Audi supply chain leaders talk global supply chain and manufacturing alignment, and the need for logistics power
At this year’s Automotive Logistics and Supply Chain Mexico conference supply chain leaders from Audi talked about the reciprocal benefits of a global strategy with a local approach.
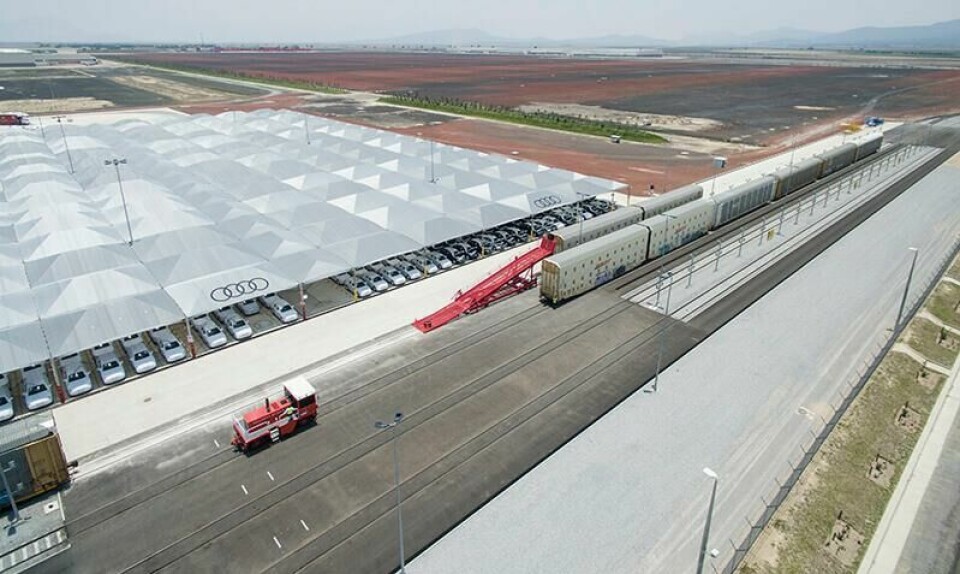
The San José Chiapa plant is a key location in Audi’s global supply chain
The transition to electric vehicle making has to move forward despite the various headline disruptions daily affecting the supply chain. Audi, like the rest of the automotive industry, is facing a completely new set of challenges across the globe. According to Dieter Braun, the carmaker’s head of supply chain those challenges demand a new supply chain strategy with faster reflexes.
Having a 100 years’ experience developing cars has until now been an advantage to Audi but that legacy of manufacturing vehicles with internal combustion engines (ICE) risks being a disadvantage in the switch to EV production without a more flexible approach. From a competitive angle, this is especially important given the speed at which China has adapted to EV production, both on home turf and in its international footprint, which now includes Mexico.
“We have discussions around whether this or that is the right path, but I will tell you one thing, in China the change to electric cars is being executed more quickly,” said Braun.
Logistics momentum
One of Audi’s guiding principles is to push the limits of innovative and sustainable production, according to Braun. That involves embracing new technologies such as automation and applying those technologies quickly, measuring the results and using them to stay competitive.
Supply chain and manufacturing have to be closely aligned and logistics operations have to produce results that move the company forward, and not end up as wasted energy. Braun said logistics was a function of its supply chain organisation that added value and it was key to the success of the company wherever it is making cars.
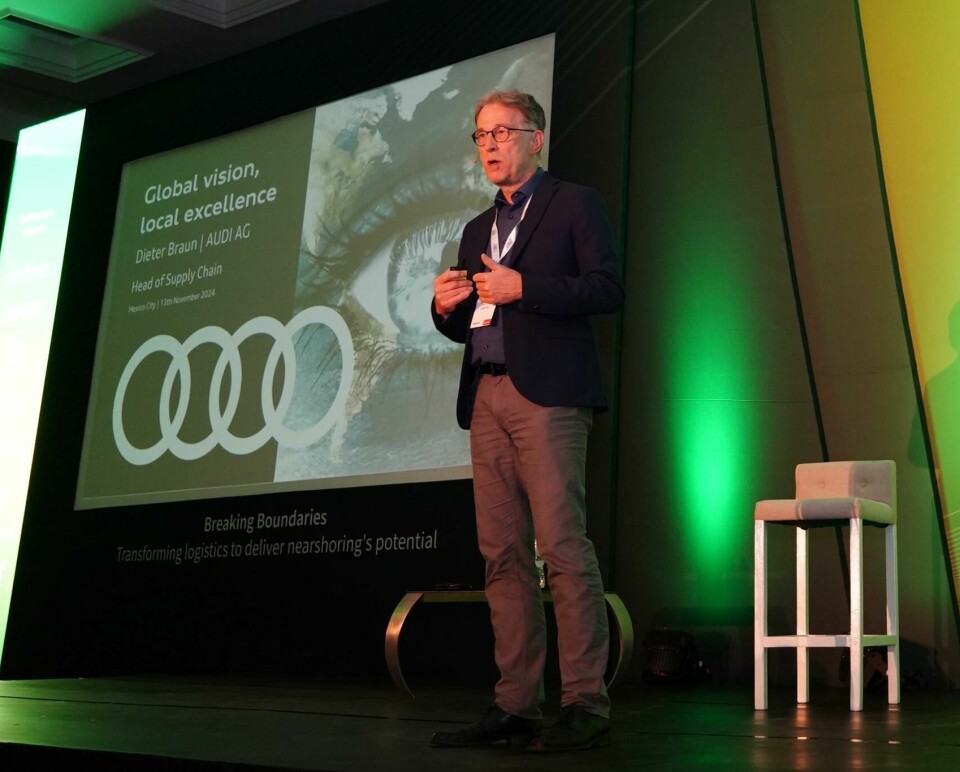
One of Audi’s guiding principles is to push the limits of innovative and sustainable production, according to Dieter Braun, head of supply chain at Audi
In Mexico that means orchestrating a lot of moving parts. Audi Mexico’s senior director of supply chain, Francisco Bravo Gomez, pointed out that Audi Mexico had a very complex supply chain operation covering everything from the inbound movement of materials from Asia, North American and Europe, through to plant logistics and manufacturing, and the shipment of the finished vehicles both domestically and to international markets. It also has responsibility for collecting all of the parts that are sourced in Mexico for shipment to Q5 production in China. On top of that Bravo’s team manages the supply of spare parts to the aftermarket from its consolidation centre at the plant in San José Chiapa.
Bravo said it is very important for the team in Mexico to understand the whole of the supply chain from global brand perspective and how it is implemented at the San José Chiapa plant – a key location in Audi’s supply chain.
That link in the global Audi supply chain is given added precedence by the fact that Mexico now has free trade agreements with more than 100 countries around the world, which was a major advantage for the Mexico operation according to Bravo.
Bravo highlighted that its operations were supported by the best qualified team, helped by a high level of education in Mexico. “The level of education that we have and the level of specialisation that we have in Mexico is at the level with the best in the world and we are also working to develop this talent,” he said.
Bravo said that Audi Mexico is also helping to define Audi’s global strategy from the local level, providing input on Mexican law and how that impacts operations, as well as informing the carmaker on the specific market conditions in North America.
I think that it’s very important that as an organisation you have the ability to distinguish trend words from real potential. That is why you have to invest in people and you have to collaborate – Dieter Braun, Audi
Potential in the process
Audi’s global strategy is guided by specific criteria, according to Braun. The first is decarbonising the order-to-delivery process and making the movement of parts more sustainable. The delivery of those parts also has to gain in efficiency with an eye on cost reduction. Related to which, is the focus on connecting logistics and manufacturing with sales, purchasing and financing. Digitalisation of processes is also a key focus, though Braun also pointed out that, when it came to AI, Audi was exercising restraint where its application did not guarantee savings. “Years ago everything was big data or something to do with e-business,” noted Braun. “I think that it’s very important that as an organisation you have the ability to distinguish trend words from real potential. That is why you have to invest in people and you have to collaborate.”
That fed into Braun’s final criteria – the importance of building a resilient team of individuals and creating more knowledge, a lesson learned through Covid pandemic.
In addition, given the global competition and the different crises affecting the global supply chain, Braun said well-functioning logistics helped secure investment and guaranteed timely delivery of vehicles to the customer, which was another important competitive advantage.
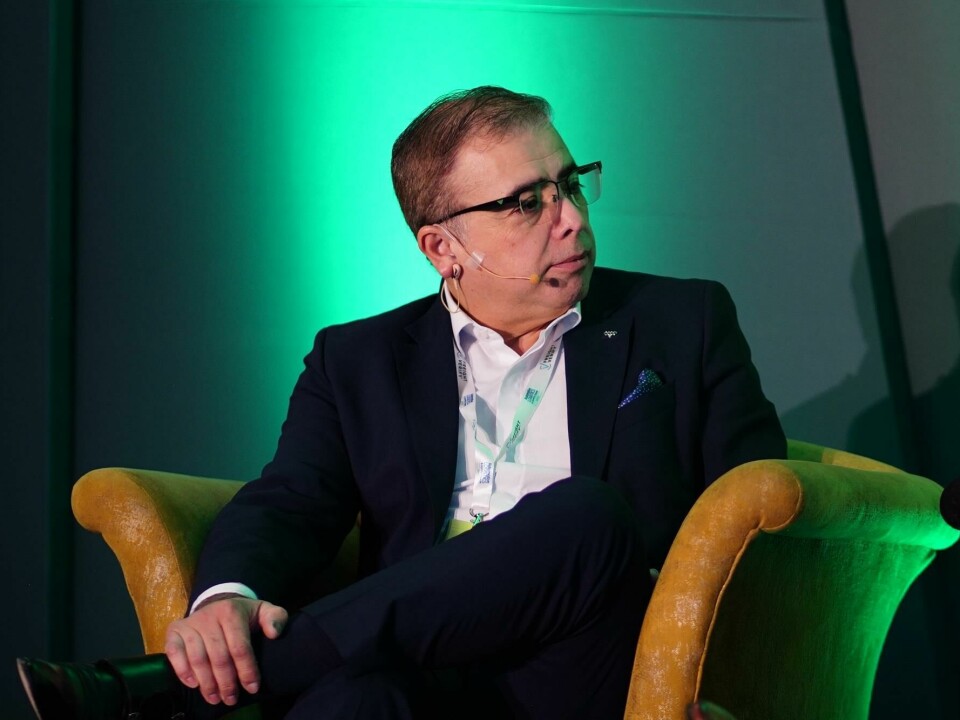
Audi Mexico’s senior director of supply chain, Francisco Bravo Gomez, highlighted that operations were supported by the best qualified team, helped by a high level of education in Mexico
As part of its comprehensive Factory360 strategy for production and logistics, Braun reiterated Audi’s guiding maxim that it is pushing the limits of innovative and sustainable production. Braun said that over the last five years a lot of new technology has come to market, such as those used in factory and warehouse automation. “We have to apply those technologies quickly in order to be competitive,” he said, adding that Audi’s supply chain strategy had to align EV manufacturing with the supply chains feeding the new materials into its factories.
For Braun measuring the implementation of the strategies developed to remain competitive in a transforming industry and identifying the results is critical to the success of the company and its transition to an EV future.
Resilience to voodoo
The supply chain of Audi Mexico is part of that overall production and logistics strategy, according to Bravo, including its product complexity and sourcing. Bravo is one of the ‘godfathers’ of the supply chain order-to-delivery strategy and oversees its application in daily operations at Audi Mexico. That includes managing the production control and programme planning for the supply chain organisation in Mexico. That enables Bravo to analyse the processes and identify where to elaborate proposals to reduce complexity in relation to certain products and in doing so reduce costs while becoming more flexible and delivering vehicles to the customer faster.
We are all voodoo dolls in supply chain logistics, receiving 200 “nails” a day in our heads, but we have to be resilient and the way to do that is to create a scenario planning and implement it together – Francisco Bravo Gomez, Audi Mexico
In terms of the sourcing strategy, Audi Mexico is providing information up the central supply chain in Ingolstadt where the localisation of certain suppliers can make Audi more competitive. That includes suppliers beyond the tier one level, down to tier two and three. With key suppliers localised Audi Mexico can plan scenarios in collaboration to react more quickly and efficiently to disruption said Bravo.
It also involves partners across the logistics and transport modes. As an example, Bravo pointed to a close collaboration with the port authority of Veracruz on the impact of weather conditions on vessel operations.
“Every time we have bad weather, we need to adjust our organisation and now we are doing the forecasting based on our historic data and what the weather behaviour could be in the next months,” said Bravo. “We try to adjust our forecasting and our operation based on that, and based also on the communication and the input we get from Veracruz.”
Adapting programme planning to disruption in Mexico is about building resilience as part of Audi’s overall global strategy, according to Bravo, and that includes not only adapting to unforeseen changes, but also developing the people it employs to be resilient enough to support the operation.
“We are all voodoo dolls in supply chain logistics, receiving 200 “nails” a day in our heads, but we have to be resilient and the way to do that is to create a scenario planning and implement it together,” he said. “Since we are all now interconnected all over the world, we do this daily with the central functions in Germany, using technology and data.”
Audi’s global teams are creating use cases and choosing together which plan to use where and which technology to apply, making the first steps, learning from it, and then spreading it out to Audi plants across the world.