Scratching the surface of damage protection
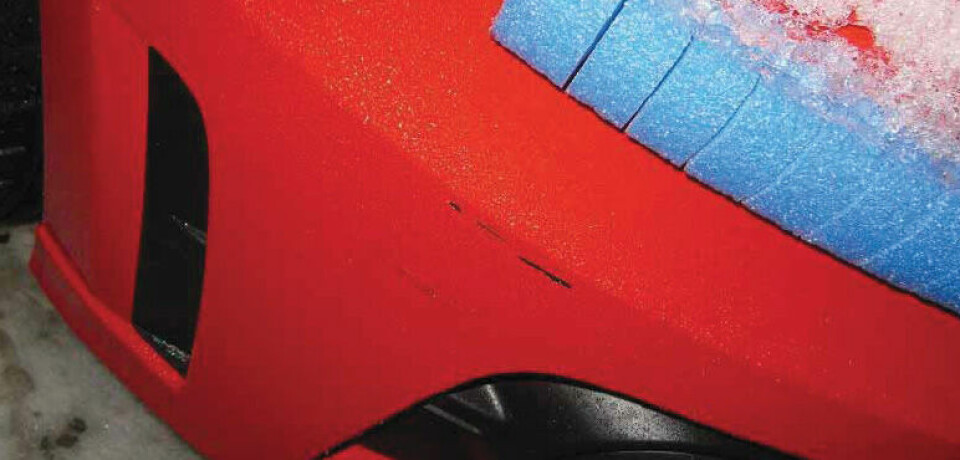
The long journeys experienced by finished vehicles require a co-ordinated approach to improving handling and prevent the risks of damage in transit, writes Andrew Williams.
By the time new cars roll off production lines they will have undergone a series of strict and rigorous quality control tests to ensure they hit the dealerships in immaculate condition. However, for most car companies, the reality is that after new vehicles leave the factory there is always a risk that they will be damaged before they reach the showrooms. Damage to vehicles in transit is a major headache for car manufacturers, and one in which they invest a good deal of time and money in trying to cure. So what are the latest developments and innovations in the damage protection sector–and what part might logistics providers play in minimising the risk of transport-related damage?
Types of damage
The most common types of damage to finished vehicles in transit are minor scratches and dents, often to the driver’s side door, bumpers, wheel rims and fenders or wings. At American Honda, these two types alone account for some 40% of total damages–mostly ‘severity two’ or less, or about one to three inches (2.5-7.5cm) in length or diameter. Limited clearances in or on various conveyance types and improper handling frequently contribute to such damage.

“Poor clearance may result in damage when handlers make contact with a vehicle while applying chocks in railcars where space is limited or when securing a vehicle on a truck. Poor handling practices such as driving too fast on to or off of transportation equipment can contribute to the high frequency of damages to bumpers,” says Gary Cooper, assistant manager at American Honda’s logistics planning and quality assurance department. “When cars leave production sites they are very often transported on trucks specially designed for these kinds of applications. During this transport you need to open doors to manipulate the cars and this is where the damages [often occur],” says Eckhard Rössler, senior product manager at Nomafoam.
Some observers suggest that damage to tyres can be caused by metal anti-skid systems of the typical welded square bar (or ‘fishbone’) and expanded metal design. Mark Butler, technical sales manager at RS Clare, has seen examples of tyres embedded with metal when the fishbones and/or expamet on such surfaces have broken away from the ramp surfaces, normally as a result of welding failures. “Also, when they have aged and worn somewhat the fishbones offer very limited traction in wet conditions, causing vehicles to slide and skid, sometimes impacting with other vehicles or the sides of the ramps,” he explains.
Damage limitation
To minimise the damage to vehicles in transit a wide range of protection products have been developed over the years. Commonly used products include protective plastic wrappings and covers, waxes, protective tape and polymer coatings. The effectiveness of each product depends on a number of variables, particularly the logistics mode and type of transport used, although they all tend to have advantages and disadvantages. Plastic wrapping effectively prevents minor damage and environmental fallout on horizontal panels depending on the area covered. Protective plastic wrap can also be effective when applied along the side of vehicles, where contact by the handler is often more likely due to limited clearance. Covers may be better for longer-term storage, but are only about as effective as plastic wrapping for preventing minor damage during handling.
“Provided that it is well applied I would say that [wrapping] is quite effective. Full covers are expensive, and even if reusable they would only be applied to premium class models. We only advise clients to apply wrap film or PGF in case the stock area is in a high risk area for chemical fall out,” says Norman Van Der Werff, manager at Tokio Marine Management Services.
However, full body covers can hide damages until the vehicle arrives at the dealership, warns Eric Imiola, managing director of the UniCar Group. This can cause problems in assigning liability or understanding the root causes of damage. When applied to targeted areas such as exterior door handles, protective tape can be effective in preventing minor damage. Used inside a vehicle, it can also prevent scuffs on doors or rocker panels and prevent soiling on armrests. Protective waxes and polymer coatings are also generally effective at preventing scratches but not dents.
“[Wax is] more effective against environmental hazards such as salt, soot or other fallout than for protection against physical damage,” says Richard Duvall, logistics quality coordinator at American Honda. “Polymer coating will not prevent dents but will protect against hairline scratches, which are very often caused by the improper or dirty clothes of people handling vehicles,” says Van Der Werff.
Other products used include weather-resistant protective sprays, which provide a similar degree of protection on the exterior of vehicles as that provided by protective plastic wrapping and tape and may effectively cover a greater surface. Foam pads, or ‘transport protection pads’ are now also used by many of the big European and North American car producers; they are fixed on commonly observed damage sites such as doors and boot panels with light adhesives. Nomafoam also produces ‘windscreen profiles,’ a patented foam solution to protect windscreens while being transported.
“We expect, that [use of] the door and bumper pad foam solution will increase in the near future. [This is] mainly due to the fact that transport costs are increasing and parking places during transportation will become more narrow, so that you have to be very attentive while manipulating cars and opening doors,” says Rössler. However, although each protection product can prevent against some types of damages, none of them are generally effective in all situations.
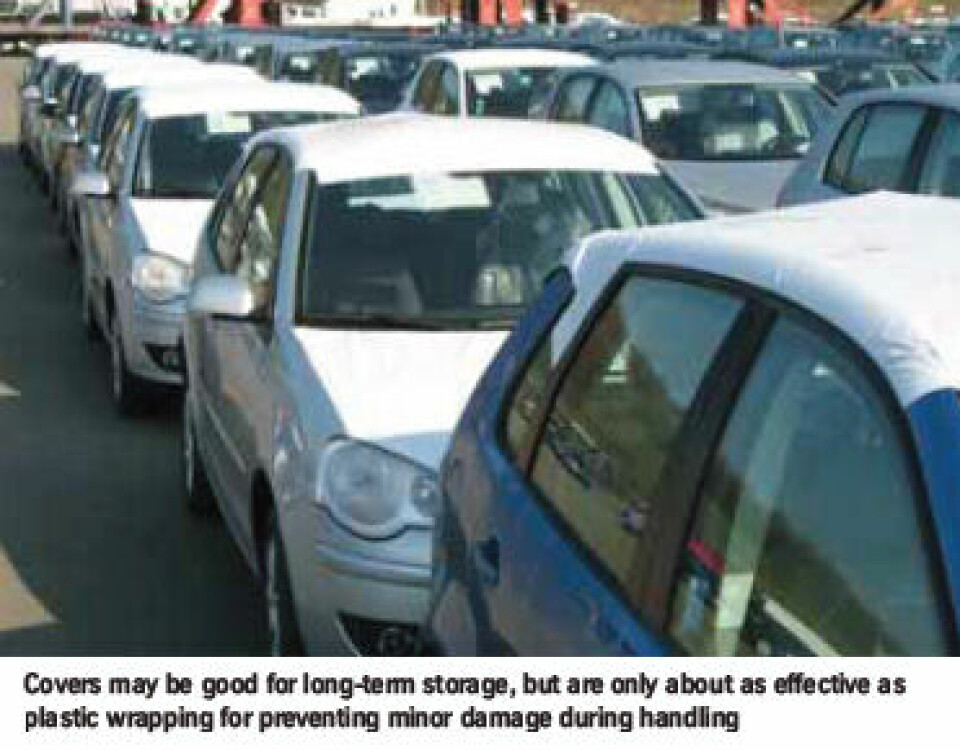
“In consideration of the financial and environmental cost, protection measures must be carefully chosen and positioned in order to be effective. [However], even with the use of covers, tape, coatings and wax, damage to finished vehicles in transit will still occur,” says Imiola. In practice, each model is often protected with a specific combination of products. For example, American Honda uses foam blocks, protective tape and plastic wrap on North American-built vehicles and a protective spray and foam blocks on imported vehicles.
“There is always cost pressure to use protective products economically. This requires consideration of the cost of the product, the cost to install and remove the product and a measurement of the reduction in damage we realise from using the product. Additionally, the environmental impact from disposing of the product is increasingly important,” says Cooper.
“Our internal studies have determined that some products such as foam blocks have been only marginally effective for us and may be reduced in the future,” he adds. In terms of how the use of each different product might affect insurance premiums, Van Der Werff explains that Tokio Marine Services does not request its insured clients to apply protective measures–preferring instead to leave this decision to individual OEMs.
“Normal insurers would try to exclude damages that are repetitive or want to apply a high deductible. Tokio Marine will handle such reoccurring losses in order to collect loss data, and together with the insured OEM start to prevent such losses,” he says.
Handle with care
In spite of the fact that protection products are used widely by carmakers, the reality is that improper handling or transport can still result in damage to vehicles. Some observers believe that the liberal use of visible protection products may in some instances even be counter-productive. “I believe that the more you try to protect the vehicles the people handling vehicles will behave less carefully,” says Van Der Werff.
“The only way [to further reduce damage] would be to optimise the trailers and the handling processes, I don’t see another solution,” adds Rössler. For American Honda’s Duvall, loading trials to establish clearances within conveyances such as railcars and on trucks are important to determine where protective products could be applied to decrease the likelihood of damage. “Otherwise, emphasis on proper inspection and handling techniques will provide the greatest opportunity to reduce damage during transit,” he says.
When reviewing with a vendor as to why they are liable for a damage claim, the two most common reasons quoted to American Honda are ‘missed on inspection’ and ‘improper handling during loading or unloading.’ In this light, the proper training and retraining of truck drivers, yard crews and rail loading and unloading crews is a critical aspect of the transport process.
“The people that touch the car have an opportunity to discover a problem during the inspection process and also to ensure that no damage occurs as a result of their handling. That said, time pressure and just being in a hurry are factors frequently cited when a poor inspection misses a problem or damage is incurred during handling,” says Cooper.
“[Logistics operators should] create awareness amongst all their workers of the high value of a new car and the impact of damage to the quality of the car make,” says Van Der Werff. Imiola agrees that logistics operators, in cooperation with OEMs, are best placed to prevent damage by adopting excellent handling processes and strict controls on the proper handling of all vehicles. “At the same time this is the most cost-effective way to achieve damage reduction,” he says.
For both improvements to handling or specific protective product use, the employment of these measures can only be targeted, he says, through strong analysis and monitoring of damage. To achieve this level of effectiveness logistics providers and OEMs are likely to need damage analysis that can ‘drill down’ into the details relevant to them, such as that provided by UniCar’s own survey data system.
“This level of analysis helps determine which protection is suited for each vehicle depending on its specific logistics path; protecting damage risk positions for loading on a type of railcar, for a method of lashing or a storage site,” says Imiola. “Such targeted protection and handling control is the future for cost-effective damage prevention and damage reduction,” he adds.
Meanwhile, at sea, Butler’s view is that logistics providers are already constantly seeking to improve their systems to minimise any cargo damage–and work with ship builders and ramp providers accordingly.
“When you visit a new Pure Car/Truck Carrier (PCTC) and compare it to one from, say, 20 years ago, the design is significantly improved, in particular by removing any obstacles, such as pillars, that pose a risk to vehicles,” Imiola says.
New innovation gaining traction
In an effort to reduce damage caused during seaborne transport, anti-skid surfacing has also become increasingly popular and is now used widely by many carriers. One popular innovation, the RS Clare Bimagrip anti-skid surfacing system, was originally developed more than 20 years ago and consists of a special polyurethane adhesive incorporating a highly abrasion-resistant aggregate dressing. It was initially aimed at the traditional carriageway anti-skid surfacing market because it greatly increases the traction of vehicles travelling over it, especially in wet weather conditions, thus reducing skid-related accidents.
Following further successful applications in maritime and port settings, the company became increasingly aware of the potential benefits of employing the system as a low-profile skid-resistant surface on the steel ramps and decks of ro-ro vessels–contributing to the safer and more efficient loading and discharging of vehicles in wet and dry conditions. “In the early 1990s we carried out numerous trials on ship’s ramps. Wallenius Lines of Sweden was particularly impressed with the performance of the product and the way the increased traction allowed for the faster, safer and smoother loading and unloading of cars and freight,” explains Butler. “As a consequence when they placed an order for four new build PCTCs with DSME of South Korea they insisted that Bimagrip be applied instead of the conventional welded metal systems,” he adds.
Now DSME and Wallenius, as well as Ray Car Carriers and Grimaldi Lines, use the product as their standard high-friction surfacing. Hoegh Autoliners and AP Moller have also adopted the system for all of their future new builds. “Today, either through direct ownership or chartering, every major PCTC operator now uses Bimagrip,” says Butler. “As a consequence the same applies to all OEMs, and a comment I have received via the logistics providers is that because the Bimagrip system is of a low profile there is none of the ‘bouncing’ which occurs when vehicles are loaded over welded square bars and this has to benefit the vehicles,” he adds.
In recent years Bimagrip has been applied onto new build PCTCs in South Korea, Japan, Vietnam, China, the Philippines, Poland and Croatia–a total of in excess of 120 such vessels have been treated as well as numerous ro-ro and ro-pax ships. “We are now looking to offer the Bimagrip system to logistics providers for application over existing welded metal systems,” says Butler.
“By utilising vacuum blasting equipment this is achievable without the need to remove the existing square bars which can be extremely time consuming and therefore expensive. Recent jobs carried out are receiving very favourable reviews, including, for example, K-Line,” he adds.
Looking ahead
So, what new damage protection products and innovations would companies like to see developed in the coming years? For Cooper, the ongoing transition from chain tie-downs to straps on trucks is an important step. “While we do not mandate strap or ‘soft’ tie-downs by our carriers, we see this equipment as being more vehicle-friendly and contributing to less damage overall,” he says. For Rössler, the most effective way of protecting cars is simple–produce cars close to where they are needed. “From a German producer to a German end-user, a car is manipulated and transported a maximum of three times. The same Germany-produced car will be manipulated more than 10 times while being transported to China or the USA,” he explains.
In summary, the damage caused to finished vehicles during their long journey between manufacturing facility and showroom remains a real and pressing concern for carmakers. Although an extensive range of new and existing damage protection products continue to be employed, the above analysis reveals that the situation is unlikely to improve significantly unless more work is done to improve handling during transit–particularly while loading and unloading at ports, freight terminals and other major hubs. In the long run, the effective minimisation of transport damage is likely to be achieved through a sensible combination of damage-protection products, improved handling techniques and ongoing innovation in the logistics sector. In doing so, OEMs, logistics service providers and transport operators would be well advised to adopt a collaborative approach to keep chipping away at the problem and ensure that damage in transit is kept to a minimum.