Keeping a yard ahead of the game
Outsourcing responsibility for end-of-line yard operations can present challenges as well as benefits for both carmakers and their logistics partners
In the relentless drive to squeeze cost out of automotive supply chains, specialisation is the watchword. Carmakers increasingly see their own core competence as manufacturing; for their part, logistics providers understand their own core skill set, creating a division of labour that tends to be split at the factory gates. Inbound, providers move automotive components by truck, rail or containers; outbound they haul away finished vehicles.
In this story...
At least, that’s the theory. Yet within the plant are important pockets of logistics activity – ‘supermarkets’ for parts picking and kitting areas; line feeding from sorting centres; yards for finished vehicles – that many OEMs choose to outsource. Such outsourcing can accomplish two important objectives: it transfers activities to companies with a lower cost structure; and it sees those activities carried out by a partner with a core competence in such processes.
This trend explains an industry-wide move for carmakers to relinquish control over end-of-line yard operations, and hand these tasks, together with the finished vehicle, to logistics providers. For the most part – but not always – OEMs entrust their yards to companies with experience of vehicle yard management, such as vehicle processing firms with extensive port and railhead operations.
In some cases, such companies may even be, or have been, part of an OEM. In Europe, Gefco and Groupe CAT manage vehicle yards at plants for Peugeot and Renault, respectively, their former major shareholders. Around ten years ago in North America, WWL bought the vehicle processing and yard management arm of Nissan, Distribution and Auto Service, which has since formed the basis of much of the provider’s in-plant and port yard processing in the region. Elsewhere, Global Auto Processing Services (GAPS), owned by Hyundai Glovis and part of the Hyundai Motor Group, does yard activities at Hyundai Motor’s plant in Montgomery, Alabama, and Kia Motors’ plant in West Point, Georgia.
But there are also plenty of privately established companies working or entering the field. Amports, for example, won the contract to handle post-assembly yard operations at Mazda’s recently opened plant at Salamanca, Mexico. While the Salamanca operation is as yet Amports’ sole venture into post-assembly, in-plant yard management, that may not be the case for much longer. “Amports’ primary focus is port-side vehicle processing,” says Steve Taylor, Amports’ president and chief operating officer. “But while we intend to increase our business offerings to include ‘back of plant’ yard management, we’re not there yet.”
Just as it can make commercial sense for carmakers to hand off the work to a third party with specialist capabilities, logistics companies and vehicle processing firms see a range of possibilities in bidding for post-assembly, in-plant yard management contracts.
To begin with, there’s a strategic appeal to such activities, observes Konrad Zwirner, senior vice-president for international sales and business development at Europe’s Hödlmayr International. Hödlmayr’s experience in this field goes back over 30 years to Mercedes-Benz production at the Magna Steyr contract manufacturing plant at Graz, Austria. Today it extends to five other European plants, including for Ford in Valencia and Cologne, and Audi in Györ, Hungary.
When a logistics provider is involved in the releasing and load preparation of vehicles, points out Zwirner, the resulting efficiencies accrue to both the carmaker and logistics providers, one of which may be Hödlmayr itself.
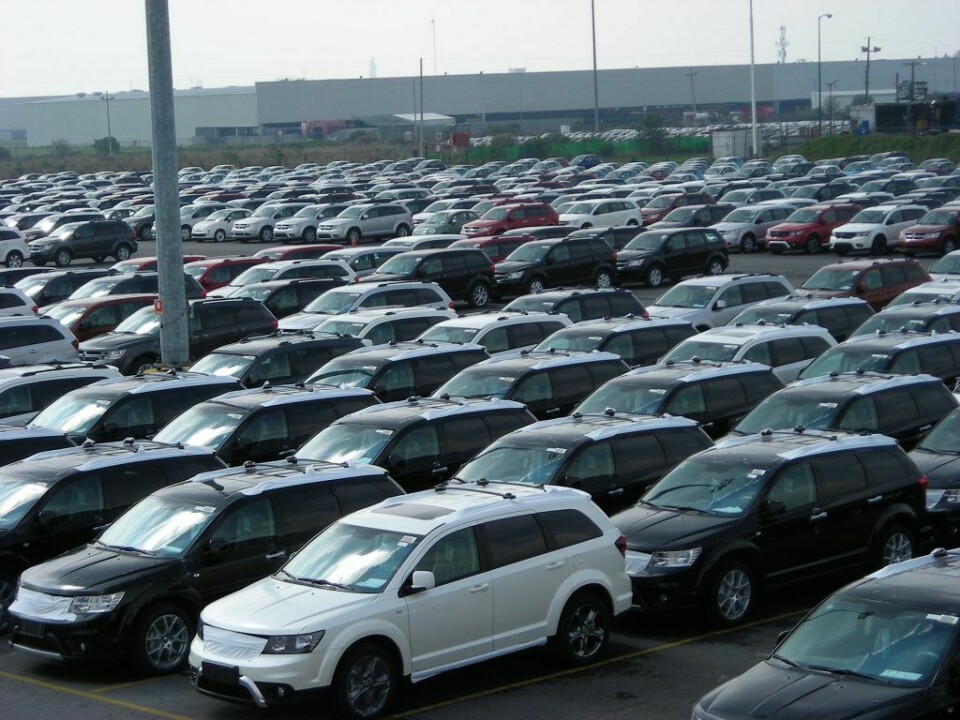
“The value for us is the opportunity to add value, and move away from the commodity business of transportation,” he observes. “It’s not the vehicle manufacturer’s core business, and it helps the logistics provider to be directly involved in the releasing of vehicles, and arranging transport for them. Our strategic position is that the closer we are to the factory’s assembly line, the better.”
What’s more, in contrast to the variable workloads of port and rail head operations, in-plant yard management offers a steady flow of work at volume.
“You’re touching 100% of the vehicles produced at a plant, so if it produces several hundred thousand vehicles a year, you’re earning revenue from all of them,” says Marty Colbeck, director of east coast sales at the Auto Warehousing Company (AWC), which handles vehicle yard operations at a number of GM and Chrysler plants across Michigan, Ohio, Illinois and Ontario. “And often, you’ll typically pick up additional work, such as vehicle movements to handle any off-standard work caused by quality issues, or additional accessory fitting.”
Bill Garrett, president and chief executive at processor and logistics services provider Vascor, agrees. “It’s steady work, it’s everyday work, it’s routine – and there’s room for us to demonstrate a value that the customer will recognise,” he explains. “Plus, we can bolt-on additional services to that base operation, such as inspection, driveaway, ancillary yard operations, plant releasing, and repair tracking and monitoring.”
There’s also an opportunity to bid for periodic off-site work, offering a compound extension should it become congested as a result of downstream logistics bottlenecks or quality ‘holds’ at the plant. Thus, while Vascor handles yards solely for Chrysler and Toyota’s Mexican operations, it has working relationships with many more carmakers, responding nimbly to offer compound space when in-plant compounds fill up.
“We can have an off-site compound open and fully manned within 48 hours – and we’ve done it in as little as 24 hours,” says Garrett. “We have ongoing relationships with landlords right across Michigan, Ohio and Ontario, and can gain access to locations very quickly. Plus, there’s no need to get T1 [broadband] telecommunications lines installed – our barcode scanners have cell phone technology fitted and can communicate back to our servers over a cell phone connection.”
"[In-plant yard management] is steady work... Plus, we can bolt-on additional services to that base operation, such as inspection, driveaway, plant releasing and repair tracking and monitoring" – Bill Garrett, Vascor
Quite apart from the cost and efficiency savings stemming from outsourcing the task of in-plant yard management to a lower-cost, specialist provider, outsourcing offers carmakers the option of re-thinking established business processes – transferring vehicle modification work that might be outsourced to dealers, for instance, to logistics providers at the plant itself.
Don Asdell, president and chief executive of GAPS, suggests that outsourcing yard work to providers can create economies of scale by completing tasks at the point of origin rather than later on. “Handling a campaign at the origin is much more cost effective than dealing with it once the vehicles reach the dealerships,” he says. “The process is repeatable, thus creating efficiency; there are savings on shipping the parts to one location versus shipping to multiple dealerships; and there are manufacturing quality experts on hand to assist and monitor the process.”
However, outsourcing an activity is never going to be a magic wand that miraculously eliminates all problems. Yes, a logistics provider should have higher levels of logistics capabilities, and thus be able to operate in-plant compounds more effectively. But the provider’s presence adds a second entity into the transfer process from assembly lines and onto rail wagons and trucks. As with any activity where two commercial entities work in tandem, much depends on how they work together – especially when the unavoidable profit imperative is potentially pulling them in different directions.
There are, thus, fundamental questions about how yard operators and carmakers work together to achieve best practice, as well as the IT and communication tools they use. For example, how should those managing in-plant vehicle logistics operations interact with the assembly plant?
In the case of IT, an effective yard management tool is often expected to be one of the capabilities that logistics providers bring to the task. Take scheduling, for example. This is not just ensuring that vehicles planned to depart for specific sailings or rail shipments are loaded on time; rather, yard operations involve elements of ‘micro scheduling’, including allocating vehicles to specific parking bays to maximise employee productivity and reduce driven miles and damage risk.
“The location decision is quite important,” observes Hartmut Haubrich, director of finished vehicle logistics at IT specialist Inform, which provides in-plant compound management solutions to the likes of Volkswagen, Daimler, and Audi. “Where is there space? Which route should be taken? And how can drivers be most effectively picked up by bus, and driven back to pick and move the next vehicle to be parked?”

Secondly, technology can help by linking auto-ID capabilities such as barcoding and RFID to yard management systems, thus providing up-to-date data on vehicle location and status, as well as facilitating better planning and management. “The ability to scan barcodes on the units, capture each step in the yard’s processes, and analyse performance using real-time data is paramount to a solid in-plant yard operation,” sums up Vascor’s Bill Garrett. “Focusing on the timely availability of equipment has proved to be very valuable in planning yard activities, labour and the overall flow of the yard.”
Thirdly, yard management technology can also provide insights into opportunities to further improve efficiencies. “Technology is key to improving efficiencies,” says Don Asdell at GAPS. “For example it is critical to track both the location of the vehicle in real time and also the action completed by the employee. We have found that by tracking the labour time standard of each activity, we have been able to improve efficiencies, reduce wasted movement, and foster a competitive nature among departments and employees.”
Taken together, too, these various technologies can help providers and OEMs to minimise the amount of vehicle movements prior to their departing a plant, says Garrett. “Building units that are immediately shippable is top of the list, as units that require repair create congestion and all the usual issues that result from a congested yard: an increased amount of handling, higher damage rates, lower workforce productivity, and spikes in the outbound volumes that must be handled by the carriers,” he points out. “The ideal is a unit rolling off the line and right into a load lane for departure via rail or truck.”
However, the nature of in-plant yard management mitigates against such an ideal, as vehicle yards often serve as abrupt transition points between an assembly line working to ‘first in, first out’ (FIFO) principles, and a compound that must work to shipping priorities. Yard operations – whether physical activities of release and driveaway, inspection, accessorisation and modification or load-building – are by their nature more variable than many of the activities along the assembly lane, and their priorities do not always align, such as in managing vehicles for deep sea transport.
“When vehicles are headed off to remote markets where the sailings are deep sea, or involve long-haul rail, then it’s important to avoid empty vehicle places simply because the correct vehicles weren’t available on time,” says Inform’s Haubrich. “Such vehicles should be prioritised at the inspection, vehicle modification and load building stages – but plant operations people carrying out quality inspections and vehicle fault-fixing activities often have very limited visibility into such sailings and rail departures, and so just follow FIFO principles. But FIFO won’t always be the correct course of action. That’s why we suggest the use of finite capacity scheduling, planning such activities by working backwards from the sailing date.”
Periodic sailings and rail departures aren’t the only interruption to the smooth flow of vehicles headed for the load lanes. Market demands, too, bring their own conflicting drumbeat, including prioritisation of fast-selling or customer-sold vehicles.

“For obvious reasons, end-customer sales require prioritisation over all others, and at Vascor we take great pride in the systems that we have developed to manage the ‘hot or sold’ units, mixing them into the flow of units rolling off the line,” observes Garrett. “This process requires planning, but with our IT capabilities we can easily see which vehicles require prioritisation and take appropriate steps to get them shipped.”
However, says Hödlmayr’s Konrad Zwirner, carmakers don’t always make it easy for their in-plant yard management outsourcing providers to use such systems. Hödlmayr prefers to use its own systems as they have built-in links for transport processes. However, some carmakers prefer that providers use their proprietary systems, even if they lack links for transport.
“In emerging markets, such in-plant yard management and releasing activities are very largely outsourced, so it’s not a problem to use our own yard management systems,” says Zwirner. “But in Europe, there are unions and human resources issues to contend with, because there’s an existing operation in place – and so you have to take over the existing operation, including its IT systems and people.”
For the most part, any resulting inefficiencies are reluctantly tolerated. Yet over time, if logistics providers’ own IT systems do make a genuine difference to a plant’s yard management, the betting must be that they will indeed be installed: the imperative to move vehicles out of the plant and into the supply chain is just too strong.
After all, to paraphrase Vascor’s Bill Garrett, plants don’t stop manufacturing vehicles because the yard can’t cope: it just doesn’t work that way.