Skoda: Simply Clever logistics
Jirí Cee, head of Skoda brand logistics, discusses the processes in the OEM's Czech homeland that are setting a standard for further growth around the world
Mladá Boleslav, 70km north-east of Prague, is the town of Skoda. It has been the carmaker’s home since Laurin and Klement built their first car there in 1905. You’re unlikely to see much else being driven on the roads, except for the odd rebellious Volkswagen – which, given the company’s group owner, perhaps isn’t so outlandish.
In this story...
After adding component and assembly plants in Vrchlabí, another 75km away, and Kvasiny, 120km to the east, by the 1930s, this region of what was then Czechoslovakia formed Skoda’s footprint for the rest of the century, by the end of which Volkswagen had acquired it. Skoda has since become an international manufacturing force, building more than 1m cars last year at its own and Volkswagen group plants in the Czech Republic, China, Slovakia, Russia and India, as well as at several knockdown plants.
However, Mladá Boleslav is still very much at the heart of Skoda’s global production and supply chain. Today, Fabia, Rapid and Octavia models are manufactured here, alongside on-site production of 3-cylinder engines, the supercharged TSI engines for Skoda and Volkswagen cars, MQ 100 and MQ 200 gearboxes, axles and other components. The plant builds 2,000-2,400 vehicles a day. It also packs and ships thousands of containers of parts to international production sites, including semi- and complete-knockdown kits (SKD/CKD).
The Mladá Boleslav plant and its surrounding facilities are also a showcase centre for logistics. Impressive levels of parts handling and packaging innovations can be found, including for pallet sorting, conveyor feeds, automated guided vehicles (AGVs) and smart tablets. An array of ‘pick-by’ systems have been implemented across supermarkets and parts centres, while ergonomic improvements have been studied across parts handling areas, according to Jiří Cee, head of Skoda brand logistics.
“Overall improvements in ergonomics also have a positive effect on productivity. As an example, we can mention pick-by systems used for SKD vehicle sequencing, the deployment of AGVs, or ergonomic vacuum-operated Vacu-Cobra manipulators, which make it easier to handle cardboard packaging,” Cee explains.
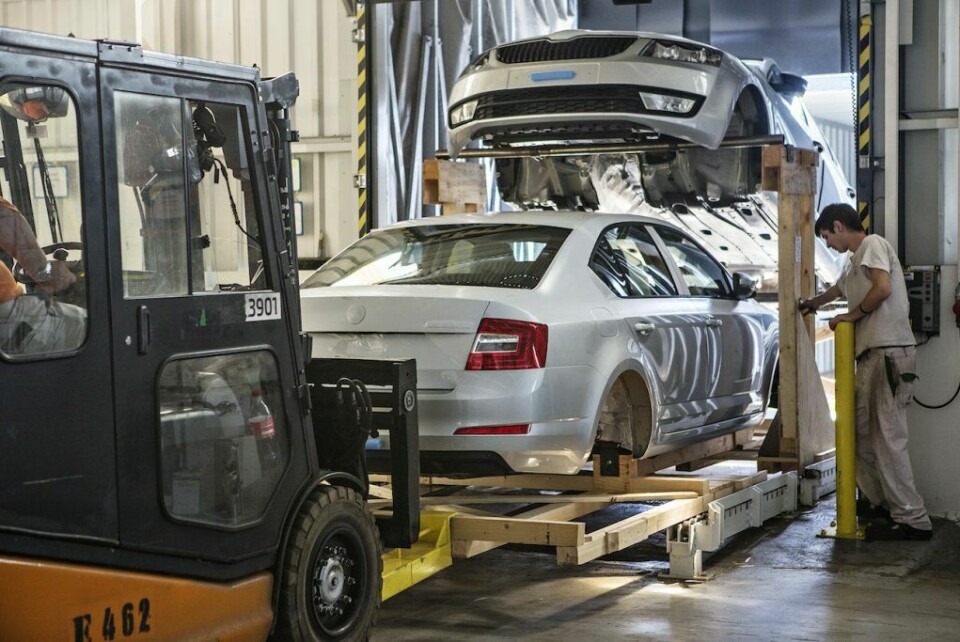
Brand logistics is an important function at Skoda, with around 1,250 logistics employees in plants, warehouses, knockdown centres and headquarters. Cee is in his 15th year as head of this organisation, and his fourth decade with the company, most of it spent in logistics and production processes. “Logistics is a vigorous discipline and companies, as well as employees, are taking a growing interest in it. You can never get bored in this field or think that you have hit a plateau, and even after 15 years on the job I still learn something new every day,” he says.
Skoda’s logistics are based on its ‘Simply Clever’ principle, with systems aimed at simplifying processes, saving resources and reducing costs. As part of the Volkswagen Group, this includes sharing ideas, standards and best practices across other brands. “It is absolutely imperative that the systems and processes used by the individual brands of the Volkswagen Group are standardised if we are to cooperate and work alongside each other,” Cee says.
Cee’s responsibilities include management of inbound logistics across Skoda plants and knockdown centres, as well as in-plant logistics management. Shared facilities and part flows are managed together with Volkswagen Group Logistics. For outbound logistics, the group provides services and synergies accounting for about 70% of transported vehicle volume, while Skoda exclusively sources and manages the rest of distribution, especially in eastern Europe.
Mapping a complex supply chain
For its Czech plants, Skoda’s high volume suppliers are located 5-10km away, and many are within a 25km radius. The only on-site supplier at Mladá Boleslav is one of the carmaker’s two seat suppliers; the seats move on a ‘ski-lift’ that travels over a bridge from the supplier and onto the Fabia line. The other seat supplier is located 5km away. Both ship in sequence, and the products are combined within the Skoda plant.
“Our company has an exclusive service provider for securing part deliveries in a JIS (just-in-sequence) concept. Other sequences and minor pre-assembly operations are carried out in-house,” Cee says.
However, in terms of numbers, the largest percentage of suppliers are based in Germany at 44%, compared to 20% from the Czech Republic. While the company is trying to encourage local supplier operations, many are located further afield both in Europe and abroad (2% and rising are from China, for example).
"The current need for consolidating parts by using crossdocking centres is growing rapidly. We use synergies with VW Group volumes and capacities to maximise the available financial benefits" – Jirí Cee, Skoda Auto
This distance requires careful management and systems monitoring. Like some of its Volkswagen Group peers, Skoda uses some long-distance, just-in-sequence suppliers (the ‘pearl chain’ process, read more here), including cable harnesses for the Octavia from Romania, 970km away. “The whole production and logistics chain, from the harness production order to the delivery for the fitting cycle on the Skoda assembly line, is controlled and based on the exact specification of a vehicle assigned to a vehicle identification number,” Cee explains.
Although Skoda successfully manages a large and diverse group of suppliers, Cee admits that he wants Skoda’s logistics to improve. “We wish to optimise and lower the cost of negative logistics aspects, such as an increase in the number of suppliers, longer distances from individual suppliers, the growing complexity of parts, and unfavourable macroeconomic conditions affecting some countries.”
Skoda’s logistics network is based on the volume of transported goods, part complexities and supplier structures. It uses direct deliveries from individual suppliers, and also milkruns and deliveries through centralised collection locations for smaller volume deliveries, including combining with other group brands. “The current need for consolidating parts by using crossdocking centres is growing rapidly. We use synergies with VW Group volumes and capacities to maximise the available financial benefits,” Cee says.
Increasing complexity in the supply chain is an issue facing most OEMs, and Skoda is no exception; as an example, it now has more than 60 types of steering wheels. In total, Skoda currently works with more than 1,300 suppliers. This variety puts even more emphasis on the company’s logistics processes.
“The current trend for lean logistics requires suppliers to adopt new approaches for meeting the given rules and the demands of supplier processes,” Cee says. “Production material deliveries must unconditionally meet a given term and the required volume for each part delivery. Deliveries must be executed faultlessly, which also applies to the attached documentation and the agreed quality.
“The supplier must have a functioning, flexible and reliable internal logistics system, and functional IT systems are also essential,” he adds.
Skoda brand logistics constantly assesses its suppliers and providers on the punctuality, regularity, and organisation of deliveries, with its executives often getting directly involved in operations with some companies. The average punctuality for meeting delivery time windows is currently 91.5%, while the accuracy of these deliveries has reached 99.9%. Meanwhile, the average loading/unloading time at a single warehouse location is 26 minutes, according to Cee.
Innovation and technology play an important role in these processes. A staggering 1,900 trucks per day come in and out of Skoda’s Czech plants alone. To improve arrival and dock processes, Jiří Cee explains that the OEM is currently in the pilot phase of a ‘Quick Check-In’ project, which uses mobile technology and geo-fencing to control both check-in and the location of trucks – a system and application that has also been trialled and put in place at a number of other Volkswagen and Audi plants in Europe.
“We expect this project to increase the accuracy of our forecast of the check-in times of trucks arriving at control stations, and to improve the gate traffic and routes of trucks on the way to their destinations without the need to stop them at the gates,” he says.

Technological innovation and automation is at the centre of Skoda’s logistics development. Examples can be found in the material flow from the warehouse connecting the Octavia and Rapid production line, as well as the line-feed processes from supermarkets to assembly line. The 15,500 sq.m parts warehouse, which has 14-metre high shelves and receives 9,000 pallets every day, connects to the assembly hall via an automatic conveyor system that locates and transports 1 x 1.25-metre pallets. The conveyor system is fully automatic, and transports one pallet every 6-10 seconds.
Pallets with sequenced parts are moved by trolley directly to their point of consumption on the production line. Parts that cannot be stored directly on the line are taken to the central supermarket for further sorting. From the supermarket, parts move to their place on the line by trolleys or by AGVs following magnetic strips, with no forklifts being used. There are more than 90 AGVs in use in the production areas (with plans to increase this to 160 by 2017), guided by a control system based on the plant’s cycle times.
According to Cee, the control system has helped eliminate collisions, even with an expanded AGV fleet; it has also helped Skoda navigate and manage traffic flows in the assembly area and parts supermarkets, as well as to reduce inventory at the line-side.
Skoda is also using automation to transfer sequence pallets at the assembly line. “Door trims are transported to the production line by an AGV. This special train arrives at the production line with a vacant position and uses an automatic mechanism to load an empty pallet from the line-side and replaces it with a full sequence pallet,” Cee explains.
Other automation possibilities are being considered where they are applicable for economic efficiency and “common sense”, says Cee, indicating that some processes are just better handled manually. However, he is interested in Skoda being a leader in innovation; the carmaker is even considering the potential of using drones in its warehouse in the near future, with pilot projects lined up for deployment.
Skoda has also looked to improved parts picking processes in its supermarkets. Currently, the sequence printer prints out orders for operators to prepare parts in sequence following a one-minute cycle time. Skoda has begun to replace these printers with tablets. “Thanks to the deployment of tablets, we can increase the certainty in the preparation phase and also work towards our goal in the area of green logistics,” Cee says.
Skoda also deploys a number of ‘pick-by’ systems, including a ‘universal light frame’ in combination with trays for pick-by-light. The operator scans the order sheet, and the information appears on the light frame, telling them where to find parts, the number of parts required, and the position of the parts in the trolley. If the wrong box is scanned, it will not let the operator continue.
For Skoda’s pick-by-voice system, the operator instead wears a headset and scans the sheet with a wearable device. Finally, in the Fabia production hall, which has several supermarkets, Skoda uses a pick-by-point system: when the sheet is scanned, an arrow appears in front of the parts required.
While operators can still pick the wrong parts, there are now only a few instances per month when an incorrect part makes it to the assembly line.

As Skoda has expanded across Europe and globally, it has become a significant exporter of SKD and CKD to markets including India, China, Russia, Ukraine and Kazakhstan. The carmaker runs an important packing centre for this material at Mladá Boleslav.
Operations in the CKD and packaging centre are country-dependent. For Russia, the parts are ordered for a certain week, with the CKD centre acting as a crossdock on a pull principle. For China the parts are repacked from their original packaging into one-way packaging and sent on a pull principle. For Kazakhstan and Ukraine, SKD kits are shipped.
Skoda is looking to improve its CKD cubic utilisation in trucks and containers, as well as ergonomics in its packing areas. To make the best of space in kits, Skoda fills the car body with boxes, and to protect the body, there’s a prescribed sequence for the box loading. Once the car bodies are filled, Skoda uses horizontal or vertical one-time interlocking racks. Four CKD car bodies can fit into a container – by using both the horizontal and vertical racks this number has been improved from an initial three. The cycle time for Skoda’s CKD kits is 34 minutes.
Transport modes for CKDs are mixed. For Russia, where Skoda sends kits to the Volkswagen Group plant in Kaluga and the GAZ plant in Nizhny Novgorod (where Skoda models are assembled on contract), it sends shipments by rail, and uses returnable packaging.
When shipping CKDs to India, the kits travel 60-70km by road to the nearest container transhipment point, and are there put on a train and moved to Bremerhaven, before heading to Mumbai on a Maersk ship. The whole process takes 6-8 weeks from packaging at the Mladá Boleslav plant to arriving at the India plant. Part quality is particularly critical; the CKDs are not shipped with spare parts, so if a part is damaged or incorrect, it takes another 6-8 weeks to replace.
Keeping it green
The Volkswagen Group has targeted a 25% reduction in CO2 levels by 2018, compared to 2010 figures; in response, Skoda has made many changes to its logistics. For intra-plant activity, the OEM is now using a pilot truck that uses compressed natural gas (CNG), and it is running two CNG trucks within the plant. Cee says that it is a green as well as cost priority that Skoda maximises truck loading; the utilisation rate on direct routes is currently at 90.3%. The company has further increased its use of returnable packaging.
Rail is used where possible instead of road, and Skoda has joined other group brands, like Audi, in using a ‘green’ train that runs on electricity. In some plants, Skoda has tried to replace paper sheets with eSheets, which have a battery life of around five years. While they’re not used in Mladá Boleslav, there are around 60 such devices in the Vrchlabí plant.
As the pressure mounts to reduce environmental impacts while lowering costs and maintaining quality, Cee wants to increase standard systems and equipment in the supply chain, both across brand plants and the wider Volkswagen Group. According to Cee, Skoda will improve its IT by moving towards global and group-wide solutions, transitioning to a unified interface in SAP, as well as pursuing new technologies.
Competition is tough and getting tougher, both in the segment for quality affordable cars in Europe, and in fast changing overseas markets critical to the company’s strategy. Jiří Cee believes that logistics has a critical role to play in keeping Skoda competitive in the game – indeed, its logistics have been recognised at a European level for their innovation (see box below). He is confident this will help the brand win further in the next phase of its globalisation. While much of Skoda’s growth may well come in places like China or India, the foundation for logistics systems and standards starts right where the company began at Mladá Boleslav.
Skoda’s plant and CKD logistics have been recognised both within the Volkswagen Group and the wider logistics community. Last year, Skoda won the ‘European Gold Medal in Logistics and Supply Chain’ competition, and the award for ‘Logistics Project of the Year in the Czech Republic.’
In particular, the awards recognised four critical pillars that form the heart of Skoda’s logistics strategy, according to Jiří Cee (left). The first area deals with process optimisation by applying automation, including setting up a semi-automated central warehouse at Mladá Boleslav – an area of 15,500 sq.m with a fully automatic conveyor system with a length of 60 metres that automatically pairs pallets and undercarriages.
Another strategy has been the extensive use of ‘pick-by’ systems in supermarkets and parts centres, including pick-by-point, pick-by-frame and pick-by-box technology.
Other areas include intelligent transport concepts for internal logistics, including those for moving and storing parts at the assembly line. Finally, the impact of logistics on the environment has been minimised as part of Skoda’s ‘green logistics’ strategy.
“It is important to be able to rely on support from Skoda’s management, especially from the head of production and logistics, board member Mr Michael Oeljeklaus. The support we receive from company management is very important for the significant role of logistics in the overall structure of Skoda,” says Cee.
“We are continuously in the playoffs, my team is in the finals every day, and I am proud of having the opportunity to lead an experienced team of logisticians of the Skoda brand,” he adds.