Real-time visibility platforms keep automotive supply chains moving
The global automotive market is competitive and volatile, and manufacturers and OEMs were already under pressure thanks to new market challengers such as Tesla, and consumer preferences shifting towards electric vehicles (EVs).
Now they’re also facing a global pandemic, with lockdowns, travel restrictions and greater financial uncertainty. Production plant managers are struggling to develop more efficient ways of carrying out day-to-day supply chain execution. Fortunately, technology is on hand to help tackle these challenges.
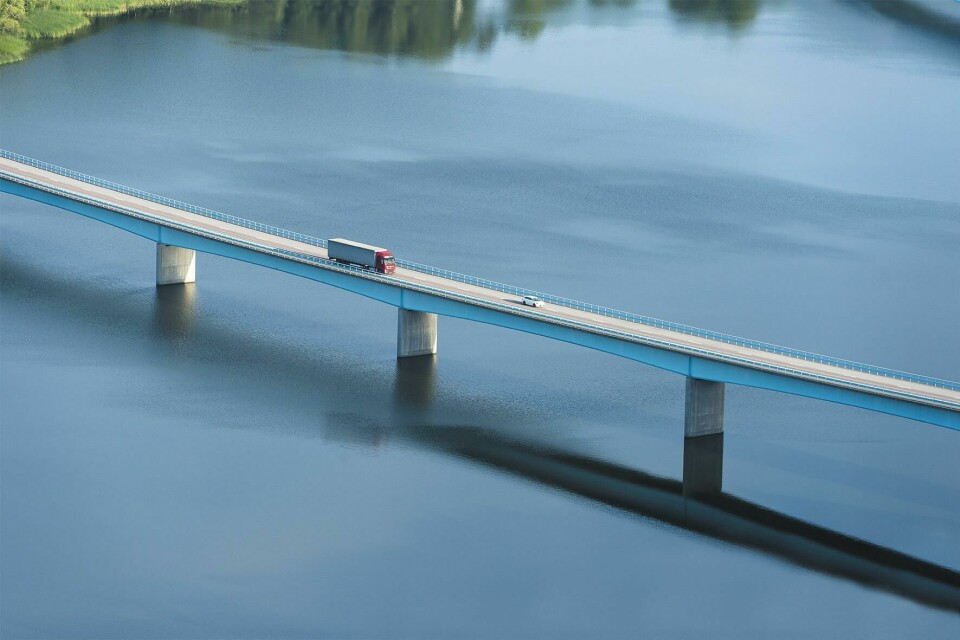
Real-time transportation visibility (RTTV) platforms help to improve efficiency, reduce costs, and improve planning capabilities. They boost collaboration amongst supply chain partners, reducing friction and duplication of tasks, and overcoming silos. Using new, easily integrated RTTV platforms to share real-time datasets shifts collaborators’ mindsets from a nodal to a network mentality, paving the way to tackling some of the industry’s biggest difficulties, such as reducing time to market.
By incorporating a high degree of visibility throughout the end-to-end supply chain, more data and information becomes available to facilitate smarter decision making. This is shifting planning horizons from periodic to real-time, facilitating the continuous development of plans based on the latest operational performance data.
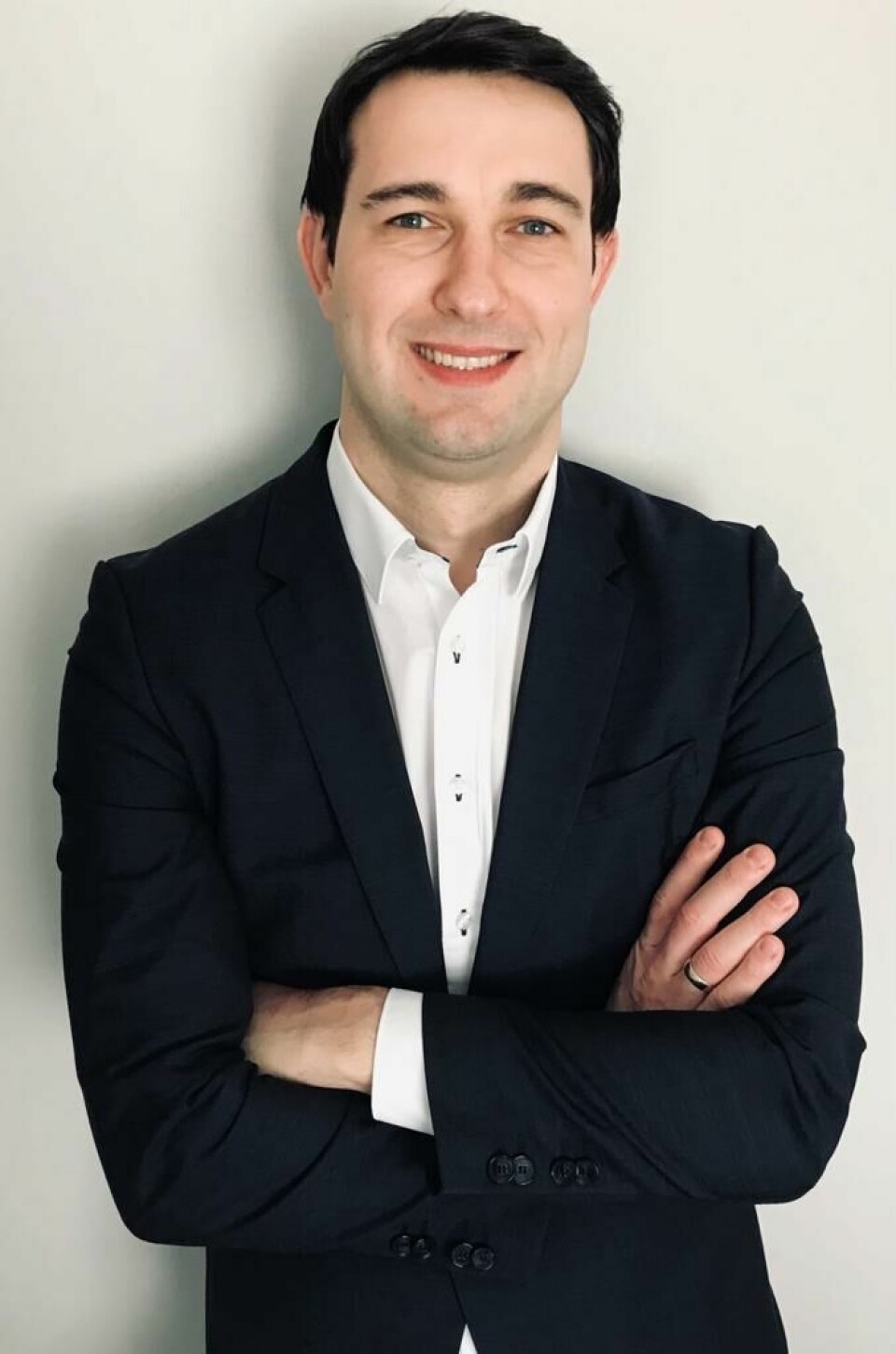
Reducing downtime, penalties, recalls
Assembly line downtime is expensive and suppliers can face hefty penalties if they fail to meet delivery deadlines. An RTTV solution can provide highly accurate and reliable predictive ETAs, helping suppliers and carriers to satisfy strict just-in-time (JIT) manufacturing requirements. Sophisticated solutions automatically send alerts if a shipment is likely to miss its planned ETA, allowing corrective action – such as urgent air transfers of parts – to be taken. Accurate ETAs also help manufacturers and OEMs avoid the cost of unnecessary expedited air deliveries, saving suppliers and carriers hundreds of thousands of euros in penalties.
Recalls are another potential cost factor. With the sheer volume of parts in cars, and the globalisation of platforms and technologies, suppliers’ systems and components are used in multiple car models around the world, greatly increasing the number of customers potentially affected by a recall. Real-time tracking of parts supports quality control, with network-connected smart sensors receiving objective data on indicators such as the temperature or humidity inside a shipping container or truck at any given moment. Being able to identify and ring-fence parts shipments affected by quality breaches helps to avoid a far wider and costlier recall.
Increased agility and greater resilience
In addition to improved decision making thanks to real-time supply chain performance data, the flexibility of application programming interface (API) integrations used by RTTV platforms also unlocks further organisational agility. Most of the automotive industry operates on electronic data interchange (EDI) technology standards for securely sharing data between ecosystem partners, specifically the Edifact international standard with the VDA norm 4984, ASN 4987 or IFTSTA 4945.
While this enables manufacturers and their OEMs to make requests for the transport of parts and receive pick-up confirmations and planned delivery slots, no data is available on whether parts will be delivered on-time in-full (OTIF) in case of disruption.
The technology is expensive to maintain and update, and adding new data exchange partners can be cost-intensive. This makes it difficult to change or add suppliers quickly in response to market changes, potentially taking months to onboard and requiring significant investment, which in turn limits agility. API integrations on the other hand can be implemented in weeks or even days and are relatively straightforward and cost-effective.
A lack of visibility is a major supply chain risk factor and a potential source of vulnerability for any company. The increasing complexity and fragmentation of automotive supply chains has left it vulnerable to disruptions. In 2011, a major earthquake and tsunami in Japan shut down factories that produce widely used electronic components for cars, halting assembly lines worldwide. The Hitachi plant produced sensors used in Peugeot’s diesel engines to regulate the flow of air. Peugeot had just 10 days’ worth of sensors in stock, forcing seven factories in France and Spain to slow production. For some carmakers it came as a surprise to find out that their components had any links to the disaster zone. Contingency plans had not gone far enough, and original assumptions needed to be rethought. This event served as a reminder of just how complex, risky and under stress automotive supply chains had become and highlighted significant end-to-end visibility gaps.
Automated continuous improvement
Both real-time and historic performance data for key transport key performance indicators (KPIs) such as dwell time, OTIF and punctuality, can be fed from an RTTV platform back into a car manufacturer’s or OEM’s existing system to improve their level of supply chain performance data for analysis. Vast data sets can be processed by machine learning algorithms to identify more subtle, complex patterns based on historical disruptions and their outcomes. Artificial intelligence applies machine learning techniques to establish correlations and patterns, identifying future events further in advance based on past lessons learned. This allows the supply chain to ‘self-learn’ by automating the process of continuous improvement as intelligence and decision making continues to improve all the time.
RTTV can play an important role in helping manufacturers and their OEMs cut operational costs. Improved quality control and security of freight in transit, more streamlined processes and communication between internal and external teams, reduced safety stock and savings in transport costs and carbon emissions can all be achieved through greater visibility of transportation. Tactical and strategic benefits further boost the ROI of RTTV solutions by facilitating better collaboration between supply chain partners for a faster pace of innovation, enhanced planning capabilities, increased agility and resilience. By leveraging new technologies to eliminate unnecessary operational costs and increase flexibility and agility throughout automotive supply chains, manufacturers and their OEMs can better cope with disruptions, gain a competitive advantage and ultimately improve both customer experience and shareholder value.
Andreas Seide, strategic account executive for automotive at Shippeo SAS