Getting to the point of return
As China’s use of returnable packaging for automotive parts grows, the need for standardisation has become increasingly important
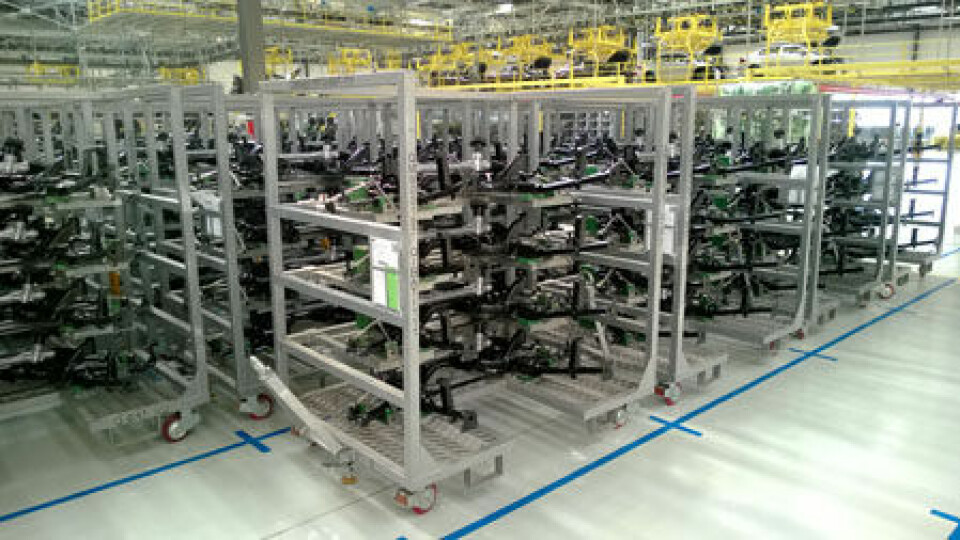
The move towards wider use of returnable packaging is gaining momentum in China, although it still has a long way to go. Increasing the use of such equipment still depends largely on further standardisation of pallets, containers and stillages, however this is held back in China by the variation in truck size regulations among its provinces. Although some automotive manufacturers and packaging providers are trying to take a more holistic approach to designing and implementing returnable packaging, fragmentation within the supply chain remains an obstacle.
China’s automotive sector uses about 40% returnable packaging and 60% expendable packaging, according to Jon Salemi, executive director, Asia sales and marketing at Orbis Shanghai Material Handling Company. Of those returnables, between 70% and 80% are metal and 20%-30% plastic.
Most returnable containers are used either between tier ones and OEMs or between an OEM’s own facilities. For tier two to tier one movements in China, packaging is almost entirely expendable. There is also a significant gap in the Chinese market between local manufacturers and foreign joint ventures. “Chinese shippers have not quite valued the cost of transportation compared to US shippers,” says Salemi. “Handling is not as efficient. It is a harsher environment, with a greater chance of damage to packaging. Our focus is on Western OEMs in China; Chinese OEMs are more about the price.”
In this story...
Although returnable rates are lower in China than in European or American markets, a number of OEMs have wide networks of returnable packaging, which are growing as they build new plants. One of the most significant is Shanghai Volkswagen (SVW), which operates seven plants in China, including a recently opened factory in Ningbo, south of Shanghai. Zhou Zhou, senior manager for logistics at the Ningbo Plant, says the carmaker uses returnable packaging for more than 98% of the parts for each car produced at the new plant. The carmaker’s challenge is at its legacy plants and for models that use old containers. “In these cases, we have found that investing in new containers does not cover the cost of replacing the old ones,” says Pan Rongsheng, senior manager for logistics planning.
Qoros, a Chinese-Israeli joint venture that started production at its plant in Changshu last November, is also using about 99% returnable packaging at its plant. Paulina Chmielarz, the company’s senior manager for logistics planning, points to a lack of equipment and truck standards hindering efficiency, however.

According to Jon Salemi, for about two years Shanghai General Motors has been using an Orbis 980mm by 1,440mm standard plastic returnable container for imports as well as its tier ones in China.
Others, including Ford and PSA, have also been moving towards returnable equipment within China and for international shipments, although they face difficulties in standards, equipment tracking and service levels for managing such equipment. Witold Orlowski, regional director at packaging provider Schoeller Allibert, says there are too few local hubs in China to make pooling effective.
At Ford Motor Company, Amlan Bose, Asia Pacific material flow and packaging engineering manager, points to the limited availability of a high-quality supplier base, such as fabricators of steel racks.
A growing use of returnables
SVW’s returnable packaging system includes standard series of small and large containers of collapsible and rigid packaging. Pan says switching to returnable containers has led to greater size conformity, load maximisation, ergonomics and parts protection, which in turn have brought cost benefits.
Meanwhile, Bose says that Ford’s predominant packaging strategy is to use returnable packaging for locally sourced parts. Ford also uses returnable packaging for shipping engines and transmissions to and from the Asia Pacific region, as well as for powertrain and sheet metal components that move between Ford plants in the region. Ford also aims to use returnable containers for more intercontinental shipments of other critical commodities in the region, according to Bose.
Qoros uses three types of returnable containers, all of which are supplier-owned. About 100 different part-specific metal racks hold axles, brake fuel lines and exhaust systems, according to Chmielarz. The carmaker also uses 30 different standard KLT or VDA plastic containers (which are large and foldable, following standards set by the German carmakers’ association) that handle small and medium components. Qoros also uses standard industrial containers that are designed, forged and owned by suppliers for holding paint shop chemicals, sealants, and glues. These are drums, buckets, or special barrels, of which most are returnable.
According to Duncan Deng, sales director for automotive service at container pooling provider Chep China, Capsa, the Changan PSA Peugeot Citroën joint venture based in Shenzhen, switched to the company’s returnable system around 18 months ago. Deng says the share ratio has increased within Capsa’s pool with its tier one suppliers. It currently provides pooling of metal racks and stillages, but not yet for metal boxes.

Schoeller Allibert Asia Pacific also offers KLT and VDA containers. Its main customers in China are BMW, Ford, and Jaguar Land Rover. Packaging director Tim Mabbutt says more foreign manufacturers in China are following the European approach to using VDA containers, including the Volkwagen joint ventures and their tier one suppliers. For foreign or joint-venture carmakers, Schoeller Allibert has been focusing more on specialised packaging, including dunnage, and on reducing handling from tier one suppliers to the assembly line.
No two boxes alike
Despite this push deeper into returnable packaging, there is a general sense that China’s factories lack standard equipment and practices when it comes to both plastic and metal packaging. In establishing Qoros’s packaging regimen, for example, Chmielarz says it has been difficult to use returnables for some parts. “There is a huge need for container standardisation in China. It affects our inbound execution and our suppliers’ performance,” she says. “Container quality is also an issue – especially for metal ones.”
Chmielarz explains that since Qoros has special containers coming from different suppliers, it would like to establish more conformity, such as a tow-and-hitch standard and a rack-base standard. “During our current ramp-up phase, sustainability and quality of containers is a challenge, since sometimes suppliers use containers other than the agreed ones”, she says. Controlling the container loop size is another difficulty. “We want a fixed one and sometimes suppliers do not hold to it”, she adds. [sam_ad id=6 codes='true']
Daniel Hettel, chief engineer, global material flow and packaging engineering at Ford, points out that the short lifecycle of products as well as multiple vehicle launches drive the need for standardised containers in the Asia Pacific region. “The objective is to drive down float obsolescence and gain higher reusability. Standardised containers are also the key to ensuring the launch of global products concurrently in multiple markets,” says Hettel.
Packaging provider Goodpack supplies returnable containers and racks in China that ship domestically and overseas. “We certainly have a need for packaging standardisation,” says Thomas Ong, chief operations officer at Goodpack. “However, each player often defines its own standards, although there are similarities. The question is whether the automotive industry would be better off with a common pool of standard containers operated by an independent third party, instead of each player operating its own.”
"There is a huge need for container standardisation in China. It affects our inbound execution and our suppliers’ performance" - Paulina Chmielarz, Qoros
Deng says his company has been pushing the use of more modular equipment. “The problem is that there is no system to control cycle time,” says Deng. “Standardisation is also a main objective. Without it, we will need to continue to invest in new sizes as new models come out.”
So many different trucks
Supply chain experts agree that the major issue around pallet and container standards in China is the lack of unified truck sizes across China. Schoeller Allibert’s Orlowski says there is currently little drive to standardise transport. Although Chinese automotive logistics are dominated by a number of large companies, such as Anji-Ceva, the average trucking company in the country has a fleet size of just one-and-a-half trucks. Standards vary widely by province or city. For example, truck widths and heights that are illegal in Shanghai may be legal elsewhere in China, says Duncan Deng.
The differences go down even to individual carriers. “Every supplier has a specific type of truck,” adds Qoros’s Chmielarz, “which could be open platform, rear opening, or side opening. Containers must conform to the truck’s dimensions. In fact, we do not permit non-standard trucks to enter our facility.”
Ford’s Bose adds that by increasing the cubic utilisation of transport vehicles, standardisation also improves the quality of parts since it reduces the damage rate. “The challenge is the availability of standard-sized trucks in the region. Ford is working with its carriers to increase the availability of standard trucks with side unloading capabilities,” he says.
Since there is a lack of truck standards, some packaging standards are based on sea containers, which can have multimodal applications. “Recently, we developed a standard container series that fills 100% of a 40-foot high cube container, which we use to serve our Urumqi facility [in the northwest province of Xinjiang] by rail,” says SVW’s Pan.
Looking for better ways to track
Tracking container assets is a concern for manufacturers in China, including Ford and Qoros. According to Chmielarz, Qoros controls the loop size by quantity at the plant, in transit and at the supplier, which is especially important for specialised container and plastic containers. Qoros will implement a special module in its warehouse management system by the end of the year to keep track of all packaging stock quantity and serial numbers. Currently, its SAP system handles all package size codes and its communication portal with suppliers shows the coded and labelled container in the advanced shipping notifications.
"Standardised containers are also the key to ensuring the launch of global products concurrently in multiple markets"
- Dan Hettel, Ford Motor Company
“This includes the code, warehouse stacking factor, destination dimension and any loose components that need special handling. We are in the process of synchronising all three systems and plan to go live in September,” reveals Chmielarz.
Similarly Ford also sees tracking and tracing of returnable containers as one of its main challenges, says Bose.
Investments in packaging
Among the recent advances in returnable container networks, SVW is promoting the use of returnable pallets and uniform caps to replace wooden pallets at its plants in Nanjing and Ningbo. Zhou says this could improve its logistics efficiency, including increasing the truck load factor and reducing the use of wood.
The carmaker has also promoted the use of collapsible KTP boxes instead of rigid metal containers at its plants in Yizheng and Ningbo. This measure has reduced empty space on the return leg by 75% and has reduced the space requirements for empty containers. SVW hopes to expand its KTP container network to suppliers for its Urumqi plant and its upcoming plant in Changsha, which will open next year.

Pan says that because of its increased logistics costs, SVW’s use of returnable packaging will focus more on collapsible containers, which it will promote mainly at its more distant plants (like Urumqi and Changsha). “Since our collapsible containers are standardised, we hope to use them interchangeably among our plants and suppliers,” he says.
As it promotes the use of collapsible and returnable packaging, Pan says that SVW will pay more attention to the folding operation for empty containers to reduce damage, thus prolonging their life and ultimately reducing logistics costs.
Hettel says Ford is looking toward standardising its returnable packaging and minimising the number of footprints as a method of reducing logistics complexities. He foresees continuous improvement in Ford’s use of returnable packaging for imported parts and intercontinental movements.
Qoros’s main growth is in the standardisation of metal containers. It is also working with its suppliers to eliminate the need for repacking. “This is part of the Chinese legacy system that does not have much flexibility. They work at a slower pace and maintain higher inventory,” says Chmielarz.
Of the carmaker’s 120 suppliers, 55% are within a 300km radius and do not require repacking. Of its long distance moves, Qoros has eliminated the need for warehousing and repacking in ten cases. Now, it repacks only when the distance from the supplier is greater than 2,000km.
There are also product improvements in the market. Orbis has introduced special vacuum-formed trays for powertrains and engines, which are nestable when empty. It also offers textile packaging as interior dunnage for headlights that increases parts held per container and reduces damage.
The company is also focusing on bulk containers and custom dunnage or foam. It is launching a 980mm by 755mm bulk container, which is new for China. Salemi says this container has a high weight capacity, is not as tall, and takes up less space. It can be used for heavier parts such as metal stamping. This increases the part density and more containers can be loaded on a truck.
About six months ago, Schoeller Allibert introduced a plastic pallet and sleeve, which does not require strapping or cling film. Orlowski says it has also implemented its 360-degree vision from cradle to grave, in co-ordination with Chep’s pooling and rental infrastructure. “In addition to Western-based manufacturers, we are moving into Chinese companies with the help of benchmarking and quality and cost analyses,” he says.
While returnable packaging in China is evolving, it would seem that the lack of equipment or truck standards continues to minimise the wider impact on efficiency and costs. As carmakers build new factories, there are opportunities to increase the use of this equipment, but the industry is likely to need to work together as a whole if it is to bridge the gap between its legacy packaging systems and its newer ones.