Recalls: whose responsibility is it anyway?
With voluntary automotive recalls on the rise, it begs the question of who should handle what across the supply chain, including logistics
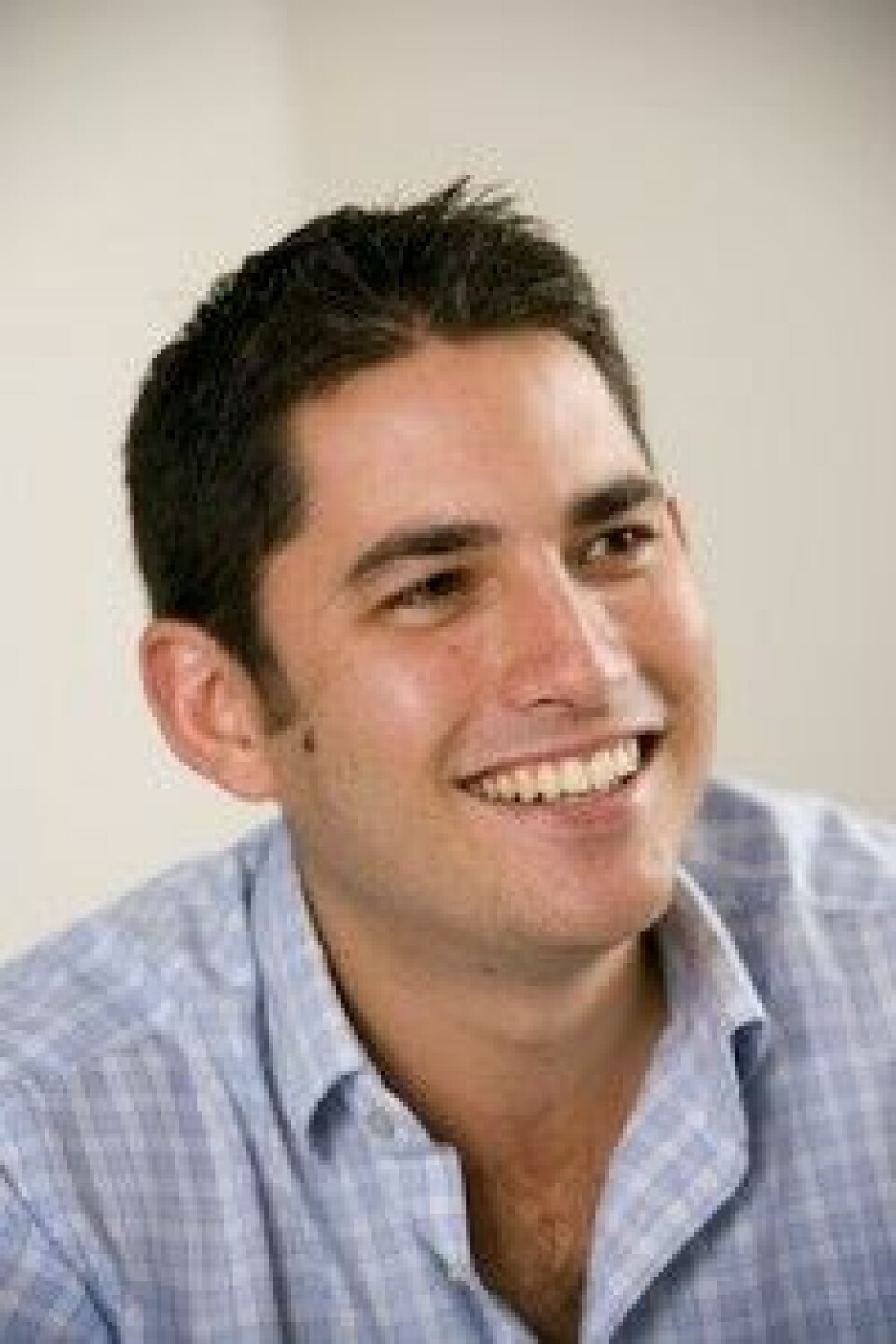
The automotive industry has a higher percentage of voluntary recalls and product notifications than any other industry. In the second quarter of 2014 it was 100% and every notification was voluntary. However, in the automotive sector, recalls and notifications are complex, and issues over responsibility or ownership can easily become clouded.
The physical supply chain is made up of a vast network of OEMs, global parts suppliers and dealerships. And when it comes to safety notifications and recalls, local and national legal bodies, and insurers, are intrinsically linked to the process too. There are many players involved and it is important to understand where responsibility lies.
Usually, an OEM, or a body such as the Driver and Vehicles Standards Agency (DVSA) – the government body in the UK responsible for monitoring recall standards – initiates the recall process. This comes from a manufacturer discovering a potential fault or security hazard within a vehicle, or the DVSA collecting customer reports about potential issues. Despite the huge scale of recent recalls, the majority in recent years have been voluntary, and initiated by an OEM, which highlights a continuing ‘safety first’ approach by the industry.
OEMs have the responsibility to identify faulty vehicles and begin communication with those affected, including suppliers, dealers and customers, but as the supply chain is so complex, the process of a recall can become significantly prolonged.
In the UK, the automotive industry is closely monitored due to its high value products and the potential safety implications. For example, the DVSA dictates the level of return rates OEMs must achieve before a recall can be deemed complete, but an OEM must oversee the recall, and manage communication.
Not only that, but manufacturers must also prove to the DVSA that they have taken all possible actions to inform customers, and resolve associated issues. In the case of any recall, manufacturers must follow this protocol. [sam_ad id=6 codes='true']
Dealerships come into the equation when OEMs do not have the local presence required to deliver a satisfactory level of customer service. If parts need to be replaced or servicing needs to happen, an authorised dealership is likely to be the body that takes this on.
The outlay for new parts, replacement cars, and labour can quickly lead to escalating costs, so who is responsible to foot the bill?
For a specific part that has sparked a recall, an OEM would expense the supplier, who would then claim it back on insurance. In some cases, larger OEMs operate a hub system, with a local market recharging the cost back to the hub. But there are potential issues with this system: if a local dealership has to bear the initial cost, how long could it be before they are reimbursed?
The rise in voluntary recalls is not necessarily a bad thing, however, as it shows that OEMs are committed to protecting customers and delivering good service. But it is important that quality and safety is continually monitored. While many would assume that brand reputation would suffer after a recall, if handled correctly, brand reputation can be enhanced, or at least maintained. Earlier this year, a report by Kelley Blue Book found that the majority of shoppers remain unaffected by the General Motors’ US recalls, with just 5% saying they would not consider purchasing a GM model. This is despite a strong awareness of recalls, with 48% of respondents remembering Toyota’s recent recall, and 40% aware of the GM recall.
A recall gives OEMs and dealers the opportunity to go ‘above and beyond’ to strengthen customer relationships, but this only goes so far. If recalls continue to happen, trust and patience will eventually run out. After all, the customer has the final say. But if a recall should become a necessity, it is the responsibility of all involved to co-operate and protect the customer.
Barry Nielsen is automotive solutions director at Stericycle ExpertSolutions