The cross-border crawl
With the number of vehicles and parts moving between the US and Mexico set to increase even further, there are efforts to speed up the import and export processes. Are they enough?
Freight flows between the US and Mexico have been steadily increasing, helped by strengthening economies on both sides of the border, with automotive a big driver of this. Carmakers such as Audi, BMW, Volkswagen, Kia, Honda, Mazda and Nissan have been pumping investment into plants in Mexico, announcing new or expanding operations.
Mexico is the world’s fourth largest auto exporter and was expected to overtake Brazil in 2014 to become Latin America’s largest producer. In the first ten months of 2014, Mexican production grew 8.5% compared to the same period in 2013 to 2.7m units, with exports also up 8.5% to 2.2m, most of which were destined for the US. Consultancy IHS Automotive forecasts that Mexico’s domestic new vehicle sales will also grow 28% between 2013 and 2020, to 1.37m units, making Mexico a reasonably large destination for aftermarket parts.
In this story...
- More vehicles, more parts
- Border delays
- Working on security
- Ford looks to improve
- The driver dilemma
- Streamlining bureaucracy
- Seventh
Other Mexico coverage...
Full reports from our coverage of Mexico earlier in 2014
And the following stories on finished vehicle logistics in Mexico:
Join us 27-29 January in Mexico City for Automotive Logistics Mexico
Likewise, there has been a shift in parts sourcing for North America from low-cost countries in Asia to regional locations. Aleks Kobylecki, manager of material planning and logistics for North America, international operations, parts service and logistics at Ford, says that higher costs in markets like India and China are driving parts to be sourced in Mexico and then moved across the border to the US. He adds that many OEMs are also sourcing parts globally from Mexico and that its local supply base will continue to increase.
Border crossings have risen as trade between the US and Mexico zooms ahead. Volumes moving across all modes, including road, rail and intermodal, have seen increases, with some experts worried about capacity and driver shortages. Scott Grady, senior vice-president of corporate sales solutions at logistics provider Landstar Transportation Logistics, says flows between Mexico and the US have been increasing about 10% year-on-year over the last few years.
The crossing point at Laredo, Texas accounted for around 1.9m crossings in 2013, for example, about 80% of which were by truck. Out of the total, 670,000 crossings were related to automotive. Jeff Bullard, senior vice-president, central region, at Penske Logistics, estimates that there are more than 10,000 daily over-the-road crossings in each direction, with as many as 30-40% carrying automotive material.
Frank Bateman, director of customer logistics for Ryder, said during a recent Automotive Logistics webinar that by 2020, the amount of trade moving between the US and Mexico by truck could reach $463 billion.
“The main concern is congestion and delays at the border, especially at Laredo, the main crossing point for flows into Mexico,” says Grady. “The border should be a process not an obstacle,” he adds, noting that the road crossing isn’t open 24 hours and there are often long lines each morning. Landstar has 700-800 trailers daily on the Mexican side, working closely with Mexican handlers.
The US doesn’t allow Mexican trucks and drivers to operate in-country, while it is also complicated for US rigs to enter Mexico. Therefore, Grady says the crossing can take up to eight hours and may involve eight touch points, including drop-offs, pick-ups, trailer switches, and changing highway carriers. Crossings from the US to Canada, on the other hand, typically involve just a single touch point with one truck that picks up, delivers and moves the load.
Others add that handling a US-Mexican border shipment requires a minimum of five logistics suppliers, including the US carrier, US broker, drayage company, Mexican broker and Mexican carrier.
Carmakers and logistics providers often complain that congestion causes additional costs such as demurrage, driver waiting time fees, expedited shipments, and even potential plant shutdowns. Grady adds that being located close to a suitable rail location can be a big plus. However, in general, trucks are 2-3 days faster than rail, which is important when inventories are razor-tight, he says.
Michael Silvio, director of supply chain management at Cooper Standard, notes that growth in Mexico has led to increased border traffic and a shortage of equipment. “We have also seen numerous alterations in customs laws and keeping up with changes can be challenging,” he says.
Congestion is part of managing the border and it is vital to plan for it, adds Silvio. “Once everyone is on the same page and understands it takes two hours, or even sometimes eight hours, to cross the border, then you can manage expectations.”
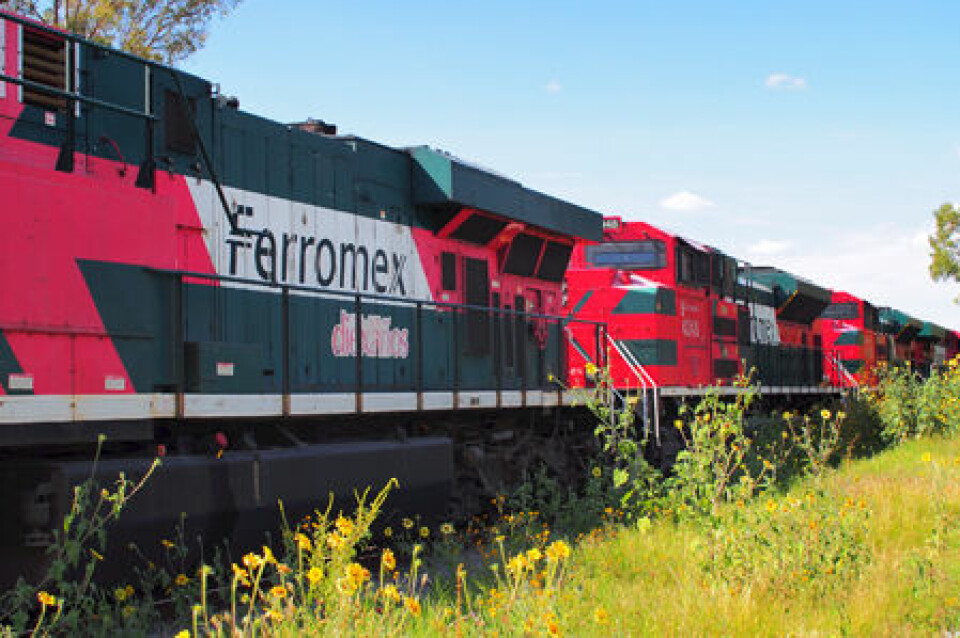
Silvio says there are a number of initiatives to fast-track shipments, including the Free and Secure Trade programme (FAST) which is for products deemed to be low-risk shipments entering into the US from Canada or Mexico. However, Silvio points out that congestion at the border can undo these good intentions. “If a driver is stuck in traffic, miles from the bridge, it really doesn’t matter that you are in the ‘FAST’ lane,” he says.
Most manufacturers and logistics providers work with a variety of carriers and trucking companies in crossing the border. Companies such as Swift Transportation and Celadon have acquired stakes in carriers like TransMex and Transportes Jaguar, while most US carriers interchange their equipment with Mexican carriers to provide services to and from the borders, Silvio adds.
Seeking secure capacity
Bill Cook, Chrysler Group’s director of worldwide logistics and customs, says the carmaker transports around 40,000 intermodal loads each year, moving all kinds of automotive parts and materials from the US into Mexico. Meanwhile, the carmaker uses rail boxcars for some 20,000 north and southbound routes, as well as some 25,000 conveyances for 53ft trucks going southwards. The aim is to move more loads to intermodal transport, says Cook.

Chrysler’s production in North America has risen to 3m units and its cross-border parts shipments have grown with it. Cook says that using rail and intermodal is usually the priority for cost and security issues, as it tends to be faster in terms of clearance. Parts such as large engines, metal stampings and other auto components move between the US and Mexico. Most of the rail and truck flows go through Laredo and some via Eagle Pass. “We need to keep a close eye on rail congestion and capacity issues,” he says.
While there have usually been enough trains, rail capacity could become an issue as the economy strengthens and more commodities, from corn to oil, compete for space. Last winter, there were some difficulties, admits Cook.
Chrysler is working on security issues such as monitoring the trains and loads, and it is also a member of various customs programmes to expedite clearance such as Customs-Trade Partnership against Terrorism (C-TPAT). Such programmes help protect the supply chain, identify security gaps, and encourage specific security measures and best practices such as cargo controls and examinations.
There is also a programme to offer training for suppliers on things like how to seal boxcars, trailers and intermodal containers, as well as to look out for security risks such as theft, hijacking or the hiding of contraband, says Cook.
He notes that it is important to keep to the schedule through estimated time of arrival updates via Chrysler’s internal systems. He adds that companies such as Chrysler work with carriers to provide a series of steps for protection. Carriers must be part of FAST, for example, and need to certify drivers and standards, which allows preferential treatment at borders. “It helps moving northbound,” he says.
Ford forges on
According to Aleks Kobylecki, Ford sends 1,650 shipments from the US into Mexico per week, with 1,025 weekly shipments of products from Mexico into the US. In the year to November 2014, Ford’s customer service division, which is responsible for service parts, had completed 8,452 cross-border shipments of aftermarket parts. Rail is usually the first choice when transporting large items such as heavy, metal objects or powertrain over long distances. Meanwhile, trucks are used for supplies that have more variations in production.
Ford’s inbound logistics team ships freight by road that is picked up by a carrier and delivered to the border in a drop lot, says Kobylecki. A second carrier within the delivery country will come and pick up that trailer. The carriers typically have an interchange agreement, so they can pull each other’s trailers to the final destination. For the longer haul moves, Ford tries to move the freight by rail or intermodal.

Roger Huff, Ford’s manager for global customs, adds that for customs and material export operations, communication is critical to identify constraints and improve transit times. Ford recently added resources to analyse trends, identify areas for improvement, develop processes and facilitate the smooth flow of goods across the border. Engaging all parties throughout the pipeline has been the first step. Suppliers, carriers, customs brokers and Ford representatives need to be clear on who the single point of contact is for escalating concerns, he says.
Ford’s customer service division uses Schneider Logistics for the aftermarket business. For parts imported and exported from Mexico, it uses NAD as a broker for declaration services. For parts imports in and out of the US, it uses Livingston Brokerage as the inbound declaration services provider and BTS as the export declaration provider.
Huff explains that Ford is training its Mexican suppliers and carriers for certification in C-TPAT and NEEC (Mexico’s version of C-TPAT) as OEMs can avoid queuing at customs when suppliers and carriers are certified. Ford’s aim is to have around 100% of suppliers and carriers certified by mid-2015 compared to about 60% currently. “If we do this, we’ll need just 12 hours of inventories rather than up to 72 hours as we can use the FAST lane,” he says.
Capacity crunch
According to carmakers and LSPs, driver shortages become more pronounced when there’s bad weather that hampers rail transport or causes delays. Also, changes in US trucking regulations mean that drivers must now work fewer hours.
Olga Salinas, Ceva Logistics’ senior vice-president of global business development for the US southern border, Mexico and Central America, confirms that there are truck and driver capacity issues, particularly for northbound traffic from Mexico. The number of US trailers going into Mexico has decreased, resulting in fewer US trailers available to load export product, which increases cost and slows transit times, she says. The truck driver shortage is pervasive, she adds.
Cooper’s Silvio says the tight availability of drivers and equipment is a concern throughout North America. The system has costly waste designed into it and having to use a carrier just to cross the border adds no value at all. “It would be great if the Mexico carrier that we use in the interior could deliver the goods to our US warehouse,” he adds.
According to Ford’s Huff, 2014 was a carriers’ market and 2015 is also likely to be so. Carriers can afford to be selective about the freight that they move, for example. Ford uses around 15 carriers, and prices have risen by 3-20% depending on the carriers and when the prior bid was completed. Although Ford tries to be a customer of choice for truckers to mitigate costs and change, sometimes the carmaker needs to hold a competitive bid, he says.
Kobylecki says that with the truck shortages, some carriers are moving towards pooling chassis. The obstacles are to rebalance the chassis among the carriers, ownership, repairs and maintenance.
Huff explains that the problems could get worse as fewer and fewer younger people choose to become truck drivers. Therefore, groups such as education institutions, government and companies need to collaborate and create a focused strategy to train the unemployed to fill such needs in the economy, he says. “It’s a serious problem industry-wide. According to the American Truckers Association, the trucking industry has a current shortage of 35,000 drivers, and the shortfall is expected to grow to 240,000 by 2020,” says Huff. “It’s a big problem.”
Penske’s Bullard agrees that Mexico has a driver shortage similar to the US, although there have been far fewer issues with drivers for border drayage. However, he is concerned about projected growth, particularly in the automotive sector, and its effect in the years ahead. Bullard says that while rates have not really been affected yet, they definitely will be in the coming years.
An accurate estimation
Silvio says one of Cooper Standard’s key improvements was to create a schedule based on the speed that it can cross the border and the estimated arrival times at the plants. Logistics providers had issues with plants wanting a single part early, so were sending a half-empty trailer and then another five hours later. Now, the plants have adjusted and improved their inventory management. Silvio adds that Cooper Standard’s partnership with logistics company Protrans has led to lower transit times, and that its savings for less-than-truckload shipments were considerable. Protrans’s processes improved visibility and reduced the risk of miss-shipments, he adds.
Landstar’s Grady adds that the current bureaucratic process needs to be streamlined and brought into an electronic format such as the barcoding, web-based and electronic paperwork used between Canada and the US. The Mexico government has made commitments to streamlining the process and the situation is starting to become more fluid, he says.
"The main concern is congestion and delays at the border, especially at Laredo, the main crossing point for flows into Mexico. The border should be a process not an obstacle" - Scott Grady, Landstar Transportation Logistics
Pressure needs to be put on the government to ensure that the congestion is reduced to minutes rather than hours, adds Grady, who suggests these improvements should be done as part of the North American Free Trade Agreement, under which the border should be tariff-free and without extra financial and physical barriers.
Salinas says Ceva is looking at ways to enhance communications with customers and vendors to improve border performance. The logistics provider holds daily communications with its US and Mexico brokers to assure that documentation is accurate and provided in a timely manner. Ceva also reviews KPIs with truck vendors to assure that milestones are met and any deviation is reported quickly. Last March, Ceva expanded its operations with new facilities in Guadalajara and Monterrey, as well as expanding existing locations in Mexico City and Queretaro.
Global ocean links
Mexico’s ports are important gateways for automotive freight coming in from Asia and Europe, as well as a smaller amount moved between the US and Mexico by container. Grady explains that ocean transport of automotive parts takes longer than road and rail transport, and is therefore a less popular mode for moving automotive material within North America.
However, seaports in Mexico have seen investments in expanded capacity and handling capabilities, which has helped to improve the import of global parts. Whereas some global material would have previously been consolidated in the US first, more companies are shipping directly to Mexico.
"It would be great if the Mexico carrier that we use in the interior could deliver the goods to our US warehouse"
- Michael Silvio, Cooper Standard Automotive
By using the west coast port of Lázaro Cardenas, for example, Penske’s Bullard says Mexico-bound freight has been skipping the delays and congestion previously experienced at US west coast ports. This has increased reliability and the confidence of customers who now realise they can get their overseas products much quicker. Mexico has also made significant infrastructure investments to transport containers from this port across Mexico.
Silvio adds that developing the seaports is important to Mexico. They need to handle larger ships and bring relief to the overwhelmed ports in the US, much like Vancouver does in Canada.
There are clearly some persistent, industry-wide issues at the border. Although drug smuggling seems to have decreased, there is always a risk, says Huff. According to Ryder’s Frank Bateman, in 2013 authorities still seized 11,945 pounds (5,400 kilos) of drugs, and $4.7m worth of products with intellectual property rights violations. There are also high rates of cargo theft and other security issues.
Driver shortages and equipment capacity continue to be a problem, while OEMs need to work with suppliers on improving participation rates in C-TPAT and NEEC and communicate the overall benefits, which would include fewer delays at the border and overall lower costs as a result.
On the whole, however, carmakers and logistics providers are confident that the Mexican and US authorities are working closely to improve the crossing process. Investment in infrastructure, slashing red tape and using more technology should streamline the process. Kobylecki points to improvements at Ford’s main border crossing in Laredo, including updated forms and software in 2014.
Silvio even imagines a day when the border authorities’ main role will be to count statistics, and when crossing times could be measured in minutes rather than hours. “It could happen soon,” he says.