Kia West Point: Midnight freight trains to Georgia
In this story...
- The need for precision
- A multi-party approach
- Paving the way
- A model for automotive
- Keeping a distance
The use of an inland port in Cordele is helping carmaker Kia to achieve the reliable, transparent supply chain it requires at its 24-hour production operation in West Point, Georgia – even for parts from South Korea
Since Kia opened its plant in West Point, Georgia in November 2009 – at the time the South Korean OEM’s first in the western hemisphere – the factory has become one of the most important globally for the carmaker, as well as for the wider Hyundai Motor Group. Last year, according to the Automotive News Data Center, Kia produced around 351,000 units at West Point, close to its 360,000 annual capacity, while through July this year volumes were up 10% year on year. The plant is currently running 24 hours a day for five days per week, as well as some Saturdays. With a number of model changes in the pipeline, Kia is gearing up for further growth.
West Point, about 80 miles (130km) south-west of Atlanta, is also among the OEM’s most complex plants for product and parts variety. Today, it assembles the Kia Optima, a midsized sedan, along with the plant’s flagship Kia Sorento, a crossover SUV, while also building the Hyundai Santa Fe, another crossover. A version of the Santa Fe is also built at Hyundai’s plant in Montgomery, Alabama, about 90 miles south-west of West Point.
[sta_anchor id="1"]It’s an operation that depends on strict precision and reliability in the supply chain, as well as flexibility. The plant uses two on-site sequencing centres, as well as a number of local warehouses – all of them managed by lead logistics provider Glovis America, a division of Hyundai Motor Group’s logistics subsidiary – to smooth parts handling, allow the use of more standard packaging and reduce line-side inventory. Suppliers deliver to these centres and parts are then repacked in sequence with production.
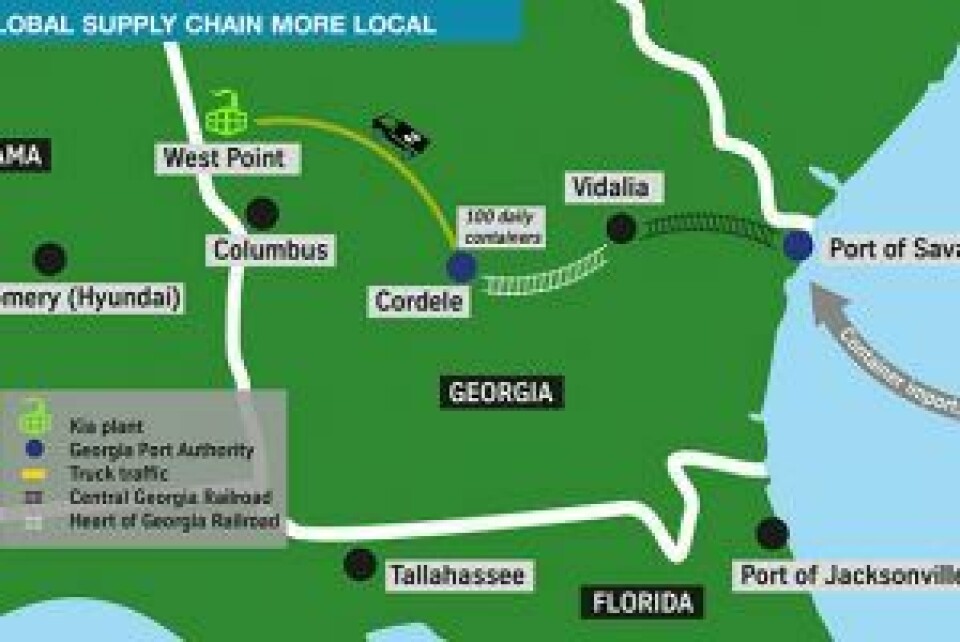
Kia's multimodal connections – click to enlarge
Kia’s growth in Georgia has spurred an expanding local and regional supply chain, with suppliers building or expanding production locally. However, with a significant base of South Korean and Asia-based suppliers, and vehicles built on global platforms in West Point, the carmaker also has a significant amount of imported material that arrives at the plant by sea.
Kevin Kinsey, head of department for procurement at Kia Motors Manufacturing Georgia (KMMG), explains that the carmaker does not necessarily want tooling in three different locations for the exact same part. “We try to look at what is the best for the company logistically. Many times, it will be built in Korea and exported to other plants,” he says.
“Therefore, we may take a bit of a hit for parts going into another facility, but it all balances out. Our global headquarters looks at it holistically,” he adds.
The volume coming from overseas is not marginal, amounting to around 50 containers imported per day that arrive at the port of Savannah, some 275 miles from West Point.
Kia’s production requirements pose challenges when managing material across long supply chains – not only from overseas, but also the distance between the port and the plant. “We wanted to bring the material near to the plant to provide Kia with better access to it, especially since KMMG is a 24-hour operation for most of the week,” says Kinsey.
Along with material call-offs, the imported volume has also required considerable trucking resources from the port to the plant – resources that, according to Kinsey, have become scarcer owing to a shortage of drivers and chassis. “Chassis are a commodity and it is about who can get to them first at times,” he declares, pointing also to the rising costs of drivers and regulatory restrictions, such as rules about driving hours, which contribute to the problem.
"The new intermodal centre reduces our costs by enabling us to bring inbound railcars closer to the plant, which provides several benefits. Among them [is] the potential for shorter-distance expedited orders." - Kevin Kinsey, KMMG
As volumes have increased and trucking capacity has become more of a worry, Kia has sought solutions for storing imported material closer to the plant, as well as to use rail to move the containers more efficiently. The carmaker first looked at bringing in the containers by rail directly to the plant, however Kinsey notes that, because of the significant flow of finished vehicles on rail from the plant, the tracks would not be able to accommodate inbound trains.
[sta_anchor id="2"]A multi-party solutionFacing this challenge, Kia worked together with the Georgia Ports Authority (GPA), which runs the port of Savannah, to come up with proposals to improve the carmaker’s imported supply chain. Upon learning that Kia was looking for streamlining options, John Trent, GPA’s senior director of strategic operations and safety, suggested Kia tap Cordele Intermodal Services (CIS), which runs an intermodal centre at the Crisp County Industrial Park at Cordele, Georgia, about 200 miles from the port and 125 miles south-east of West Point.
The idea was that Kia could move containers from the port to the Cordele centre, where containers could be stored and staged, and dispatched to the plant on demand by truck for just-in-time delivery. The advantages were plain: using rail on the main route would help reduce trucking requirements and thus alleviate equipment and driver bottlenecks, while storing the containers closer to the plant would allow Kia more security and flexibility.
“The new intermodal centre reduces our costs by enabling us to bring inbound railcars closer to the plant, which provides several benefits,” says Kinsey. “Among them [is] the potential for shorter-distance expedited orders.”
While the concept might be fairly straightforward, making the link work has been a multi-party as well as multimodal project, including Kia and the port authority, but also CIS, class one and short-line railways, and trucking providers, to name a few.

It starts with careful control and planning at the port of Savannah. Griffith V. Lynch, executive director of GPA, says that it monitors KMMG’s cargo prior to its arrival; while the containers are still on the water, it ensures that all documents are in order to allow the immediate availability of the cargo, with no customs holds, for example. It also offers flexibility on having truck gates available to move priority containers.
The Cordele centre was chosen as the key link in this new chain for several reasons. The terminal has been operating as a GPA affiliate since 2013, and Cordele Intermodal Services is part of GPA’s Network Georgia initiative, a state-wide logistics plan in which GPA is establishing rail hubs around the state.
Rail connectivity was obviously critical; Savannah has links with class one railways Norfolk Southern and CSX Transportation.
CIS procures the rail services to Cordele on Kia’s behalf, offering a five-day weekly service with next-day availability. The rail link is itself a collaboration between class ones and short-line rail operators – a setup that Kinsey suggests is an advantage in terms of getting the dedicated service that Kia needs. Containers arrive at Savannah, where Norfolk Southern handles them at the Garden City terminal. The company then moves the containers (marshalling them rather than by rail) to short-line railway Georgia Central, which rails them from the terminal to an interchange at Vidalia, roughly halfway between Savannah and Cordele; here, the cargo connects to Heart of Georgia, another short-line railway that serves Cordele directly.
According to Kinsey, the short-line railways move freight efficiently at night, allowing Kia to avoid using the class ones’ busy service. Overnight transit time from Savannah to Cordele is about ten hours.
“It is a great opportunity to work with the local community and get what we need at the same time, which is to bring our freight closer to us,” says Kinsey.
[sta_anchor id="3"]Paving the wayThe Cordele terminal itself has also seen significant investment to prepare for the new operation, including a new paved yard area of around seven acres (2.8 hectares), and a total space for parking and truck staging of around 12 acres, according to Jonathan Lafevers, president and chief executive of Cordele Intermodal Services.
Around 50 containers are transported per train, Lafevers says, most of them 40ft. “We handle about 100 containers daily for Kia [including the return load], which equals about 2,000 monthly and 25,000 annually,” he says. “Our capacity is now about 3,000 to 4,000 containers, depending on the stacking height, which averages about three high.”
Upon arrival at Cordele, containers are typically available within one hour. When KMMG needs parts shipments, the containers are transferred to truck chassis and delivered to KMMG as just-in-time inventory. Lafevers says the operation now includes about 250 new chassis for Kia.
Lynch adds that staging cargo in Cordele gives KMMG the ability to control the timeliness of freight delivery. “This freight will have already cleared customs by the time it gets to Cordele, so orders can get moving immediately,” he explains.
CIS estimates the inland port will eliminate 6m truck miles each year. For Kinsey, the closer access to production material is as important as the transport savings. “With the intermodal centre, we value the convenience of access to our parts. There is a tremendous value in preventing parts shortages, and most extremely to preventing production downtime,” he says.
While the intermodal service ultimately offers Kia better access to material, Kinsey adds that backup measures are necessary to ensure that freight can be expedited directly from the port if required. “CIS is a full-service operation that also has infrastructure in Savannah if we need a faster method that would bypass the Cordele facility,” he says.
Since going live this past summer, the centre has continued to expand operations. In September it was certified for C-TPAT (Customs-Trade Partnership against Terrorism), which required the installation of security measures including perimeter fencing, barbed wire and lighting. CIS also plans to start operating 24 hours per day by the autumn, increasing from its current opening hours of 6am to 6pm.
The intermodal centre is set to reduce costs across Kia’s inbound supply chain. “This is going to allow drivers to have better turns, fewer chassis in the system and help us from a standpoint of profitability and logistics efficiency,” says Kinsey.
“This model drives out waste and redundancy in the supply chain, delivering greater efficiency for customers and environmental benefits through reduced diesel consumption,” says Lynch.
Kinsey says that KMMG and CIS have been collaborating since March to minimise any challenges and to ensure a smooth start-up. “The ‘Kia Way’ philosophy is built on trust, and our relationship with Cordele has been very positive,” he says. “We know that with the one system, one team element of the Kia Way philosophy, we are working together for a better future and can overcome almost any challenge that we face.”
[sta_anchor id="4"]A model for automotive?For Kia, the Cordele facility handles only imports, mostly from Korea as well as other countries, but the feasibility of the inland port depends on other customers and freight as well, including using return loads from Kia for potential exporters.
Lynch notes that the influx of empty containers at Cordele from Kia imports, for example, provides new shipping capacity for exporters across south-west Georgia, south-east Alabama and north-west Florida. GPA plans to help other port customers use the link effectively, which would not only boost business for CIS, but could save customers money by using rail instead of road for the 200-mile transit to the coast.
“Lowering the cost of export will help Georgia products be more competitive on the global market, and aid economic development within the state, which is a central purpose of the GPA,” says Lynch. “This expansion of lower-cost transit via Cordele rail also aids the port of Savannah’s initiative to capture more cargo from within the CIS service area.”
Indeed, the success of Cordele is setting a precedent for the state to invest further in inland ports and terminals. “Seeing rail cargo as a growth opportunity, the GPA is establishing inland rail terminals throughout the state. Shifting more cargo to rail takes advantage of high-volume train movements, reducing truck traffic on Georgia highways,” says Lynch.
"We handle about 100 containers daily for Kia, which equals about 2,000 monthly and 25,000 annually. Our capacity is now about 3,000 to 4,000 containers, depending on the stacking height, which averages about three high." - Jonathan Lafevers, Cordele Intermodal Services
On July 22nd, for example, the GPA’s board of directors, together with the state government, approved $19.7m for a second inland terminal in the state at the Appalachian Regional Port in Murray County. Located in northern Georgia, this inland port is close to the border with Tennessee, not far from Chattanooga, where Volkswagen has a factory, and other automotive plants in Alabama.
“The KMMG-CIS agreement serves as a good business model for other auto plants,” says Lynch.
Indeed, the Cordele model itself has parallels to other successful inland port and intermodal supply chains in the automotive industry. Over the past three years, for example, BMW has used an inland port in Greer, South Carolina, close to its factory, as a similar staging centre for inbound containers arriving by rail from the port of Charleston. The daily train service there replaces around 25,000 truckloads per year.
Local mattersThe Cordele intermodal centre is now an integral part of Kia’s sourcing strategy. Kinsey emphasises that because KMMG’s products are global models, supplier decisions are coordinated between the plant and Kia’s headquarters in Korea. To that end, he anticipates imported volumes continuing at high levels through Savannah and Cordele.
However, local and regional supplier localisation is increasingly a driver for Kia’s supply chain in the US and North America. Kinsey points to the NAFTA requirements of a vehicle having at least 62.5% of the value of parts sourced within North America to qualify for tariff-free export across the US, Canada and Mexico. However, local sourcing is increasing beyond those requirements, often to the benefit of logistics costs. Kinsey reveals that the carmaker has not recently added any new South Korea-based suppliers at a tier one level, instead looking to local suppliers.
He points in particular at localising parts that may be specific to the American-built version of its models, such as higher technology content and features. “If Americans want something different than do Koreans, we would look at trying to source that locally.”

Kinsey points out that shipping a small part from Korea versus a large part also has significantly different costs. If it is a large, painted part that could be damaged easily, Kia prefers to use a local supplier to avoid multiple handlings and increased packaging costs.
The carmaker’s regional growth – in September it officially opened a plant in Pesqueria, near Monterrey, Mexico – should also strengthen its North American supply chain further.
“As we introduce new models and grow in the community, we continue to localise with our suppliers as well,” says Kinsey. “We are always thinking about this key strategy. With the building of the new Kia facility in Mexico, it also gives us a new opportunity to utilise some of the suppliers there. KMMG can benefit from their knowledge and expertise and look at using them for future sourcing.”
[sta_anchor id="5"]Keeping a distanceFor now, however, Kinsey admits that there is little connection between Kia’s supply chain for Georgia and the Mexico plant. Both plants currently build different model types, with Mexico assembling the small Kia Forte, while Georgia focuses on a larger sedan and SUVs. Kinsey describes KMMG as currently being “pretty hands-off” about the decisions made by the new plant. It has instead focused on upcoming model changes. In future, however, he believes the two plants will have opportunities to share more logistics.
“One example would be reverse KD [knockdown] parts exchanges. If Mexico wants some parts from the US, we can optimise our runs back and forth,” says Kinsey.
Perhaps also surprising is the degree to which KMMG and its supply chain operate separately to Hyundai’s plant in Alabama, and to a certain degree its logistics as well. Purchasing, for example, is completely separate at Hyundai and Kia. Kinsey describes the two plants and car brands as having a kind of “stepbrother-stepsister relationship”.
“We do not share information; we do not talk about costs. We are two separate businesses,” he says.
There are exceptions, however, particularly if one plant has a shared supplier that is in trouble or falling behind. In that case, the supplier may be able to supply one of the carmakers from its Georgia rather than Alabama plant, or vice versa.
However, there are links that go deeper. KMMG builds a Hyundai vehicle, for example, which would mean both common suppliers and some Hyundai material imported from South Korea for the Georgia plant.
"Lowering the cost of export will help Georgia products be more competitive on the global market and aid economic development within the state... This expansion of lower-cost transit via Cordele rail also aids the port of Savannah’s initiative to capture more cargo from within the CIS service area." - Griffith V. Lynch, GPA
In large measure, however, logistics optimisation between Hyundai, Kia and other companies is left to Glovis America. The logistics provider works with various carriers, importers, warehouse providers and 3PLs directly, some of which may overlap between the carmakers.
There are cases in which Kia’s supply chain is separate to Glovis as well, however.
“KMMG is a bit different in that we allow suppliers to say that they want to use carrier A, for example,” says Kinsey. “Although we may use carrier B, as long as they meet our costs, we are okay with that. We have some carriers that do not use Glovis’s 3PL services because it is not necessary, but for the majority of our suppliers, Glovis handles everything.”
One system to trustIn sourcing more material from local suppliers, Kinsey emphasises that Kia must verify quality and processes. For example, the carmaker is currently running systems checks to ensure its suppliers’ IT systems are compatible, backed up and running well. An internal group at the company also carries checks on quality and capacity, and does safety checks to make sure that the suppliers are meeting Kia’s standards.
“With the high mix and the sheer number of types of vehicles that we run here, capacity is always a challenge to make sure our suppliers’ lines are running as well as they can,” he says. “We are always working with suppliers to ensure that they have the information needed to send the supplies to us. Our sequencing centre provides a little bit of a buffer, but we are talking only hours – not days.”
Building buffers to allow greater efficiency and security of supply is key in the Cordele intermodal centre as well, which, like other parts of the carmaker’s supply chain, has required tight communication across all stakeholders.
“We try to do things together [with suppliers and providers]. We have one system that governs and drives all of the activities,” concludes Kinsey. “Trust is the number one part. A team is a group of individuals that trust each other.”
The complexity and volume of parts at Kia’s Georgia plant has led to increased use of parts sequencing, for which Kia and Glovis have added or expanded a number of logistics centres and warehouses.
According to Kevin Kinsey, the sequencing centres are helping Kia reduce inventory levels in the plant and at the line side, as well as to control parts and quality, while optimising packaging.
“[At KMMG] we have a lot size of one Optima, Santa Fe and Sorento, so we need high flexibility in packaging,” he explains. “A sequencing centre helps us to manage that better. If we bring in cases of 50, we do not want 50 parts sitting on the line, which could be two hours of inventory, so the sequencing centre helps control that. We do internal sequencing as well at a couple places in the plant for large parts such as hose assemblies.”
Glovis operates two sequencing centres directly at the plant, including one that handles most of Kia’s inbound knockdown parts; it also has a number of sequencing centres in the area for local suppliers. “For example, mirrors come from a number of suppliers and we sequence them at the sequencing centre rather than having three or four centres online; we pull from the sequencing racks and deliver [to the plant],” he says.
Glovis continues to expand its footprint around Kia; it recently built a new warehouse near West Point, shifting from a location in Valley, Alabama, close to the Georgia border. The Alabama warehouse, which served Kia exclusively, had less room to expand and had higher logistics costs than the new warehouse in West Point offers.