Pairing up for progress: The advance of digital twins
Offering a more accurate picture of an asset or process than simple modelling systems, digital twins are now widespread in the automotive industry. Soon they may be essential
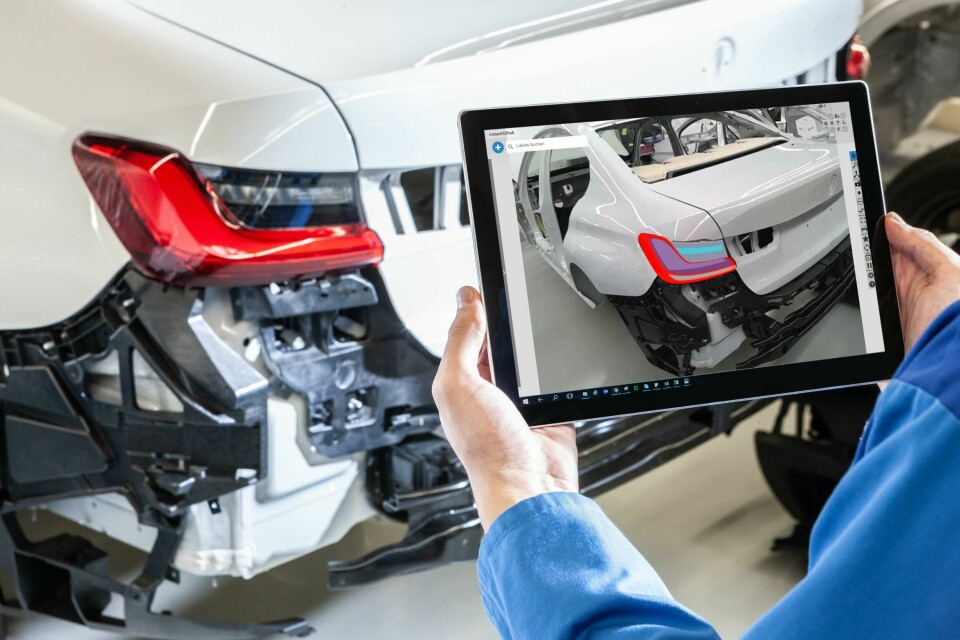
A computer-based tool for process planning, quality checking, monitoring systems and a wide range of other uses, digital twinning is increasingly making its presence felt across the automotive industry. In essence, this is a version of something in real life, such as a piece of machinery, a production line or a supply chain operation, which is recreated on a desktop computer or a tablet.
“Digital twins can give insight into your entire supply chain, enabling you to strategically plan production depending on stock levels and supplier lead times,” says Andrew Aitken, chief commercial officer of software company Lanner. “Through having this knowledge, automotive plant managers can plan production with a full understanding of what materials and resources are available to them, ensuring targets are met.”
Digital twins are now used across manufacturing and warehouse operations to manage material flow, complete the order-to-delivery process and make efficiency and quality improvements in vehicle production. Something may in fact have digital triplets, quadruplets or more for different users or purposes, such as ‘what-if’ planning or the prediction of behaviour under operational changes.
“Digital twins can give insight into your entire supply chain, enabling you to strategically plan production depending on stock levels and supplier lead times”
Andrew Aitken, Lanner
In some cases, the twin may be reproduced via virtual reality (VR) or augmented reality (AR) viewed through special headsets, though there is some debate in technology circles about whether these systems are complex enough to be true digital twins. BMW Group, however, has used virtual and augmented reality for more than two years to assist production workers and to support designers in planning new facility layouts (see second box, below).
Among the benefits of a digital twin is that it autonomously captures and continuously evaluates data and information about processes such as production, design and logistics systems to streamline and optimise a company’s operations, according to Peter Macuš, chief technical officer of Slovak technology and automation firm CEIT.
A digital twin reduces costly errors and provides a comprehensive picture of the production and logistics operations. It also ensures fact-based decision-making in real-time through quick access to relevant and detailed information, and it captures a valuable of feature: enterprise knowledge.
“The digital twin tool enables the creation of system knowledge and its use for the immediate identification of sites with the potential of an added-value increase. The key step here is the reaction that [induces] a positive change in the analysed system,” Macuš says.
Data can be collected, processed and visualised, leading to the evaluation of emerging problems and a rapid response to them, something that Macuš calls reactive control. “If there is enough information available about the historical behaviour of the system, then ‘offline’ optimisation can follow,” he adds.
From there, based on the facts, industrial engineers can optimise the entire system, change processes, alter operations and modify layouts to achieve higher productivity and cost reductions.
With the use of appropriate algorithms, a digital twin can also simulate the system’s future behaviour and generate forecasts. “This results in a predictive response to potential risk situations,” says Macuš.
Making predictions
Lanner has extensive experience within the automotive sector and has worked with OEMs including Ford, Nissan and Kia on the implementation of digital twin systems. For example, Ford has integrated the company’s predictive digital twin technology within its Powertrain Manufacturing Engineering department as the foundation of its own customised platforms, known as the Ford Interactive Simulation Tool and Ford Assembly Simulation Tool.
“These tools have improved efficiencies across Ford’s plants, such as Dagenham [UK], and led to senior management having increased visibility of production and the ability to react to external factors before any problems can occur on the factory floor,” says Aitken.
“The digital twin tool enables the creation of system knowledge and its use for the immediate identification of sites with the potential of an added-value increase. The key step here is the reaction that [induces] a positive change in the analysed system”
Peter Macuš, CEIT
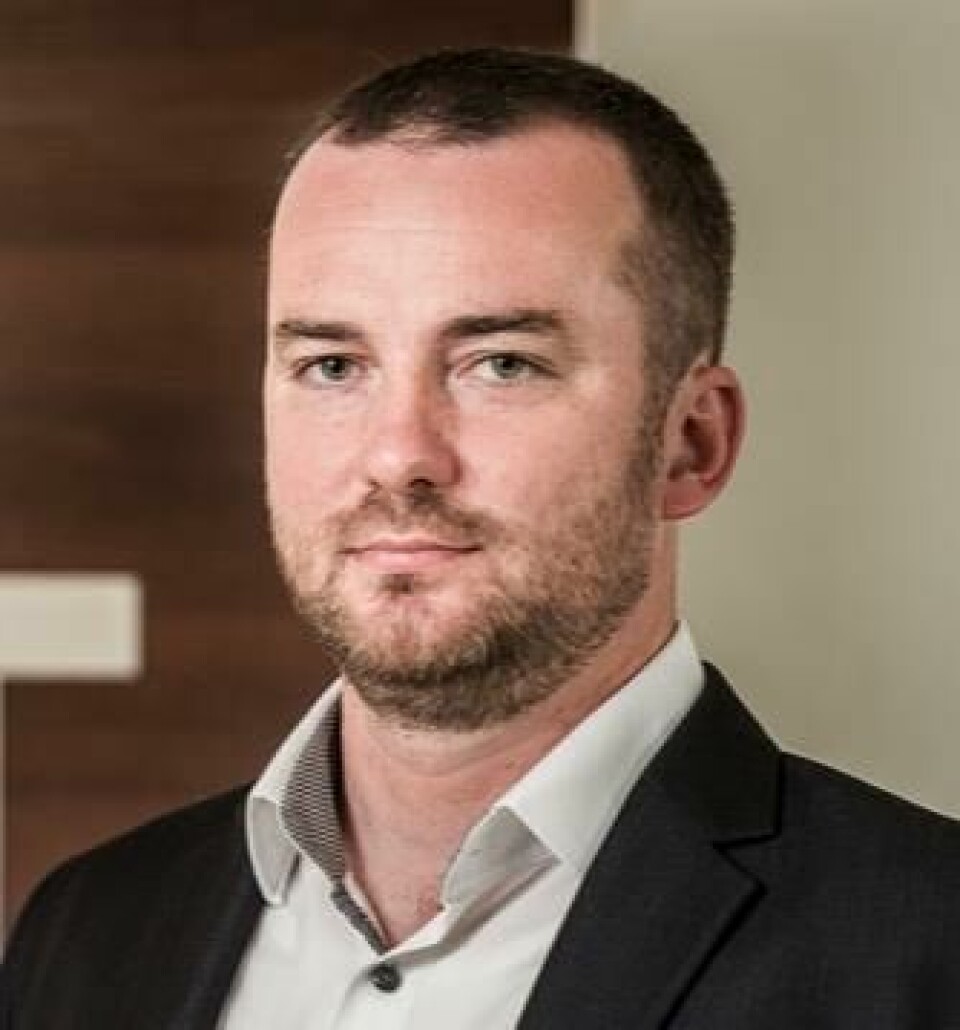
At Nissan, predictive digital twins have been deployed across a wide range of applications, from meeting powertrain production targets to reducing bottlenecks within a bumper paint facility and understanding battery leak test failures.
“The use of digital twins across all these areas has led to significant cost savings for Nissan, as well as effective long-term planning, ensuring KPIs and demands are met,” says Aitken.
Another potential use for a digital twin is as a training tool. CEIT is working to train top management in production quality through a digital twin. “Within the training module, a digital twin production line will be created to visualise the impact of individual input variables on the length of the production cycle,” states Macuš. The advantages include future heads of production being able to try out various ideas in a virtual world and so avoid potentially costly errors in the real world.
In the automotive industry, CEIT has implemented a sensor network in a warehouse to collect detailed data on the position of objects such as pallets, forklifts and automated guided vehicles in real time, displaying the results in 3D via a digital twin.
“Based on this data it is then possible to quickly and efficiently manage the internal material flow and achieve higher efficiency of processes and monitored devices,” says Macuš.
Decentralising capacity
Not only private companies but academic institutions are involved in developing digital twinning technology and applying it to industry. The Fraunhofer Institute for Software and Systems Engineering in Dortmund, Germany, is working on digital twins covering the whole order-to-delivery process for European car and truck-makers.
According to Dr Jan Cirullies, head of its department of digitisation in logistics, current projects include designing a pilot digital twin with a vehicle-maker to decentralise capacity for data exchange across manufacturing tiers.
“The problem is that the OEM has usually only transparency to tier one suppliers, although often preceding suppliers cause shortages,” he explains. “However, suppliers are mostly very reluctant to share capacities, especially with the customer of their customer.
“I expect digital twins to be essential for the success of automotive companies”
Jan Cirullies, Fraunhofer
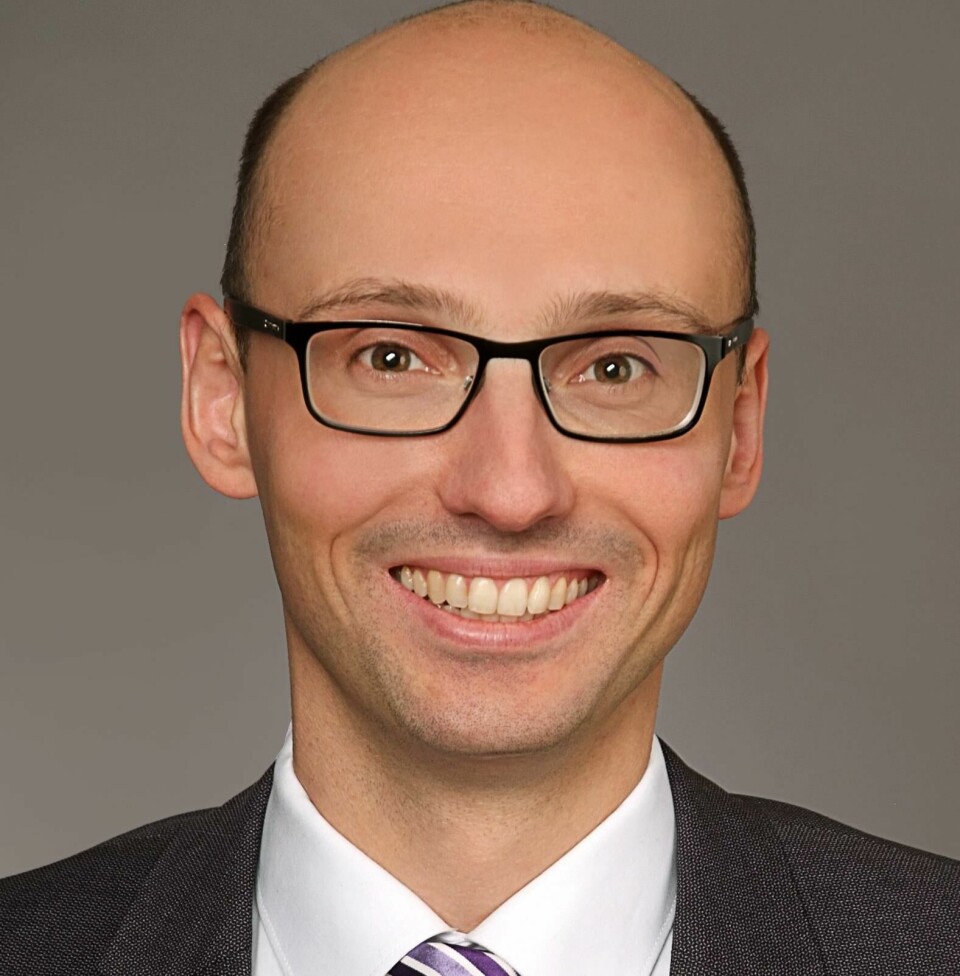
“That’s why we have the assignment to build a shared digital twin for the supply chain based on the international data space, where every participant keeps the sovereignty of his data, and data is propagated in cascades,” Cirullies states.
Commenting on the value of digital twins, Cirullies adds: “From our experience, the benefits are what all companies want: short planning cycles, up-to-event driven decisions, supply chain transparency for proactive decisions, data-driven decision support for both regular planning and exception handling, such as bottlenecks, capacity optimisation in production and logistics, and holistic planning.”
But he also had a word of warning for carmakers. “To stay competitive in value creation, many companies have a deficit in using, linking and managing data. The insufficient digitalisation of processes leads to unnecessarily high costs due to slow or wrong decisions, slow adaption to market requirements or even the incapability to serve customer needs with regard to digital service offers.”
Diverse applications
A ‘Digital Twins in Logistics’ report was released in mid-2019 by German logistics provider DHL. In it, Matthias Heutger, senior vice-president global head of innovation and commercial development and Markus Kueckelhaus, vice-president innovation and trend research, suggest many possible supply chain uses of digital twins: managing container fleets; monitoring shipments; and designing entire logistics systems.
For example, Internet of Things (IoT) sensors on containers can show their locations and monitor damage or contamination. This data can be fed into a digital twin of the container network, which uses machine learning to make sure that the containers are being used as efficiently as possible.
“Digital twins offer unparalleled capabilities to track, monitor, and diagnose assets. They will change traditional supply chains, with a range of options to facilitate data-driven decision-making and collaboration, streamlined business processes, and new business models. We are keen to work with our customers and partners to jointly explore applications in our industry,” says Heutger.
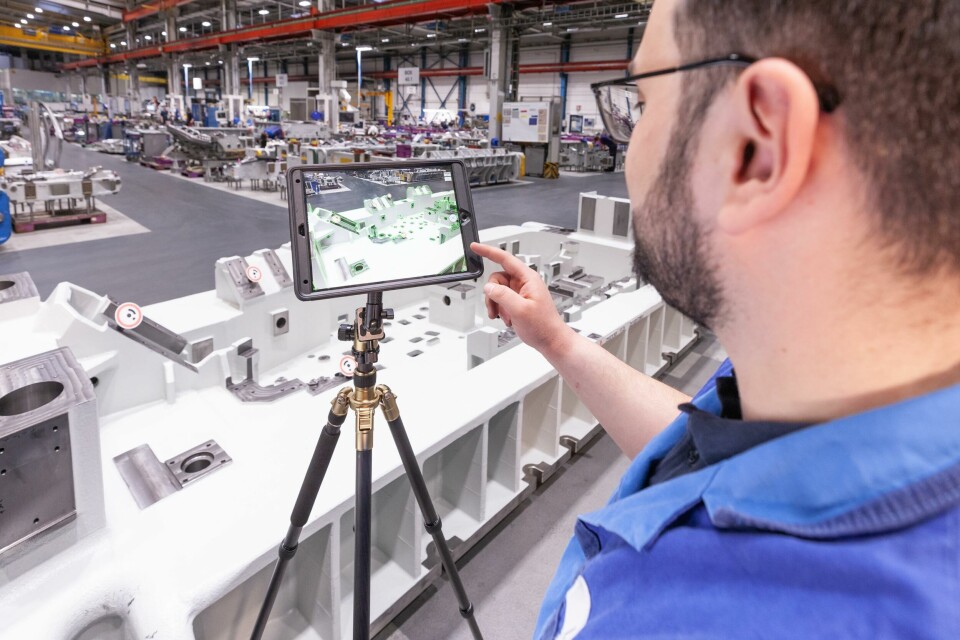
Moreover, digital twins can be applied not only to individual assets or networks but whole ecosystems. For instance, a 3D model of a facility such as a warehouse can be combined with inventory and operational data to keep a check on product availability and machine status, enabling predictions and autonomous decisions about stock and deliveries. Beyond that, major logistics hubs or even global networks can potentially benefit.
With so many applications, not to mention input from a wide range of sources and different functions, it would not be surprising if there were questions over what exactly constitutes a digital twin. But it is generally agreed that it is far more complex than existing 3D modelling, simulation and asset-tracking technologies, Heutger and Kueckelhaus explain in their report.
A true digital twin simulates the physical state and behaviour of the thing or process, such as material flow through a warehouse, that it is replicating. But it is also unique, designed for a specific machine or system and connected to them, updating itself according to real-world changes such as a machine working faster or shipments being delayed. Perhaps the most important quality that sets a true digital twin apart from other computer-based applications is that it provides visualisation, analysis, prediction and optimisation of the machine or process.
Dangers of data
Data is key to having a well-functioning digital twin, as the software providers point out. “As with any output related technology, you also need input. A lack of data, for example, can cause initial problems but these can all be resolved in working with our partners,” says Lanner’s Aitken.
Meanwhile, in a white paper entitled ‘An Introduction to Digital Twin Development’, AnyLogic comments: “Data is required to maintain an up-to-date digital twin throughout its operational life. Indeed, a model must be paired with relevant data for it to become a digital twin. A model without situational data is generic; with data, it is unique.
“The data brings the model alive and delivers its usefulness. Data describing the state of the subject, its environment and how it operates is essential. Without such data it is impossible to verify the model, and as a result, all diagnostics, forecasting and experimentation are compromised.”
“Uniting complex and disparate processes and operations requires a flexible modelling environment, ideally one able to connect differing modelling methods”
AnyLogic
But collecting this data just once is rarely enough. “It must be timely and in agreement with the real-world system it is representing,” the paper stated, adding that this is why digital twins are closely tied to the IoT, with connected devices reporting operational data for processing and analytics.
AnyLogic warned that developing a model of a real-world system “can quickly become complex”, with models expanding into different realms. “Supply chain analysis can benefit from modelling warehouse and retail operations. However, modelling these environments may require different approaches, possibly due to the information available, or the nature of the operations – warehouse operations will usually be modelled differently to network-level supply chain operations.”
The company continues: “Uniting complex and disparate processes and operations requires a flexible modelling environment, ideally one able to connect differing modelling methods.”
Complex and challenging
In DHL’s report, Kueckelhaus cautions that bringing all the relevant technologies together into full digital twin implementation is a complex and challenging task. “Close collaboration between all partners along the value chain is therefore essential to fully capture the potential,” he says.
Cirullies of Fraunhofer and Macuš of CEIT both suggest that persuading companies of the value of adding a digital twin is the first big challenge. “The return on investment calculation is difficult, as a cross-organisational, integrated and well-managed data model, namely a digital twin, is fundamental and essential in any number of use cases,” says Cirullies. Nonetheless, he expects digital twins to become “essential for the success of automotive companies”.
Macuš emphasises the human element amid the focus on technology. “People are an irreplaceable part of manufacturing systems… some industrial companies may still be concerned about introducing their digital twin. However, our experience suggests that the digital twin tool can be a very helpful and, therefore, welcomed technology for employees.”
“Digital twins offer unparalleled capabilities to track, monitor and diagnose assets. They will change traditional supply chains, with a range of options to facilitate data-driven decision-making and collaboration, streamlined business processes and new business models”
Matthias Heutger, DHL
There are also questions about data governance for companies. Executives will ask how it can be read, how they acquire the data required, who is in charge of providing it, who defines its quality and monitors it, and how data from external sources is integrated.
There will also be a need to integrate new data sources into digital twins. “Combining digital twins with other technologies is also going to be a key factor in success, and we are already seeing some of our customers explore these options,” says Lanner’s Aitken. He explains that digital twins and artificial intelligence can complement each other, offering much faster solutions than before.
“Looking to the future, the use of digital twins will only continue to increase. To stay competitive, companies need to be more agile and prepared for market conditions, rather than reactive when a problem occurs,” Aitken states. “Digital twins give decisions certainty and offer significant cost savings at the same time. Soon, if you don’t have a digital twin of your supply chain or manufacturing process, you will be left behind, as competitors move forward in the digital landscape.”