Keeping it well covered
Insurance and recovery processes in the finished vehicle supply chain are designed to ensure that the responsible party pays for any damage, but they can also help drive up quality, as Jonathan Ward reports. Additional reporting by Christopher Ludwig.

The fact that a new car rolls off the production line in pristine condition doesn’t guarantee that its eventual owner will receive their new vehicle in the same manner. There are hundreds of opportunities for damage to occur on the journey between factory and customer. Vehicles can be bumped and bashed as they are squeezed into trains, trucks and ships. They can be scratched by drivers in ports and storage facilities and they are exposed to corrosive dusts and chemicals or pummelled by hailstorms.
Carmakers fight this expensive and inconvenient damage on two fronts. First, they take great pains to pick the right logistics service providers, and to enforce handling standards and processes that minimise the occurrence of damage.
Second, when inevitable damage does occur, the carmakers ensure that they have reasonably slick processes for executing repairs (usually at the dealer, but also at vehicle processing and distribution centres) and for recovering the cost of those repairs from the responsible party in the supply chain. The performance of the system as it stands varies significantly by supply chain, say those involved. According to Matt Holmes of newly-renamed Sevatas (formerly known as Pound Gates Vehicle Management Services), some routes work “nearly perfectly”, while others are more precarious. “On some routes, like those from the UK to Europe, we have a situation where there are well-documented handovers, good relationships with the carriers and well-written carrier contracts,” Holmes says. “In those cases [claims] recovery is very straightforward.”
Other situations, by contrast, make it much harder to allocate responsibility, putting more of the burden of damage back on the manufacturer or its insurer. “Rail is one good example,” notes Holmes. “The rail companies that carry the vehicle often don’t load or unload, and they can’t be held responsible for damaged to vehicles carried in open wagons.” Alex Garcia, who works for VW Insurance Services Spain, the group’s internal insurance broker, agrees that recovery rates do vary significantly. “Everyone wants 100% recovery, but that is hard to do, so you end up with a situation where some markets are stricter than others.”
Where a process works, it can usually be made more efficient, and it was here that most of the players we spoke to saw the most potential for improvement. That improvement comes from two principal places: reduced labour requirements and improved transparency.
To reduce the labour involved in inspecting and documenting vehicle condition at handovers in the supply chain, companies use a variety of different techniques. One approach is the use of pairs of inspectors to evaluate each vehicle, one from the organisation delivering the vehicle, the other from the one receiving it. This approach eliminates any chance of a dispute over the source and severity of damage, but comes at a high price. Increasingly, says Holmes, companies agree to outsource inspection to a trusted third party, or adopt an exception basis (where the delivering company’s inspector only checks a vehicle if the receiving inspector notes a discrepancy between the recorded condition of the vehicle and the one in front of him).

These approaches can cut the cost of inspection by up to half, but some supply chains have taken things even further, eliminating interim handovers altogether and agreeing to share the costs of damage for a given supply chain leg, regardless of how it is caused. Such an approach, says Holmes, has proved itself very effective in some tightly controlled supply chains, between two port operators and the carrier running between them, for example. Most supply chain players accept inspection costs as the price of ensuring quality compliance in the supply chain. They do, however, relish attempts to improve the speed at which damage data is passed through the supply chain.
“Our suppliers inspect in the field, record the damage using AIAG standard inspection codes, and feed that information back to us using EDI,” explains BJ Alicandro, vehicle damage prevention and claims manager at Chrysler Group. “Using manual processes might take five to seven days, whereas we want to know right away if damage has occurred.”
Disconnects like these can occur at various points in the supply chain, potentially adding costs and delays, as dealers wait for authorisation to carry out repairs, or claims management companies attempt to recover costs from LSPs. Increasingly, investment in automation is attempting to reduce these issues. Chrysler, for example, is in the process of outsourcing its own damage claims management process to repair specialist Fenkell Automotive Services, which offers a web-based portal through which LSPs can report damage, manage claims, and gain a better understanding of their potential claims based on recorded exceptions. “This system is faster and gives us a beat on the performance of our supply chain,” says Alicandro. “The most important thing to making this work is the timeliness of data. The output of our claims system will be improved data for use in damage prevention initiatives.”
At Sevatas, accelerating information exchange has become an important part of the company’s offering. “Inspectors now use hand-held units with graphical displays to record damage,” says Holmes. “These systems can automatically translate the inspection data into the manufacturer’s preferred damage code system, and the liable carrier will learn in real time that they have a claim coming their way.”
Damage superhighway
Fast exchange of data eases in the administration of damage claims, but it can also allow companies to make material changes to the flow of damaged vehicles while they are still in the supply chain. Traditionally, the dealer repairs damaged vehicles, and the retailers themselves sometimes see such repairs as a useful source of additional revenue. Javier Morales who is in charge of transport quality for VW’s Seat brand, says that only damage that will make a vehicle unsuitable for further transport–such as broken windscreen–is fixed in transit. Other vehicles are repaired at their destination dealership.
At Chrysler, however, opinions have shifted on the best place to execute repairs to transport damage. “We are looking very hard at the impact of damaged vehicles arriving to our dealers, and it is clear that nobody likes to receive a damaged vehicle. Roughly 40% of our dealers have their own body shops, so we are trying to increase the amount of in-transit repair so the receiving dealer can prep the vehicle for the customer right away instead of having to delay delivery. This, along with the innovative damage prevention initiatives we are working on, leads to improved customer satisfaction. When customers happen to be at the dealer waiting for their vehicle we want them to be able to drive it home that day.” As a result, says Alicandro, Chrysler increasingly diverts damaged vehicles to repair facilities situated close to destination ports and railheads, so they can be returned to perfect condition before they reach the dealer.
In some supply chains OEMs attempt to strike a compromise between the cost of damage and the administrative burden of recovery. They may, for example, introduce damage waivers into transport contracts on the assumption that the cost of repairs will be offset by lower logistics prices. Such strategies may be a false economy, suggests Matt Holmes, since they reduce the incentive for the carriers to continually reduce damage levels.
Prevention is better than cure
Even the most painless and efficient repair, claim and recovery process is a big step down from delivering an undamaged vehicle, which is why claims handlers, LSPs and car companies are all extremely keen to gather damage data to root out and fix shortcomings in their logistics processes.
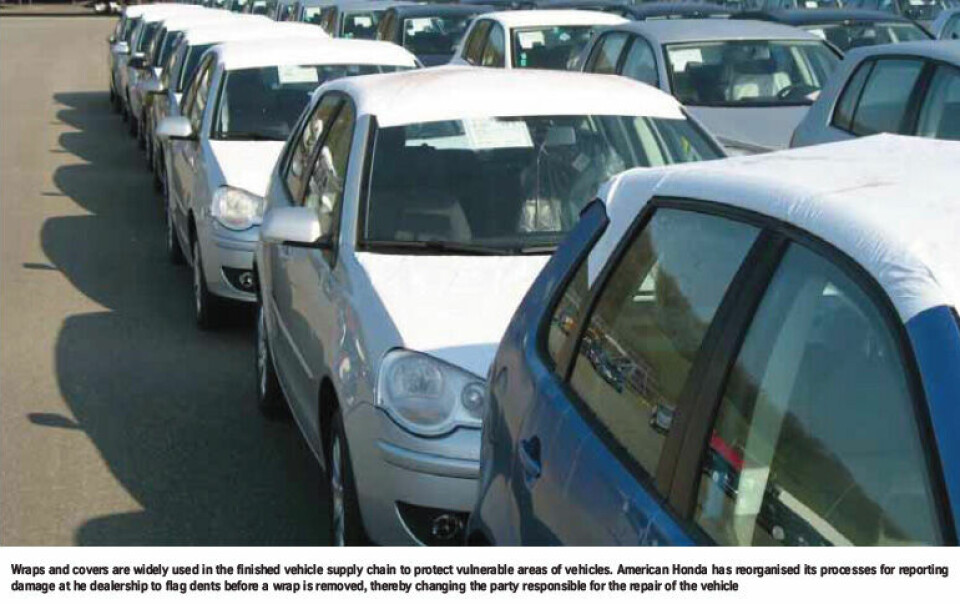
For Ellen Fontaine, general manager of strategic planning and marketing at Vascor Group, a joint venture between APL Logistics and Fujitrans Corporation, data analysis is one of the most important ways that her organisation is able to add value to logistics processes for its clients. “Our analysis department collects data, conducts data preparation and analyses the data by breaking it into smaller parts to gain a better understanding. In addition to routine reports found on our web portal, the analysis group conducts in-depth analysis that provides actionable information that our customers can use to improve their processes.“
The ability to audit incoming claims and work with carriers to identify problems is also an important part of the Sevatas offering, says Matt Holmes, “We had one case quite recently, where vehicles were suffering a lot of very specific front-end damage and paintwork problems caused by an oxidising dust you commonly see in rail transport situations. When we shared our data with the vehicle manufacturer, they were very surprised because they weren’t aware vehicles were being carried by rail.”
Sevatas sent an auditor to review the route taken by the vehicles, and that process revealed that an LSP was, in fact, transporting them by rail for one leg of the journey, and that a separate offload activity onto a very poor surface was the cause of the front-end damage. The OEM was able to encourage its service provider to switch offload operations to a better surface, and to take appropriate action to prevent the rail dust from damaging paint.
At Chrysler, BJ Alicandro says that someone from his Damage Prevention and Claims group is travelling throughout the supply chain for a minimum of three weeks every month, reviewing the processes used by LSPs and helping get to the root causes of damage. “The most common types of damage have been the same for several years” he notes. “The front bumper, the rear bumper, the hood [bonnet], the left front door [for left-hand drive vehicles], and the roof.” A lot of the efforts in the supply chain are focused on ensuring that LSPs are sticking to prescribed methods for handling vehicles. “I began this job a year ago and one of the first things I did was re-write our shipping manual,” says Alicandro. “It was the first major update in ten years and was a big effort; the bottom line is, if our carriers don’t know what they are supposed to be doing we are heading for a disaster before the vehicle even leaves the plant.”
When they are not out in the field, Alicandro and his staff also invest significant time benchmarking, developing and testing improved forms of vehicle protection. “Some changes we’ve made to the system are quite simple,” he notes. “Why do we use seat protection that does not stay on the seats? We are also evaluating new protection options and validating their performance in the field with feedback from our carriers. There is an increased willingness to spend money on vehicle protection, for example, to prevent problems downstream and increase customer satisfaction.”
At Spain’s Seat, Javier Morales says that a number of recent changes have helped to substantially reduce vehicle damage. “The introduction of a new rail link between the factory and the Port of Barcelona was very effective,” he says. “And about three years ago we introduced the simulation of loading and transport processes as part of the new vehicle design process, allowing us to test the vulnerability of our vehicles to damage and to evaluate transit protection.”
While analysis of the data from individual supply chains can help to identify particular problems, there is also considerable enthusiasm in the industry for the value of wider data exchange, with a view to improving standards and the overall performance of the industry. Most of the experts we spoke to were quick to praise the role that industry groups like the AIAG or the ECG are playing in the establishment and promotion of such standards.
Asked about the opportunities for future improvements, the specialists we spoke to could offer a litany of options, ranging from the cheap and accessible to the expensive and complex. At Sevatas, Matt Holmes points out “There is still a lot of paper in the inspection process that can get wet, or fade or blow away or get lost.” This will now begin to be replaced by electronic data collection and distribution systems, he suggests. “Ten years ago, there was a lot of resistance to electronic systems, but we’ve passed a tipping point now.” At Chrysler, BJ Alicandro is looking forward to even greater amounts of automation in inspection. “One of the rental car companies experimented with a full vehicle scanning system to automatically detect damage. That kind of approach would be invaluable in giving a fair, consistent and unbiased evaluation of damage.” Even without such hi-tech solutions, however, Alicandro points out that better uses of more mundane technology, like digital photographs of damage, could help to deliver improved consistency today.
Better weapons for the battle against the elements are an important concern for Seat’s Morales. “I’d like to see greater use of hail nets at all our vehicle storage areas,” he says. “Covered storage is obviously the best option, but that is not always possible or economically viable.”
Whatever car companies and LSPs do to reduce the cost of damage in vehicle distribution, there is no doubt that the pressure to do so will be unrelenting. “Our insurance only covers catastrophes in the supply chain, so I’m the last line of defence before the company has to bear the costs,” concludes Chrysler’s Alicandro.