BMW: Getting connected for a new era of distribution
BMW’s vice-president of vehicle distribution Ulrich Wieland (right) and head of global vehicle dispatch and transport Mathias Wellbrock (left) talk about how connected car technology could transform the OEM’s outbound operations over the next decade
Few carmakers have seen as much change and success over the past decade as the BMW Group. It was in 2005 that the Bavaria-based OEM surpassed its rival to the west in Stuttgart as the world’s largest luxury brand. That proved to be the starting point rather than zenith, as BMW has kept the top spot from Mercedes-Benz and maintained high profit margins. Since 2005, sales and production have risen by 800,000 units, to 2.1m cars per year, while the BMW brand has also widely expanded its model family and derivatives, including the creation of the 2 and 4 Series, the X1, X4 and X6, and the low-emission BMW i Series. The Mini brand has enhanced its offer as well, with models including the Countryman.
Such expansion and diversity has had to be absorbed by BMW Group’s vehicle logistics and global network, says Dr Ulrich Wieland, who took over as vice-president of vehicle distribution and vehicle distribution centres (VDCs) last year. In China, where its sales have grown 19-fold in ten years, the BMW Group has added plant and VDC capacity to meet the needs of demanding Chinese customers. Meanwhile, its plant in Greer, South Carolina, which builds X model SUVs, will probably surpass Dingolfing, Germany this year as the company’s biggest globally, with output headed towards 450,000 units, driving huge demand in rail transport and for exports; 70% of production is shipped abroad via the port of Charleston, South Carolina.
Production and export growth has also been sustained at BMW Group’s core German plants: Dingolfing, Munich, Regensburg and Leipzig. This growth required a big increase in rail wagon capacity over the past decade, as well as rising port volume at Bremerhaven for exports to the US and Asia, and from Cuxhaven to European markets like the UK. Investment in the Mini brand has meant not only growing production in Oxford, England, but also the addition of a new contract manufacturing site at the Nedcar plant in Born, Netherlands, creating a new ‘Mini’ network in north-west Europe for global distribution.
For Wieland, one of the vehicle distribution team’s major achievements has been maintaining stability while reducing damage rates. One sign of this success is reflected in the company’s best-ever ratings in the 2015 JD Power Initial Quality Study reports. BMW had three segment leaders with the 2 Series, 4 Series and 5 Series. The company also took a Platinum award for the best plant worldwide in terms of production quality.
“These are by far not only the achievements of vehicle distribution, however such recognition would have been impossible without good quality control in our deliveries,” Wieland says.
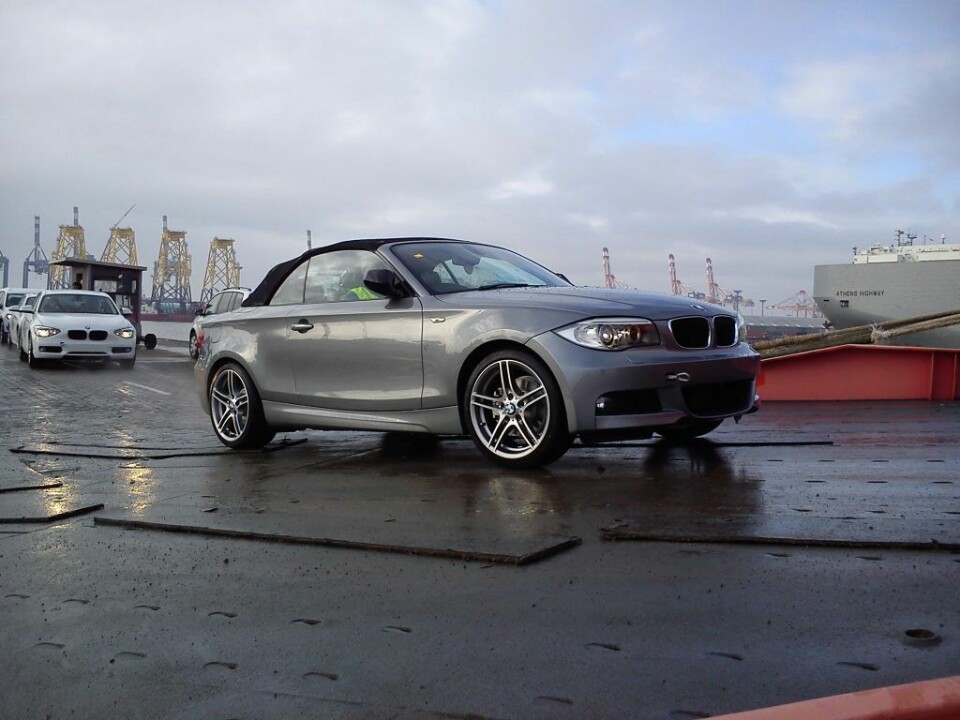
The transmission of automated and collective data through connected car technology could have positive effects on anything from shipping forecasts to battery charging processes
Mathias Wellbrock, head of global vehicle dispatch and transport, praises logistics providers for helping the BMW Group consistently hit its quarterly and annual targets even amid strains in capacity. “Our logistics service providers are the real backbone of our systems, and we have them to thank for our stability in many instances across our major markets,” he says.
Wellbrock points to good flexibility and a general willingness among providers to invest in serving the BMW Group. Car carrier shipping lines, for example, have pleasantly surprised him with their fleet expansion and network updates. “They did it using Augenmaß – in the right proportion and very professionally,” he says. There have also been significant investments in rail transport. After beginning as one of the first OEMs in Europe to use covered rail wagons for vehicles in 2006, today BMW uses a fleet of 1,000 wagons owned and operated by ARS Altmann. At a cost per wagon of around €250,000 ($275,600), this investment was “quite strategic”, says Wellbrock.
“The finished vehicle logistics sector is a small family compared to the container business, and we almost always find a cooperative partner willing to support us with strategic initiatives,” Wellbrock adds.
When BMW Group’s vehicle distribution department absorbed plant dispatch functions four years ago, it marked a significant change from how these operations had previously been managed. In the past, individual plants made local decisions on operations and logistics providers. Today, performance metrics, systems and processes are more closely aligned, with an approach that is at once centralised in quality control and data, but also based on sharing practices across locations. According to Mathias Wellbrock, this integration has been an important breakthrough in the BMW’s overall quality handling.
Processes are also now standard even in cases where third-party providers operate plant yards, as is the case in some yards depending on local conditions and historic decisions.
“In the past, the plants made their own decisions about these operations, and distribution process owners in Munich had nothing to do with it,” says Wellbrock. “But now this has changed, and all of our plants, regardless of whether it is BMW, a contract manufacturer or logistics provider, are happy to get involved and learn together.”
BMW runs workshops and meetings at both global and regional levels. In one example, it brought plant yard operations together with rail provider ARS Altmann, and port processors BLG Logistics from Bremerhaven and Rhenus from Cuxhaven.
“Quality is driven by the top level and that is why it is important that our management takes the time to talk to the people in plants and ports to get their ideas and feedback,” Wellbrock says. “This has really been a new approach in our organisation.”
One important aspect that the plant dispatch group mustface is managing space limitations at yards, which can arise partly because of volume increases, and often following disruptions to the transport network, such as strikes orshortages in rail wagons. The centralised approach can again be effective in managing these issues, as BMW’s distribution team gives its logistics providers and yard operators access to its internal systems, including immediate schedules, mid- and long-term plans.
“Our partners can proactively check our plans and raise a flag if they are concerned about a coming peak or increase, in which case we might look to speed up transport or rent temporary space,” says Wellbrock.

Network growth has also been supported by improvements in BMW Group inventory management, IT visibility and damage monitoring, with significant developments ongoing. In 2016, for example, BMW Group’s vehicle logistics will finalise the implementation of an improved Transport Quality Control (TQC) system that combines all of the events in the delivery chain in a dashboard view. The system helps BMW pinpoint damage incidents at the vehicle identification number (VIN) level, resolve insurance claims more quickly, and help identify root causes.
Get ready for the next generation of distribution
The future of BMW Group’s vehicle distribution is likely to bring more change. The carmaker will be in a tight race with Mercedes-Benz and Audi to maintain its luxury crown without sacrificing profit margins. As ever, the conditions of one decade are unlikely to mirror the previous, and Wieland wants the carmaker and its providers to be ready to adapt.
On the one hand will be network and operational adjustments. In China, for example, new regulations and market demands are already prompting the need for more multimodal transport and local compounds. In the US, the carmaker is adding a new port of entry in Galveston, Texas, and exploring potential on the west coast. By 2019, a new plant in Mexico will give rise to even more complexity in North America, with rail flows and short-sea shipping northbound, and more global exports. In Europe, changes in the production network are prompting new routes. The carmaker is also looking carefully at potential export routes from southern European ports.
Besides volume, changes in vehicle technology may also be a good indicator of BMW’s future both in product and distribution. The i3 and i8 electric and lightweight vehicles, for example, set the tone for the company’s low-emission strategy and its urban mobility solutions, such as the car-share programme, DriveNow. The company has also invested significantly in ‘connected car’ features that integrate mobile and internet into vehicles. The ‘ConnectedDrive’ programme is now available on all BMW and Mini models, putting cars online and allowing customers to use smartphones to control and monitor things like heating, location or maintenance diagnostics.
Such technology has had little to do with the distribution process so far, but that may be about to change. Like other OEMs, BMW’s vehicle tracking and logistics processes are based on manual scans of VINs at release and arrival points. However, Wieland and Wellbrock are now looking towards real-time and automated tracking to help reduce lead time and to manage inventory. ConnectedDrive means this ability may now literally be at their fingertips.
“Our inbound logistics colleagues would pay a fortune to have stillages with their own electric power supply and GPS, which were able to transmit data on temperature, expiration dates of material and other self-diagnostic security checks,” says Wieland. “We already have that in the vast majority of our vehicles, and it is up to us to utilise it and bring it into a more dynamic and proactive steering.”
The concept, which BMW has dubbed ‘Connected Distribution’, is currently being studied internally to understand the uses and risks of such technology in logistics, including several trials underway for real-time location and diagnostics tracking.
While the impact of this approach needs further evaluation, its potential has excited those in vehicle logistics – as well as engineers in research and development working on ConnectedDrive – with the idea of unprecedented levels of supply chain information directly to mobile phones or tablets.
“We are talking about data solutions that we believe will lead us to the next generation of vehicle distribution,” says Wieland.
Logistics organisation from order to handover
Reaching that “next generation” depends on innovation, but also on BMW being able to manage its supply chain stably. Over the past decade, it has made significant changes to its central organisation to achieve that. The vehicle distribution department has been reshaped according to the group’s order-to-delivery (OtD) processes, starting from ordering and parts supply through production and customer handover. Wieland believes this setup has the right integration and process logic.
“We can fully rely on the setup of the organisation so that my daily routine, for example, is less about day-to-day operational topics and more about looking to what we want to achieve, including on innovation topics – such as the digitalisation of the supply chain – as well as operational excellence,” Wieland says.
One important change came with the split of purchasing and planning functions; although the BMW Group divided these tasks for most departments some time ago in line with the ‘Prime’ management model – including for inbound logistics in 2007 – the separation came slightly later for vehicle logistics. Today, the vehicle distribution department sets process guidance and global standards, while purchasing does final contract negotiations.

More recently, the wider logistics department, led by Jürgen Maidl, was also moved out of the purchasing division and into manufacturing, where it reports to the board member for production, Oliver Zipse (who took the role this year after his predecessor, Harald Krüger, became chief executive officer). Within production, the BMW Group regrouped the logistics department’s responsibilities in line with its OtD processes.
Therefore, the distribution department now takes over once a car comes off the assembly line, known internally as ‘F2’, up to vehicle handover at dealers, or ‘F3’. Together, F2 and F3 cover plant yards and dispatch operations, handling and transport to dealerships, including VDCs, which gives the department a strong operational flavour to go with its planning organisation.
“We have the entire process design in one hand. It is quite well balanced and linked to other OtD steps including manufacturing and programme planning,” says Wieland.
Within vehicle distribution are four departments and three smaller functions. Mathias Wellbrock is responsible for vehicle dispatch and global logistics, overseeing transport processes. The plant function, which was added to the department four years ago, means yard operations at European BMW Group plants report directly to Wellbrock.
Another department within vehicle distribution is responsible for global VDCs, led by Michael Bomann.
The third and fourth departments are for the US, headed as of this past summer by Bryan Burke, and China, led by Al Cordona, both of whom provide local resources and oversight for VDCs and transport while sharing global KPIs and standards centrally with Munich. “These four departments are very closely linked,” Wieland says. “There isn’t a day when I don’t have a call with Bryan or Al.”
The other smaller, but still important functions that report to Wieland include teams for quality management (which has been expanded recently), financial control, plus a manager covering environmental and sustainability strategies.
From metals to a new outbound mindset
Dr Ulrich Wieland took over the top job in BMW’s vehicle logistics last year from Dr Karl May, who now leads a project aimed at revamping the OEM’s OtD flexibility across plants and distribution. Wieland’s appointment is in itself an interesting evolution for the department, particularly as he brings something of an outsider’s perspective to the role.
If using the connected car in its distribution system might be one important part of BMW Group’s future logistics, looking at other in-vehicle technology could point the way to further developments. The new 7 Series has automated parking, for example, and a number of other semi-autonomous features. Could self-parking or self-loading vehicles play a role in yard and compound management?
Mathias Wellbrock says BMW has mapped out processes that would see F2 and F3 functions completely automated, reducing labour, accidents and errors. However, he stresses that it is an approach for the future – perhaps the distant one. The 7 Series parking feature may currently have only limited benefits for vehicle logistics.
“The parking feature is relevant for vehicle distribution and we are looking at how we might be able to use it in yards and compounds. It starts with the 7 Series and will likely spread to other models,” says Ulrich Wieland. “However, the real scale of quality gains can only come if a large share of vehicles are equipped with the feature, and on this point we don’t yet have a clear perspective.”
A further question is whether fully automated driving can be used soon within distribution. “There are many opinions on this, but I don’t expect a dramatic change within the next five years”, says Wieland.
Wellbrock believes that this change would require close to 80% of process steps to be automated, which would mean a huge shift not only in technology, but also legislation, training and perhaps even infrastructure. “We’ve not lost sight of the potential, and we’re keeping it in mind,” he says. “But I seethis more as a change for the next 20 years rather than themid term.”
The company has explored using a robotic parking solution – developed by a Bavarian technology firm, Serva – already used by some retailers and at Düsseldorf airport (Audi is also trialling the robots). However, the robots’ current inability to function in snow or off-road conditions prevented BMW from using them.

Joining the BMW Group was nothing short of a “dream fulfilled” for car enthusiast Wieland, who is known to spend his holidays driving at Nürburgring, Germany’s most famous racetrack. But his background is not purely automotive. Before BMW, he spent five years leading European operations at German multi-metals distributor Klöckner & Co, which included logistics and processing for 150 sites, an operation that, despite obvious differences, Wieland compares to vehicle logistics in its demands for visibility and lead times.
Before Klöckner, Wieland led the logistics department for vehicle assembly and convertible roof systems at Karmann, a contract manufacturer in Osnabrück, Germany, whose main operations were taken over by the Volkswagen Group in 2010.
“In terms of leadership and having responsibility for many employees, it was really an interesting and very challenging time in the course of the financial crisis,” he says.
Wieland previously worked for five years at consulting firm McKinsey & Company, focusing mainly on OEMs and tier one suppliers in Germany, and in Japan for a year.
Getting priorities in order
As at other carmakers, the BMW Group’s vehicle distribution department places a high value on the visibility and control of units in its supply chain, and its ability to plan and react to changes. Increasing the overall automation and flexibility in this process is one of the carmaker’s objectives for the future.
While it has been updating its damage monitoring and distribution cockpits recently, both Wellbrock and Wieland see further opportunity in terms of visibility, including a legacy transport management system. While the collection of data is quite advanced and its inventory accuracy reliable, the system depends on manual processes at distribution centres and yards that are subject to human error. The information is also static, with data only as up-to-date as the latest scans, rather than globally automated feeds. Although logistics managers are constantly monitoring for potential changes and disruptions, most intervention is reactive and may come too late to avoid knock-on effects in the supply chain.
Likewise, there are limits to BMW’s distribution flexibility when it comes to changes in production or to a vehicle’s sold status. Historically, BMW has moved vehicles through the supply chain in the order they were built as the most “fair” approach, says Wieland. However, the group is now working on solutions to prioritise certain units. For example, a customer-assigned vehicle may warrant faster movement than a stock order, especially if there is a time-sensitive sailing to meet or the chance to build a full rail or truckload. Currently, BMW only makes such changes by manual overrides.
BMW is working on projects that could have big impacts on these areas. One is a major order flexibility project, called ‘Pro-flex’, which would, among other things, automate BMW’s distribution according to certain customer priorities and transport schedules.
Changing systems to account for such considerations is a big change, and the project – led by Karl May, Wieland’s predecessor – aims to improve order flexibility across all OtD functions, including sales, programme planning and logistics.
Trialling future visibility
Connected car technology is at the centre of Ulrich Wieland’s vision for transforming the static information currently collected across the supply chain into one that transmits data in real time via satellite. Such “dynamic proactive steering”, as he calls it, would allow the carmaker to plan according to the most accurate and up-to-date visibility.
Mathias Wellbrock gives an example of a potential storm moving over the Atlantic Ocean that might delay a ro-ro delivery between the US and Europe. While today there might be awareness of a storm, the precise impact on the ship’s arrival and subsequent vehicle processing is highly variable.
The key aspects of such a system would be its automated and collective data. GPS points on vehicle location would be transmitted to a central data centre, combined with vehicle status indicators such as tyre pressure or the battery charge. Metrics would be scanned constantly, prompting warnings about deviations, damage incidents or unexpected trends. Different levels of information could also be available across BMW management, logistics providers and dealers.
While the full potential of ‘Connected Distribution’ may be years in the making, BMW is already in the midst of two important trials. It ran tests on tracking the location of i3 and i8 models exported to Japan to understand the speed and quality of the data transmitted, including GPS tracking of the vehicles prior to customer handover.
“The vehicles had no technical changes applied to them, but were sent to Japan on a normal shipment,” says Wieland. “It worked very well and we had no problem obtaining highly accurate GPS data.”
The early trials have yielded positive results, but Wieland acknowledges that significant research will be needed to understand the full implications of such tracking.

Along with information on location, regular updates on the health status of the car can also be valuable in the distribution process, particularly in preventing damage or misuse. The distribution team is currently running a trial for tracking vehicle diagnostics for the new BMW 7 Series, which entered serial production this year in Dingolfing. The model has a battery guard that reads the state of charge; during the trial, battery information is transmitted directly to BMW’s distribution system when the door is open or the engine started. By monitoring the exact charges and impacts on the vehicles, BMW can adjust its charging patterns.
“Currently we charge batteries on a six-week cycle, however with this up-to-date information, logistics providers can see exactly when the vehicle needs charging,” says Wellbrock.
Wieland points out that this accuracy could be important, as under-charging a battery can impact negatively on its health, especially in the initial uses. “It may not be a big, singular improvement in quality, but it could be a small, important step in eliminating this functional risk from the distribution chain,” says Wieland.
Results of the initial trial are expected in early 2016.
Considering the testing that is still necessary, Wellbrock and Wieland do not assume that ‘Connected Distribution’ will become the only form of vehicle tracking in future. They welcome competition between it and other technologies, such as RFID. Up to now, the BMW Group has avoided such an approach, which would have required new equipment at all of its plant gates, compounds and VDCs. However, drops in the price of RFID and improvements in its reliability have made the executives more open-minded. BMW has sent an executive to participate in an RFID working group at the German Automotive Industry Association (VDA), and Wieland says he is open to pilot projects. “We are approaching solutions without prejudice and we will see how it develops in the coming years,” he says.
However, he remains sceptical that hardware-based solutions like RFID could offer the “adaptability and flexibility” the company seeks across its global distribution.
A major focus across the BMW Group in recent years that will continue in the future has been on quality. For vehicle distribution this target has translated into efforts to reduce damages and make delivery more reliable. Dr Ulrich Wieland believes that the main levers of improving damage rates are in operational excellence, including staff training in handling and improving yard or VDC infrastructure. Some of the biggest jumps have come with shared programmes and workshops, including meetings run by Mathias Wellbrock’s team across plant yard, logistics and port operators. Michael Bomann’s VDC division also manages global programmes, including one called ‘The eight principles of VDC operations’.
However, protection products and transport equipment have important roles to play. BMW’s use of covered rail wagons in Europe is a strategic investment the company will continue to make, says Wellbrock. The company has also carried out audits of every rail wagon it uses in the world to determine the impact of iron dust, including consulting experts from BMW’s paintshop division to determine how to reduce damage.
“In North America, we tested our wagons moving from Greer to the west coast and found that we needed a full body cover, so we invested in that,” says Wellbrock.
One size does not fit all
In looking across its network, wheel rims, door edges and bumpers are still the most vulnerable parts of the cars for damage. However, one of the biggest worries is an increasing disparity between the dimensions of newer vehicles – especially their width and clearance – and standard transport equipment.
“Already today, BMW and others sometimes cannot load vehicles into the standard equipment used by providers, including trucks and wagons that are too narrow,” says Wieland, citing rail wagons in the UK as one example. “It is absolutely clear that this issue will increase in importance.”
Wieland acknowledges that the scale of investment needed for equipment means no company can revamp its fleets overnight. He also knows that his vehicle distribution team needs to work closely with vehicle designers and engineers to make sure future models are designed with consideration for how they will be transported. However, he stresses that changing vehicle dimensions should be a major consideration for logistics companies making new investments.
Wieland also makes it clear that this is an opportunity for vehicle logistics providers that are ready to take a lead in equipment. He again highlights the general lack of covered rail wagons in the UK, where only DB Schenker has a small fleet. Elsewhere in Europe, he stresses that “now is the chance” to get ahead of competitors.
“I personally believe that any provider that tackles this topic faster than the competition, and can provide better infrastructure and equipment to cope with larger vehicles, will have a competitive advantage,” Wieland says.
“If ‘Connected Distribution’ works out the way we hope, it would mean we have a solution that works independent of additional, or at least major, new investments by our service providers or us in equipment or compounds,” says Wieland. “If you look into the latest market structure, it is hard to see what will happen in the next 5-10 years. However, solutions with huge investments and decentralised hardware are not the way to go.”
Mapping the medium term
We do not have to look to volume forecasts, or try to guess about new technology to understand what will shape much of BMW Group’s logistics in the immediate future. Many expansion projects are already planned: in China, one of BMW Group’s largest global markets, local production is expected to rise at the two joint-venture plants with Brilliance in Shenyang, in north-east China. Although the market is slowing down, the BMW Group remains the largest vehicle importer in China, and managing this combined volume safely across the country is a top priority. Overall customer demands for shorter lead times, as well as an anticipated change in trucking regulations, have prompted considerations for multimodal transport options, as well as expanded VDC operations inland and at its ports.
Currently, BMW has VDCs at Tianjin, Shanghai and Guangzhou, and an inland centre at Xi’an, Shaanxi province. “We’re looking at concrete options that would get the cars physically closer to the dealers with more regional hubs, which will allow us to operate our transport as ‘warehouses on wheels’,” says Wieland. “This will allow us to have lower inventory and shorter lead times.”
The current tendency to use oversized and overloaded trucks in China is expected to come under sharp scrutiny as the government moves closer to establishing (and enforcing) a new standard. For Wieland, moving away from BMW’s total dependence on truck for imported and domestically built vehicles in China will be a must.
Furthermore, BMW is also looking to increase the technical expertise for maintenance, accessories and local adaptations at its VDCs in China. Currently, the import centres are “VDC-lite” compared to global facilities, according to Wieland. “We’re in an intense process to better equip our Chinese VDCs, and in a year-and-a-half, they will be at a completely different level to what they are today.”
There is also a flurry of activity in North America. The Galveston terminal, which WWL will operate, should be ready by the end of the year, giving BMW the opportunity to reduce overall delivery times to Texas and the central region, and avoid long-distance trucking from either coast.
After Galveston, and a switch to a WWL-run terminal last year in Baltimore, BMW is also eyeing California. “Our development on the west coast has been positive, and there are peak constraints in Oxnard [at the port of Hueneme], which would make adding another port an option,” says Wieland.
Production in Greer, meanwhile, is slated to grow to 450,000 units with the introduction of the X7. And although BMW Group’s Mexico plant in San Luis Potosi is nearly four years away from the start of operations, planning has already begun on shaping its routes and in considering the impact on the wider North American network.
Wieland reveals that the plant will have a rail connection, and that most northbound exports will move by rail. However, he and Wellbrock share concerns over rail infrastructure and wagon capacity across North American.
“In a perfect world, everything from our Mexico plant would go to the US by train, but we don’t think that will happen, so we need to look at short-sea alternatives,” says Wellbrock.
BMW already uses short-sea to move Greer-built vehicles to Canada and Mexico. However, introducing new rail flows to the US may also present some return opportunities and the potential for new routes.
Although the decision to open Galveston was made independently of plans for Mexico, Wieland acknowledges that the port, which would be a relatively short sail from Mexico’s Gulf ports, could also be an alternative for Mexican imports. Taking this location in combination with BMW’s other ports (Port Jersey, Baltimore, Brunswick, Hueneme and, for export only, Charleston), and considering that San Luis Potosi will export beyond North America as well, by the end of the decade BMW will have one of the continent’s most dynamic logistics networks for rail connections and ocean shipments.
In Europe, where BMW’s distribution is more established, there are still regular changes and optimisations. The Russian market’s difficulties have disrupted some export flows and it remains unpredictable, while some adjustments have been necessary in light of production changes, such as adding the Nedcar plant. According to Wellbrock, most of these flows have been easily absorbed into BMW’s existing network.
Ready for the Med, ready to adapt

A potentially significant change may be on the horizon for southern European ports. Already, Mercedes-Benz has switched China-bound exports built in plants in southern Germany, Austria and south-east Europe from northern German ports to Koper, in Slovenia. The shift is part of a strategy to send other Asian exports via Mediterranean ports, reducing overall lead times and costs thanks to shorter overland routes compared to the north, and potentially shorter sailing times eastbound.
According to Wellbrock, BMW Group logistics has also investigated this option, including studies at Koper and other Mediterranean ports. However, for the time being, the carmaker has not changed its exports from Bremerhaven. Although Wellbrock generally believes that southern ports could handle the business, he suggests there won’t be a significant benefit in switching until those ports start handling more imported vehicles from Asia. Should more cars from Japan or South Korea (or perhaps even China) come inbound, it would create a more balanced shipping trade east and west, and allow shipping lines to make return trips between Asia and the Mediterranean without extra calls in northern Europe.
“We need a balanced transport to gain the shipping advantage, which could be five days compared to north Germany,” says Wellbrock. “However, if you need to use vessels stopping both in the north and the south, you lose most of the advantage.”
Wieland and Wellbrock both say that the option remains “on the agenda”, and that they are watching carefully should other carmakers start using the southern gateways more.
For the executives, a readiness to adapt to such changes, whether in product dimensions, markets, technology or export flows, will be essential if BMW and its providers are to thrive over the next decade as much as it has over the previous one. Although there are exciting developments, like production growth in Mexico, the US and China, or technology like ‘Connected Distribution’, success is not destined for those chasing trends so much as those able to provide stability across the network.
“Our success is based on our overall network of providers, systems, our own staff and also our stable processes,” says Ulrich Wieland. “We need to identify and leverage new opportunities across all of them, and equally be even more adaptable and flexible than we ever have been.”