More needs to be done to reduce waste in the outbound sector
All aspects of the automotive industry generate waste, whether that is environmental, in terms of productivity, or in business; and logistics and the supply chain are not exceptions. While efforts by OEMs, suppliers, and logistics service providers to reduce waste have significantly stepped up over the past few years, more can always be done. One of the main issues in finished vehicle logistics is first identifying where the biggest waste is, before work can begin to start minimising it.
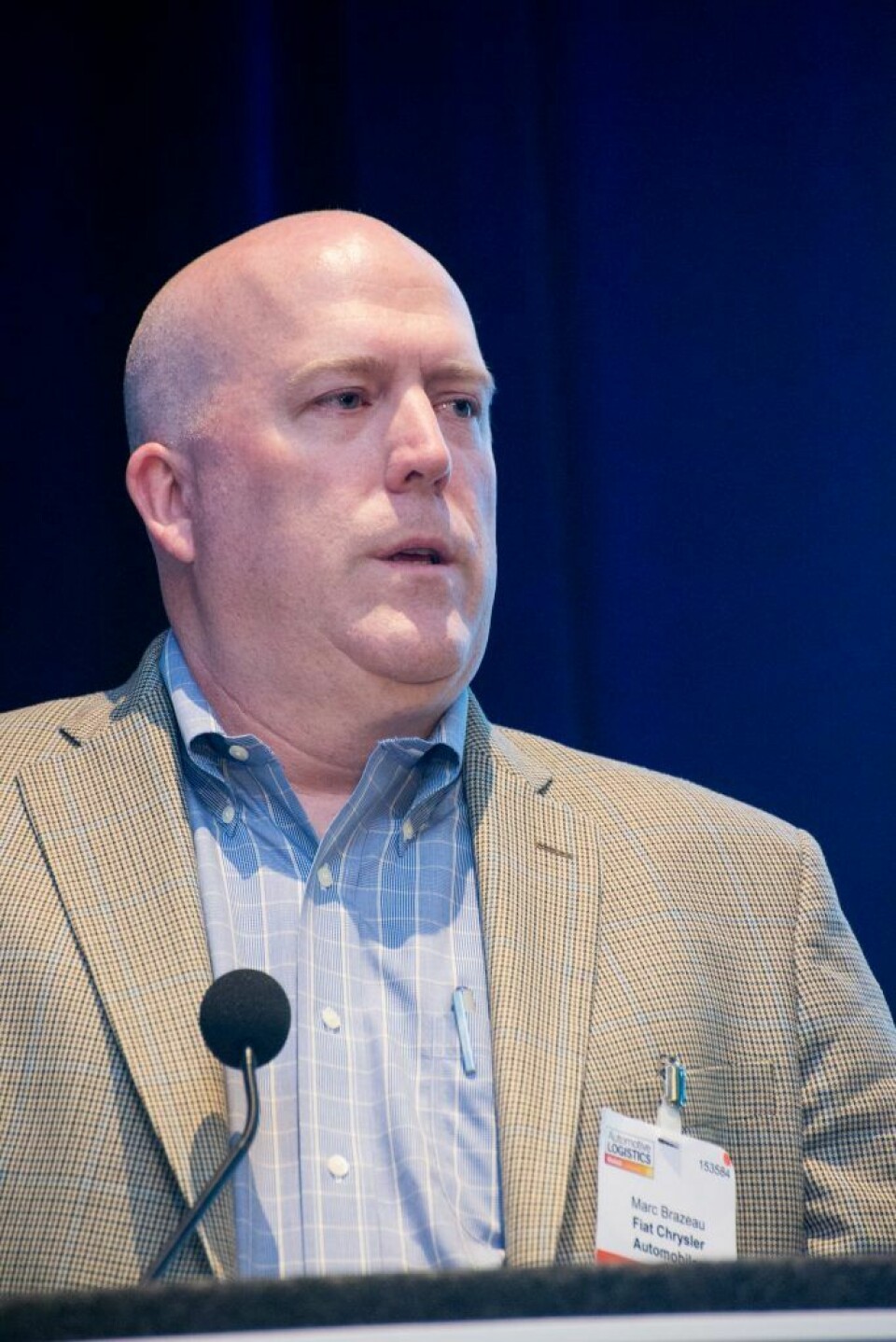
For Chrysler, waste lies in areas such as capacity planning and utilisation, network velocity and dwell time, and duplication of efforts. Brazeau said, however, that he was encouraged by discussions as to how companies are preparing and investing in surge capacity.
Bill Pawluk, chief executive, CTM, said that one significant area of waste is empty miles, with 42% of automotive transport miles being lugged with empty trailers.
Pawluk said among other things, the automotive industry is wasting time, profit, progress, and resources. “We’re running out of fuel that we can’t make later, and we’re wasting capacity. Companies are investing in more assets, but capacity is there, you just have to get smart and work out how to use that capacity more effectively,” he said.
Pawluk explained that in order to start utilising capacity, the automotive logistics industry needs to move closer to general freight. CTM has been working on creating an entire industry-wide system that can highlight areas of flow imbalance, and cross-pollinate information with inbound automotive, and non-automotive too, in order to reduce empty miles, and waste.
Reality check
Bill Kerrigan, program manager, FVL supply chain, AIAG said that the automotive industry needs a reality check. “We’re back to pre 2008/9 levels, but we’re running into the same problems that we had back then. We need to utilise the capital assets we have now, and break down internal and external silos – especially on the FVL side,” he said.
One big concern is a lack of accurate forecasting. There is always a rush at the end of the month to deliver vehicles, which stretches capacity. Kerrigan said that those working in FVL need to provide an even flow of vehicles throughout the month, and manage exceptions.
Mike Riggs, CEO, Jack Cooper Holdings agreed that bad forecasts are a huge concern. “When companies have forecast 25-30% under what projections are, it’s virtually impossible to have the capacity to respond… projections haven’t been anywhere close, and it makes us look like we’re underperforming.”
Brazeau said that having more of a dialogue between OEMs and LSPS as to how the inaccurate forecasting can be purged could help, and that any changes throughout the month need to be made more visible to the carrier base. “There are things we’re doing to improve upon the visibility in our processes, but I don’t think it’s about forecasting accuracy, it’s more about advanced planning, which is related to capital planning,” he said.
In order to provide more accurate forecasting, and consequently increase utilisation and reduce waste, Kerrigan said that several things need to improve: visibility, metrics, benchmarking, and collaboration.
Collaboration to reduce waste
“I don’t like the word [collaboration] any more than Marc Brazeau does. It should be cooperation instead. However, it needs to be done in a legal environment. The problem is that we’re looking at individual solutions… we need a neutral collective effort to analyse the entire FVL supply chain, and find where we can maximise utilisation,” Kerrigan said.
“As long as we all go our different ways it’s not going to happen. We need to reduce inventory days and dwell time, we need to increase capital asset utilisation, and we need better FVL collaboration – it will be forced upon us as we alter the delivery model,” he added.
Brazeau agreed that all those involved in FVL need to take a “collective shared asset approach” to waste, and identify where shared asset components can come together effectively. Efforts to reduce waste will allow companies to make it through some of the downturns that lie ahead.