Getting the teams up to speed at Toyota
Restocking US dealer vehicle inventories remains a priority for carmakers after three years of supply chain disruption. That requires a talented workforce that can make and move the vehicles, and troubleshoot with accuracy any holdups in the process. Toyota is tackling that problem with the latest digital tools from Microsoft
Disruption to the production of vehicles caused by the Covid pandemic and its impact on the supply chain mean inventories remain low, a situation exacerbated by capacity constraints across the transport modes used to deliver vehicles in North America.
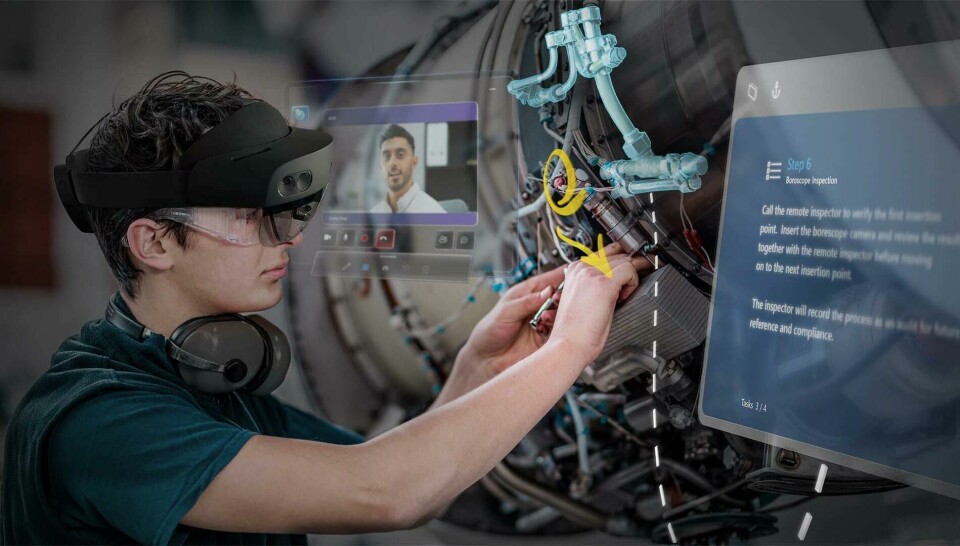
The Covid pandemic also led to a wave of resignations in more traditional frontline industries, such as manufacturing and vehicle haul, exacerbating a demographic trend among a younger generation of workers looking for less arduous working patterns. The pandemic also shut down a lot of schools delaying the qualification of new talent.
Carmakers and their suppliers now need to attract a critical mass of people and train them quickly, as well as speeding the uptake of new more efficient processes in manufacturing and logistics among the experienced workers they have retained. Toyota Motor North America (TMNA) is addressing both issues through the adoption of technology from Microsoft.
The two companies have been collaborating closely over the last five years on the application of Microsoft’s HoloLens augmented reality headsets and the supporting Dynamics 365 software – including Guides and Remote Assist (see box Vision things). Applying the technology to its own manufacturing and logistics processes, Toyota is not only speeding up and improving the quality of training, but also putting the collaborative problem-solving of tasks on a new interactive level that breaks the restraints of time and space.
Ultimately, the carmaker is accelerating one of its fundamental principles – kaizen, or incremental improvement – and applying it to both manufacturing and the value-added logistics services applied in the delivery of finished vehicles.
A new reality
Microsoft’s HoloLens 2 headsets capture and generate holograms from live or recorded information that can be communicated to other headsets. Users can participate in a shared augmented reality regardless of where they are located, meaning problem solving is shared in real time even if it is remote.
The efficacy of using the system is immediately apparent. Anthony Sanor, transformation manager at Toyota Logistics Services (TLS), points out that 75% of annual productivity gains at Toyota don’t come cold from research and development, or IT engineering departments, they come from the people actually doing the manufacturing or logistics-related job on a daily basis.
“We started out looking out at how we could improve training quality and get a higher amount of people trained quicker,” says Sanor “Think of new model launches or the fitment of new accessories – how do we get teams up to speed quicker so we are producing cars with a higher throughput at our facilities and ultimately to the end dealer?”
Asynchronous kaizen
According to Dave Kleiner, manager of immersive technology, Applied Tech Research Lab, TMNA, the advantage of the headset hardware, supported by the Dynamic Guides and Remote Assist software, is that it moves continuous improvement from a linear process with a long lead time to one that is asynchronous and achievable in minutes.
Typically, if an operative in a logistics location has an idea for making an accessorisation process more efficient they submit a form that gets passed through quality and management departments for approval until it is presented in MS PowerPoint and redistributed for training. That can take weeks, according to Sanor.
“Instead, by putting on a HoloLens headset and carrying out a scenario, the team member can share live with other team members at other sites, and with the tools on hand,” he explains. “You can ask questions live and share lessons learned, and that builds confidence.”
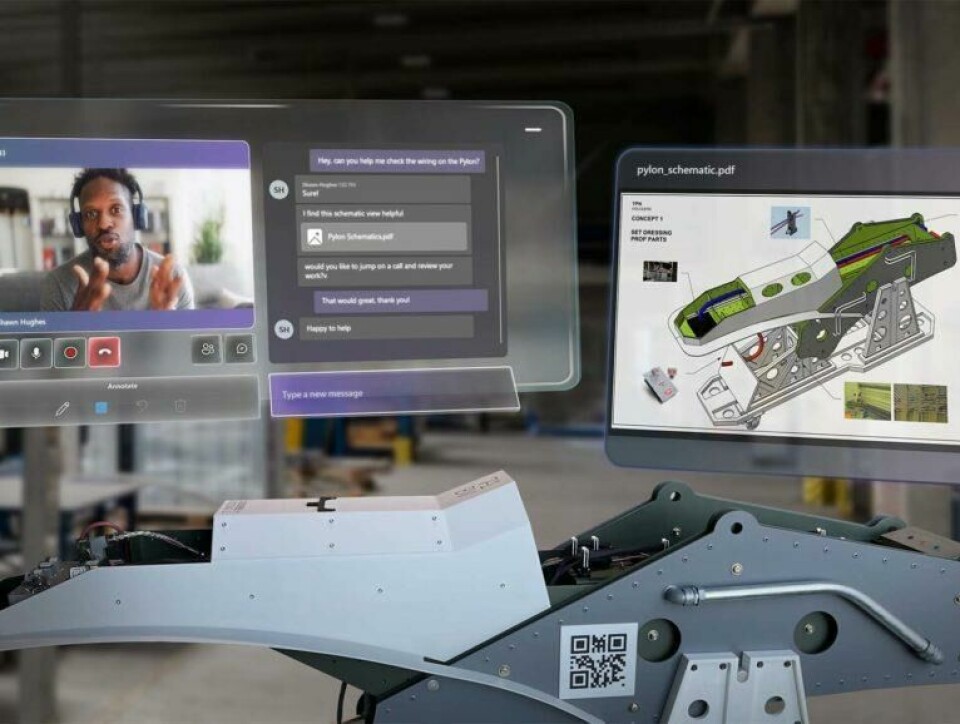
That process of upskilling has been a big success for Toyota with regards to its experienced employees, who already have a strong skill base and working knowledge of process off of which to develop.
“If we give them a new vehicle, and we are introducing a lot of new vehicles to market, they are able to upskill and work on that vehicle quickly,” says Kleiner. “They put the HoloLens on for a session and know the new procedure, they don’t need a lot of time with an instructor, the instructor is in [Dynamic 365] Guides.”
What was also unexpected, according to Kleiner, was how ready that more experienced workforce was to the new technology.
“We thought we were going to get resistance from the older workforce but they were the ones that adopted it quickly,” notes Kleiner. “They see it as a vehicle for their knowledge to have an impact with the rest of the company and with the next generation.”
What was also something of a surprise was that the tool slowed down experienced workers when it was initially tested as a wearable device for improving takt time in the proof-of-concept pilot.
“We found it was a better training tool than it was a day-to-day tool,” says Kleiner. “We don’t expect people to wear this their entire shift, in fact it has a negative effect on employees used like that.”
Set and match
With regard to training employees in new processes, and training new recruits, standardisation of processes is important and the technology promotes this through its immediately wider dissemination through the digital Remote Assist platform.
“From trainer to trainer you get differences, but this is a one-standardised set that is going to be recorded for ever,” says Eric Swei, principal architect at the Applied Tech Research Lab at TMNA. “That is one of the reasons this is working – its inhouse, standardised and the knowledge is recorded.”
Documenting all procedures removes once and for all the risk of recondite inefficiency that comes with experts working in isolation. Procedures passed at one location from teacher to student are now tested across the whole organisation.
“Previously, if you weren’t in Long Beach, you didn’t get that particular knowledge,” says Kleiner. “Now, if you are in Newark, you can now benefit from that one master without travel out there.”
Shared standards
There are also processes for standardisation that the Microsoft tools provide that cannot be written down or put in a PowerPoint document. Sanor points to a specific example, the fitment of protective door edge guards as an accessory, explaining that the seal emits a specific pitch when it is correctly tapped into place. That required one trainer to repeat the process multiple times until a trainee could identify the correct sound.
“That has now been recorded and put into the HoloLens performance criteria for sharing,” says Sanor. “We are looking at ways where the decision criteria [and feedback] are audio or visual… it takes standardisation, which Toyota is already known for, to a new level.”
That is especially important for recruitment and training at time when there is a shortage of labour. It is now less certain that a company will be able to draw from an available pool of seasoned mechanics. The mix is more likely to contain people very new to manufacturing or to post-production accessorisation.
“There are some people who haven’t used hand tools much in their life and you have to get down to the basics,” observes Sanor. “That group is where we are seeing more of the improvement… they can watch the videos that have been pre-recorded in context and it’s a confidence booster.”
Cost-effective empowerment
Toyota says investment in the technology has a good return given it is being joint funded by the manufacturing, logistics and IT departments, with manufacturing investing around $3,500 per headset and IT picking up software licences at a rate of $48 each per month. According to Kleiner the headsets fit seamlessly into operations from an IT point of view, much the same as a PC.
Added to which, Microsoft has the ultimate goal of making its software ‘vendor-agnostic’, Dynamic 365 Guides and Remote Access will work with any other headsets that come on the market in future.
“The second reason we chose the Microsoft technology is that it is the only piece of software out there that has user-generated content… so we don’t have to have an army of consultants or increase the burden on our IT resources,” explains Kleiner.
Toyota believes it is a small price to pay for the empowerment of its workers and that is part of a wider digital strategy to provide continuously improve productivity. Part of solving the recruitment crisis is making the job, whether it be manufacturing or logistics, more attractive and for many that involves greater autonomy and the ability to collaborate.