Ready for any crisis, anywhere in Volkswagen Group’s supply chain
Crisis management has become de rigueur for Group Logistics, and has led to changes in capacity planning, visibility and mindset across the company.
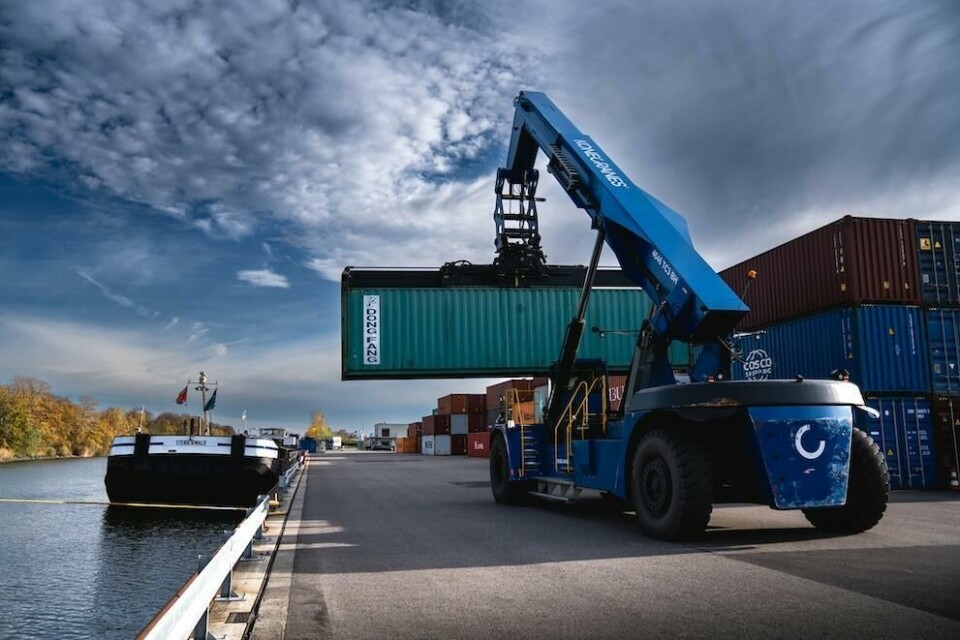
The semiconductor crisis taught Volkswagen Group that it needed to have much deeper visibility across its supply chain, which it is achieving through mapping, supplier communication and digitalisation
Volkswagen Group Logistics series: Simon Motter on securing the supply chain
-
How Group Logistics is overcoming crises and shaping Volkswagen's future supply chain
-
Ready for any crisis, anywhere in Volkswagen Group’s supply chain
-
The electrifying influence of logistics
-
The many roads, fuels and tech leading to zero emission logistics at Volkswagen Group
-
The quest for one source of truth in Volkswagen Group’s digital supply chain
Volkswagen Group Logistics continues to face many logistics disruptions, whether in shipping, operations and vehicle logistics. But whilst the company has shown strength in mitigating these issues, its managing director, Simon Motter, wants to ensure that the group can better anticipate and respond to future issues.
One clear example was in the chip shortage. With supply so limited, Group Logistics not only led on allocating semiconductors to plants and vehicles, but its team drilled down into each stage of the supply chain and production process to define the controllers that might go into a particular part. “It was very complicated, but it was important to work together with our counterparts in procurement and with our suppliers,” he says.
Group Logistics continues to extend that detailed visibility across the tier-N supply chain, both for critical components like chips, controllers and electronics, as well as strategic materials for battery cells and packs. New order and transport management systems will also help further, while Motter sees opportunities in shared data networks like Catena-X, a data-sharing consortium in which Volkswagen is a leading member.
Updating demand-capacity planning for vehicle logistics
It has been important to bring this detailed analysis to addressing bottlenecks in logistics capacity, too. The most critical area in 2023 was vehicle distribution and logistics, with gaps across all transport modes in Europe and for shipping. The reasons are well documented, including a shortage of ro-ro ships, port yards full of unmoving vehicles, and a significant disruption to rail services from ongoing works to the network, especially in Germany.
Group Logistics took several direct measures, including transferring vehicles off the railways and onto the road to ensure delivery, even where it led to higher transport costs and emissions. Furthermore, it commissioned and controlled more direct truck capacity. “It was not always a favourable measure, but as capacities were so scarce, it gave us more access and control,” says Motter.
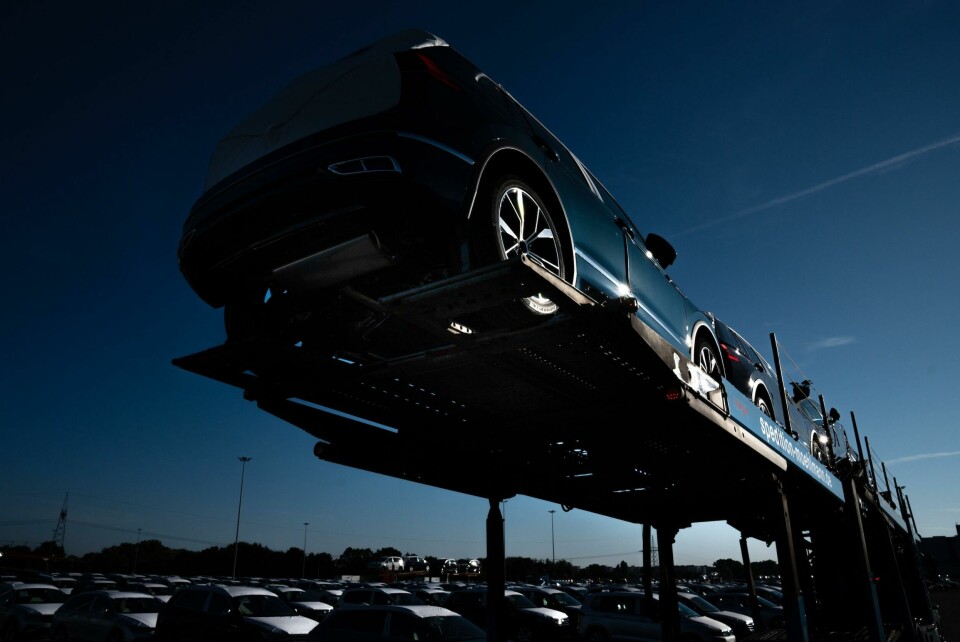
Group Logistics has taken steps to improve digitalisation of its vehicle logistics, including order management, demand and capacity planning and partner management
Group Logistics, which already charters ro-ro vessels, also increased services and capacity for routes between Europe and North America, for example. “We can already see the trend that in some particular cases we are going deeper into our own capacity,” he says.
But although taking more control of vehicle logistics flows has been necessary, Motter emphasises that he would prefer to work with external logistics providers wherever possible, as they are best positioned to run a balanced network. That is why Group Logistics has invested in improving partner management, for example in vehicle logistics capacity planning across its network.
”We are setting up processes and systems so we can derive precisely from our production and sales requirements what we will need for vehicle logistics, and where our capacity gaps might be in the future.”
Simon Motter, Volkswagen Group Logistics
Motter admits that because vehicle logistics capacity has historically been readily available, Volkswagen only had a rudimentary ability to forecast capacity for vehicle logistics services, and a limited view on the specific services the group needed by product, regions and different transport modes.
”Now, we have transferred some of our tools and processes for forecasting and planning from inbound parts to vehicle logistics,” says Motter. “We are setting up processes and systems so we can derive precisely from our production and sales requirements what we will need for vehicle logistics, and where our capacity gaps might be in the future.”
The delivery results in the fourth quarter of 2023, confirm improvements in both capacity availability and the carmaker’s planning. Motter says that, although the crisis has subsided, the company has come away with a stronger understanding for vehicle logistics operations, as well as the impact that it has on positive net cash flow when vehicles move more reliably through the supply chain.
“It has become an important goal for Group Logistics to influence our finished vehicle inventories and thus capital by managing and controlling lead times more effectively and in more detail,” he says.
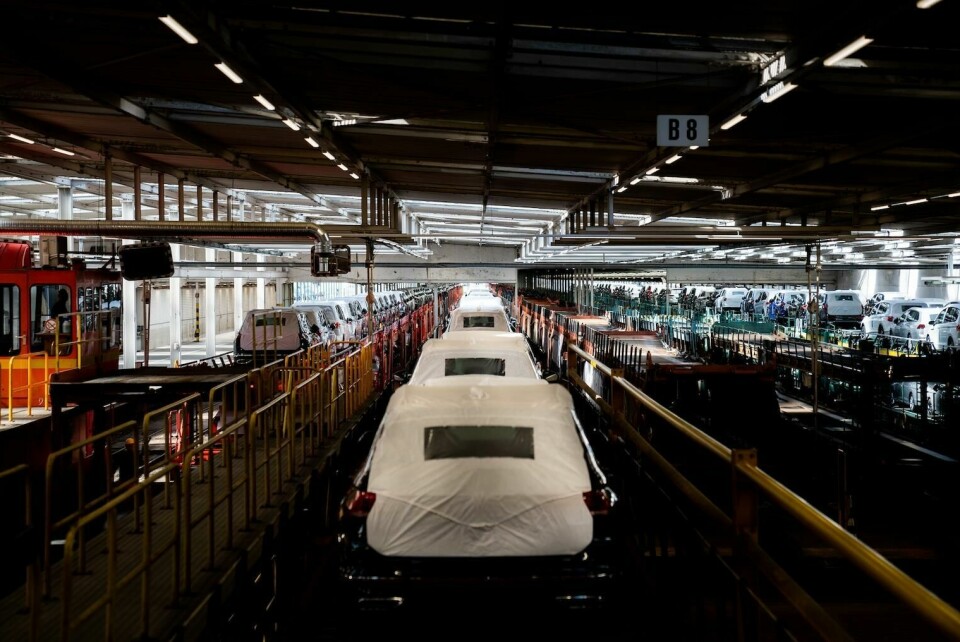
Group Logistics has taken extra measures to mitigate disruption, ranging from trucking goods from China to Europe and moving empty rail wagons closer to plants ahead of rail strikes
Developing a crisis-ready mindset for logistics
While Volkswagen Group Logistics has made strategic investments and changes to mitigate supply chain disruption, Simon Motter doesn’t underestimate the collective experience that logistics experts have gained in recent years in crisis response.
In managing issues in the Red Sea, for example, which has added around 14 days of transit time from Asia to Europe, the carmaker moved quickly to divert cargo and inventory on this route. It also didn’t hesitate to take even more creative measures together with its suppliers.
“We have managed this well, but that has included using exceptional transport, including special flights, and even using trucks from China to Europe,” says Motter.
In fact, it wasn’t the first time that the group has resorted to trucking from China. But having such a plan B was a key asset for the company, he says. “We knew that it was possible, and we could take the solution out of the drawer and make sense of it.”
Experience also played a role in helping to mitigate the impacts of ongoing strikes on the German rail network. Working together with brand and plant logistics teams, Group Logistics increased inventory where required, and diverted material from rail to trucks. In anticipation of strikes, the plants brought empty rail wagons close to the sites so that it could load the vehicles on the tracks whilst the trains weren’t running and use them to buffer the inventory for several days before the strike was over. “It was a great team effort of all involved logistics areas”, comments Motter.
Advanced data analytics, digitalisation and better supply chain visibility are all essential, but Motter also praises the ability of these employees to stay calm under pressure. That is important because the situations won’t always be the same – the Red Sea disruption requires a different response to the blockage of the Suez Canal, for example – but with the right approach and partners, solutions can be adapted.
“All employees in logistics – not just in Group Logistics but across operations in the plants and at our partners – have been tested again and again, and that has instilled a mindset to create alternatives,” he says.