critical or could even cost something to use, depending on usage policies and contracts.”
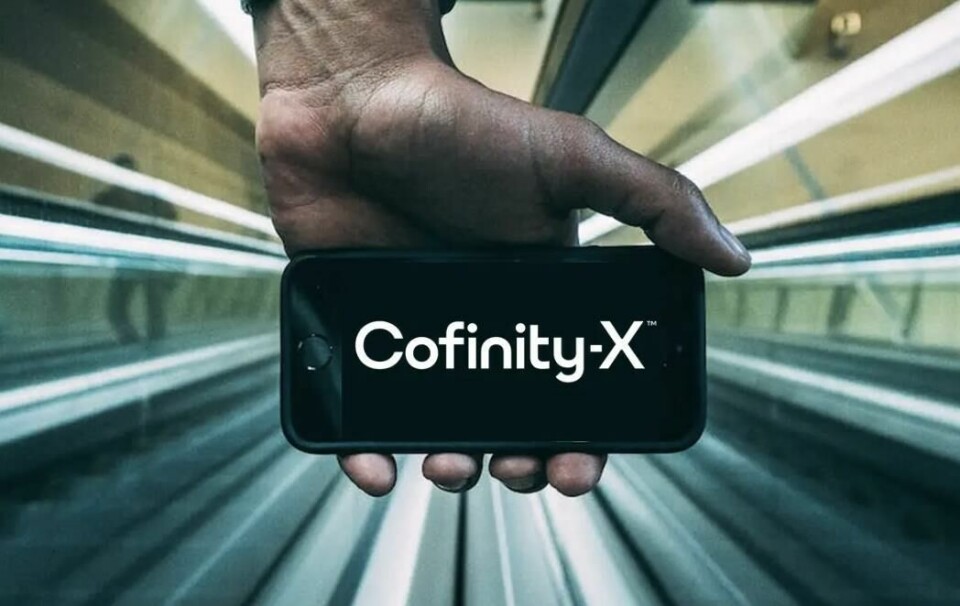
Usage policies and access policies also set out where other parties are required or allowed to access shared data, if it can be shared with a third party or for how long it can be accessed.
Boss says that digital twins are an important building block to also help fulfil legal requirements in the area of sustainability and circular economy, for example the Digital Product Passport and provision of the carbon footprint of your product. These are use cases that require collaboration and this is why data spaces like Catena-X are so important. These data spaces will only be successful if all players, small and large, participate. Successful onboarding of smaller and mid-size companies is a very important topic for success.
Cost compared to payoff
“Standardisation helps decrease costs because you do not need to implement interfaces for every customer,” says Boss. “Standardisation also increases security in investment, if there is a powerful community built around the standard.”
This is where the IDTA that Boss is part of can help. “The IDTA is the first point of contact when it comes to implement digital twins,” she says. “You need to have a community where you can share and experience all of this, otherwise we will not be successful in reaching interoperability.”
“Standardisation helps decrease costs because you do not need to implement interfaces for every customer”
Dr Birgit Boss, Bosch
Boss adds: “If you have a good idea for a use case, but there is not yet a standardised model for a digital twin, there is a way to go to the IDTA and ask for a new model, and ask if there are any other interested parties in the association who would work with you on it. Then the IDTA can create a working group, the group makes a proposal, and the IDTA then may publish such a submodel as a standard.”
Once this first step is taken, Boss says it can be easily scaled up. “You learn how to make and use digital twins and their standardisation faster and better and improve your own use case. It’s a learning curve,” she says. “But it’s not the learning that’s the best bit, it’s finding new use cases.”
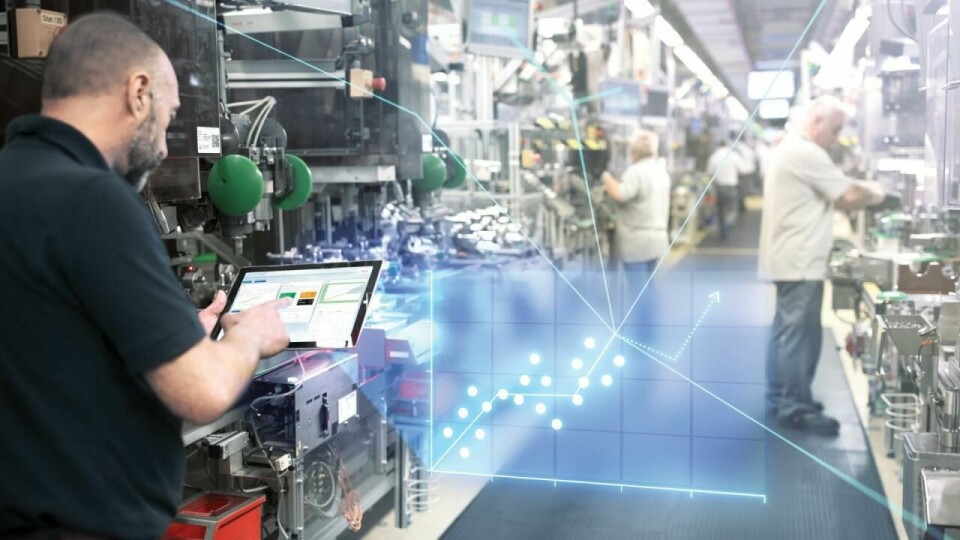
Adding more of them benefits the customer, according to Boss – more data, information, partnerships, lifecycle phases and anything else that is needed. “You could start with documentation or carbon footprint as your use case, but it’s extendable and modular,” she says. “That’s what is so convincing about investing in digital twin technology.”
She adds that it’s important to remember that investing in digital twins doesn’t mean you will immediately see an increase in customers or profits. Instead, Boss says it is “an enabling technology” to more success. “That’s why it’s sometimes difficult to explain to management, because it’s not the final application or solution, it’s enabling you to build other solutions on top of it. It’s providing you the data you need, but it depends on what you then do with it. Without these technologies, you can’t achieve the same solutions.”
The end goal for digital twins
“I am happy to see the digital twin community growing,” says Boss. “In Catena-X we showed that digital twin technology is an enabling technology for sharing data. Of course, there still is work to be done, especially in the context of standardising submodels but the GoLive! of Catena-X in October this year was a very exciting and important milestone for all of us.”
Boss is hopeful that once the industry really begins to utilise it fully, the digital twin technology and its benefits will snowball.
“I would like to motivate every company to just start and participate in our common journey in the automotive ecosystem,” she says. “Just participate in a first use case and build your first digital twins for a select group of your products. The technology is scaleable, whether you have 1,000 twins or millions. The use cases that can be supported and extended at any time. There is really no reason to wait for the overall complete and best model of your product.”