Mazda's key to unlocking a continent
Michael Beyer (right), group manager of vehicle logistics at Mazda North American Operations, reveals how logistics for the OEM’s new Mexican plant will be crucial to its success in the US and in global markets
The current decade has been a transformative one for Mazda in the US and North America. After Ford sold most of its 33% stake in the Japanese carmaker, the two OEMs stopped producing cars together at the AutoAlliance joint venture plant in Flat Rock, Michigan in 2012, by which time Ford had also wound down output of Mazda-badged vehicles at its plant in Kansas City, Missouri. Mazda, which since the 1980s had been a transplant OEM with a more American business flavour than most – including using unionised workforces at plants and transport carriers – came to rely entirely on imports from Japan. And even though its sales rose steadily following the recession, a strong yen and a lack of new models held back Mazda’s growth and profits in the US.
In the past two years, however, a falling yen and investments in models and production have helped the OEM to its best US sales figures for two decades, along with healthy profits. The carmaker’s chief executive officer, Masamichi Kogai, has aggressively targeted US sales of 400,000 units as early as 2016 – around one-third higher than last year. Meanwhile, after entering the Mexican market in a small way in 2005, Mazda is now seeing brisk sales increases south of the border.
The lynchpin to Mazda’s North American ambitions is its new plant in Salamanca, Mexico, which started production early last year. The plant, which built 100,000 units of the Mazda3 in its first year, recently added a second shift to build the Mazda2, and will start producing a Toyota model this year. By 2016, Mazda expects the plant to reach its 250,000-vehicle annual capacity, including 50,000 units for Toyota.
Also critical to Mazda’s ambitions in North America and beyond are its vehicle logistics operations. Not only does Salamanca serve large sales markets in the US, it will be a global export hub to regions including Europe and Latin America.
Under the leadership of Michael Beyer, group manager of vehicle logistics at Mazda North American Operations (MNAO), the carmaker has long run a highly stable logistics flow to its 640 dealers in the US. One of Beyer’s top priorities has been to ensure the change in sourcing doesn’t impact the quality of delivery expectations and timings for dealers. While successful, he admits this has not been easy given the infrastructure and systems challenges that Mexico presents Mazda. “Our top objective this year is to support the vehicle processing and shipping operations so that Mexico production becomes stable and consistent,” says Beyer, who is based at the MNAO headquarters in Irvine, California. “We are still in start-up mode in Mexico and with Toyota vehicles coming in a few short months, there is much to do.”
More complexity within
The Mexican plant has reshaped many aspects of Mazda’s logistics network in North America, with its routes now more diverse by mode, provider and origin. For US-sold vehicles, rail now accounts for 39% of vehicle logistics costs in the country. Along with traditional rail flows from its west coast ports of Tacoma, Washington, and National City, near San Diego, California, Mazda is moving vehicles from Salamanca by rail to western and midwestern states (all Canadian-bound vehicles from Mexico also move by rail).
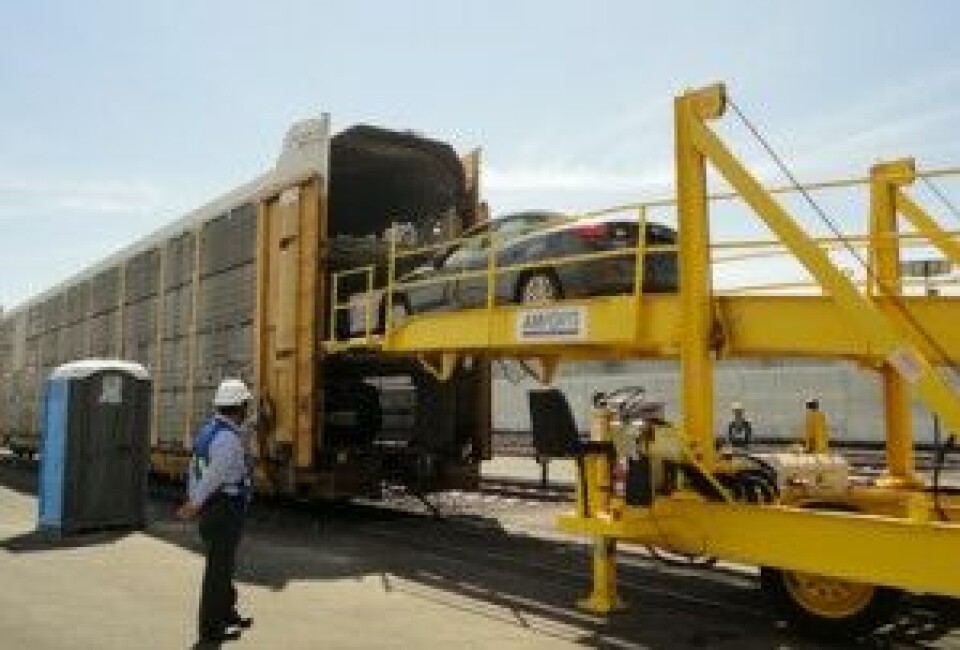
Likewise, short-sea shipping will account for 10% of US-bound vehicle logistics, with vehicles moving by ro-ro ship from the Mexican east coast port of Veracruz to Mazda’s established east coast ports in Baltimore, Maryland and Jacksonville, Florida.
Road remains Mazda’s majority mode for the US, at 51% of logistics cost, spread across eight different carriers, according to Beyer.
However, changes in the physical network only scratch the surface of the supply chain complexities the Mexican plant has raised for Mazda’s outbound processes, particularly for managing the different handling requirements of destination markets. Between the US and Canada, for example, there is an entirely different approach for assigning and installing accessories. Mazda had to develop separate handling and route capabilities for each of Salamanca’s destinations.
While making such distinctions might seem basic, it involves deceptively complex questions around IT systems, logistics provision, yard space and labour.
To manage it all, Mazda has been in the process of updating and refitting its four-year old vehicle processing system, ePort, to manage international flows. When Toyota enters the mix, it will get even more complicated.
“There are a lot of cooks in the kitchen, and much effort in trying to figure out how to handle everything, whether that should be in a central group, or individually, for example,” says Beyer. “It is still evolving.”
That evolution, which brings the chance to redefine supply chain processes, makes it an exciting time for Mazda’s vehicle logistics. While there are a collection of corporate entities involved in Mexico – including the plant manufacturing company, Mazda Motor Vehicle Operations, plus Mazda’s Mexican and US sales arms, its Japanese headquarters, and Toyota – the expertise and experience of Beyer’s vehicle logistics group have led it to take an influential if not deciding role for many outbound logistics tasks at the plant and the wider network.

Mapping out Mexico
In choosing transport routes out of Mexico, MNAO and Mazda Mexico considered the entire field of options to the US and Canada, says Beyer, including concentrating the majority of volume on rail, or using short-sea shipping to any or all of its ports. Mazda also considered reorganising its port networks in the US, whether by adding terminals or concentrating volumes into one “super port” on either coast, he says.
To determine its routes, Mazda took into account market locations, volumes and transit times. The plant is set to play a significant role across North America in the US, Canadian and Mexican markets, so choosing the right mode and methods is vital to Mazda’s sales and distribution.
For the US, the analysis for vehicle logistics led to the creation of a multimodal export route. Based on the projected proportion of supply to Mazda’s current US sales (305,000 units in 2014), Salamanca will export around 60,000 vehicles to the US (excluding

Toyota), according to the company, which would rise to more than 75,000 if Mazda sales reached 400,000 units. Of these exports, Mazda is moving 54% to the US by rail. Ferromex is the rail provider from the plant, however Mazda also uses Mexico’s other major rail provider, Kansas City Southern de Mexico (KCSM), to cross the border at other points.
Around 46% of US-bound production is expected to move by short-sea out of Veracruz to Baltimore and Jacksonville. Mazda’s studies, meanwhile, confirmed that the carmaker’s existing port network on both coasts would continue to serve it best.
For Canada, based on Mazda sales of 72,000 units in 2014, the carmaker will export more than 30,000 units per year from Mexico, all of which will move by rail. Japanese imports to Canada, meanwhile, will continue to move through the port of Vancouver, where they are railed to markets in the middle and east of the country.
In Mexico, Mazda’s sales grew nearly 30% last year to 41,000 units; at this level, at least 17,000 will come from Salamanca. Domestic vehicles are moved from the plant by road nearly 300km to Toluca, west of Mexico City, where they are combined with imported vehicles from Japan for final distribution by road.
Mexican exports from Salamanca to the rest of the world are shipped from either Veracruz or to Lázaro Cárdenas on the west coast. With rare exceptions, Mazda sends all vehicles to the two ports by rail.
[sam_ad id=6 codes='true']
This logistics strategy has parallels to the routes used by other carmakers exporting from Mexico. Nissan, the country’s largest OEM with multiple plants in Aguascalientes, 200km north of Salamanca, sends 70% of US-bound vehicles by rail over several border crossings, while the rest leave from Veracruz to the east coast (100% of Nissan’s Canadian-bound vehicles also move by rail).
Honda, whose plant in Celaya is just 50km away from Mazda’s, relies more on short sea, splitting its transport in roughly even thirds between rail to the Midwest, and short-sea services from both Lázaro Cárdenas and Veracruz to the west and east coasts, respectively.
While American carmakers have a somewhat different geography in Mexico, their networks have tended to be weighted more heavily to rail, with short-sea services traditionally used when rail capacity was maxed out (although Ford, at least, has added more regular shipping services to the east coast).
Michael Beyer is a 28-year automotive logistics veteran, including 23 years with Mazda. He’s soft spoken and modest, but his deep knowledge of the sector comes through decisively whether he is explaining differences in labour and terminal service at ports, or unpicking the complexities of an IT system. Beyer has led Mazda’s vehicle logistics department since 2006, following a variety of roles in logistics, as well as several years as head of the OEM’s sales planning in its US western region and its national distribution. Previously, he worked in distribution and logistics at Isuzu and Hyundai.

However, the Mexican plant has, by necessity, fostered a more integrated and cooperative approach to managing major logistics flows in the region. Beyer and his team consult with Mazda Mexico directly on operational areas such as network design, accessory installation, rail equipment forecasting and acquisition, while they also coordinate with Mazda’s various markets and stakeholders, including Canada, Mexico and Japan, plus Toyota.
For example, in procuring shipping services within North America, Beyer worked with Mazda’s local companies to crunch numbers and determine service requirements, while Mazda management in Japan negotiated with shipping lines as part of a global sourcing strategy.
The MNAO team has been particularly involved in running the Salamanca plant yard, which for US-bound vehicles functions as a port processing and distribution centre. As such, MNAO has designed its processes and systems, and helped choose the logistics provider to operate it (terminal provider Amports).
MNAO’s involvement in these areas marks something of a return to business as usual for Beyer’s vehicle logistics group. For years, they coordinated vehicle logistics out of the shared Ford plants, including arranging road and rail logistics, as well as choosing and managing Mazda’s port terminals.
“When our plants with Ford came down, there was a lull in our domestic logistics, but with the new plant our top management in Japan knew that we could help and apply the same lessons we’ve learned over the years to Mexico,” says Beyer.
It’s good to pick up the phone
For Michael Beyer and Mazda, determining these transport routes is based not only on lead times and quality, but also reliability for its sales regions and dealers. For example, unlike some OEMs, Beyer doesn’t want to depend very often on shifting between transport modes based on their capacity, preferring fixed routes to build both scale and predictability. The Mexican network, he says, is not suited to “flip-flopping” between modes, while dealers can plan their sales better when they have consistent pipelines.
“The main reason is to help our customers have a better understanding of their pipelines,” Beyer says. “If a dealer in Florida knows their vehicles arrive by vessel, after a while they learn to plan around that. Swapping between rail and vessel would create havoc for dealers.”
This line of thinking reveals something at the fabric of Mazda’s distribution strategy. Vehicle logistics, Beyer explains, remains a tactile business, based often on human relationships even in the digital age. Having worked previously in distribution and allocation, he especially understands how “hot vehicles” are often reassigned to dealers at the last minute, and frequently by phone.
For example, if dealers request a vehicle swap, regional distribution managers usually call the port to hold or track down particular vehicles. Mazda’s ePort system monitors vehicle inventory at ports, and shows if they have been released for transport or are still at the yard, so in principle distribution managers can see and select what they want online. However, the system is only as up to date as the latest scan of vehicles by terminal staff. To know all options in the ‘real’ world, a phone call is often best.
“Life is still made up of little batches, so there could still be vehicles queued up on a truck that have been scanned, but are still at the port even though the system says that they left,” he says. “Likewise, the port processor could end up bunching up vehicles for rail loading and scan them into ePort 15 minutes later. Well, in that time a dealer could be looking to make a trade, so it is better to talk to somebody.”
To allow for these relations to continue, Beyer prefers imports from Mexico to move on consistent distribution channels in the same way that Japanese imports do. That is not always easy to achieve, but he and his team are putting the processes in place to do so.
Adapting ePort for a global plant
An important part of the plant’s launch has been defining vehicle releasing and processing in the yard. For vehicles moving to Canada, for example, dealers install accessories, while in Mexico these are done at Mazda Mexico’s Toluca distribution yard; in the US, port processors carry out this work. A different process is needed for each variation.
For Mazda’s Japanese plants, such differences matter little. Exports are built and shipped to market as quickly as possible, with modifications, homologations and accessories determined by the national sales companies and distributors in export countries. “Any flexibility or capacity to regulate vehicles based on market demands is given to the destination markets,” says Beyer.
Salamanca and its plant yard, however, are something of a new export model for Mazda, which Beyer describes as a “hybrid” between a plant yard, in the Japanese sense, and a port terminal, in the American sense. Vehicles off the line move direct for export to markets like Canada and Europe, while for the US, Mazda uses the plant’s yard as a distribution centre, where vehicles can be held for allocation to a specific dealer, and accessories and options installed.
“Mexico has to be able to put cars out to ports as a plant, but also to regulate vehicles so that if we have a new dealer point opening up, you hold the car until the dealer can receive it,” says Beyer.
Vehicles for the Mexican market have yet another process. Since Mazda Mexico already had a distribution centre in Toluca handling Japanese imports, MNAO and Mazda Mexico determined it best to centralise inventory. “This allows Mazda Mexico to do dealer trades more easily, and to avoid duplicate processes” says Beyer. “The processes in Toluca are all standard, and they accessorise them there, which frees up space at the plant.”
All of these different routes and handling procedures required a system to regulate them. Mazda’s management eventually determined that MNAO’s ePort should be implemented in the yard. The system, rolled out across MNAO’s four port terminals several years ago, is a vehicle processing tool that allows Mazda to see and manage vehicles at every stage of arrival, processing and departure at ports.
“The real value of ePort is the real-time view of vehicle processing, which helps answer customer questions related to what is happening to their vehicle and when it will be shipped,” says Beyer. “Internal to Mazda, this real-time view has helped with making overall decisions regarding processing and shipping priorities, inventory levels, vehicle age, processor performance, etc.”

When ePort was designed, however, it was intended to handle US-bound vehicles from Japan, rather than a plant operation that would handle multiple markets, and require information from each destination. “We have been spending a lot of time adapting ePort to be able to do that, such as establishing processes for basic things like what transport mode and port will be used for a car going to Europe?” explains Beyer. “Or, for a US car, how do we know if the car needs a spoiler or not? A lot of that development has been about getting all of those needs into a central system to process and ship a car.”
Those system complications are only going to increase with the planned launch of Toyota production this year, after which the plant yard will incorporate the processing and shipping needs of the two brands. The extent to which Toyota will use ePort is still being discussed, admits Beyer, but either way, ePort will need to account for these vehicles or at least communicate with another system.
While there is still more work to be done, the upgrades to ePort and to the overall processes at the yard have made the operation fit for wider purpose. Mazda is now able to handle a complex, international operation with diverse demands that it previously couldn’t. This progress is notable since Salamanca is set to become Mazda’s most important production site outside Japan, and its processes are likely to be influential across the company.
New network, familiar headaches
While the Mexican plant has led Mazda to extend its reach across the continent, as well as update its IT systems to handle more complexity, it has also exposed it to transport problems familiar to other carmakers in North America. Limits to railcar supply and velocity have been chronic at various points across the US and Canada since last year. In Mexico, Beyer points to higher incidents of theft and vandalism. Overall, he admits that Mazda’s accuracy in providing vehicles’ estimated times of arrival (ETA) to dealers and logistics providers – a critical project for Mazda – suffered last year after the plant opened, although it has since improved.

Although Mazda didn’t experience as many delays as other carmakers during last year’s rail disruptions, railcar capacity is still Beyer’s top concern for increasing volume out of Salamanca, and more broadly across the North American network. At the least, he would like to see rail providers recover the two days in average transit time that have been lost across the network compared with two years ago.
“Things were very difficult last year for the industry, even if Mazda was not affected as harshly as others,” he says. “We would like to see the railroads get back to the velocity we saw before the weather and growth caused problems last year.”
Incidents of damage and vandalism for vehicles moved in Mexico, meanwhile, occur three times more often than in the US, including frequent theft of key fobs, batteries and wheels. While such damage is an industry-wide problem, Mazda is investigating the degree to which changing the carmaker’s processes might mitigate the issue. While some things are outside Mazda’s control, such as delayed or stopped trains (almost always where vandalism occurs), Beyer notes that some rail equipment is more prone to theft than others.
“An OEM who has been in Mexico longer probably already knew that certain equipment is more susceptible to break-in and damage because of the spacing and end doors, for example,” he says. “Initially, when equipment like this was spotted to us, we were glad to have the capacity, whereas now we are learning what needs to be rejected.”

For short-sea shipping, service has been reliable. Indeed, Beyer is almost surprised at its frequency, as he initially worried that services to the US might be no more than once or twice a month. Instead, Mazda can often find two sailings per week between its three shipping lines, MOL, K-Line and NYK. Beyer credits the service levels to Mazda’s relationship with the shipping lines in Japan.
The big problem, instead, has been delays in unloading railcars, especially at Veracruz, leading vehicles to miss scheduled vessels. Beyer is quick to assert that “no one group is to blame”, and that Mazda continues to make improvements as it moves more volume at the port. But the problem is evidently there.
One issue is that Veracruz’s rail terminal is currently outside the city, several miles from the port itself. The Veracruz port authority and Mexican railways have announced plans to build a bypass, however Beyer is worried whether current plans will be enough or completed in time to deal with the growth of carmakers and other commodities.
Paying for what is right
The question of investment and capacity is one that Beyer sees as a danger across the North American rail network. “The rail industry is frequently communicating how much money railroads are investing into improving their network, and I have no doubt that they are doing what they say,” he says. “Unfortunately, from a Mazda perspective, we are looking for tangible benefit in the areas that are of value to us – namely, railcar supply and transit time. To date, these expected benefits have not materialised.”
While Beyer is not yet satisfied with the rate of improvement in the rail network, he says he is “hopeful” that investments will have a material impact on Mazda’s vehicle logistics. And it must be said that, across the network, overall services have been good. Beyer praises the flexibility and services provided by Mazda’s truck carriers in particular. He also notes that, unlike other OEMs, Mazda has very rarely diverted vehicles from rail to road – although he admits this may be down to luck of geography, since San Diego is a large destination for inbound railcars, keeping port users like Mazda well supplied.

Beyer does, however, see potential for logistics providers to work better together, especially in managing information at rail yards. “Often, the railroad will report that a vehicle is ageing at their rail ramp but the trucking line says it didn’t know the unit was available for pickup,” says Beyer. “Lines of communication can improve if they leverage current methods of information exchange.”
For Beyer, keeping open communication with providers is important to providing consistent service to dealers. Mazda, though not among the larger OEMs in North America, has a reputation as a reliable, long-term partner. Beyer and his team try to nourish this, especially since the new plant was launched. Beyer has been glad, for example, that he could assure port processors that the plant was intended as incremental production capacity, and that, overall, they could still expect growth, even if it was at a slower pace.
“Many of our port partners were sceptical, but now they see that we meant it. Overall, Japan imports have not dropped,” says Beyer.
Like any good vehicle logistics manager with nearly three decades of experience, Beyer’s support of providers does not come with a blank cheque. However, he makes it clear that vehicle logistics can and does add value for Mazda, which he believes will be strategic; investing in growth, he suggests, goes hand in hand with investing in delivery quality.
“Eliminating waste and being cost effective are always factors to be considered, but they are not our main focus,” he says. “That is to support Mazda’s customer satisfaction and vehicle quality goals. So will we purposely hold a vehicle at a port to support a dealer? Yes. Would we increase costs to ensure vehicles leave the port damage free? Absolutely.”
Mazda’s production of Toyota vehicles in Salamanca, Mexico will require considerable sharing in the supply chain and the plant, not least in Mazda supplying the model’s engines. For outbound logistics, Toyota and Mazda vehicles will roll off the same line to the same vehicle yard, while many of the vehicles are also likely to be destined to similar locations, whether in Mexico, at ports, or across North America.

Beyer admits that there could be benefits to sharing transport, including less dwell time before filling railcars or truckloads. “There are potential positives, but we have decided to talk about it again later,” he says.
The extent to which Toyota and Mazda will interact on the plant yard, as well as with Mazda’s ePort processing system, is currently being decided. It is not yet clear whether Toyota will move all of its vehicles through the yard or move them (or some of them) to another location, as Mazda Mexico does.
Toyota will also decide, as Mazda did, how it will treat processing and accessorising vehicles for destination markets. Toyota Logistics Services, which runs vehicle logistics for Toyota’s US sales arm, may look to outsource these operations to the provider on site, or arrange its own installations elsewhere in Mexico or the US.
According to Beyer, Mazda is open to working with Toyota to the extent deemed appropriate for cooperation on the yard. What has already been established is that Toyota vehicles built at Salamanca will be integrated into ePort, and the system will be used to communicate the necessary vehicle services at the yard to the port processors. This means, at the least, that data will be exchanged between Toyota’s system and Mazda’s.
Still to be determined, however, is how Toyota will handle operations at the yard, such as accessory installation. Should the carmaker decide to carry out such work here, ePort would be able to manage this information as well. “The ability for ePort to handle the services Toyota chooses to use is now there, and it is an option for Toyota,” says Beyer.
Both brands are using the experience to learn from one another, adds Beyer, and he remains open to Mazda working more with Toyota in logistics in the future. “Toyota is a great company to work with,” he says.