Looking down the rail lines
India is enticing private investment in its railways while the US is looking to improve cycle time. Meanwhile Europe’s rail surplus allows little room for design development.
Rail’s share of the automotive outbound market fluctuates wildly between continents. In North America, railways haul 70-75% of output, while in Europe they move 30-40%, with short-sea shipping capturing a similar share. In India, less than 5% of finished vehicles move by rail.
That modal fluctuation is currently mirrored by varied market and regulatory environments. In the US, wagon producers want more multi-level equipment to meet growing demand, while in India changes to legislation will prompt the introduction of the first privately owned wagons. In contrast, European operators have a surplus of equipment, with vehicle production in decline.
Insufficient design in India
In India, vehicles are moved mostly by road. However, road congestion is eating away at reliability, while legislation currently under review could see loads cut from ten to eight units, a productivity loss that could make rail more attractive.
The wagon fleet of state-owned Indian Railways reflects its small role in the transport of vehicles. It owns just seven rakes (block trains) of old passenger coaches (NMGs) retrofitted to carry vehicles. Each rake is composed of 25 wagons and can accommodate a total of 125 Maruti Suzuki Alto-size vehicles (a small car). It also operates two rakes of bi-level, converted container flat wagons, called BCACMs, with a capacity of 270 Alto-size cars. It has another rake with a wagon type called a BCCN, which has a similar capacity to NMGs.
Some of the vehicles that are moved by rail include Maruti Suzuki exports from Gurgaon to Mundra port using the BCACM wagons. There are also exports of vehicles in containers that move to ports by rail.
So far, Indian Railways owns all the specialist rolling stock. Industry sources confirm the wagons are neither technically advanced nor reliable, as the NMGs are more than 20 years old. Worse still, their original design rules out carrying the larger hatchbacks popular in India today.
Knowing that the industry needed a change, the government mooted a new policy in 2010 aimed at attracting private sector investment in the transport of finished vehicles by rail. Unfortunately there were no takers, as companies deemed that the Automobile Freight Train Operator (AFTO) initiative did not make for a bankable business plan.
Both the government and the railways subsequently consulted widely and a new, more flexible AFTO is to be launched that should make investment by the private sector more interesting. The first steps were taken in February when the revamped policy was put forward, but those showing an interest have yet to see whether both rates and investment structure will make owning private rolling stock viable. Thereafter, it will be the price of the wagons that dictates whether they get built, or not.
Bill Villalon, senior vice-president of global automotive for APL Logistics and chairman of the APL Logistics Vascor joint venture in India, says the company is studying this market carefully. “The geography of India is one characterised by very long distances between production and consumption centres, making it ideal for rail,” he says.
APL Logistics has been in discussion with various OEMs about rail pilot projects, which would initially use Indian Railways’ converted passenger rolling stock. The aim would be to acquire a more sophisticated product as soon as possible. “Infrastructure, such as terminals, will have to be built up, and we are definitely interested in this area, too,” says Villalon.
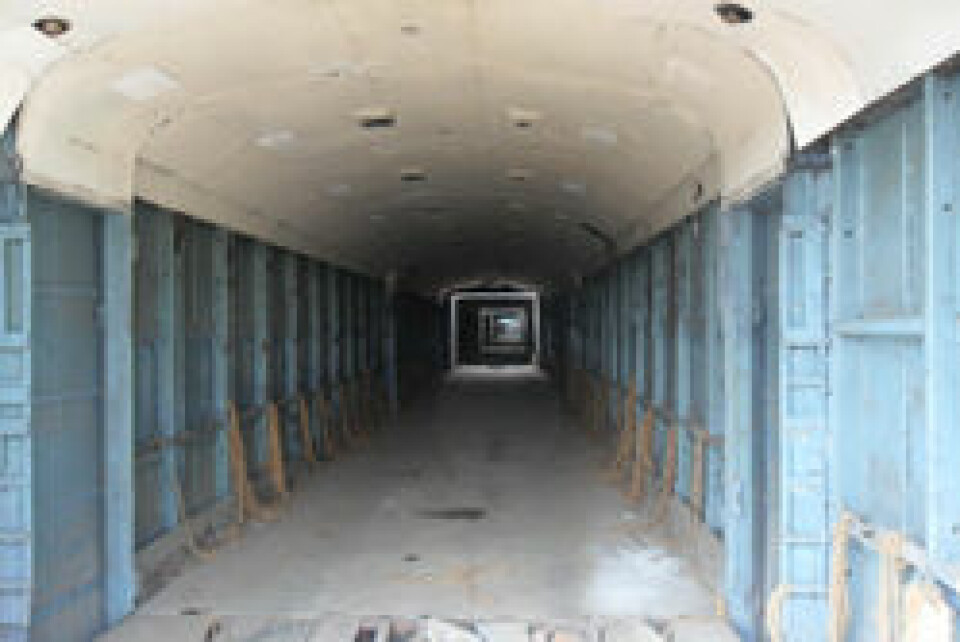
Villalon believes that existing space at container terminals will be used to store vehicles, though he predicts more dedicated facilities will emerge to provide ancillary services, many of which are being done today at dealerships, including customisation and fitting accessories.
However, suitable rolling stock alone will not immediately solve India’s problems. A hotchpotch of state-based taxes has led to many regional stockyards rather than large centres where volume could be aggregated and more efficiently moved by rail. There are plans for a nationwide Goods and Service Tax (GST), but they have been delayed for years. “Moving to a more uniform model under the GST scheme will make volumes denser in nature, which plays very much into the hands of rail,” says Villalon.
Villalon believes that fundamentals in India point towards rail. “All we now have to do is get to a workable policy in place,” he says. “We have been talking to all the OEMs and there is a clamouring for an improved rail option. Indeed, nobody can see a way forward that doesn’t involve rail.”
"We don’t have an upper limit in mind as to how many rakes we might eventually acquire. We want to achieve maximum utilisation, whether by loading in both directions or triangulating" – Bill Villalon, APL Logistics
Two new rolling stock designs are currently under development. The BCACBM was designed by Indian Railways’ in-house team, while the so-called COR wagon has been developed by Titagarh Wagons in conjunction with APLL-Vascor. Both are bi-levels, given that in India tri-level wagons are constrained by overhead wires on its electrified network. However, tri-levels may eventually run on the so-called Indian Dedicated Rail Freight Corridor, although they could not then cross over to the core network to access freight depots.
Villalon says that APLL-Vascor is supportive of the COR wagon design, since it can accommodate smaller, but taller SUVs. “We believe the COR wagon can carry more potential models and mixes of models than any of the other [designs],” he states.
Indian Railways’ basic plan calls for the investor to build a minimum of three rakes under the AFTO policy, which would cost a combined $8m-9m. Each rake will accommodate 318 standard-size vehicles.
“The market potential goes into the hundreds of rakes; it is certainly a big market,” says Villalon. “We don’t have a specific upper limit in mind as to how many rakes we might eventually acquire.”
He adds: “We want to achieve maximum utilisation, whether by loading in both directions or triangulating, although hauls will vary between 1,400km and 2,600km. If everything goes according to plan, we might see operations commence towards the end of this year.”
North America adds capacity
As volumes rise in North America, there has been concern over a shortage of auto wagons (called railcars and auto racks in the US). The shortage began in 2011, however equipment builders have been ramping up production after strong new orders. The industry is expected to add around 4,000 railcars in the next year (see FVL North America conference report) but there are questions over whether that will be enough as Mexican production increases in the coming three years.
According to Rob Ortner, senior vice-president for sales at railcar manufacturer TrinityRail, the demand is for a mix of 90ft racks in bi-level and tri-level designs, and for convertible versions that can adapt to changing consumer demand.
“Designs continue to evolve, although adding more cubic capacity within the railroad clearance lines is a challenge,” says Ortner. “Some articulated cars have been on the market for several years, but have not gained much share versus the standard length cars due to limitations at the terminals and need for additional switching efforts by the railroads on the longer cars,” he says.
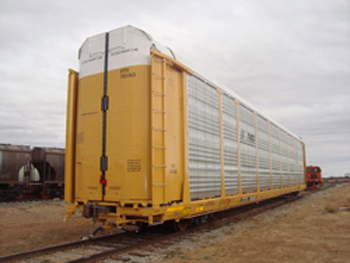
Ortner estimates the equipment being built today should last about 30 years, although this implies a potential mid-life rebuild. He adds that the industry has worked together to improve the ‘maintenance-free’ aspects of auto racks, including approaches to painting preparation and the use of isolators to keep metal from rubbing against metal, which would potentially lead to rust. Many moving parts have also been designed to reduce maintenance during the life of the wagon.
Ortner says that for the 90ft railcars, a tri-level configuration would often handle 18 vehicles. However, on the available articulated tri-levels, up to 24 small vehicles can be carried. “Those quantities are likely to remain the maximums that can be accommodated within that design,” he says.
The industry is also developing technology to track and communicate with moving wagons, including the use of sensors detectable by satellites. “It is still very early in the development phase, but we would expect this to gain favour in the future to be able to monitor train action forces, to check whether doors are closed and locked, and to check on other factors regarding the running gear and brakes of the flat car beneath the auto rack,” says Ortner.
In Europe, with the current set of rules, we have reached the loading limit with existing equipment. To accommodate more vehicles, new ways of thinking would be needed – Philippe Robert, Gefco
Union Pacific Railroad (UP) owns or leases more than 15,000 multi-levels, which account for roughly 30% of the national multi-level pool. “Union Pacific has also led industry initiatives that have improved multi-level cycle time and thereby enhanced multi-level utilisation,” says Linda Brandl, the company’s vice-president and general manager for automotive. “It is estimated that improving cycle time by one day is the equivalent of adding 1,500 bi-levels and 850 tri-levels to the fleet.”
In 2010, UP introduced the AutoFlex wagon, which can be converted to bi-level or tri-level mode in 20 man-hours while retaining the same rack structure. The AutoFlex, which was designed and built in-house at its DeSoto plant in Missouri, is one of only a few convertible wagons, including those offered by Trinity and the Automax wagon from Greenbier.
Other UP developments include enhanced security thanks to the removal of ladder access to the roof and upper decks; improved safety thanks to better ergonomic access to the decks; and less damage potential thanks to improved tie-down chock systems. “Above all, this design is compatible with the national pool, which supports efficient utilisation,” says Brandl, adding that it is also serving as a catalyst for emerging innovations in multi-levels.
While India and North America are looking to expand wagon capacity, in Europe the declining market means there are probably too many wagons. However, this situation could change if volumes recover, and as older wagons need to be withdrawn, says Philippe Robert, trucks and railways strategy manager for finished vehicles logistics at Gefco.
Gefco, which owns 3,500 wagons, has developed units with extended loading capacities, which it intends to adopt as its new standard. However, Robert stresses, “none of this can be done without the manufacturers’ [OEMs’] collaboration”.
Robert believes there are opportunities for new designs in Europe. The engineering and loading developments that have been made for car hauliers over the last 20 years haven’t been matched for rail, he says. Only limited changes have occurred, including composite brake soles, hoists and chokes.
Robert says that change is difficult given the need for compounds to handle new and old wagons, and for wagons to be compatible with each other. “Re-engineering can only take place on dedicated networks,” he says. “We all dream of loading cars on tilted ramps, using pneumatic levers. But this is currently not feasible.”
Robert says that modern designs still need as much maintenance as their predecessors. “Regulatory maintenance is still a key element of safety and we think this maintains the level of awareness among the workshops at a reasonable level.”
As for capacity limitations on wagons, Robert says this depends on the size of the cars themselves, on rail and loading gauge, the ability of operators to juggle cars when sorting prior to loading and so on. “In Europe, with the current set of rules, we have reached the loading limit with existing equipment. To accommodate more vehicles, new ways of thinking would be needed,” he says.
Gefco is also interested in having GPS trackers on its wagons, but this remains limited to certain geographical areas and traffic types, where distances and risks are higher. “For most rail operations, our current exchange of information with the rail operators is sufficient,” says Robert. “Nevertheless, we might be interested in new functionalities, such as chock detection on very delicate shipments, or in the future, when a shipment contains a large number of electric cars, devices to control and maintain batteries charge levels.”
The market is moving in rail
In many ways the Indian, US and European rail markets are entirely separate – different gauges, power and infrastructures mean that Europe cannot export its surplus of wagons to either continent, for example. In North America, rail is private and the railways divide the continent by region on a freight network that, by and large, does not overlap with passenger trains. In India, the state-run system has historically focused on passenger traffic, and its recent willingness to make it easier for private investors should mark a change. Europe’s mixed state- and private-operator model has tended to give priority to passenger traffic; but as the European Union further liberalises rail, it is exploring dedicated freight corridors.
But policy and infrastructure differences will not outweigh the market. Until European volumes recover, there will be only limited new equipment and designs. In North America and India – despite the subcontinent’s weak market this year – the potential for growing vehicle production suggests automotive rail should continue to lay down more tracks.