ZF technology is making inbound logistics more efficient and sustainable
Tier one parts and technology provider ZF has put digital technology at the centre of its commercial vehicle product offering and that is helping manage complexity and cut carbon from its own inbound operations
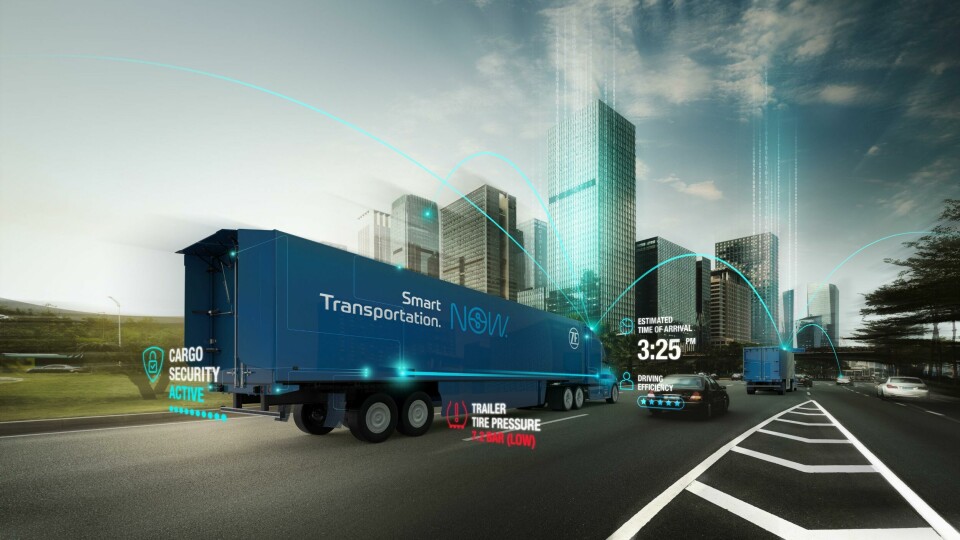
ZF is using multiple large fleet providers to move its inbound and aftermarket material. In terms of operations in the US, Canada and Mexico, including cross-border movements, ZF contracts numerous providers to move material dependent on their regional expertise.
Those providers are organised by Penske, which provides ZF with US-based transport management services (TMS) for all ground transport (excluding small parcel). Penske’s TMS provides routing, optimisation, tendering, tracking/tracing and data collection of all ground transports within the region. Penske routes the shipments to the ZF-directed freight carriers based on shipment details and established freight contracts.
ZF is the largest commercial vehicle technology provider in the world and says it is seeing more freight providers upgrading their fleets with its customers’ best new trucks and trailers. Those trucks and trailers include technology from ZF designed to decarbonise mid- to long-range trucking.
“It’s gratifying to see our work coming back to us in a virtuous circle of sorts – the freight forwarders we use are hauling our product to our customers but also relying on our technology to keep their trucks moving efficiently,” says a spokesperson for ZF.
Decarbonisation up front
In choosing its logistics providers ZF factors sustainability into its tender process prior to awarding contracts.
“We identify providers with sustainability practices and certifications, such as SmartWay, a partnership between EPA [US Environmental Protection Agency] and thousands of businesses and organisations that aims to reduce freight emissions, environmental risks and energy use, and invite them to our tenders,” says ZF’s spokesperson.
As carriers are onboarded, they sign and agree to the ZF supplier code of conduct, which outlines the company’s sustainability requirements. ZF says this ensures that awarded carriers complement ZF’s efforts to improve end-to-end sustainability.
Over in Europe earlier this year ZF contracted logistics provider Duvenbeck to carry series production gearboxes and building components from Saarbrücken in Germany for onward delivery to ZF’s customers and for carrying back empty containers to the factory. The logistics provider is using a fleet of 40 trucks running on biogas provided by viGo Bioenergy, which is helping to reduce CO2 emissions by up to 8,000 tonnes per year.
“We are tackling the sustainability challenge in many ways as we focus on meeting our CO2 reduction goals and actively seek opportunities to apply best practices from around the world to our supplier freight,” says its spokesperson in the US.
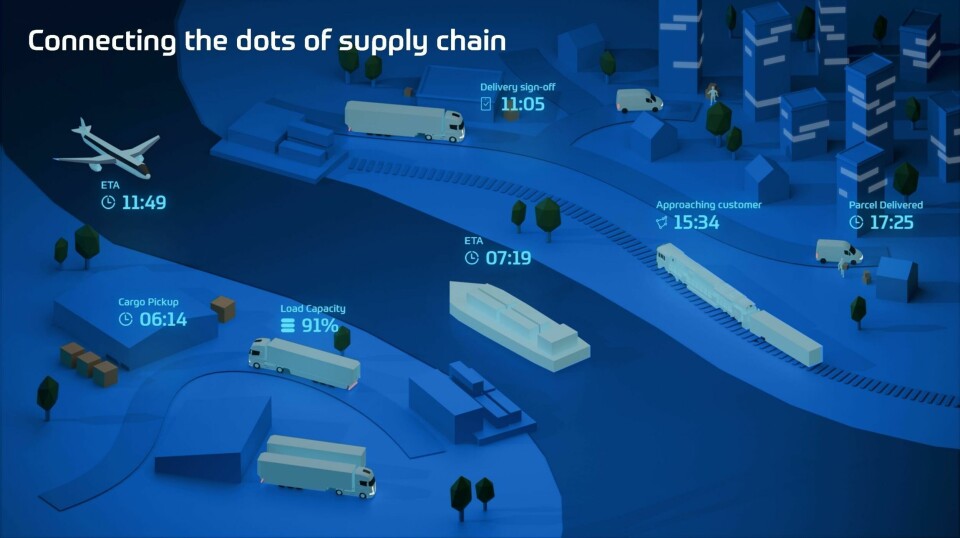
Digital metrics
Greater efficiency in transporting its goods also brings savings and ZF is providing a range of digital technologies to enable this. These include real-time freight monitoring and asset tracking technology for transport companies.
ZF’s digital fleet orchestration platform for commercial vehicles, called Scalar, helps users increase truck and trailer utilisation, optimise routes, track locations, improve preventative maintenance and reduce unscheduled downtime. It also provides visibility into asset performance. Logistics companies can make decisions more quickly with accurate results using the data that the Scalar platform provides, according to ZF.
“For example, vehicle health monitoring identifies potential problems before a failure happens, so a deteriorating part can be replaced during scheduled maintenance instead of failing during operation and causing unscheduled downtime,” says the company’s spokesperson.
Other advantages, according to ZF, are on-the-road monitoring to increase driver accountability and encourage safe driving habits. Logistics providers can then coach drivers using historical driving records to maintain operational safety. By using data to generate reports and reduce administrative load, the Scalar technology also helps users stay in compliance with government regulations.
According to the company, Scalar is also utilising on-road data to provide data on how ZF braking systems and other intelligent truck parking (ITP) systems are being used by its customers. ZF is using the metrics to inform its own research and development, and warranty coverage teams to improve products and services.
Brake alerts
One notable application of Scalar is to report ABS braking faults in real-time, alerting operators to any issue occurring with a trailer’s braking system.
“Fleet operators can assess the severity of the fault code and route the trailer to a service facility as needed,” says its spokesperson. “This eliminates the need to bring the trailer into a service shop to diagnose the issue, helping to reduce downtime.”
ZF has announced a collaboration with Manac, a leading North American manufacturer of specialty trailers, to integrate its Scalar fleet orchestration platform, Scalar EVO Cast telematics hardware and intelligent ABS system (iABS) on its smart trailer technology, SmartHorizonTM.
Other ZF ITPs and integrated partner products used for maintenance, such as brake pad wear indication, tyre pressure monitoring and light out detection are installed on the trailer and reported through Scalar. Alerts are generated to provide real-time status, assisting fleet operators with maintenance of the truck and trailer.
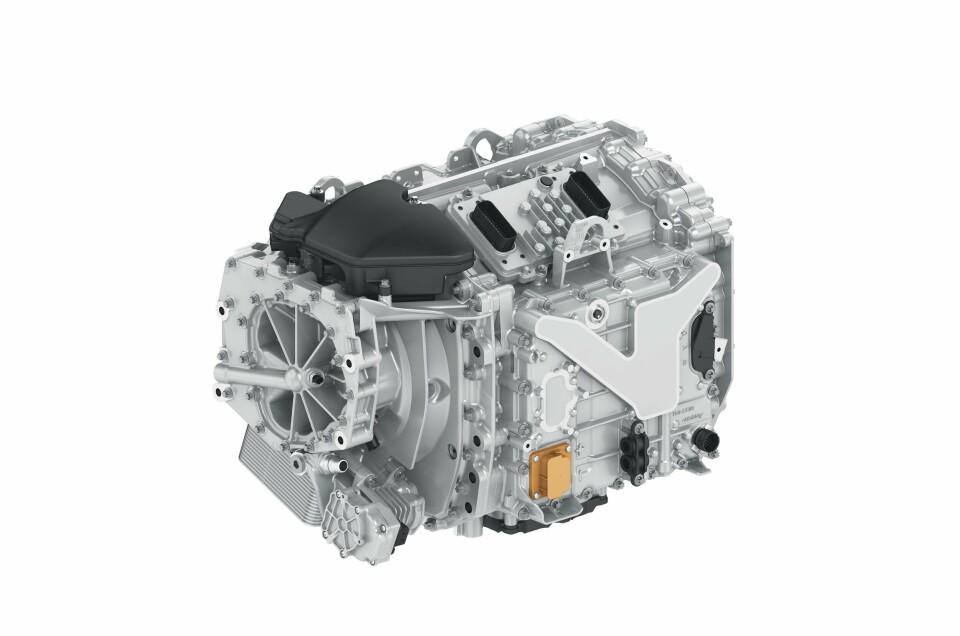
In addition, ZF says its Braking and e-Drive Synergy Program harmonises the electric driveline and braking functions to recuperate energy under full stability control to improve efficiency, safety and comfort while reducing the total cost of ownership (TCO).
The system works by combining ZF’s next generation e-drives with its mBSP XBS advanced braking system to leverage the capabilities of the e-drive to help control acceleration and braking. In doing so, the company says, the system maximises energy recuperation to recharge the onboard batteries during driving, effectively extending the vehicle’s range. The system also provides ‘one-pedal-drive’ functionality, increasing driving comfort especially in low-speed manoeuvring, such as for yard vehicle applications or urban driving.
In March this year ZF and Noregon, the commercial vehicle diagnostic and repair firm, announced an agreement that will allow Noregon to use ZF’s Scalar platform to incorporate smart trailer data into its remote diagnostic application, TripVision. This integration will enable fleets to monitor their tractors and trailers in real-time from the same application, with access to the necessary information to quickly make impactful maintenance decisions. ZF said the service can provide unique insights using proprietary braking system data developed from years providing braking systems, and associated repair instructions.
AI supply chain strategy
Back in 2021, ZF worked with Microsoft on the launch of its ZF Cloud data platform with the aim of improving efficiency and global supply chain management through the digitalisation of all its industrial, operational production and business processes. Since then, it has made significant progress toward its Manufacturing 4.0 goal.
“In the area of supply chain and logistics specifically, we are developing an AI toolbox we call SpAIder,” says ZF’s spokesperson. “This Azure-based strategic platform assists human controllers, managers, and executives in the automation, optimisation and control of the entire supply chain. It provides linked AI tools to streamline and optimise planning processes, to manage inventory and to monitor the state of the supply chain.”
According to ZF the toolbox provides automatic planning processes and visibility across the supply chain which helps with risk management and building supply chain resilience. It also helps cut energy consumption and decarbonise logistics through better resource use and provides simulations and forecasts to foster better decision making. It also helps reduce cost through improved cash flow by supporting predictable production, avoidance of dead stock and optimised use of transport.
Managing complexity ahead
ZF expects inbound logistics networks to increase in complexity for multiple reasons. They include government regulations on tax codes and customs, border crossing, localisation efforts and security, to name a few.
“We believe the complexity challenge is here to stay and we need to continue to be flexible and adjust to the changing environment driving sustainability. This is why building digitalisation in logistics with the ability to react quickly to changes in the supply chain is critical,” says its spokesperson.
As mentioned, ZF is using its TMS to manage fluctuations in volume and make the most of opportunities in moving material between FTL/LTL and milk-runs, thus minimising trailer movements within the network. It is working closely with its carrier base to further optimise movements across the network and leveraging tools that provide real-time visibility into the supply chain to help identify areas of improvement.
“Another advantage that we are finding is paying dividends is our digitalisation transformation with business intelligence to bring added visibility to our network,” says its spokesperson. “This is enabling us to see very clearly all touch points for freight movements/communication from carriers. This has minimised manual input errors and is increasing our efficiencies within our inbound logistics.”