Localised parts production for Chinese EVs
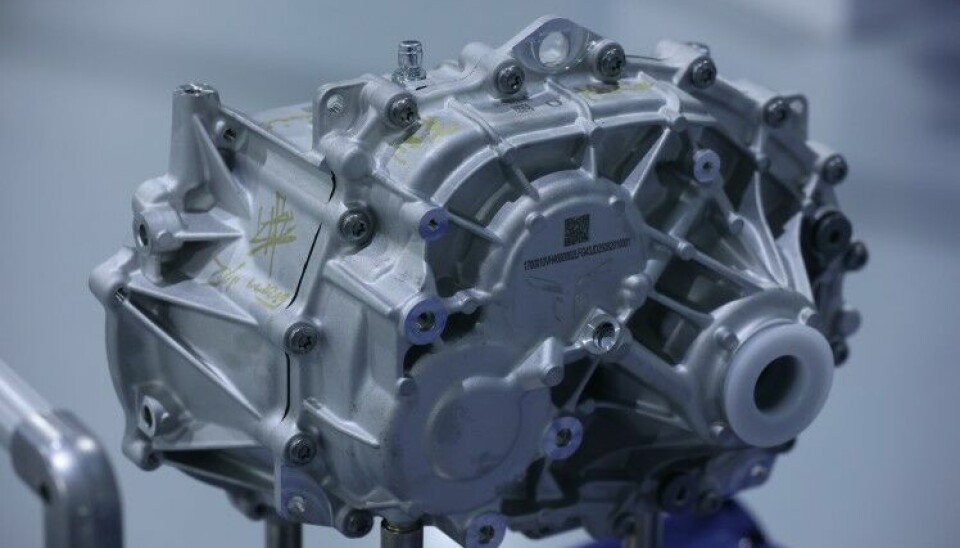
First NEV-focused reduction drive produced by ZF for Chinese market
The electric reducer has been wholly designed and manufactured locally, and is tailored for the domestic market.
ZF Transmissions Shanghai (ZFTS) has reported that the first units of its new reduction drive for new energy vehicles (NEVs) have finished production at a Shanghai plant.
ZFTS is a division of ZF Group that was formed in 2004 following a joint venture between ZF (China) Investment Co., Ltd. and Shanghai Automobile Gear Works (SAGW).
The reducers are a key component in electric drivetrains and have been tailored for the Chinese domestic NEV market. Their design includes a compact axial parallel architecture and adherence to local regulations surrounding efficiency and noise levels.
The first units have been earmarked for “one of China’s leading automotive manufacturers,” according to ZFTS, with the first vehicle Start of Production (SOP) being a midsize SUV scheduled for late 2025. Mass production for the reducer is expected now that the first units have been delivered, though no production forecasts have been released.
ZF executives have pointed to the production milestone as reaffirming the tier-1 supplier’s commitment to localised production and its ability to leverage local expertise. “From customer nomination and project approval to the successful rollout of the product, the entire process was led and executed by our Asia Pacific team,” commented Timo Maisel, senior vice-president of electrified powertrain technology division, Asia Pacific, ZF Group.
The Friedrichshafen-headquartered tier-1 supplier has been committed to a Chinese localisation strategy for “over 40 years”, and plans to continue upgrading its domestic and regional manufacturing and logistics capabilities, Maisel explained. “This achievement fully demonstrates the region’s outstanding capabilities in localised R&D, project management, procurement and manufacturing," Maisel said. "It not only reflects ZF Asia Pacific’s technical strength in NEV key components but also proves our capability to respond quickly and execute efficiently in the local market.”
OEMs, such as Mercedes-Benz and Stellantis, have similarly taken steps to nearshore elements of EV manufacturing, in part driven by increasing volatility in global supply chains and higher levels of protectionism. However, for localisation strategies to be successful, they must be built on effective partnerships. This is an idea explored by Dayan León, parts logistics subdirector at Nissan Motor Corporation, during his Red Sofa at ALSC Mexico 2024. He explained that this can involve embracing innovative approaches to partnerships, “thinking outside the box" and not being afraid of failure. "In failing you start to create, and after a couple of tests you’ll have a new process, new infrastructure and new capacity," he outlined.
To hear more from León and other nearshoring experts, check out our Top 10 Red Sofa round-up: