Executive summary: Blue skies over Bonn as logistics returns to growth
Vehicle sales and production are rising again in Europe, while supply chain complexity is driving more demand for logistics and better systems. But many risks remain both within the industry, and on Europe's periphery. Additional reporting by Marcus Williams and Zoë Apostolides[sam_ad id=6 codes='true']
Although the Europe conference was held at the same location in Bonn, Germany and during the same week of March, delegates who came the past two years will have noted stark contrasts. Last year, executives travelled from across Europe through a late winter snowstorm, with temperatures in Bonn below freezing. This year, there was barely a cloud in the sky, the sun glimmering over the river Rhine and the air as warm as 19C.
Weather may be a clichéd metaphor for discussing the economic climate, whether a ‘storm cloud’ for recession or ‘sunny skies’ for growth – however, in the case of European automotive logistics, it is an irresistible comparison. Last year was the sixth consecutive in which new vehicles sales declined in Europe (reaching a 20-year low), with production and exports also stagnating. This year, however, has been better. Sales in the European Union have been growing steadily, and current forecasts call for increases for the rest of the decade.
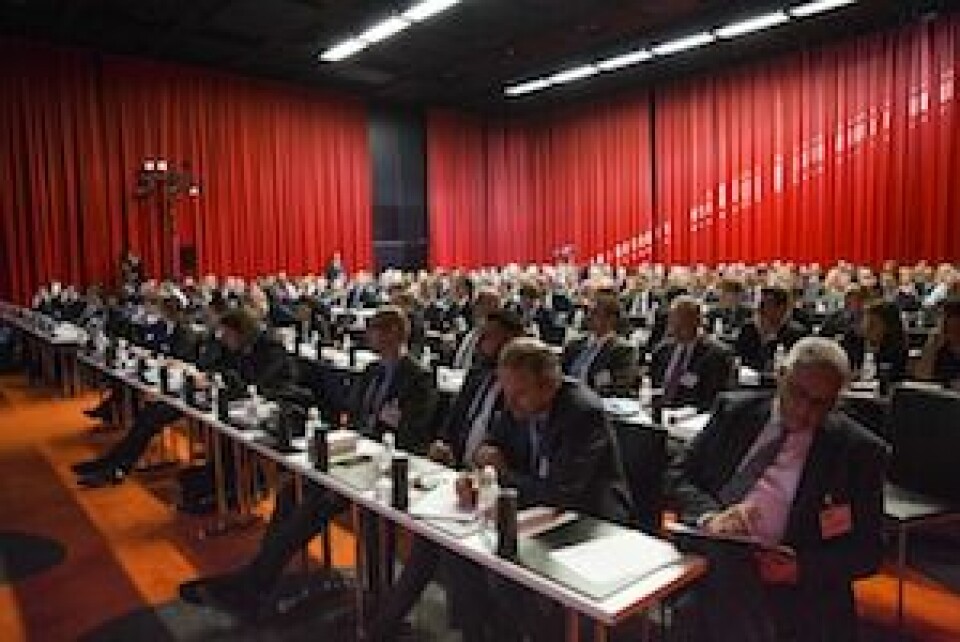
Michael Gartside, senior manager of the Autofacts strategy group at consultancy PwC, predicted that sales would rise around 4-5% this year to 12.6m, climbing steadily over the coming years to around 14m units in 2016 and 15m by 2019. While growth will be uneven, even hard hit southern European markets such as Italy and Spain are heading back up a bit.
Production should be even stronger, rising 600,000 units this year to 16.5m units and climbing close to 19m by 2017 or 2018, above the 18.8m peak in 2007. Production capacity utilisation should recover to 85% in the coming years, as OEMs localise more models in Europe at the same time that a number of large factories are closed, including for Opel, Ford and PSA.
An overdue sunny day for logistics
18 March 2014: Follow the links below for our comprehensive coverage of all the news and happenings from throughout the conference.
Watch videos of the key presentations here
- View the results of the live voting sessions
- VW efforts to cut emissions in logistics
- Healthier times ahead for Europe
- Will Russia be left out in the cold?
- Audi wants visibility on logistics cost, flows
- Opel seeks ‘total enterprise cost’
- Light and darkness in IT visibility
- Just in time frappuccinos
- JCB cuts emissions with dual-fuel, multimodal logistics
- Hertz consolidates outbound logistics
- Lohr and CTM to build convertible trailers
- Lohr restructures North America business
- OEMs buying too much packaging
- Excess inventory costing Europe millions
- Save €30m outbound with B2B standard
- Damage down, catastrophic loss up
- OEMs should use ‘floating warehouse’
- Chep unveils intercontinental system
- Overheard at Automotive Logistics Europe
The outlook is also relatively ‘sunny’ for logistics providers. Sales and production growth will bring needed relief to logistics providers, while the European supply chain is increasingly complex, driving demand for logistics volume, expertise and IT systems. Opel/Vauxhall, for example, has recently implemented new order management functions to help it improve its material and production plans. With the increase in part number and production locations, carmakers such as Audi and tier suppliers like Magna stressed the importance of logistics visibility and good systems in managing and controlling transport orders.
Indeed, during a live survey conducted during the conference, IT systems and software came top of the list for the best means of improving automotive logistics, with 34% of the vote.
The complexity is also driving more transport routes and multimodal services, according to Bram Ewals, chief executive officer at Ewals Cargo Care. Those solutions are also subject to change at short notice even within the lifecycle of one car model. “If we were to design a blueprint today we actually know by default that it might not be the right one tomorrow,” he said. “As a logistics provider it is a challenge to embrace the volatility of the customer and ask what we can do to follow them. We see it as a fact of life.”
Ewals added that despite the constraints logistics providers work within, better information and forecasting solutions were increasingly available.
Changes were perhaps most evident for the Volkswagen Group, where there has been a group-wide project to better consolidate flows, as well as to reduce carbon emissions by 25% by 2018 (from 2010 levels). Andrea Eck, general manager for outbound logistics at the Volkswagen Group, said the company was looking at better use of crossdocks, milkruns and direct runs between supplier and plant. The group is also looking to improve multimodal logistics, as seen in VW’s recently completed multimodal complex at the inland port located next to its Wolfsburg plant in Germany.

“There is a packaging station there, storage for cars and a port,” Eck explained. “These are three functions together and we started to optimise the network in the transport of cars and reduce the distance and therefore the emissions. We also package parts for overseas companies.”
Jens Tilgner, head of material transportation at Audi, also outlined how the carmaker was moving towards a system of consolidation centres to help synchronise the supply chain and improve truck utilisation. He added that he wanted to see all of the information within the transport network in a web-based control tower with visibility over transport orders and operations.
Clouds on the horizon
But despite the volume and complexity increases across Europe, there were many ways in which the good weather in Bonn could be seen as a false promise. While growth has returned to the European Union, the uneven recovery may reinforce some divisions across the continent’s wealthier and poorer regions. It is also off of a low base, while Gartside said that he doesn’t think Europe will ever reach 2007 sales levels again. The factory closures will help utilisation, but will certainly bring pain and shifts in the supply chain.
"I think the logistics community is busy trying to build its own world rather than looking at how we can really support value stream optimisation" - Paul Lemoine, Magna Exteriors & Interiors
Furthermore, the crisis between Russia and the Ukraine only highlights the worries at Europe’s periphery. Even if a resolution to that issue can be found quickly, the Russian market is currently struggling, as is Turkey’s. Investments made by logistics providers and carmakers in these regions could be at risk.
Many at the conference complained about familiar issues such as cost pressure and contract terms. Years of decline have left some providers reluctant or unable to invest in equipment and systems despite rising demand.
More fundamentally, others alleged, not all players are willing to make the changes necessary that would benefit the ‘total supply chain’.
“I think the logistics community is busy trying to build its own world rather than looking at how we can really support value stream optimisation,” said Paul Lemoine, director of world class manufacturing at Magna Exteriors and Interiors.
The idea of eliminating transport might rankle those in the business of providing exactly those services, for example. “You don’t ask frogs to drain the pond,” said Bruce Arlinghaus, an independent consultant. But he felt that the biggest barrier to change was often the internal politics at the OEM and not the fault of suppliers or service providers. Others thought it was short sightedness at many companies.
“I’ll guarantee you one thing, when the OEMs or tier ones do make a change to their supply chain they won’t remodel it,” said Mark Ellis, global industry director for automotive at Geodis Wilson. “They give a request for a service to add on to the existing one and simply send it out as a tender. As an LSP you can never offer an innovation that means an increase in price even if it promises to save them a huge amount of money in the overall process.”
Smashing T-Rex bones
Some pointed to issues of misalignment in how targets and rewards are set. Dr Michael Kluger, vice-president of the commercial division at Neovia Logistics, used the example of engine parts that might be made close to a vehicle assembly plant, but must first be shipped to another continent where the engine is built.

Kluger offered an anecdote from the author Bill Bryson, about early archaeologists searching for dinosaur bones who realised farmers were often turning them over in their fields. They offered money to farmers who gave them their findings. However, they paid the same amount no matter the size of the bone, leading farmers to smash up even the largest remnants they could find.
Kluger, who has worked in automotive logistics for nearly 30 years, said that the automotive supply chain was full of such flawed incentives. “We’re smashing up T-Rex bones everyday in the supply chain because are targets and incentives are not properly aligned,” he said.
On a better path
There were nevertheless signs of improvement in the logistics landscape at the conference, including the ways OEMs and providers work together. Andreas Ginkel, director of logistics for Opel/Vauxhall, said that the carmaker’s outsourcing of logistics management to Gefco last year had been making progress. For example, Gefco and Opel have implemented a freight audit and pay system that has standardised invoicing across GM’s entire carrier base in Europe. “It’s the first time that we’ve ever had such a system in place,” said Ginkel.
He admitted that the GM-Gefco project had not yet realised its full potential, and that it was too soon to make full assessments. “We knew when we started this project that we wouldn’t accomplish everything we wanted by 2014,” he said.
GM is in the midst of a major project to reduce logistics cost by $1 billion over the next four years from its global logistics budget.
Marzell Bandur, director of supply chain planning at Opel, said that the carmaker had been improving its approaches for understanding ‘total enterprise cost’ in the supply chain. This has lead to redesigns in packaging and supply flows, including more consideration for logistics costs.
Marzell Bandur says that GM has improved its total enterprise cost approach in the supply chain
This, he said, required more planning across the group's operations; he also pointed out that supplier relocation and double tooling for certain components have become increasingly common.
Opel has also made recent strides with a new 'order slotting' system together with software provider flexis.
Wake up and smell the coffee
The live voting survey revealed that 55% of participants thought that automotive logistics was still leading edge compared to the logistics of other industries, but mainly because of historic innovations (such as lean, just-in-time, etc) and not for current developments. But the conference offered the opportunity to look beyond the world of automotive, including presentations from the food and beverage sector, as well as the manufacture and distribution of rolling stock and two-wheelers.
Jan Huijgens, senior manager of logistics for the European region at Starbucks, outlined a network that includes 2,000 stores (including more than 700 in the UK), which are served with more than 1,200 stock keeping units. The material flow is made up not only of coffee beans, but also store supplies (including cups, mugs, napkins, etc), food, tea and merchandise.

The coffee is sourced from South America, Africa and Indonesia, with some supplies also coming from the US and most merchandise from the Far East. Starbucks, which has a roasting plant in Amsterdam serving all of Europe, runs a disciplined and fast-turning order management process. Most stores in the core markets order supplies everyday, which they receive several days later.
“We are measured on perfect order fulfilment,” said Huijgens. “Our product has a perishable demand and if we are not accurate in our forecasts and reliable in our delivery, we put our businesses at risk.”
Huijgens who joined Starbucks in 2009 following a career in automotive supply chain and logistics, was reluctant to label the company’s logistics as more innovative than those of automotive. Many of the processes and dynamics of the industry are similar, including a fast-turning distribution and crossdock network. Indeed, the order fulfilment parameters are similar to service parts in some ways.
He did, however, point to the complexity of moving goods that needed special storage or refrigeration, and the importance of velocity in a supply chain with a product that must be kept fresh. But he also acknowledged that the food and beverage industry is still learning the ‘lean’ mindset that is so ingrained in the automotive industry.
Whichever way the wind is blowing
The lessons from Starbucks and others at the event suggested that automotive has both plenty to learn, as well as things still to teach. Interestingly, Huijgens from Starbucks, as well as a delegate at the conference from Amazon Logistics, confirmed that each of their companies had supply chain and logistics representatives on the board of management. Such a function is rare in automotive, despite its cross-departmental nature.
"Logistics needs to be thought of as cross-functional: it's as much about trying to keep customers, manufacturers and suppliers all happy,” said Levent Yuksel, plant group manager for global logistics at Jaguar Land Rover. “We should be putting a logistics person on each company's executive board. This would give a competitive advantage. We shouldn't be thinking 'logistics is a cost and a waste.'"
While such debates over logistics management or the relationships between OEMs and providers will probably stay unresolved, the conference showed signs of progress in the way carmakers analyse their manufacturing and supply chain decisions. Meanwhile, rising complexity in part numbers and transport routes have forced many to pay closer attention to their logistics budget and operations.
l to r, Andreas Ginkel from Opel/Vauxhall; Matthias Schulz, Ford Europe; Levant Yuksel, Jaguar Land Rover
“We saw it in the US during the crisis, and now we’re seeing it in Europe, that you have to match capacity to meet demand,” said Matthias Schulz, director of material planning and logistics at Ford Europe, citing the importance of adjusting capacity to demand both for production and in the supply chain. “That’s vital for our industry and the overall supply chain.”