Upskilling and training at Audi
How Audi strengthens its supply chain: The key role of employee resilience
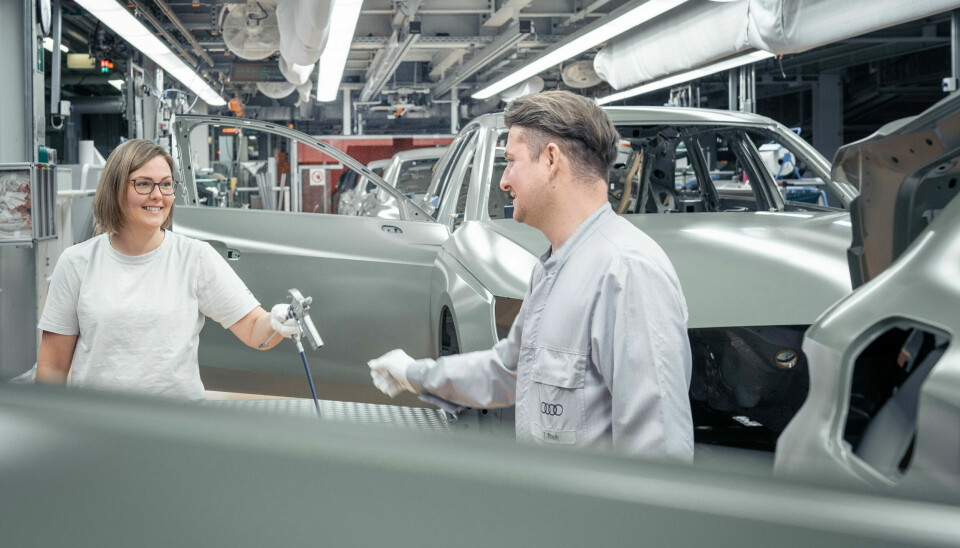
Times are volatile. But the challenges facing logistics and supply chains can be overcome if teams are accustomed to dealing with adversity. Practitioners share how employees can become more resilient in times of crisis.
After the crisis comes the crisis. And that doesn't necessarily have to be a bad thing. This is the impression you get when listening to Dieter Braun, head of supply chain at Audi. In our sister site Automotive IT's podcast "What Moves Me," he doesn't lament the volatile VUCA (volatility, uncertainty, complexity and ambiguity) world, but rather, with a view to the recent past (pandemic, chip crisis, wars, etc.), he praises his "highly crisis-tested team, capable of optimally dealing with rapidly changing conditions". One could say: Practice makes perfect.
In addition to multiple baptisms of fire in practice, Audi has also helped employees with a "resilience program" that teaches them how to better cope with stress. "Because ultimately, it's the employees who have to make the right decisions," emphasises Braun. "Resilient logistics only succeeds with resilient employees." Therefore, developing such skills is becoming increasingly important. But how do managers and employees themselves even recognise whether they are resilient?
How employees recognise their resilience
"Resilience is a technical term. It describes how well an object returns to its original state after being subjected to pressure," explains coach Renate Sperber. Therefore, you should ask yourself this self-test: How well can I relax after a day at work? Can I still switch off? Can I enjoy myself? Have I changed? Do I feel like I can't make a difference? "A resilient person doesn't assume the role of victim," explains Sperber. "They have a strong sense of coherence."
This is based on three components: comprehensibility, manageability, and meaningfulness. "A person with a high sense of coherence is more likely to react to threatening situations with situation-appropriate and goal-oriented feelings," explains the expert. "People with low coherence tend to experience diffuse, difficult-to-regulate emotions, such as blind rage or fear. They become incapacitated because they lack the confidence to solve the problem." This must be avoided. And it is possible. "Our experience is that resilience can be trained," says an Audi spokesperson, referring to the resilience program that was launched in logistics at the height of the semiconductor and coronavirus crises.
However, it doesn't always have to be extreme situations that are challenging, the OEM emphasises: "In the logistics industry, disruptions are part of everyday business." Traffic jams on the highway are enough. "That's why it's so important that our employees are both process experts and have personal resilience to stress."
The Supply Chain Resilience Program, which has been running since 2021, has two core elements aimed at maintaining the health, performance, and motivation of employees despite increasing pressure throughout the supply chain.
- Resilience Dialogues: Participants have the opportunity to receive input from experts (such as coaches, psychologists, experienced Audi employees or doctors) in a protected virtual space and then to deepen their understanding in group work.
- Resilience Wheel: A questionnaire measures resilience at the individual, team, and organisational levels within a department. The questionnaire is part of a metric-driven concept known as the "Resilience Wheel". It enables an annual assessment of resilience competence, which is supported and promoted in subsequent formats—in collaboration with Audi Healthcare.
This is supported by a series of health-promoting measures. "Resilience doesn't only become relevant in a crisis; rather, it begins with structural preparation through stable processes, is anchored in the corporate culture, and grows steadily through the joint mastery of new challenges."
How do you become more resilient?
At Audi, four skills are central to helping employees become more resilient: First, the ability to analyse large amounts of data and derive informed decisions from it. This also includes knowledge of data visualisation and interpretation. Second, a holistic perspective, because every decision in global logistics can have enormous consequences. Third, the ability to respond quickly and creatively to unforeseen problems, which requires analytical thinking and flexibility. Fourth, the willingness to change.