Honda part 1: Field of dreams
Since Honda took root in a cornfield in Marysville, Ohio, the carmaker has created a supply chain of stunning complexity, length and scale
Carmakers preside over plants and sales channels as diligent farmers and shepherds would cultivate their fields, flocks and harvests. The supply chain supporting it all, meanwhile, has typically been a somewhat wilder crop to nurture, its roots (and routes) spreading and twisting in every direction, breaking through the surface in surprising places and running like culms of bamboo. Take a Japanese brand that opens a factory in the US Midwest; its supply and technology origins may be in Suzuka or Saitama, but over time it comes to life across the US, Canada and Mexico, with offshoots sprouting as far and wide as Thailand, Italy, India and the Philippines. It grows without respect to proximity or irrigable land; the only chance to order its shape is in reverse, by pruning the brush and ploughing it into rows.
In this story...
The setting of Honda’s largest North American campus, in Marysville, central Ohio, brings this image of farming exploitation vividly to life. The 1,000-acre (400 hectare) tract of land was a sprawling cornfield when Honda founder, Soichiro Honda, and other Japanese executives chose it back in the mid-1970s. It now holds both the Marysville and East Liberty assembly plants, a regional headquarters, engineering and research centres, a test track, along with key logistics and supplier sites. It also remains a working farm, even producing a relatively rare type of soya bean, which Honda exports by the container load to Japan where it is used in tofu.
Beyond this literal cultivation, the carmaker’s considerable expansion here and across North America has created a supply chain of stunning complexity, length and scale. In Ohio, the carmaker builds some 680,000 vehicles per year, plus more than 1m engines and transmissions across four assembly and component plants. Since opening its eighth North American assembly plant last year – in Celaya, Mexico – Honda has capacity to produce more than 1.9m vehicles. It also sources parts from more than 700 suppliers, imports around 150 containers per week, and is increasingly exporting parts around the world.
“Our supply chain is becoming so complex. In the past you’d call ‘Joe’s Supply’ in Marysville when your production went a bit higher than planned and asked for 30 more parts, which could usually be delivered quickly,” says Dana McBrien, associate chief advisor, who leads the logistics department at Honda North America. “Today, if you tell the supplier that you need more, the response is likely that it only has what you forecasted, and its supply line starts in India and needs five months to ramp up, unless you start flying parts.”
While it may have grown like bamboo, it would be wrong to imply that Honda’s supply chain is somehow ‘out of control’; thousands of trucks move swiftly through local crossdocks and consolidation centres, with many suppliers delivering just-in-time to assembly lines without disruption, coordinated in “an orchestrated ballet”, as McBrien puts it.
Honda’s North American logistics department, which has increasingly become something of a corporate supply chain team for Honda, manages around 2,000 of these truckloads every day, along with around 50 intermodal deliveries to Mexico and dozens of import and export containers. By the end of this year it will add more responsibilities, including control of cross-border material of tier ones from Mexico.
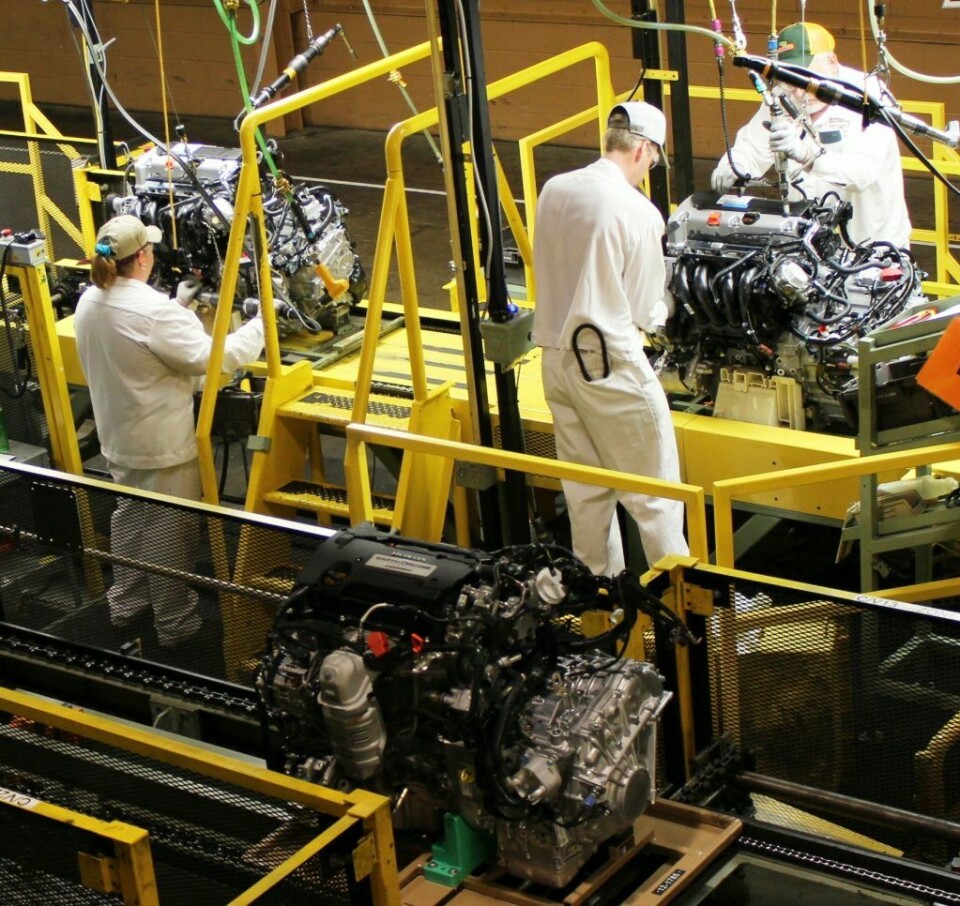
However, there is little doubt that Honda, like many other carmakers, wants firmer control and standards over inbound material flows. The risks have become all too evident, especially in the wake of two consecutive harsh winters that have disrupted rail services, production and sales. This past winter was further exacerbated by six months of labour disputes that clogged US west coast ports, leading Honda, along with others, to charter flights and expedite freight to assembly lines. McBrien admits that the carmaker is analysing potential changes, including switching some imported material to east coast, Gulf coast or even Mexican ports.
Such weather and labour issues are critical for a supply chain as voluminous and global as Honda’s. At the offices of Honda North America logistics in Maryville, a dedicated team from the carmaker and its lead logistics provider (LLP), Ceva Logistics, focus on coordinating around 60 expedited shipments per day, according to Kevin Wade, senior staff administrator, who leads the transportation team at Honda North America. “The team is fully equipped to expedite using single vans, 53ft trucks, airplanes, helicopters, whatever it takes,” he says. “Our expedited freight volume has grown because of the recent disruptions, but even at 60 a day we are told we expedite less than most.”
At the Marysville office, a large screen hangs on the wall displaying a customised, live weather map of the North American continent that signals potential events in proximity to Honda’s supply and assembly points, flashing red with warning signs that the team tries to get ahead of. During my visit, in the middle of May, the map was mostly green amidst the relative calm of spring, except for a swirl of red near Oklahoma, which would become deadly storms and flooding there, in Texas and Mexico. During the icy winter months, red warnings across much of the northern US and Canada sent regular chills through the office.
This careful monitoring and response to events is just one part of the strategic development of the North American logistics department based in Ohio, and its satellites at Honda plants. Today, logistics is made up of around 120 Honda employees covering transport routing and purchasing, material follow-up, premium freight, imported and exported material, and supply chain innovation; 44 Ceva employees supplement the team, assisting with systems, analysis and route engineering, most based directly at Marysville.
Over the years, this department has grown with the Honda farm, starting as a seedling that covered little more than transport purchasing, into greenery touching nearly all aspects of the supply chain.
“Logistics at Honda used to be more transportation procurement. We’d say to suppliers, here is the route, here are your carriers, make it work,” says Wade. “Now, we have taken a lot more ownership to make sure the networks work, including managing the KPIs and costing indices to keep us on the right track.”
"Today, if you tell the supplier that you need more [parts], the response is likely that it only has what you forecasted, and its supply line starts in India and needs five months to ramp up, unless you start flying parts"
– Dana McBrien, Honda
Not so long ago, Honda’s plants – even those in close proximity to one another – ran their supply orders in isolation, each with separate logistics teams. While this approach sufficed in an era of relatively fixed, high-volume models, with a large knockdown kit supply from Japan, today logistics are infinitely more tangled. Supply locations are more global and part numbers and options more diverse, while plants produce a wider range of niche models and variants at inconsistent volume.
In response, Honda must move quickly to adapt routes, customise and standardise packaging types, and adjust line delivery methods across the entire network. McBrien’s logistics department is evolving to do just that. It is part of the manufacturing and planning group (known as ‘e-planning’) at Honda North America Inc., the corporate entity created in 2013 to bring together support functions across plants, including purchasing, planning, human resources and public affairs; it also combined aspects with the company’s sales arm, American Honda, based in Torrance, California. While the department’s responsibilities cover a wider scope across US plants, Honda North America is increasingly turning into its namesake, with closer cooperation, if not integration between the US, Canada and Mexico.
For example, North American logistics technically covers all inbound routes and logistics facilities up to the delivery docks at US plants or onsite consolidation centres, as well as freight to or from the US border and ports. However, it is increasingly difficult to draw a boundary line delineating where the reach of the logistics department begins and ends. At Canadian and Mexican crossdocks, for example, it is directly managing providers and routes, while there is considerable interaction and sharing with plants. In some cases, legal entities in each country require separate commercial agreements, but there is a move towards more centralised contracting.
“Part of the positive thing about having Honda North America Inc. is that we are moving to the point where we can sign a contract that applies to all of our sister organisations,” says McBrien. “It means that when we sign a deal with Ceva or Ryder, Marysville or Celaya can use their services.”
A broad sense of supply chain management

While Honda’s North American logistics still navigates through a degree of decentralisation, with some plants retaining logistics teams for their own routing, it is increasingly managing the “supply chain in the broad sense”, McBrien says, rather than pure transport and inventory operations.
“We now really have part of everything within North American logistics, including an ordering function, a receiving function, customs, shipping, transport purchasing, packaging, engineering and export,” says McBrien.
For example, last year Honda launched an important parts centre within the Marysville campus: along with the growing number of exports to global destinations from North America, the new location was established to handle parts from Japan. Within the import centre, known as the Regional Logistics Centre (RLC), McBrien’s team has centralised parts purchasing and orders inbound from Japan, and onward to local plants, controlling the chain from beginning to end.
Likewise, while plants manage internal material handling, line feeding and container handling, the logistics team is more involved in helping to calculate the full implication of plant operations, such as kitting. For example, the logistics department has been pushing plants and purchasing to bring back on site the sequencing and special packing that Honda had previously pushed back to most suppliers’ plants over the past decade or more. By doing this work at Honda plants, the carmaker can simplify supplier shipping processes, and better control packing for errors. Also, as logistics is responsible for the transport of returnable containers, it wants to better track the locations of its packaging assets.
McBrien anticipates that his department could expand further into other areas. He would like to see logistics costs allocated and managed from the suppliers to the assembly line in the same budget as outsourced parts, for example, rather than attributed to individual plants, as today. He sees benefit in concentrating in-plant material handling in the same budget as inbound logistics as a way to eliminate wrangling between departments or plants over who might have to spend more in order for the total cost to decrease. He also believes that it would not be “blazing a trail” in the automotive industry to combine logistics management with parts ordering and scheduling, which are again still mostly controlled by plants at Honda.
But McBrien, who admits to being impatient when it comes to improving operations, understands that changing decades’ old habits does not happen overnight. However, in many ways the change is already underway at Honda. North American logistics has expanded its remit; the order function out of the RLC, for example, has been an important step in wider management oversight.
"Logistics at Honda used to be more transportation procurement... Now, we have taken a lot more ownership to make sure the networks work, including managing the KPIs and costing indices to keep us on the right track" – Kevin Wade
In some cases, Honda is even managing logistics from tier two suppliers to tier ones before they deliver to Honda, including out of Mexico. At a Ceva-run crossdock in East Liberty, around 300 suppliers are now moving through the ‘suppliers’ supplier network’, where freight is delivered, staged and sent by shuttles to tier one suppliers. Tier two freight is also moving through the RLC.
“In theory this freight moves entirely within our existing network, so it helps to reduce overall costs rather than moving it by less-than-truckload methods,” says Kevin Wade.
If individual plants, other departments, and even tier suppliers might have worried about losing some control to a central logistics group at Honda, they can be reassured by the ever-improving success of current projects.
“What has happened is that we have been integrating a piece at a time. We are building a business model that, eventually, we can say ‘we are already doing this’,” says McBrien. “For example, we are now doing ordering for Japan parts; next it will be parts out of Asia; we are managing parts flowing between suppliers, and soon for parts out of Mexico. This sets a model for the possibilities to centralise more of the supply chain operations.”
Click here to read part 2 in our Honda series, "Getting the lay of the land".