IT implementation: Touching the cutting edge
Twenty years ago, parts of today’s automotive supply chain would have seemed like science fiction – plants keeping just a few hours’ worth of highly traceable inventory, unmanned drones being used to monitor site activity, glasses with computer chips in them, self-driving vehicles, and management systems that predict the future, among other things.
Supply chain executives who once pored over spreadsheets and maps to determine the best ways forward are increasingly tasked with overseeing the best technological applications. And the level of visibility today’s OEMs and other supply chain participants have over their supply chains enables systems and processes that would once have been impossible.
Yet despite all the progress, few executives look at their operations today and think ‘wow’. Many are more likely to reflect on their logistical inefficiencies, including areas where manual processes or spreadsheets still dominate, or where uptake of more modern technologies has been slow. In low-margin businesses like car manufacturing and logistics, only a hair’s breadth separates enjoying the long-term benefits of being at technology’s cutting edge and dropping an organisation deep into red ink.
Success tends to come in small steps, rather than giant leaps. Systems implementation takes a long time, investment in new technology and equipment is often small, and resistance to change can be great. The giant leaps mainly appear over time.
One step at a timeCompanies that decide to take the small steps that become giant leaps in efficiency can be inspired by many factors. Consider the actions taken by Darryl Bol, section manager for material management logistics with Subaru of Indiana Automotive (SIA).
Bol was a little more than a year away from the start of production of the Impreza at the plant in Lafayette, Indiana, when he saw an opportunity to introduce a set of coordinated technological applications that would streamline logistics.
In early 2015, he had his first meeting with Mike Meier, president of 3PL provider Venture Global Solutions. From that conversation, Bol sensed that Venture had the systems in place to facilitate the types of process improvements the plant needed to meet its increased production plans.
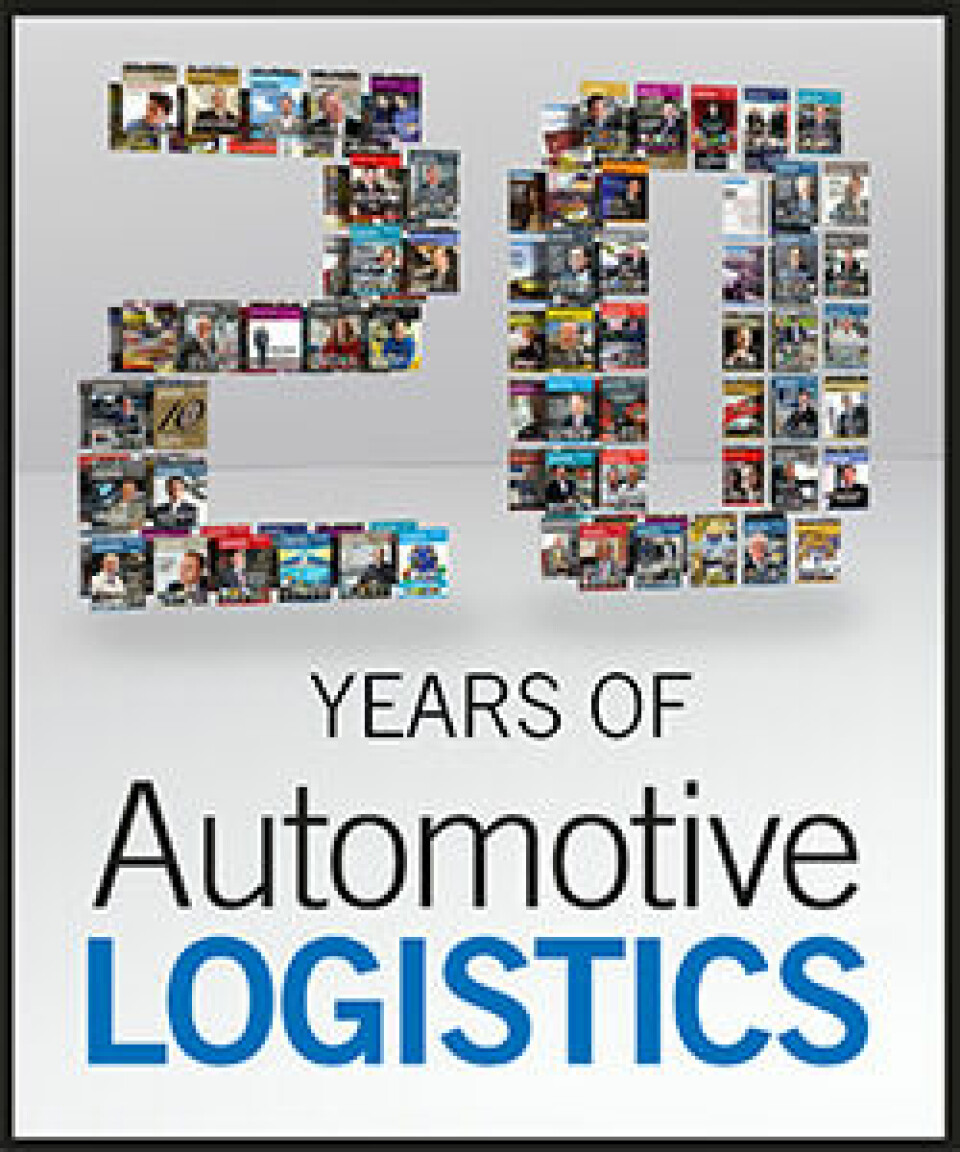
Click here to access more Automotive Logistics 20th anniversary features
“We started discussing the optimisation tools, and what Mike had to offer through this program was flexibility – the flexibility of rapid change to make the entire system smooth,” states Bol.
His vision for greater productivity, efficiencies and visibility within the supply chain went beyond the plant itself, however.
“One of the things in execution of the entire system was changing the culture – not only from a Venture side, but also from the supply base and the people inside our own organisation – bringing them all together and getting that culture shift moving forward,” he explains. “This is not an easy task. We’re talking many different companies that have to come through and mould into one – one direction, one plan, one goal.”
Adding to the implementation challenge for Meier and his team was a February 2016 deadline for a significant increase in line-speed and volume. In a period of under six months, Venture collaborated with Bol and the SIA plant team to test and install a new transport management systems (TMS) while updating the optimisation and crossdock processes at the facility. Venture also added a new yard management system that will eventually use unmanned drones as part of its monitoring programme. From a tracking and visibility perspective, the entire platform is integrated with monitoring and placement for more than 1,000 daily trucks carrying parts and products into the plant.
“We knew that we had the right tools in the technology. We just had to execute it,” comments Meier. “We had the systems in place, and this is why I’m in the business. This is my passion – finding a partner who understands the whole inbound solution. It starts with building the blueprint for the plan, and saying ‘here’s how it’s going to work’.”
The detailed planning and execution of the implementation, which included running more than 30 ‘what-if?’ scenarios, was not without long days and tense moments. After reviewing the processes in the early stages of implementation, Meier, Bol and their respective teams executed a number of refinements that changed the flow within the plant. These changes were implemented in a three-hour period during an overnight shift.
Some 18 months after rollout, Bol says SIA has realised numerous benefits, including a 13% reduction in miles travelled; a dramatic increase in inbound visibility at route and part level; quicker identification of potential issues; more even delivery flows; improved ability to deliver to a specific point in the facility; better visibility across the whole SIA supply chain; and an impressive reduction in inventory.

“Overall, we used to carry about a day’s worth of inventory. We were able to reduce that down to a standard inventory level of about four hours. That can only be accomplished by visibility of the parts flow and ensuring that you have that pipeline full of parts,” says Bol. “You are not bringing in bulk loads at one time. You are bringing in small amounts throughout a long period of time.”
Decision-makers, Bol stresses, need to develop the ability to look beyond the capital investment in such technology projects to the benefits on the other side, in order to realise a vision for productive change.
“From the beginning, we knew this was a direction that we wanted to go in. We got through the challenges by working together,” says Bol. “There was a capital investment involved, but the overall investment will pay for itself over the long term. It’s not necessarily all about money. It’s about how you manage the complexity of your business. That was the real selling point.”
Meier, who was on the floor of the plant for 72 consecutive hours at one point overseeing the initial implementation of the various systems, says the right partnership is critical to success in terms of implementing new technology.
“It’s tough – and I think that’s why people may be afraid of it,” says Meier. “It’s not impossible. It is achievable if you have the right partnership and you believe in one another. You are going to be much stronger as an organisation by doing something like this. It helps to have a good leader with a vision, like Darryl.”
Evaluating investmentsThe explosion in available technology and the increase in the number of logistics-related applications that can be delivered as a smartphone download look set to drive down logistics costs. Despite this, the overall expense involved in some new technology, including cost of training and of transition to a new platform, can still turn a promised cost-saver into a potential money pit – particularly if the application does not meet expectations.
A true test for decision-makers – especially those working for publicly-traded companies whose stock prices are tied to overall performance and the ability to meet analysts’ expectations – is developing processes to identify the actual value provided by a given technology. In some cases, this value can extend beyond the traditional quantifiable measurements of return on investment, where it seeks to meet changing market requirements.
"There was a capital investment involved [in the TMS], but the overall investment will pay for itself over the long term. It’s not necessarily all about money. It’s about how you manage the complexity of your business. That was the real selling point." - Darryl Bol, Subaru of Indiana Automotive
And the market’s requirements are changing, confirms Mel Kirk, senior vice-president and chief information officer at Ryder Logistics. “The supply chain industry is more intensely becoming an order management focused industry,” he observes. “The customer is evolving, with a desire to have a single view of the status of an order – irrespective of where it is at any time or whether it is in movement or at rest. This is forcing an integrated view of the full flow of the order through the entire supply chain.”
Kirk and his team engage in multiple processes to extensively vet the applications they consider for implementation within the company and its networks. Their evaluation calls upon technology providers to show how their application will be most effectively used within the company’s operation. If an application passes the initial phase of the evaluation, says Kirk, Ryder then works with the provider to run proof-of-concept trials, which are focused on its ability to deliver outcomes in areas like customer service, operational productivity and expanded products.
“Ultimately, it has to be better for our customers, shareholders and employees,” comments Kirk, adding that Ryder places significant importance on the user interface, training platform, ease of integration and the ultimate product roadmap. “We are not going to experiment with theoretical technology on the backs of our customers, employees or shareholders,” he says. “We have to press technology to innovate. It’s not the technology that provides the differentiated benefit. It’s the practical application of that technology that is the key.”
[mpu_ad]Penske Logistics, which also employs an extensive evaluation process for potential applications and customisation of systems, often vets technology on its ability to be adapted or scaled into the various markets the company serves across the globe.
“We’re looking for technology that would allow us to operate across the world, in any of the places where we serve our customers. That is always a consideration,” confirms Andy Moses, senior vice-president of global products at Penske Logistics.
“We acquire the best commercially available core platforms in technology. We also have our own application development to fill in the gaps associated with off-the-shelf type software as well as Penske proprietary applications that we develop to meet the highly specific needs of each customer – needs that aren’t necessarily addressed with some of the core platforms,” he adds.
The Amazon effectMost industry observers agree that the culture change driven by Amazon and other online consumer shopping platforms has created a new set of expectations within the automotive supply chain. The ability to buy an item on one day and receive it the next, with full tracking in-between, has stimulated a growing demand for increased visibility.
“The ‘Amazon effect’ and the evolving self-serve preference many of our customers look for today have had a fundamental impact on both how information is provided and the role of customer service. The complexity of an automotive supply chain is far more global than a DC-to-door delivery,” notes Greg Slawson, regional automotive vertical lead for the Americas at DSV. “With EDI as a standard communication system, tactical standards are applied that make it difficult to provide data in the same fashion that you receive in a visual way on your mobile. We are continually refining the ways that our customers have visibility. This is an area where the delicate balance between service and cost is important.”
"[We have] our own application development to fill in the gaps associated with off-the-shelf type software as well as Penske proprietary applications that we develop to meet the highly specific needs of each customer." - Andy Moses, Penske Logistics
Like many of his logistics counterparts, Slawson is optimistic about the possibilities for applications in the future. He believes further development of technology with artificial intelligence could play a significant role in delivering greater supply chain efficiencies. However, he cautions that the supply chain should take care in the application of technology and avoid an over-reliance on it.
“In today’s automotive supply chain, have we already passed an inflection point of over-reliance on technology?” he asks. “I say it depends – how many manual redundancy plans can be implemented at a time while the process still functions?”
Efficiencies gained from the use of technology on a daily basis should offset any short-term drawbacks when a system is not functioning, he suggests.
Elsewhere, in response to demand by automotive sector customers for greater visibility within the supply chain, DHL Supply Chain has sought to leverage its global experience in servicing the more general online consumer market.
[related_topics align="right" border="yes"]“In terms of scalability and the skill set of moving small parcels and being tracked, it’s a skill set that’s inherent within parts of DHL. There’s no point of having innovation and technology in one region if we haven’t got it for every part of the business,” says Michael Martin, vice-president of strategic development for the company’s global automotive sector. “Any technologies that we can bring into our business to keep those vehicles moving and get vehicles with more freight on them will typically bring very large efficiencies.”
The role of big dataOne of the more significant challenges for the automotive supply chain is working out how to deal effectively with the mountains of data generated by current and new applications in the market. There is already a great risk of becoming lost in it all, and that risk can only grow in the future.

Properly mining the data can lead to greater efficiencies and even competitive advantage, however.
“The biggest thrust right now is in the direction of big data, particularly with analytics. One of the things that we discuss with our customers often is the amount of data that we capture in terms of the management of these big supply chains and what that can enable us to do from a perspective of really predicting where things are going,” states Penske’s Moses.
Looking at the future role of technology in automotive supply chains, Srini Muthusrinivasa, global industries strategy director of JDA Software, also sees a value in analysing data. In his view, the changes that are ahead in the next 10-20 years may require manufacturers, suppliers and logistics providers to “break down the walls” on some long-standing approaches to meet the demands of the increasingly made-to-order marketplace that now exists in other verticals. However, he stresses that the most important changes that technology drives will be in how people work together in companies and communicate with customers, not least to keep up with constant change.
“At the end of the day, automotive supply chains have a lot to do with relationships,” notes Muthusrinivasa. “People come first. People have to make the organisation change. Open your mind for better collaboration and visualisation and consider the following: what can and should be automated?
“It’s a moving target in my mind, what I can say about efficiency today. Ask me next year and I’ll give you different definitions of efficiency,” he adds.
“Technology today can empower people to do better, to collaborate better, to gain the visibility better and to make the right decisions fast,” concludes Muthusrinivasa.
"Open your mind for better collaboration and visualisation and consider the following: what can and should be automated? It’s a moving target in my mind... Ask me next year and I’ll give you different definitions of efficiency." - Srini Muthusrinivasa, JDA Software
One trend that underscores the increasing value that companies set in leveraging technology is the space given to teams dedicated purely to innovation, including in the supply chain. Like Silicon Valley startups, these groups have more leeway to try and fail than the rest of the business.
Determining what can be found within big data was one of the reasons Penske formed an innovation team recently, for example. The company’s Andy Moses points to projects focused on data visualisation.
“It’s about ultimately understanding our big data capabilities to help our customers better manage their supply chain. There are a lot of great tools accessible to us right now that were not available just 5-10 years ago,” he says.
Among the manufacturers giving specific space to innovation is Pirelli Tire with its Pirelli Digital division. According to John Godfrey, vice-president of logistics for the Nafta region, the group was established to allow a testing environment for experimentation with potential new technologies and processes.
Pirelli Digital provides Godfrey’s team and others in the organisation with a research mechanism for sharing leads on innovations. Godfrey, as he points out, can pass along the information to his supervisor who can move the prospect up the chain of command. Once it reaches Pirelli Digital, the innovation team makes the initial determinations if the application can move forward into the company’s testing programme.
“If I see something new that applies to my world, I can check with my boss to see if it’s something we might be working on,” says Godfrey. “If we’re not working on it, we can explore it with Pirelli Digital, and it will be possible to fast-track something that might have taken a year or so in the past.”
While Pirelli Digital continues to study ways to mine data, the group has also focused on product development. Pirelli’s Connesso smart tyre, which includes an app that delivers enhanced information on a tyre’s use, is one example of its influence.
On the logistics side, meanwhile, Pirelli is researching the viability of truck platooning that could involve the use of semi-autonomous trucks, and even exploring shared mobility, which will eventually have big impacts for the automotive industry and the way aftermarket services, including for tyres, will be managed and delivered.