Mexico rail vs sea: No easy route for exports
Figures from the Mexican Automotive Industry Association (AMIA) show that between January and June this year, more than 85% of the passenger cars and light trucks made in the country were exported to the US and Canada – equal to almost 1.3m units out of a production total of nearly 1.9m. That is an increase of 13.5% on the same period last year and on the way to beating last year’s export total of 2.8m.
While rail accounts for the vast majority of those shipments, there has been a significant rise in the volume transported by short-sea in 2017. The Ministry of Communications and Transportation (SCT) in Mexico recorded that, compared to 13.5% export growth, there was a 40% rise in the movement of vehicles through the seven vehicle handling ports in the first six months of the year, equal to 668,000 vehicles. Exports saw a 45% increase, coming to more than 354,000 units, of which 220,000 were going to the US via short-sea.
There are a number of reasons for this, including the cost of land transport compared to multimodal options. According to Tomasz Lis, head of Latin America at ocean services provider, Höegh Autoliners, the short-sea option does not require big infrastructural network investment, as rail does. “Sea transport is more flexible and price-competitive per car with larger volume intake or when taking cars en route from Mexico to the US as a way-cargo on deep-sea voyages,” he says.
Rail is also sometimes at a disadvantage in the face of increasing volumes in terms of the positioning of rail equipment when and where it is needed. There is also the threat of theft, vandalism and drug smuggling on cargo moving out of Mexico by rail.
At current rates, Lis says Höegh could increase its services from Mexico to the US based on its existing tonnage, with or without the need to add ports of discharge in the US. For some operators, however, supporting the movement in and out of Mexico has put pressure on investment and manpower.
“On the processing side, scaling up and training our headcount to be able to cope with the production growth has been a significant investment,” confirms Robert Zavala, head of Mexico at ocean services provider, Wallenius Wilhelmsen Logistics (WWL).
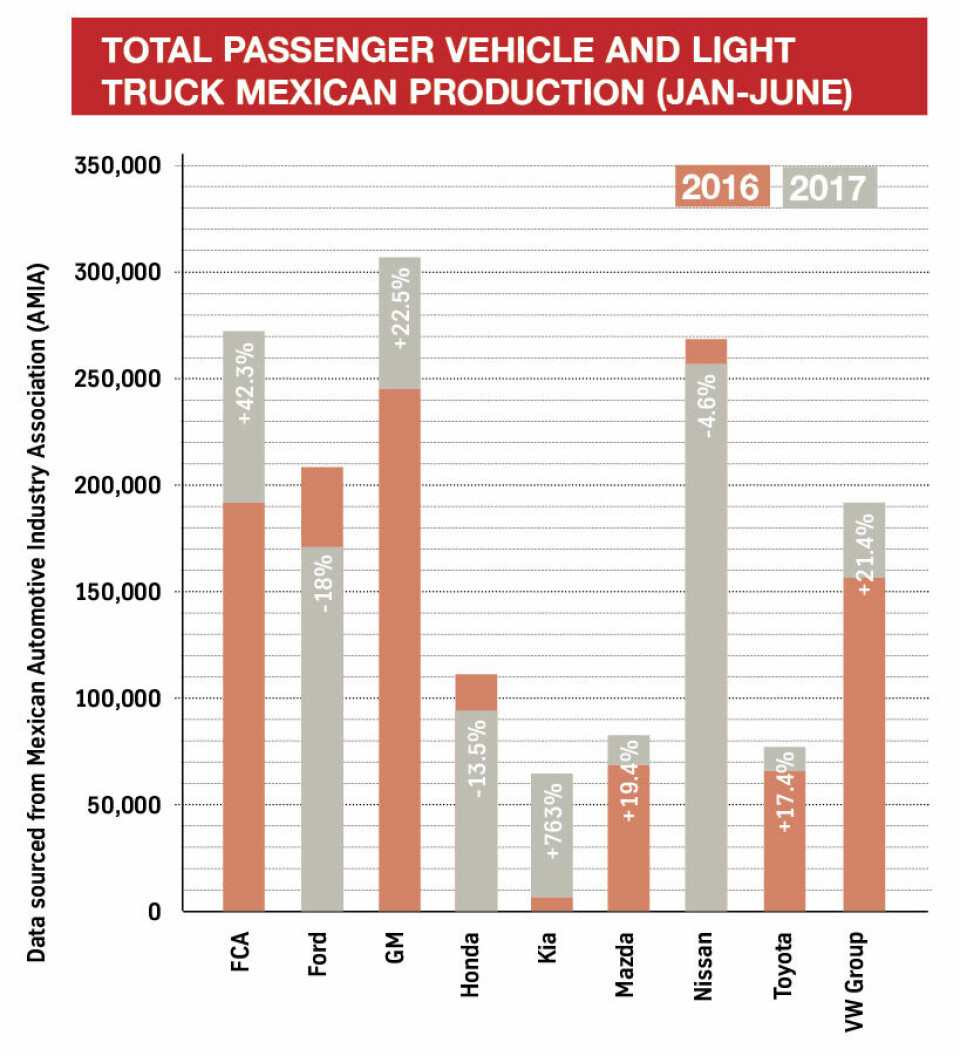
(Click to enlarge)
Congestion concernsThe increase in vehicle volumes through Mexico’s ports also adds to the issues of congestion and struggling domestic rail connectivity, not least given that imports of vehicles also grew during the first six months of this year by 34% to 547,764, continuing several years of strong double-digit growth.
For Höegh Autoliners, imports of vehicles from locations such as Asia are where it is seeing the main increase in traffic. The company expects to handle around 57% of total imported volumes into Veracruz, for example.
“The increase in exports is there but as less of a percentage compared with imports, due to the changes in moving volumes,” says Lis.
Port congestion and associated waiting times in Mexico are key challenges at the moment, he adds, particularly at Veracruz. The problems there are numerous, says Lis, and frustrate all attempts to cut waiting times, affecting call schedules at ports of both loading and discharge.
These problems include scattered yard management that does not take into account the volumes being delivered by sea, and blockages caused by dealing with export cargo being delivered on short lead times from plants. Lis says the Veracruz port administration authority lacks any yard management system for public yards.
There are also too many free days of storage for export cargo at Veracruz, he says. “Not all OEMs consider within their logistics setup a need for an off-port facility to reduce the stay of their cargo inside the port,” he explains. “Those OEMs who use the port as a storage area block the space for those who are more efficient in moving their cars to or from the port within short periods of time.”
A recent rate increase for storage at the port has had a positive impact, he admits, but more needs to be done, including a pilot of extended working hours and the removal of surcharges for calls made after working hours.
“Vessels should leave the port just after the end of operation and penalties should be imposed for those which block the limited berthing positions,” comments Lis.
Port capacity can be an issue in Mexico more generally in heavy demand periods, but investment in better infrastructure is on the way, according to Roberto Zavala. For example, vehicle processor SSA Mexico (a division of SSA Marine) is investing $56m in Lázaro Cárdenas, as part of a first phase of development that will result in 80,000 sq.m of vehicle processing space. There are also developments at a number of other ports in Mexico, with alternatives now being used at Tuxpan on the east coast and Mazatlan on the west coast.
“Both things will contribute to the relief of the still very congested port terminals,” says Zavala.
Continued investment and the development of alternatives will promote more consistent flows in and out of the ports and reduce dwell times, but this is contingent on market demand for the vehicles being transported, port handling costs and congestion at the receiving ports.

Production growthThe rise in short-sea shipments is moving up along with the volume of cars being moved north. Production in Mexico has gone from 2m to 3.5m over the past decade, and exports have almost doubled over the same period, according to AMIA. The opening of the Kia plant in Pesqueria and the Audi plant in San José Chiapa last year have significantly increased export volumes out of the ports of Altamira and Veracruz, respectively. Kia alone has increased exports in the first six months of this year by 763% to almost 64,900 units, and more than 50,000 of those went to the US and Canada. Its plant at Pesqueria, like the Audi plant, is in good proximity to the ports and both have good rail connections.
At the same time, according to Zavala, short-sea services out of those ports to the US east coast have been improved and expanded. “There are more ports and therefore more infrastructure on the east coast, so more volume is pushed there,” he says. “Also, the Mexico manufacturing base iscloser to the Gulf of Mexico.”
WWL estimates that 44% of exports could be sent via short-sea to the east coast, while California accounts for 20% of all exports from Mexico, so further growth in traffic on the west coast is also anticipated, says Zavala.
FCA has already started shipping vehicles by short-sea to Grays Harbor, Washington, on the US west coast from the Mexican port of Lázaro Cárdenas, with Pasha Automotive Services.
In 2016, FCA produced 459,000 vehicles in Mexico from plants near Mexico City (Toluca) and Monterrey (Saltillo), according to AMIA – an 8.8% decline compared to 2015. Of that total, more than 443,000 vehicles were exported to the US and Canada.
Overall, Pasha saw a 15% increase in short-sea traffic from its automotive customers through 2016, according to vice-president Ben Buben. “Increased production in Mexico is allowing the OEMs to take advantage of other modes of transportation to the US market,” he says, adding that short-sea currently offers the advantage of increased velocity between ports and avoids the problems of longer travel times and border delays affecting rail shipments.
Over the next few years, sales in the US are forecast to dip. This, combined with a continued sales decline in Canada, raises the question of how volume shipments out of Mexico will be affected over that time across transport modes.
According to Lis, there will not be much change from the relatively high percentage of new vehicles being moved by land compared to short-sea today but there is scope for multimodal deliveries.
“The US and Canada are still going to be the largest destinations for cars moving in export from Mexico,” Lis predicts. “Other factors will influence the split between land and multimodal transport, and I believe multimodal will increase.”
"Our short-sea options have grown. We just recently started shipping into Grays Harbor by short-sea, which would have gone by rail. It is the same thing to Aransas; we normally would have gone by rail but we pulled those units out and actually started going by short-sea. Having the option is definitely great for GM." - Alrick Duncan, General Motors
Avoiding vandalismRail capacity constraints, transit time and cost issues aside, the avoidance of vandalism and theft on the rail network in Mexico is another thing short-sea has in its favour.
At this year’s Finished Vehicle Logistics Import Export summit in Baltimore, Alrick Duncan, intercontinental and port operations supervisor at General Motors – which exported around 280,000 vehicles from Mexico to the US and Canada in the first six months of 2017 – said that GM wanted more options for exporting cars, in part because of the level of vandalism it had seen on the railroads.
“Our short-sea options have grown,” he said. “We just recently started shipping into Grays Harbor [Washington state] by short-sea, which would have gone by rail. It is the same thing to Aransas [Texas]; we normally would have gone by rail but we pulled those units out and actually started going by short-sea. Having the option is definitely great for GM.”
Vandalism is also a concern for Volkswagen Group of America, according to Mark Boucher, director vehicle logistics. “I will say that it has improved but it is still not nearly at the standard, so we are looking for opportunities for short-sea,” he told delegates in Baltimore.
Volkswagen has had a hybrid strategy for years, serving the eastern US by ocean vessel out of Veracruz and western points by rail, according to Boucher. However, one issue for all the OEMs is the finite space at the ports, particularly on the eastern side. “That is a challenge for all of us,” he commented. “But for all intents and purposes [ocean] is a safer route to get the products to market.”
[mpu_ad]Honda has been making cars in Mexico since 1995 when it opened its El Salto plant, and boosted output with a second plant in Celaya, which opened in 2014. Together the plants produce around 260,000 cars a year (plus 100,000 motorcycles from El Salto). The company is using short-sea on both coasts and rail for exports to the US and Canada. The Celaya plant produced 200,000 units last year and half of that volume went short-sea through Veracruz to the eastern coast ports of Brunswick, Georgia; Baltimore, Maryland; and Davisville, Rhode Island. A quarter of the overall volume goes to the west coast for local distribution through the ports of San Diego, Richmond and Portland. The remaining quarter goes by rail with Ferromex (FXE) and Kansas City Southern (KCS) de Mexico.
Security threats on rail are also an issue for Honda, as is the threat of congestion at the ports as more carmakers move to Mexico. Chuck Kendig, assistant vice-president of sales and production planning and logistics at American Honda, says both FXE and KCS have been supportive in providing tougher, enclosed rail cars. The Mexican government has also been helpful in deploying troops in the Bajío region, which was plagued by theft and vandalism last year. However, the problem has simply gone elsewhere as gangs migrate to areas not patrolled by the army.
KCS admits that security on rail in Mexico can present a problem for automotive companies versus other modes, but its spokesperson, Doniele Carlson, says it has made significant investments in the last few years in security, rail infrastructure and equipment to increase the quality of services it provides to carmakers. Carlson also points out that rail can move huge quantities of vehicles in an efficient and economical fashion.
Modal balance at MazdaRyan Kita, senior manager of distribution and logistics at Mazda North America Operations, says that while the carmaker has increased short-sea volumes from Mexico, where it has a plant in Salamanca, its ratio between short-sea and rail has not changed. While he admits that vandalism is one of the company’s considerations during route reviews, so too are such factors as consistency, capacity and cost. Kita adds that the increase in short-sea volumes is down to an overall increase in export out of Mexico, and not a change to the network to address theft and vandalism or issues of border congestion. “There are no major obstacles based on our current routing,” says Kita. “We currently rail to the central US for efficiency.”

That efficiency is why rail continues to dominate in terms of moving cars from Mexico to the US and Canada. Figures from KCS indicate that, up to this year at least, 90% of vehicle exports moved by rail with only 10% by short-sea (the proportion for 2017 appears to show an increase by sea, however).
Rail is convenient and ensures quality for carmakers as, once vehicles are loaded into the railcars at the assembly plant, they do not need to be handled again. Kita says the advantages are a faster, direct service to dealers in the central US region.
According to Lis at Höegh Autoliners, however, rail is only quicker when there are wagons available on time. There have been examples, he says, where ocean lead times have been on a par with rail. Nevertheless, he admits one advantage of rail is that there is cargo going back from the US to Mexico that is mainly moved by that mode.
Contractual obligations between OEMs and the rail providers can also influence the prevalence of rail, points out Buben of Pasha. “One of the biggest reasons for rail volume is current contractual obligations the OEMs have in place for rail conveyance,” he confirms.
Mazda’s short-sea volumes are shipped from the port of Lázaro Cárdenas on the west coast to the US. Mazda switched exports there from Veracruz but Kita says that decision was down to the negative effects of El Norte (a weather pattern affecting the Gulf Coast), not congestion at Veracruz or lead times.
Volumes are moved there by truck from the Salamanca plant but that mode is supplemented by rail when additional capacity is needed, says Kita.
Trade routesAnother issue affecting the use of ocean for cars between Mexico and the US is the imbalance in trade, with relatively few cars travelling from the US by ship into Mexico. According to WWL’s executive vice-president, Flavio Batista, that means shipping lines build their services as part of global trade loops to serve the US and Mexico, rather than dedicated shuttles or short-sea vessels, as is common in Europe.
While services out of Mexico are seen by the customer as a short-sea trade, it is one essentially supported by deep-sea vessels with transit times that are close to a trans-Atlantic crossing. Zavala points out that dedicated services normally have higher frequency and are faster. “OEMs would like to see higher frequency and more port options to ship short-sea [from Mexico],” he admits.

WWL does not offer dedicated short-sea services between Mexico and the US because of the way the company’s vessels trade globally, but Zavala says it will invest with the right OEMs when the economics makes sense.
According to Lis at Höegh, however, there are advantages of being incorporated into the global trade loops, as larger ships can provide more capacity. “All our vessels in the trades connecting Mexico and the US go from south to north, giving us possibilities to use them for shipping [between the two countries],” explains Lis. “With dedicated tonnage, such capacity would not be possible due to the imbalance in volumes moving by sea, which would require higher rates to be charged to OEMs.”
Pasha’s Buben also sees benefits. “We see synergies to help with multiple OEMs sharing vessels for different discharge ports,” says Buben. “The more OEMs that participate, the more ships a particular carrier can put into a route.”
Rail returnsAn imbalance in trade is also a consideration on the rail side, with far more vehicles moving from Mexico to the US than the other way around. “This creates challenges with relying on empty equipment being provided from the US,” says Carlson of KCS, adding that the company maintains strong relationships with its rail partners in the US to meet demand from customers.
KCS is also involved in an initiative to increase throughput of rail cars across the Laredo, Texas rail border crossing between the US and Mexico while at the same time increasing security. The rail provider has built what is called the Unified Cargo Processing facility near the railhead at Laredo as part of a joint project involving US Customs and Border Protection (CBP) and Mexican Customs (SAT).
According to the CBP, this will allow SAT to complete outbound customs inspections and let CBP perform inbound inspection processes simultaneously, eliminating unnecessary delays and duplication while maintaining security.
Carlson says the new Laredo facility will help both finished vehicle and automotive parts movements “by allowing additional capacity for a more consistent and reliable train service”.
The rail crossing at Laredo is the busiest on the US-Mexico border and processes 23 trains in total every day.
"Even though production costs are the main contributor to Mexico’s competitiveness, Nafta has proven to be the perfect channel to take full advantage of it. Any changes to the framework will have an impact on such competitiveness and, by extension, on the vehicle flows between the two countries." - Robert Zavala, WWL
Future tradeLooking ahead, one of the big issues for export trade from Mexico to its North American neighbours is the renegotiation of the North American Free Trade Agreement (Nafta) and the emphasis that the Trump administration has put on relocating production in the US and reducing the country’s trade deficit. Trump, who has criticised Nafta and trade with Mexico, said during the first round of negotiations in August that he did not think a satisfactory deal could be reached and the US would probably withdraw.
There has been a mixed response from short-sea providers to this. “Even though production costs are the main contributor to Mexico’s competitiveness, Nafta has proven to be the perfect channel to take full advantage of it,” says WWL’s Zavala. “Any changes to the framework will have an impact on such competitiveness and, by extension, on the vehicle flows between the two countries.”
[related_topics align="right" border="yes"]By contrast, Pasha Automotive Services’ Ben Buben says the company will always have some northbound traffic from Mexico, regardless of how the new agreement turns out.
Tomasz Lis at Höegh says the idea that a renegotiation will affect where vehicles are made in North America is something easier said than done, adding that there are other economic drivers pushing OEMs to make decisions on the way they do business. “I believe this is not going to change much, despite being a very popular topic used by the US administration in the media,” he says.
Over at KCS meanwhile, Carlson says the rail company is “confident that the administration has correctly focused on updating and improving Nafta”.
“This approach will lead to successful improvements to the agreement that benefit North American trade and its competitiveness in a global market,” she adds.
Many in the industry will hope she is right.

Rail connectivity within Mexico between plants and ports is still in need of improvement. The government is investing $100 billion in infrastructure, including around 32 projects underway on the rail network to improve and expand sections of mainline double tracking, sidings and extensions, bridges and yards. Until that infrastructure is in place, however, efficient delivery of vehicles from plants to ports will be hampered, with a knock-on effect on vessel scheduling. However, carmakers are making efforts with their service providers to minimise dwell and delay.
Speaking at the Finished Vehicle Logistics Import-Export summit in Baltimore, Chuck Kendig, assistant vice-president of sales and production planning and logistics at American Honda, said the carmaker does not dispatch trains to the ports unless it knows that they can meet the schedule with the ocean vessel. He adds that communication has been much more effective recently and describes it as a “block and tackle operation” that helps keep trains running non-stop, reducing the risk of theft and vandalism. “We have good visibility with the ships coming in and good communication with our partners MOL and K-Line, as well as very good communication with the ports,” he states.
Mark Boucher of Volkswagen Group said one area of the supply chain it is working on is real-time rail tracking to the vessels. “It will be a big help for the port landing and getting trains there in the right time,” he said.
GM is looking at greater visibility of vessel schedules for imports to meet with rail, meanwhile. Alrick Duncan told delegates at the conference that the carmaker has seen definite improvements on imports. GM knows when vessels are arriving with the existing technology it has, but Duncan said it wants more detail on processing schedules to avoid gaps in the service. “There are some studies being conducted into what else we can do to work with our ocean carriers and port processors to provide that visibility,” he revealed. “Even though we are meeting our metrics, there are some improvements for us as our volumes grow for imports.”