Taking hail repair in hand
The random and varying nature of extreme weather damage presents OEMs, and logistics providers, with complicated and urgent repair challenges.
In late July 2013, central Europe enjoyed a prolonged period of warm weather, with several weather stations in Germany recording temperatures above 38°C on July 27th. It wasn’t to last. Already, a convective low-pressure weather system was developing off the Spanish coast over the Bay of Biscay, and it began moving over France and Benelux towards Germany.
As the weather system tracked eastwards, a series of violent thunderstorms wrought havoc in their wake. An area of France’s winemaking Côte de Beaune region saw floods and hailstone damage was estimated to have cut 2013’s Burgundy vintage by up to 4m bottles.
Worse was to come. The combination of the low-pressure weather system and the prevailing warm air masses over Germany brought about a thunderstorm supercell, moving over Bielefeld to Hanover and then to Wolfsburg – home to the Volkswagen Group – where it bombarded the ground with exceptionally large hailstones, many the size of golf balls.
Compounds at the Wolfsburg plant were badly affected, with damage estimated to be worth millions of euros. Of around 28,000 vehicles, 17,000 needed checking, which delayed shipments and left a large number of vehicles with broken windshields, dents, dings and scratches. The impact was so bad it was partly blamed for a drop in profits at the carmaker during the quarter.
Hailstorms can cause enormous damage and delay to new vehicles parked at factories, ports or storage compounds. For Volkswagen, it was not the first time it had been hit by damage on this scale: back in 2008, a hailstorm hit 30,000 vehicles parked in the open at the German port of Emden.
Such storms are not necessarily frequent; major OEMs in Europe and the US tend to report one or two incidents of mass damage a year; the frequency can be higher, or years can pass without incident. There is vulnerability in ports, but also factory yards where vehicles are uncovered. The question for carmakers is how – short of totally covered storage – can anything be done to prevent or minimise such occurrences?
Industry insiders don’t necessarily give a reassuring response. The technology for hail damage repair seems to be more efficient than the overall, end-to-end process of repairing the vehicles. The result is a finished vehicle supply chain that’s not only vulnerable to hail damage, but also to delays, disruption, unhappy customers and lost revenues.
Quick to arrive, a long time to repair
For more proof, consider the experience of an unspecified vehicle manufacturer in France, hit by that same weather system that reached Wolfsburg in July last year. As late as mid-November, Carlo Travaglini, key account manager at hail damage repair specialists BallSystem, was still on-site at the carmaker’s compound in France, dealing with the aftermath. “As much as possible, we try to repair with paintless dent repair techniques, rather than replace parts,” notes Travaglini. “But that’s not possible in the case of damage to small plastic parts, or windshields, mirrors, lights and antennae. [Getting] spare parts for these can be a bottleneck.”
The long wait for spare parts cuts right to the heart of the automotive industry’s problematic hail damage repair process. Repair specialists, whether contracted by insurers or OEMs directly, pride themselves on their ability to be on-site in 12-48 hours, cataloguing the damage, estimating repair costs and summoning the technicians who will carry out the repairs. “In today’s automotive business model, almost by definition, vehicles in a compound are either sold, or very close to being sold,” stresses Travaglini. “Our brief is usually to be on-site within 24 hours, installing equipment and assessing damage.”
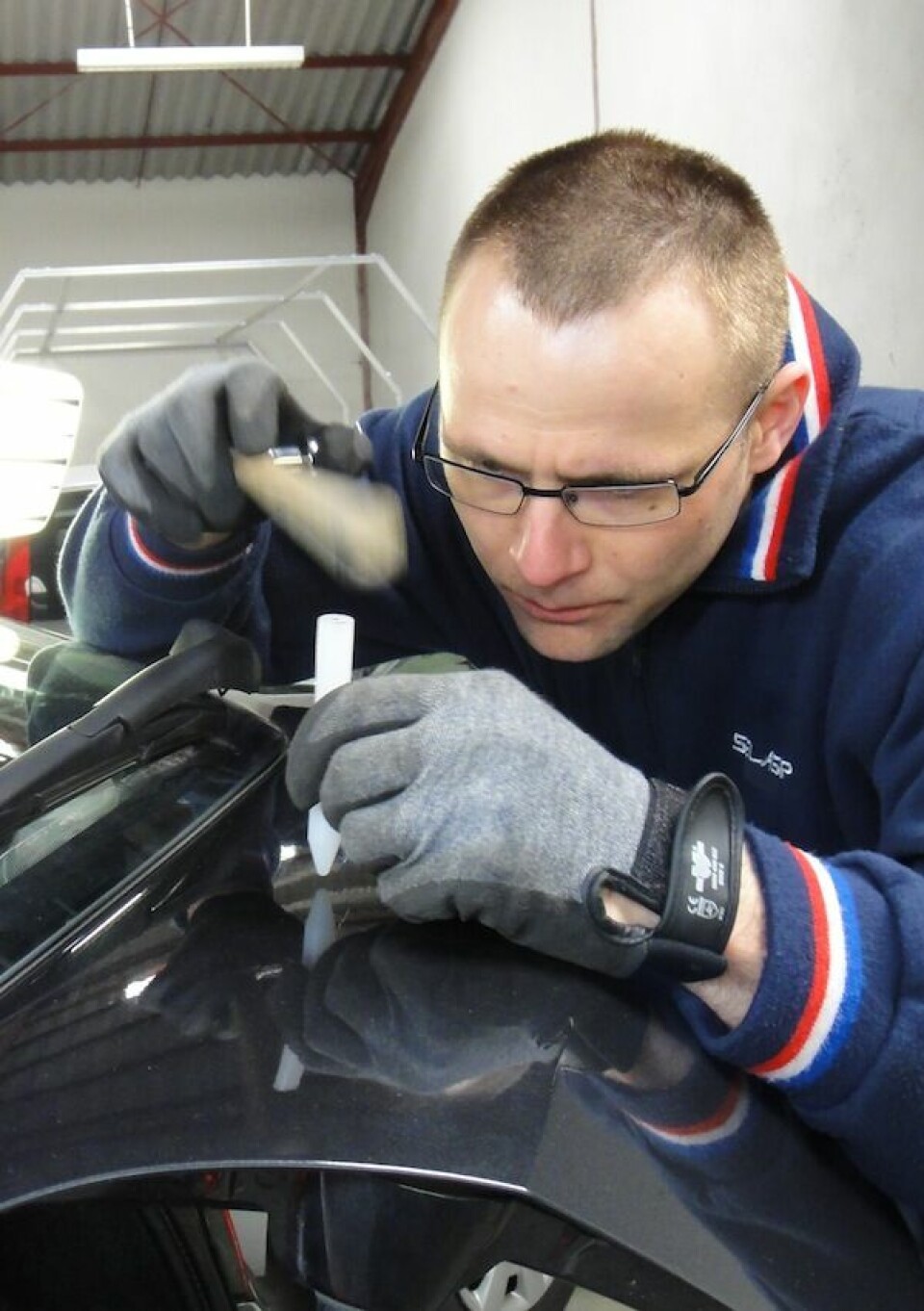
Beyond this speed of response, hail damage repair also calls for complex choreography, with paintless dent repair technicians, insurers, OEMs and logistics providers all working smoothly together to get vehicles back into the supply chain. This is all carried out in an environment that’s still an operational compound, with vehicles constantly arriving and departing.
“Selecting and gathering the right specialists together at the right time and at the right price is one challenge; balancing everyone’s interests and priorities is another,” says Willem de Lange, managing director of insurance claims specialist TES Automotive and Claims Management Service. “The manufacturer’s sales logistics and finance functions have their own priorities, as do the service providers. Terminal operators, repairers and logistics firms must work together, and the stakes are huge.”
The weatherman can’t help you
Hailstorms, by their nature, are random events. Anecdotal evidence suggests that their frequency is increasing, but firm meteorological evidence one way or the other has yet to appear. In any case, from the perspective of an individual manufacturer, the incidence is low.
Also unpredictable is the severity of the hail event. Hailstones the size of peas might cause no damage, while those the size of marbles would almost certainly cause some damage; stones the size of golf balls would cause certain damage. The duration of a hailstorm has an impact on damage levels, too; as does wind direction and wind speed. Typically, for instance, one side of a vehicle will receive more damage than another. There’s also the question of the geographic ‘footprint’ of the hailstorm to consider, and how many vehicles are parked together under that footprint.
Finally, modern vehicles themselves are arguably more susceptible to hail damage. The greater use of plastic mouldings in place of steel, points out Travaglini, achieves lighter and more fuel-efficient cars, but increases the probability that hail damage will require spare parts. In terms of the paintless dent repair process itself, notes Jim Eisenbeis, vice-president of industry relations at paintless dent repair specialists Catastrophe Solutions, today’s vehicles have both thinner and softer exterior skins, increasing the severity of any hail damage that occurs.
Roll it all together and the difficulties of creating an efficient and flexible response to hail damage incidents become more apparent. Striking at random, hailstorms can inflict damage that can range from minor to major, and impact vastly varying numbers of vehicles. In an industry which values consistency and repeatability, hail incidents are an antithesis of everything that the industry strives for.
Glovis America, the logistics subsidiary for Hyundai-Kia in the US, experienced two major incidents in 2011, impacting around 1,500 vehicles, explains Douglas Miller, manager of operations administration. During 2012, there was one major hail incident, in central Texas, damaging 1,263 vehicles. As of mid-November 2013 there had been two major losses, totalling 1,160 vehicles – both at the same Illinois location. (Apparently, ‘lightning’ strikes twice fairly often when it comes to hail, as one of Glovis’s two hail incidents in 2011 saw 701 vehicles damaged, only for some to be hit again a week later.)
At American Honda, assistant manager of automobile logistics planning Gary Cooper cites a roughly comparable level of incidents. “Hail damage is not uncommon and we probably average one to two events per year,” he notes. “But it can be years between events, or many may cluster in a given year. Our in-transit vehicles are fully insured for hail and repairs are co-ordinated through the insurance company’s chosen repair companies.”
Toyota, however, seems to experience a slightly higher level of hail damage in North America. According to Toyota Logistics Services’ national manager for supply chain quality Grant McGlynn, the carmaker’s American operations typically see hailstorms between two and four times a year. When the hail hits, he explains, Toyota works closely with its insurers, aiming to get the best service at reasonable cost.
Unpredictable repair times

The time taken to effect repairs, says McGlynn, depends on the severity of the hail event and also on the resources available from the contracted repair shops and paintless dent repair specialists. “For example, if only a few Toyota vehicles are impacted, there will be little to no delay,” he explains, “but if it’s a large hail event that impacts multiple manufacturers and thousands of vehicles, then the repair shops and specialists may be heavily utilised and there could potentially be some delay.”
Honda’s Cooper concurs. While the repair company is typically on site and beginning to organise repairs within 24 hours, the overall elapsed time before the repairs are complete is difficult to estimate. “[Straightforward repairs] are relatively swift, usually taking only a matter of days,” he says. “But larger quantities of repairs may take longer. Most delays are focused on replacing parts such as door mouldings that cannot always be repaired using standard hail repair techniques; in many cases, providing parts to the repair team is the single biggest delay in returning cars to service. For example, an event that damages 300 vehicles could see the hail damage itself repaired in a week or less, but replacing the parts could delay restoring the last of the vehicles for over a month.”
It would be a mistake, however, to underestimate the challenges involved in the actual paintless dent repair process itself. Carried out by a relatively small number of highly specialised firms, the methods involved in a specific repair vary from case to case and firm to firm, according to the technology preferences and skills of the firms involved.
Simply put, paintless dent repairs involve technicians manually ‘massaging’ the dent away, either by pulling it outwards, or pushing it from behind, using a variety of tools and techniques. Very much a craft, rather than a known sequence of steps, it calls for technicians to work away at a dent until it is gone, making it difficult to precisely predict the time required to repair an individual dent or vehicle.
Glovis’s Miller explains that the time taken to repair a vehicle depends on the severity of the hail event – the depth of the resulting dents and ‘dimples’ – and the frequency of strikes. “What we characterise as ‘light’ damage is one to three dimples per panel, and the dimples being not too deep,” he says. “Such ‘light’ damage can see a two-line paintless dent repair team achieve a rate of around 20-25 vehicles a day. ‘Moderate damage’ is three to five strikes per flat panel, but still not exceeding 1cm in depth. That’s a rate of around 15-20 vehicles a day. ‘Heavy’ damage cuts it down to 5-8 vehicles a day – that’s six, seven, eight, or more strikes per flat panel, deeper than usual, and also some strikes on vertical panels, caused by bouncing hailstones.”
Following the storms and the money
Mario Ardizzone, quality manager at paintless dent repair specialist Lever Touch, insists it is important not to overlook the training, back-office administration and technical support that stands behind the technician undertaking a repair. “From the initial washing of the damaged vehicle, to the detachment of the damaged components – either internal or external – to facilitate the repair, or the quality checks built into the repairing process, achieving the highest levels of customer satisfaction calls for a lot of activity carried out behind the scenes,” he says.
Inevitably, the starting point is a process of triage; figuring out the order in which vehicles should be repaired. “Generally, we aim to first repair those vehicles which have actually been sold, then process them in order of dispatch to the dealer or the ship,” says Jim Gerencser, president of paintless dent repair specialists Nationwide Auto Services. “Popular models create the most problems in this area, as they’re more likely to have been sold, leading to an immediate post-strike bottleneck.”
After which, the vehicles are – almost literally – in the hands of the paintless dent repair technicians assigned to work on them, who carefully remove each dent by hand, working in tent-based light tunnels so as to be sure that the vehicle’s lines are as smooth and sleek as when it was first driven off the assembly line.
However, those same technicians represent one of the main vulnerabilities of hail damage repair overall: generally self-employed independent contractors, they’re on the books of multiple repair firms and travel from hail strike to hail strike, following the storms – and the money.
"We’re not after the cheapest price – we’re after the most reliable vendor, who will deliver the right quality with the right technicians" - Tim Doonan, Tokio Marine Claims Service
“It’s an interesting dynamic in our industry: it helps to keep overheads low, but it brings other challenges in its wake,” says Catastrophe Solutions’ Eisenbeis. “There are good technicians, average ones and poor ones. The poor ones don’t work as quickly, nor do they do as good a job. If a technician can’t make enough money when working on a job, they won’t stay. Often, when a hail repair job lingers on for weeks or months, it’s because the technicians have left. As repair contracting firms, we know that if we bid too low, we’ll struggle to get technicians.”
Electronic repair processes
So what can be done to improve the overall end-to-end hail damage repair process; to make it slicker, smoother and more consistent? Industry insiders suggest the answer might be in better organising and automating the process.
“The thing that many paintless dent repair companies lack is organisation,” says Glovis America’s Miller. “They’re working in busy compounds, with vehicles shuttling everywhere and for the most part they don’t have scanners and electronic tools: it’s very manually intensive, with lots of paperwork. We want to be kept informed, with daily updates on progress. And that’s difficult.”
Finished vehicle supply chain insurer Tokio Marine Claims Service’s Norman Van Der Werff makes a similar point, stressing that the company has now mandated electronic technology. “We want them to be able to digitally update us and our clients as to progress,” he says. “As of now, that’s a requirement and we won’t work with paintless dent repair firms that can’t meet it.”
Derek Sturley, logistics loss prevention expert at Sompo Japan Nipponkoa Insurance Company, adds that automotive manufacturers themselves need to be more proactive in communicating digitally with the paintless dent repair firms working on their vehicles.
“It’s important to be able to identify which vehicles are a priority, and that has to come from the manufacturer,” he says. “Better still, digital technology should also be able to help with spare part provision, tracked back to individual vehicles – making sure that the vehicle is in the right place at the right time and with the right parts on hand.”
Staying with spare part installation, there’s arguably merit in having paintless dent repair specialist technicians concentrate on just that: paintless dent repair. It may call for more staff to be on hand, but the potential for faster repairs is very real.
“We’re somewhat unusual in that our hail repair specialists only repair hail damage,” says Nationwide Auto Service’s Gerencser. “We have other people who disassemble and reassemble, and who lower the headlining, and fill in the forms and do the administration.”
Investing in digital technology and specialist assembly and disassembly staff will, of course, add cost at the point of repair, but from an overall supply chain perspective, anything to speed the flow of vehicles to their ultimate destination actually reduces cost – as insurers and their automotive industry clients are well aware.
“Our take on this is that it’s important to use paintless dent repair firms who can manage the process well – from turning up and making the initial evaluation, to fixing the vehicles to a high standard and getting the back into the supply chain,” says Tim Doonan, senior vice-president for North America at Tokio Marine Claims Service.
“Bidding isn’t the way to go,” he adds. “You hire the lowest bidder, then have problems, such as self-employed technicians who tend to chase the storms and go for the business. We’re not after the cheapest price – we’re after the most reliable vendor, who will deliver the right quality with the right technicians: some on payroll, some self-employed, but all of them good technicians, capable of doing a good job. That’s what is necessary to minimise the number of days that vehicles are out of the logistics loop.”

Hail nets – hanging mesh over open areas to protect vehicles – spark more controversy. Most agree that hail netting needs to be kept in good condition if it is to be effective, but some doubt its efficacy when faced with major hailstorms. “I can assure you that when a hailstorm is particularly aggressive, hail will just punch a hole in the net and damage the car anyway,” says Mario Ardizzone of Lever Touch. The industry also needs to be more logical in how it deploys hail netting, urges Derek Sturley, logistics loss prevention expert at Sompo Japan Nipponkoa Insurance Company.
“Quite often we find that hail netting covers only 50% or so of a site – and not the load lanes, which contain the vehicles that are most urgently required,” he notes.
Nor are full body covers an automatic answer, says Justin Newell, manager for vehicle logistics and port operations at Porsche Cars North America. “Yes, the bags protect from hail, but they also hide other damage,” he notes. “Unless the damage in question leaves a witness mark on the bag, it’s not found until the bag is removed at the dealership. And if you don’t know where the damage occurred, you can’t claim compensation from the offending party.”
An unexpected solution could be found in France, as part of a government subsidy no less. Norman Van Der Werff, of finished vehicle supply chain insurer Tokio Marine Claims Service, points to Renault’s ambitious project to cover the roofs of the delivery and shipping centres of certain French plants with 450,000 sq.m of solar panels – an area equivalent to 63 football fields. “At a stroke, it’s a solution that offers hail protection and government-subsidised solar electricity,” he points out. But is it the way to really tame Mother Nature? We’ll see when the sun comes out again.