Russia's industry branches out
The shift of manufacturing away from Moscow and into central and eastern regions of Russia and Central Asia has given rise to new and familiar challenges for the country's inbound and outbound logistics service providers
An increase in Russian vehicle production, particularly in central parts of the country, has led manufacturers andlogistics providers to re-engineer their logistics networks. With localisation still low for global manufacturers in Russia, some are looking at multimodal and rail transport to move international freight. However, they face infrastructure gaps, customs clearance and regulatory restrictions.
According to Russia’s International Organisation of Motor Vehicle Manufacturers (OICA), the country produced 2.23m cars and trucks in 2012 – an increase of 12.1% over 2011. Russia’s market demand has also recovered since the financial crisis, although volumes are stagnating this year.
Peter Sauer, spokesperson for DB Schenker Logistics says that although automotive clusters in Moscow, Kaluga, and St Petersburg showed the most growth the last five years, his company anticipates that demand for logistics services will rise most in the Volga region over the next two years. Customers in the region include a number of OEMs in Nizhny Novgorod, Ford Sollers in Yelabuga, Kamaz in Naberezhnye Chelny, UAZ in Ulyanovsk and Renault Nissan in Togliatti.
Russia’s neighbours, including Kazakhstan and Uzbekistan, have also been expanding vehicle and equipment production in parts of the world where logistics infrastructure is still developing.
Government support for the automotive sector is an important driver of the current growth, including regulatory support and customs facilities. Much of the production capacity coming online now is partly driven by Russian industrial policy, including Decree 166, which mandates production of 300,000-350,000 units per year and localisation targets in exchange for preferential tariffs.
The government is supporting localisation in other ways. According to Sauer, the Russian government permits the development of customs facilities in exchange for OEMs and tier suppliers using at least 30% local content within a specified timeframe. He sees a definite trend towards more manufacturers localising.
An ever more global supply chain
But while global manufacturers will source more in Russia, some Russian carmakers are looking to develop further their global supply chains. Among the leading Russia-based manufacturers is the Gaz Group, which receives 550 trucks and containers every day for its light commercial vehicle production, and will receive another 220 containers for contract manufacturing operations at full production. The company has a large domestic supply base for its LCVs, most of which feeds its plants by truck, while its semi- and complete- knockdown kit assembly (SKD and CKD) uses more multimodal transport. Gaz’s demand for larger trucks is increasing following the implementation of system-wide milkruns for domestic suppliers, according to president and CEO Bo Andersson. Compared to the first half of 2012, Gaz’s transport vehicle size has increased by 25%.
Andersson says that Russia’s entry into the World Trade Organisation last summer provides Gaz with stronger incentives to look for suppliers more globally. “Our goals include an intensified focus on competitive sourcing,” he says. “With the launch of our new LCV model GAZelle NEXT this year, we have increased the number of foreign suppliers and parts sourced outside of Russia or the Commonwealth of Independent States (CIS).”
"With the launch of the GAZelle NEXT this year, we have increased the number of foreign suppliers and parts sourced outside of Russia or the CIS" – Bo Andersson, Gaz Group
Gaz is increasingly sourcing parts and components from South Korea, and especially from China and Turkey. From China, Gaz now receives 96% of volume by rail and 4% by sea, says Andersson. The OEM ships 60, 40ft containers monthly by rail from Beijing to its plant in Nizhny Novgorod, some 400km east of Moscow.
Maxx Intermodal Systems, a subsidiary of Rhenus Logistics, sends intermodal block trains from China to Russia. From Europe, it ships automotive parts to Russia via St Petersburg and Ust-Luga as well as Finnish and Baltic Sea ports.
Raf de Schutter, director sales and development at the company, says its shipments to Nizhny Novgorod and to Kaluga for Volkswagen have been growing since last year, when it began shipping three block trains weekly from Slovakia and the Czech Republic to these locations. “Although most shipments from Europe to Volkswagen Kaluga move by block trains through Maieszkowice, Poland and Brest, Belarus, we take a different approach,” De Schutter reveals. “We switch from the standard rail gauge to the narrow one in Matovce, Slovakia and cross the Ukrainian border at Uzhhorod. This route is lower priced and is 12-24 hours faster than the one through Poland and Belarus.”
DB Schenker Logistics ships by all modes to Russia, especially rail. According to Peter Sauer, its main flows are from Europe by short sea through St Petersburg and by rail from northern Germany, the Czech Republic and Slovakia.
Schenker has also developed supply chain solutions that combine ocean and rail from Mexico – which is the mother plant of the Volkswagen Jetta built at Gaz’s plant – to Nizhny Novgorod. Maxx Intermodal Systems also ships agricultural equipment from the US via the ports of Kotka, St Petersburg, and Riga, then moves them by truck to Moscow.
With CKD production growing from models produced globally, including South Korea, Brazil and Mexico, Sauer notes that inbound volumes from the Americas and Asia will likely continue to increase.
It’s not easy going local
Tier one supplier Magna International ships from a consolidation point in Chemnitz, Germany by full truckload to its plants in Kaluga, Nizhny Novgorod and St Petersburg. According to Karl Lukas, head of supply chain management and logistics services, Magna sources about 80% of its Russian production from Europe (mainly Germany and the Czech Republic) and 20% from Russia, and plans to open a second warehouse in the Czech Republic this year.
However, the pattern of supply is considerably different across Magna’s plants depending, in part, on the customer it is serving. Its Nizhny Novgorod plant began sourcing from North America this year, in particular from Mexico, which now makes up of 20% of its supplies; 10% of this plant’s supplies are from Russia and the rest from Europe. “In the future, we will have more suppliers that are domestic. In fact, at our metal production plant in St Petersburg, most are Russian,” Lukas says.
"The lead time from Europe ranges from 10-40 days and from overseas, 40-50 days. Our exception management strategy stems from the long lead times involved" - Karl Martin Lukas, Magna International
He adds that the further east in the country Magna goes, the more difficult it is to meet its requirements for lead time, service and quality. The challenges it faces include stability in scheduling; tracking; information gathering; and quality. “The lead time from Europe ranges from 10-40 days and from overseas, 40-50 days. Our exception management strategy stems from the long lead times involved,” says Lukas.
Magna would like to localise more suppliers, he adds, especially since Decree 166 requires 30% local content for certain duty and customs benefits, but he admits the company is struggling to hit that target.
As Gaz expands its sourcing network, it has centralised its inbound logistics and consolidation points, as well as reduced the use of freight forwarders, to improve utilisation in the network for

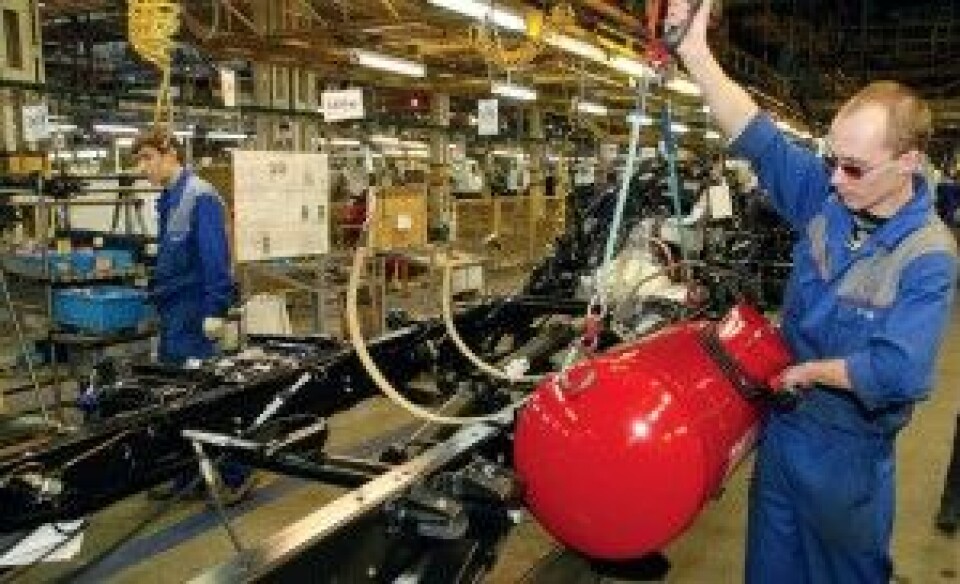
imported parts. It has also reduced the number of empty transport vehicles. “With our contract manufacturing volumes, we see a great potential to find synergies with our partners,” says Andersson.
Andersson also says there has been a 30% increase in the number of suppliers that provide just-in-time (JIT) deliveries to Gaz and a 40% increase in the number of parts involved. More frequent JIT deliveries from domestic suppliers to the production line have also reduced the OEM’s inventory.
Furthermore, Gaz now has ‘Authorized Economic Operator’ status, which speeds up customs clearance significantly, Andersson says, including helping to lower inventory in transit or warehouses.
The vehicle maker’s next objective is to create a group-wide crossdock network for its 13 plants, says Andersson, which would help it to supply smaller and more frequent shipments.
The perennial issues
Providers and manufacturers point to problems endemic to Russian logistics over the past decade. Russian Customs is a constant challenge, says Peter Sauer, including keeping up with new regulations, bureaucracy and in-transit customs clearance from inland points to the borders.
Land and warehouse availability is also scarce. Sauer points out that the vacancy rate for the highest quality warehouse space in Russia is only about 1-1.5% in key regions. “Along with the lack of warehouse space in automotive centres such as Kaluga and Nizhny Novgorod, there is little interest among developers in building for sale – only in build-to-suit projects, which are rentals,” he says.
There are also poor roads connections from container ports to inland destinations. “The infrastructure and operation of Russian ports is lacking, particularly when facing unfavourable weather conditions,” says Sauer. “The lack of infrastructure around manufacturing zones, such as container yards not having rail capabilities, is a problem.”
Disputes with Russia’s neighbours also tend to impact logistics negatively. For example, Russia and Poland have regular issues concerning road transport licences, which lead to bottlenecks in truck availability. There is an on-going dispute with Baltic Sea countries about port access and forwarding to Russia, Sauer says. DB Schenker will try to move goods onto short sea or road depending on the issue, but the uncertainty presents difficulties.
"Road restrictions on the Moscow ring road mean we have to make more night-time deliveries and use small trucks that hold only one or two cars" – Kamil Mezynski, Algai
Growth in Central Asia
Although Russia is by far the primary producer and market in the region, neighbouring Kazakhstan has a growing automotive industry with assembly centres in Ust Kamenogorsk and Kostanay. Logistics for the landlocked country is complex, however, and often involves long-distance rail. Maxx Intermodal moves containerised parts from the South Korean port of Busan to the Chinese ports of Qingdao and Lianyungang, as both have special transit rates to Kazakhstan. From China, it ships by rail via the border crossing of Alashankou in China and Dostyk in Kazakhstan as well as Khorgas, China. “We ship 50-100 containers per month to Almaty and Kostanay, which takes between 21 and 25 days,” says De Schutter.
Gefco operates in the country’s largest city, Almaty, in the southeast about 350km from the Chinese border, and in the capital Astana. For the automotive sector, Gefco handles mainly new vehicles in the country, which it clears customs at its compound in Almaty, then delivers to dealerships, according to Dmitry Gubanov, general manager of Gefco’s Eurasia Multimodal Alliance.
“When Kazakhstan joined the customs union with Russia and Belarus three years ago, the import tax on used vehicles increased, so the flow dried up,” says Gubanov.
Gefco, which is now controlled by RZD Russian Railways, has a Baltic subsidiary in Riga that moves Volkswagens from Germany by road to Vilnius, Lithuania. From there, vehicles move to Kazakhstan by covered rail, which takes 14 days. The total lead time is 20-22 days, according to Gubanov. Gefco moves about six rail wagons per month. In Russia, the company also moves two or three truckloads each month of Volkswagen vehicles from Kaluga to Almaty with a five-day transit time. “Weather can play a major role. Snow blocks roads but not railways,” says Gubanov.
Gubanov says that Gefco’s main improvements in Kazakhstan are in securing back loads, which is difficult given the relatively low volumes and density. Gefco ships from Kaluga to Almaty and then loads Suzuki vehicles that are destined for western Kazakhstan. From there, it sends the empty trucks back either to Kaluga or to Togliatti to pick up Avtovaz vehicles for Moscow.
Gefco also transports Japanese-imported Suzuki vehicles from Ust-Luga by covered rail wagons to Almaty. Marina Kuznechevakaya, Gefco Kazakhstan marketing and sales manager, says it handles the local delivery of five or six truckloads of Suzuki vehicles per month from Almaty, mostly to western Kazakhstan.
“We are considering rail transport for these moves and hope to start using it by next year,” says Kuznechevakaya. This would involve switching from the port of Ust-Luga to a route through China.
Aside from finished vehicles, Gefco is experiencing growth in moving parts for oil equipment, especially to western Kazakhstan. Suppliers consolidate components in Western Europe and move them by road as full truckloads. Gefco also ships project equipment in rail wagons and sea containers from China to Kazakhstan. The goods originate in the Philippines, Singapore, and Malaysia, says Kuznechevakaya, from where they ship by sea to Shanghai or Hong Kong before continuing by rail to Kazakhstan.
Uzbekistan also has a manufacturing base. GM’s joint venture plant produces for the local market and exports to Russia, while there is also manufacturing for agricultural and construction equipment. Maxx Intermodal ships between 150 and 200 containers monthly of SKD kits for the production of trucks, tractors, and agricultural combines. From the ports of Hamburg, Bremerhaven, and Le Havre, it ships by sea to Riga, where containers move by rail via Russia and Kazakhstan to Uzbekistan, for a lead time of about 25 days. The main destinations are Tashkent and Samarkand, the country’s two biggest cities.
Further distance, more outbound loading points
On the finished vehicle side, Gefco uses the Black Sea port of Novorossiysk, which handles automotive volumes, particularly from Turkey, Italy, and Spain. Black Sea ports have been used to a minor extent for several years as an alternative to the more congested Baltic Sea ports.
Major Auto Trans, a major outbound provider for imported vehicles and domestic movements, opened compounds last year in the Moscow region for 9,300 vehicles and Togliatti for 4,000 vehicles. The company’s CEO, Alexander Zhuravlev, says that there is a trend for an increasing number of loading points, including Moscow, St Petersburg, Togliatti, Izhevsk – for United Automobile Group, a subsidiary of Avtovaz, where Renault Nissan is also assembling vehicles – as well as Kaluga, Nizhny Novgorod, and Yelabuga for Ford Sollers.
"There is a trend for an increasing number of loading points, including Moscow, St Petersburg, Togliatti, Izhevsk as well as Kaluga, Nizhny Novgorod and Yelabuga" - Alexander Zhuravlev, Major Auto Trans
Zhuravlev predicts that the most growth in vehicle flows will come from Togliatti, particularly for Avtovaz and Renault Nissan production in the region.
Gefco’s subsidiary Algai owns a fleet of 200 car hauliers and operates two distribution compounds in the Moscow area and one near St Petersburg. General director Kamil Mezynski says that although Algai’s volumes increased significantly last year to more than 330,000 units, the stagnating market today is hurting car hauliers. “The market has an overcapacity of road transporters,” says Mezynski.
Following the slowdown, Algai has seen more stock at its distribution compounds, for which it is trying to secure more space. Mezynski says the company is also trying to organise distribution so that its customers do not suffer longer lead times as volumes decrease. To maintain the agreed lead times, the company is combining loads to different destinations or mixing the vehicles of different manufacturers.
Another issue has been recent traffic restriction on the Moscow ring road, with vehicles of more than 12-tonne capacity not allowed to use the road between 6am-10pm. “This makes deliveries to Moscow dealers much more complicated, especially considering that Moscow’s volume reaches 40% of our business or even 60% for premium brands. Thus, we needed to provide more deliveries at night and use small trucks that hold only one or two cars,” says Mezynski.
Such issues seem likely to persist in Russia, particularly as Russian policy continues to encourage manufacturing activities away from Moscow and out into Russia’s central and eastern regions. This migration is part of the country’s unique challenge and opportunity for both inbound and outbound logistics. With demand still concentrated in the west, but production growing across the country, there is more interest in multimodal services as well as pressure for more efficient routing, whether through milkruns or crossdocks for inbound, or filling empty backhauls for outbound. Although the Russian market remains unpredictable, logistics providers who can offer such services are likely to stay in demand.