VW employs AR to improve lineside logistics at Chattanooga
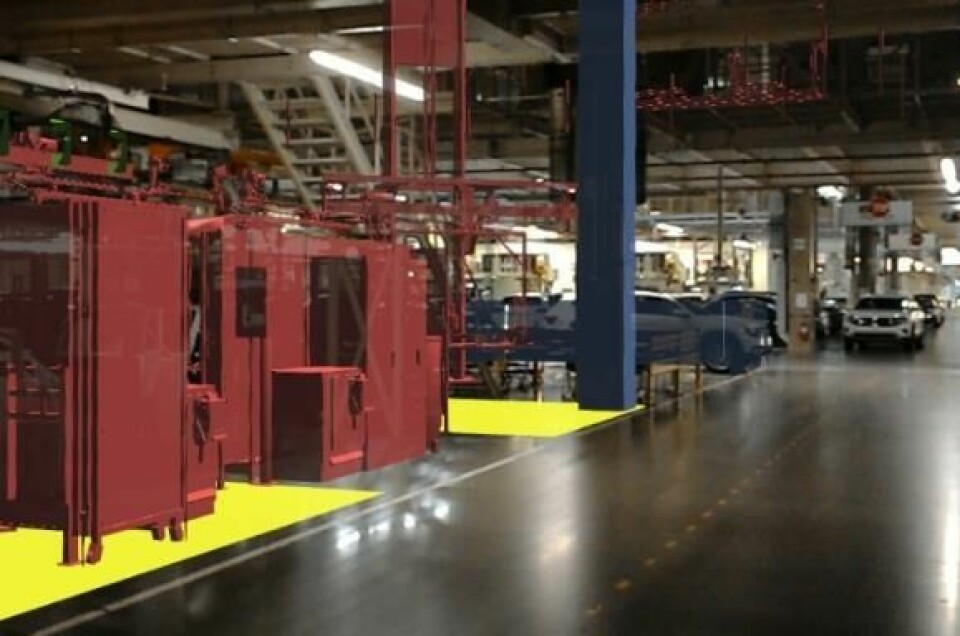
Engineers at Volkswagen’s Chattanooga factory are using specially developed augmented reality (AR) goggles to help spot potential problems with new production lines they are designing for vehicles at the Tennessee plant.
“As this is a brand-new tool, we’re still gathering data on exact gains … But it has already helped spot issues like interference on small parts that were hard to find previously and can often slow down new machinery installations,” a company spokesman told Automotive Logistics.
“As we add production of the upcoming ID.4 electric vehicle to Chattanooga, we expect this tool to play an important role.”
For now, the immediate focus is on the production ramp-up of the new Atlas Cross Sport.
The AR goggles were developed in six weeks by VW’s virtual engineering laboratory in California, based on requests and feedback from technicians in Tennessee.
By building the system in-house, the company had more room to manoeuvre and improve quickly while working with sensitive data, said Frantisek Zapletal, who heads the laboratory. “If we had done this with external partners, it wouldn’t have been as flexible or as fast,” he added.
The system helps designers see individual parts as well as how existing and future equipment could interact in a real environment.
While virtual planning and software design for vehicles and factory machinery has been standard for years, the company points out factory-floor AR goggles give engineers the ability to see how the pieces will fit together in the real world.
“This helps us to make decisions quicker, and spot potential issues sooner,” said Steffan Nunn, digital factory specialist at Volkswagen Chattanooga. “As we integrate new models into the existing factory, we need to make sure our virtual design data matches the reality in the plant.