IT updates: cost modelling the supply chain
Across several articles, we explore how IT systems are being used to integrate data, visibility and cost in the supply chain. In this final part, we look into why Tofas and Iveco are turning to cost-modelling software to help improve their manufacturing and supply chain decisions
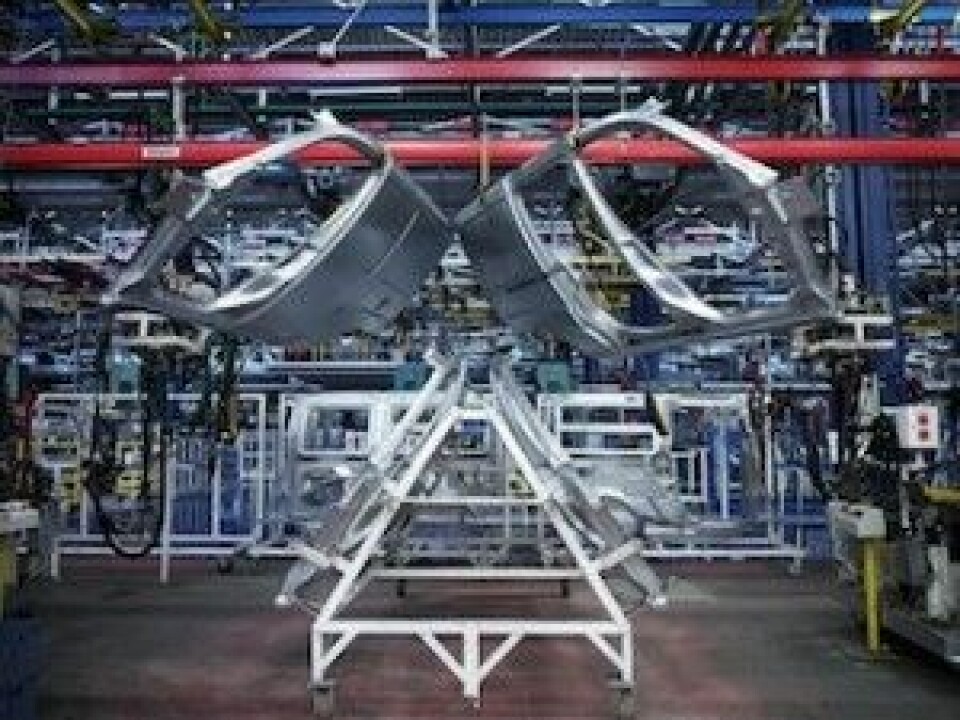
aPriori provides automated cost analysis for Tofas based on the input of different manufacturing conditionsWhile supply chain mapping might be an important tool in understanding the risks in a carmaker’s existing supply chain (read here), another IT tool could help manufacturers make decisions about future supply and production locations.
This past spring, both Tofas, Fiat’s joint venture in Turkey, and Italian truckmaker Iveco, part of the Fiat Industrial Group, signed up with US-based costmanagement software provider, aPriori.
The system provides automated cost analysis based on the input of different manufacturing conditions, locations, volumes and machining tools. The intention is for designers and purchasing managers at Tofas and Iveco to understand the costs of their decisions almost instantly, be it the choice of using a new material or shifting to suppliers in different regions.
Customised cost models
According to Rick Burke, vice-president of marketing at aPriori, OEMs tend to employ relatively few cost engineers to analyse manufacturing and supply chain costs. Such engineers are also rarely called upon to make predictions before the designs of components or products have been established, thus losing much potential to save money.
aPriori, which works with Ford and several tier suppliers, creates customised cost models. A user enters information such as the manufacturing process, the volume, the material and the location, and gets a cost prediction in seconds.
According to Burke, the software can be used at the design phase as well as for sourcing comparisons. “You can look across an entire commodity, like all plastic-injected moulded parts, to make sure you’re paying the right price,” he said.
Given the volatility in product costs, from material prices to logistics, new forecasts need to be made quickly – in a matter of minutes or hours rather than weeks. The system can process an entire bill of materials in a matter of hours. The results serve as a ‘virtual factory’ allowing comparisons of costs such as raw material, machinery, labour, energy, packaging and logistics, across multiple locations.
“Companies can compare the costs of using a plant in Liverpool for its chassis components versus switching to the Philippines,” said Burke. “Of course it’s not just the labour and fabrication costs to consider but inspection, packaging and logistics costs.”

Building a cost database
The company builds its cost database by regularly updating figures from official labour statistics, commodity indices, and directly from tooling manufacturers.
The software also pulls in data from a manufacturer’s ERP system to capture fixed costs specific to each company, some of which might be based on supplier relationships or economies of scale.
Burke admitted that logistics costs, given their variability, tend to be among those fed in from a company’s existing records rather than compiled in the aPriori database. However, while the system will not eliminate the role of a logistics engineer in predicting or mitigating freight costs, the ability to compare at a glance all potential costs could be an important procurement tool, particularly as more global products are launched.