Ocean container packaging: Hammering out a waste of space
More efforts are taking place to improve efficiency, cost and quality through the better use and construction of packaging within container transport
The expansion of international supply chains has placed increased pressure on maximising the use of ocean containers when shipping global automotive parts. While freight rates, storage and port fees all play a major part in the cost of shipping across the sea, in many ways the key component for optimising container usage is packaging, which affects shipping costs, product quality and transport routes, among other aspects.
Generally, automotive packaging is made for one-way ocean transport because of the prohibitive costs of returning it, although there is growing use of returnable equipment. However, rather than the type of the packaging itself, a more important consideration is often the impact it has on load factors – the ratio between the actual or average amount loaded in a container and the maximum amount that can be loaded.
In this story...
- Moving away from the expendables
- Returnable standards
- New uses for traditional materials
- Mixing it up
Load factors often vary according to the combination of goods. For example, transmissions or engines are much heavier than similar-sized plastic components, so some containers may be half-empty but already meet the maximum allowed weight. Thus, optimising the load factor often involves a trade-off between weight and volume. Packaging has a significant role to play in this area, both in expendable and returnable forms.
One-way more than any otherTo a large extent, expendable, one-way packaging still dominates ocean container shipping for automotive, both for cost and lack of return flow reasons. Frank Neurath, manager of outbound sea freight for aftersales at Volkswagen Group, says the carmaker uses wooden crates, cardboard boxes and wooden pallets for shipping service parts overseas, all mostly one-way packaging. Parts arrive from suppliers at Volkswagen Group’s centralised service parts hub in Kassel, central Germany, in metal boxes and are repacked into containers for global shipments.
According to Neurath, Volkswagen shipped approximately 5,500 40ft ocean containers of service parts from Kassel between January and October 2016. The largest destinations for parts from Kassel are China and the US, which account for around 10% each of total volume.
Volkswagen’s average load factor ranges from 85% to 95%, he says. The carmaker fills up empty spaces in the container by using wooden pallets; it also uses wrapping paper and bubble wrap in the boxes for security.
Achim Glass, head of the global automotive vertical at third party logistics provider Kuehne + Nagel (KN), says about 80% of its automotive shipments are received in cardboard boxes on wooden pallets, with approximately 10% in plastic boxes. KN does not receive metal containers because of the weight disadvantage compared to lighter materials and the impracticality of returning metal containers. In some cases he even notices a growing use of cheaper, weaker cardboard material.
“We are noticing the trend to minimise the strength of cardboard packaging in order to reduce costs. This often limits the stacking of pallets and sometimes does not permit any stacking at all. We estimate that the former applies to 50% of all automotive pallets received for ocean containers,” reveals Glass.
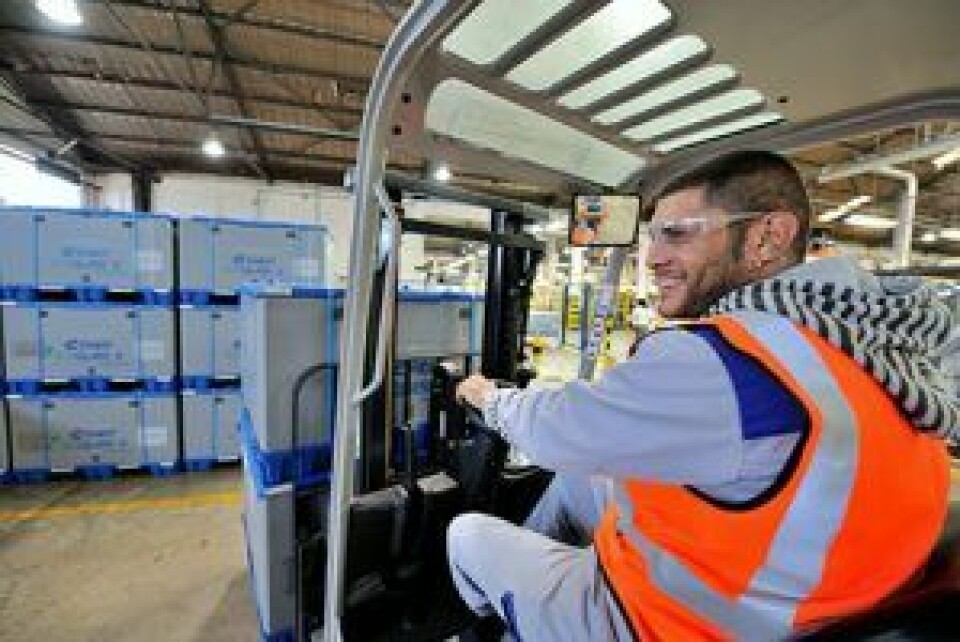
As well as cost and quality benefits, Chep’s returnable packaging uses RFID tags to improve the visibility of sea freight containers
To load the maximum quantity in ocean containers, Glass says KN must often add further support material to improve stability, such as placing plywood panels between the bottom and top pallet layers as a means to spread the weight. It also uses air bags to protect products from shifting during the voyage or air absorbers to protect products from humidity.
Greg Slawson, regional vertical lead for automotive in the Americas at 3PL DSV Solutions, says that his company uses plastic and metal containers to a limited extent within ocean containers, the latter mainly for heavy or high-valued goods such as engines, transmissions and production sheet metal, which are typically shipped in either returnable steel racks or expendable racks that are recycled at destination. Slawson suggests that wooden and metal stillages are of limited use for ocean containers, though they may be used for packing smaller cartons together or for mixed parts.
“Often, we use wood to eliminate the need for reverse logistics, but even so, the cost is still high,” he says. “However, we do offer reverse logistics, as well as scrapping and recycling programmes. Most of our automotive clients use cardboard cartons shipped on wooden, heat-treated pallets. We see some pressed board and some plastic, but at a much lower volume.”
At Neovia Logistics, meanwhile, director of supply chain and logistics Kevin Lucas says the company primarily packs automotive parts in cardboard containers, and uses wooden crates for items such as glass and large side panels because they provide greater protection.
[sta_anchor id="1"]Han Roest, vice-president of global automotive at DHL Global Forwarding, says that although plastic returnable containers should be in use compared to corrugated boxes, it is difficult to return containers to the external supplier. “Shipping plastic containers by ocean is only done for intra-OEM shipments, such as Volkswagen-to-Volkswagen, in order to maintain visibility of the containers,” he says.
Chucking out the expendable for goodAlthough expendable packaging is the primary type used for ocean containers, there is a trend to move away from material like cardboard and wood, at least for some parts and trade lanes. One way that using returnable material is achieved is through pooling networks, whereby manufacturers only rent the equipment for one part of the journey. Rodney Salmon, supply chain consultant for global automotive at Macro Plastics, says that pooling companies such as DHL and Chep offer one-way rentals of plastic folding pallet boxes for which they also find return routes.
"We are noticing the trend to minimise the strength of cardboard packaging in order to reduce costs. [In around 50% of automotive pallets received for container shipping this] limits the stacking of pallets and sometimes does not permit any stacking at all." - Achim Glass, Kuehne + Nagel
Returnable equipment is not just better for the environment, but can also eliminate a lot of excess handling. Salmon points out that with expendable containers, supplies must be bought and stored, including straps, pallet sleeves, bags and dunnage along with the containers and pallets themselves – all of which must be disposed of in some manner. Load factors can also be improved in some cases with more durable equipment.
“The biggest advantage of reusable packaging is the higher cube utilisation of the ocean container. Consolidation centres for expendable packaging can have horrible cube utilisation – as low as 40% – whereas reusable containers can have 90-97%,” he says.
Macro Plastics has recently been involved in a number of returnable ocean container packaging projects with tier one suppliers in South Africa, shipping parts in its ISO bins to Ford and other carmakers in Europe, using DHL. The project began about two years ago and has been rolling out ever since. “This system reduces transportation costs and provides environmental savings. There is no expendable packaging or storage involved,” he explains.
According to Han Roest, demand is up for ISO bins in the automotive sector, which help achieve 95% of container capacity. These may be used for buyer consolidation for 12-14 customers. DHL positions and retrieves these bins, which may be only for one-way trips. “We have seen demand growth for our ISO bins for lanes from Europe to North America, Europe to South Africa, and Japan to Europe,” he says.
DHL rents ISO bins that can be stacked three high in 40ft high-cube ocean containers. “We found that 60 built-up ISO bins fit into one 40ft high-cube container and 160 collapsed ISO bins fit into one,” he says.
At pooling and packaging solutions provider Chep, meanwhile, David Mayo, vice-president of automotive and industrial solutions for Europe, points out that returnable equipment has a number of advantages that include not only cost, but overall quality and visibility. He says that as vehicle manufacturing becomes more complex, the level of efficiency in logistics processes plays a growing role in both environmental impact and profitability. There is growing focus on reducing waste, cost and emissions in the shipping process. For example, Mayo points out that a lot of air is shipped, not only in ocean containers, but also in cardboard boxes inside the containers.
“And this is just the obvious challenge. The use of one-way packaging can bely hidden costs such as part contamination, damage, humidity, shock, vibration, or additional handling, and therefore labour costs,” he says.
He does not pretend, however, that finding returnable solutions is easy or without its own extra processes. For reusable packaging, the first challenge is to find a standardised container solution. “The next challenge is paying for unnecessary backhaul shipments in any closed-loop operation in order to get the packaging back to its origin. Additionally, managing any container pool to avoid shortages, repair, tracking, etc, is essential within a global supply chain,” he states.
However, Mayo suggests that the overall costs of ownership in many situations benefits returnable equipment, particularly where a global footprint can be used to build effective flows. He points to average cost savings in double-digit percentages. “It is not only about loading the right packaging in the ocean container; the real benefits come from the global sharing concept. Freight and load optimisation ensures the continuous rotation of containers around the globe, which benefits all users,” he says.
A further benefit of returnable packaging can come in the ability to make better use of technology and [sta_anchor id="2"]tracking. For example, Mayo suggests that as the value of electronic equipment moved in containers rises, there is growing interest in using packaging that can measure conditions such as heat and humidity, as well as identify tampering. Mayo says that Chep has already extended its product portfolio to use more technology, including RFID-enabled tags that are dedicated for sea freight containers.

A standard for allAs Mayo suggests, one of the difficulties in using returnable equipment for ocean container shipping is finding equipment that can be used across multiple regions, where varying sizes in transport equipment and packaging play a big role. Packaging specialist Schaefer Systems International is considering this challenge as it aims to increase reusable packaging for ocean shipments.
David McCulloch, chief executive of Schaefer’s packaging systems division, thinks it is a good time to make gains in returnable ocean container packaging. 3PLs now have better asset management systems for tracking returnable containers. Another reason is increased legislation prohibiting wasteful and excessive packaging.
Schaefer Systems performed an analysis of reusable packaging in the global marketplace and found that each footprint appeared to be designed for one mode of transport and none were optimised for all modes. For example, the standard footprint for a 53ft trailer does not account for the best cube utilisation in a sea container.
“That analysis led us to develop a solution called the GlobalStac bulk container, which features a multimodal footprint. GlobalStac’s 1,195mm x 990mm footprint cubes a 53ft trailer – which is used in North America – a 40ft sea container and even the three-metre high trailers used in parts of Europe,” he explains.
The main objective of GlobalStac is to simplify global logistics, establishing a standard that can cover the many regional variations and help to avoid having to use several different types of packaging containers when shipping across different regions, as well as avoid increased handling, inventory and warehousing expenses.
[sta_anchor id="3"]McCulloch says the main benefits of GlobalStac are maximising the container cube and the cost savings from a reusable system. “Historically, we have targeted a North American customer base complying with AIAG standards. This product will target a global audience,” he says.
Improving wood, plastic and cardboard Moves to improve ocean packaging are not happening strictly by increasing returnable material. 3PLs are always on the lookout for higher load factors and reductions in damage.
Neovia’s Kevin Lucas says the company has recently collaborated with an OEM client and Belgian packaging provider DS Smith to introduce new packaging for shipping bumpers that improves space utilisation in both shipping containers and bulk storage. The package is made of cardboard, paper, corrugated board and a wooden pallet, and each bumper is individually packed. The new outer ‘shipper’ holds nine high per stack with five individual bumpers per pack compared to three-high stacking with four parts per stack before. Previously, 36 bumpers could be shipped per ocean container, but the new packaging allows for 50 bumpers – a 38% increase in outbound efficiency. Lucas says the company is looking for a collapsible return ratio of 1:4 and wants to develop it for the Chinese market.

One of the problems that DSV Solutions experiences is that a consistent amount of freight is not properly packaged for international shipping. Common errors include a lack of corner bracing, tiered or pyramid stacking and non-standard pallet sizes. DSV is trying to address the issue by emphasising supplier compliance for shipping standard packs and collaborating with packaging engineers.
The type of facility at which an ocean container is loaded may also affect utilisation rates. For example, Greg Slawson points out that supplier origins are effective for large, dedicated export consolidation centres. Port locations are effective for both buyers’ consolidations and dedicated multi-client consolidations.
KN, meanwhile, consolidates cargo for weekly less-than-container-load (LCL) shipping lanes, of which the majority is done at company-operated facilities. The consolidation centres are located either inside the port or in close proximity to the harbour. It also uses its own inland stations for buyers’ or shippers’ consolidation containers, in which either one customer supplies material from various different factories or a very limited number of complete knockdown kit shippers expedite high and weekly volumes directly into the warehouse of the car manufacturer overseas.
[sta_anchor id="4"]“The benefits of inland consolidation are that it saves costs on pre-carriage and that buyers’ consolidations are unloaded directly inside the factory. That benefits automotive customers by saving an average four days’ lead-time,” says Achim Glass.
A mixed future A method that may improve ocean container optimisation would be to combine automotive and non-automotive products in the same container for the purpose of reducing transport and warehousing costs. “Mixing commodities can be a cost-effective solution for very low volume LCL shipments, but is not a recommended approach for production material,” says Jens Riemann, director automotive, global business development at DSV Solutions.
KN’s Glass agrees that mixing commodities in the same container has its disadvantages. “We try to keep the industry product mix as homogeneous as possible. The greater the variation, the greater the spread of different packaging weights and dimensions, both of which influence the container utilisation rate,” he explains. “In addition, the more homogenous the freight, the lower the damage ratio. We dispatch automotive-only consolidation containers to many automotive hotspots such as South Africa, Mexico, Japan and the United States.”
However, there is a potential reduction in efficiency in shipping automotive-only containers. Glass says that KN often cannot fully maximise the container space because it reaches the weight limit before fully filling the container.
Packaging providers and 3PLs are working to build a better container and the packaging that is so essential to its cost, effectiveness and quality. Returnable packaging, which is in such wide use for intra-regional shipments, is still testing the waters when it comes to ocean shipments and may gain further ground as technology, legislation and global footprints evolve. The top priority for most is to use container space as fully as possible – and that is likely to continue to drive the type of packaging that is used around the world.
"Mixing commodities can be a cost-effective solution for very low volume less-than-container-load shipments, but is not a recommended approach for production material." - Jens Riemann, DSV Solutions
Read more about the use of tracking technology on reusable packaging