Q&A: Mike Pilver, APL Logistics
Coronavirus has shut down automotive production operations across whole regions, disrupting supply chains and causing backlogs of both parts and finished vehicles. APL’s vice-president and global head of automotive at APL Logistics gives a 3PL perspective
How has the pandemic altered APL’s services and the nature of automotive stock keeping?
Our service scope for the automotive sector encompasses inbound logistics for both production and aftermarket parts, as well as outbound logistics for finished vehicles. That will not change.While the pandemic has resulted in a temporary shutdown of production across most assembly plants, that does not mean there is no logistics activity. At present, we are actively engaged with our clients as they are busy planning for the eventual resumption of automotive production and sales.
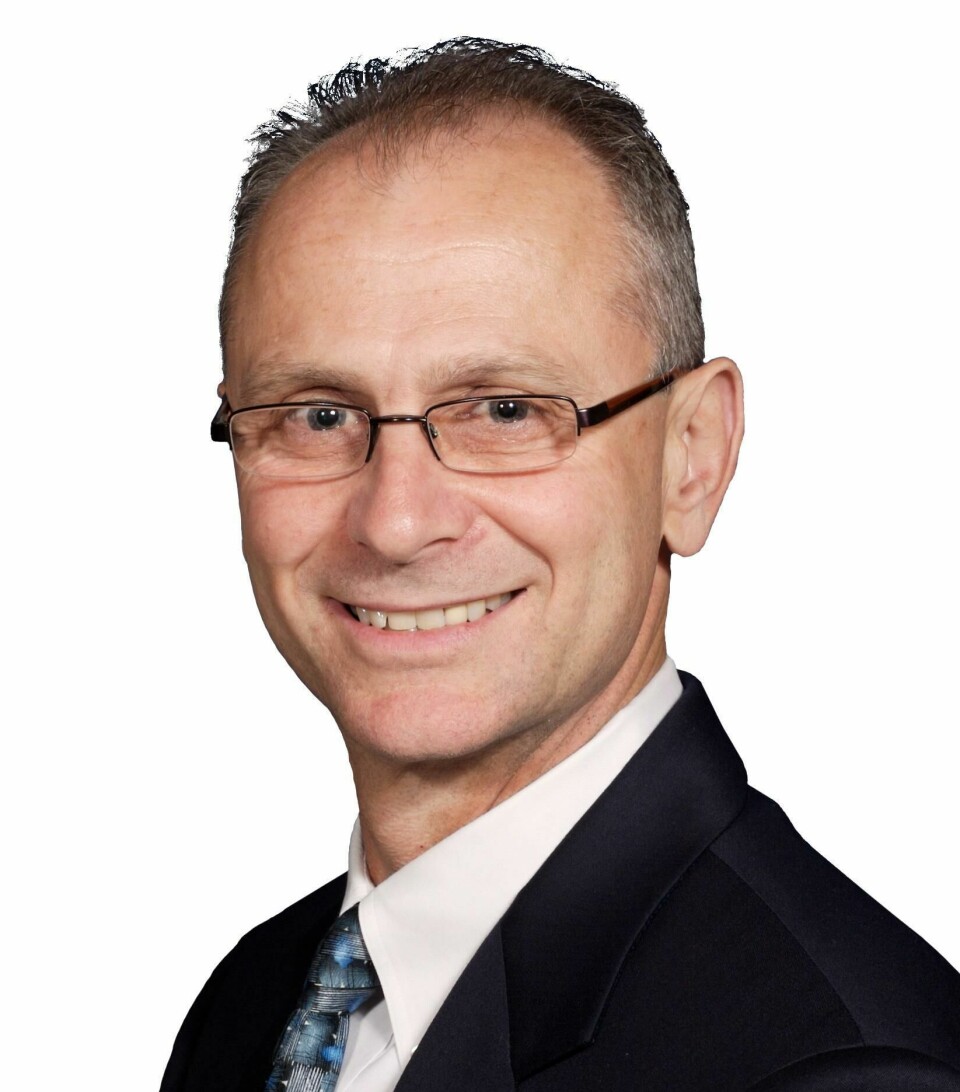
There has been severe disruption throughout the supply chain. Inventory – both parts and finished vehicles – has to be repositioned to the right places to support both production and sales. That involves ensuring the right equipment, right transport and storage capacity are available and ready. There’s a lot going on, actually.
In terms of automotive stock keeping, I think the huge shock to the supply chain from this pandemic will challenge some long-held practices and beliefs. For example, OEMs may adjust their just-in-time production schedules and hold more buffer inventory. They may start to actively diversify their supply base and look for sources closer to home. It will all be about risk mitigation, even if it means higher logistics expense, because the alternative can be much more costly.
How has the significant slump in automotive sales affected your business?
With few exceptions, almost every company in every industry has been impacted by this terrible pandemic. In North America, most OEMs suspended most vehicle production until at least early May. This temporary shutdown would allow existing vehicle inventory to be drawn down as auto sales begins to recover.
I recall that the 2008-2009 financial crisis hit the OEMs especially hard. Our experience and response then taught us a valuable lesson: in times of adversity, being there for, and supporting, your customers when they need you most is even more important than during the good times. Eventually the industry recovered and went on to experience solid growth. As a 3PL provider, our loyalty was recognised and subsequently rewarded.
What evaluation process does APL Logistics typically conduct when considering the location, lease or purchase, and rates for its storage facilities?
In terms of location, we evaluate a variety of factors. These include: yard proximity to the assembly plant; ease of access to and from the yard; links to transport modes (both road and rail); availability of labour; and other physical characteristics of the yard (security, type of ground, etc).
There has been severe disruption throughout the supply chain. Inventory – both parts and finished vehicles – has to be repositioned to the right places to support both production and sales – Mike Pilver, APL Logistics
In terms of lease period and rates, these will vary with each customer and need. Some yards are leased on a temporary basis, depending on customer timeframe. Others are held on longer-term leases, especially if the yard can be used by multiple clients in a specific geographic cluster on a year-round basis.
Pricing schemes also vary, but unit-based pricing and/or yard size pricing are typical schemes.
Are some aspects of your business model likely to change permanently as a result of the pandemic?
I think it’s a bit premature right now to comment on how the pandemic will permanently change any company’s business model. Until the fog clears and we all come out on the other side and begin to assess the pandemic’s true impact, no one can make any predictions with certainty.
That said, there will likely be short-term and long-term impacts. Short-term, we will assess the overall automotive logistics landscape and what is needed to get our customers’ supply chains flowing again. Operationally, the focus will be on getting the right equipment and the right transport capacity to the right places at the right time.
I think the huge shock to the supply chain from this pandemic will challenge some long-held practices and beliefs – Mike Pilver, APL Logistics
Longer-term, we’ll have to see what steps the OEMs take to make their supply chains more resilient and less exposed to future shocks. As I mentioned earlier, we may see OEMs holding more buffer stock or diversifying their supply base. This may imply less emphasis on expedited service and more focus on warehousing and cross-docks to store parts inventory and manage material flow.
The entire automotive industry will have to assess the business environment as the dust settles. As our customers adjust to the new realities in terms of where and how they produce vehicles, APL Logistics will likewise accordingly adjust our business model to be able to support evolving requirements.