Toyota part 2: A complex stock-in-trade
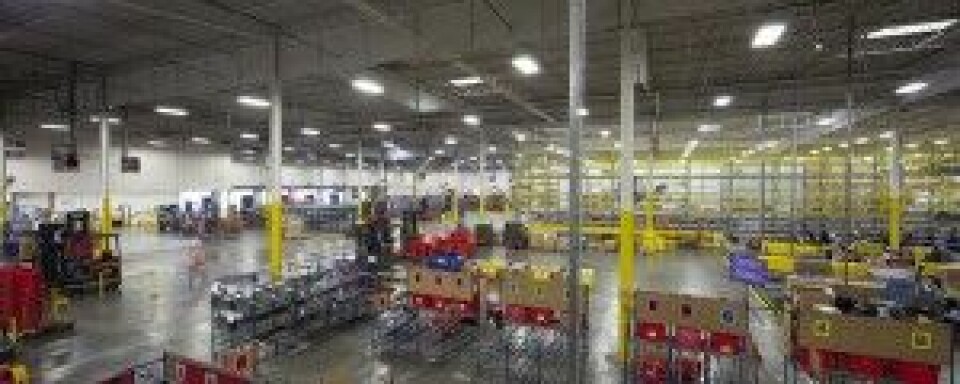
Toyota’s warehouse network and operations are strategic to maintaining the costs and efficiency of its spare parts deliveries, especially considering the scale, volume and diversity of parts and order lines that they handle
The volume moving in and out of Toyota’s huge main parts centres each day is simply dizzying: the facilities in Ontario, California and Hebron, Kentucky stock some 260,000 unique parts and ship 65,000 order lines per day between them, while the carmaker’s 13 parts distribution centres ship around 115,000 order lines each day.
In this five part series, see also...
Part 1
- Cornerstone of a strong supply chain (published March 20th)
- NAPO and becoming ‘One Toyota’ (published March 20th)
Part 3
- Engineering transport flows (published March 30th)
- In-house fleet and apps (published March 30th)
- Reverse logistics opportunities (published March 30th)
Part 4
- Understanding dealer orders (published April 7th)
Part 5
- Delivering the Toyota Way (published April 10th)
- Genchi Genbutsu at Long Beach (published April 10th)
Managing this complexity requires a high number of standard processes and systems, as well as excellent inventory visibility. This is easier said than done, not least because North American Parts Operations (NAPO) has a mix of parts distribution centre types and ownership models in North America, according to NAPO general manager Neil Swartz. There are some warehouses managed in-house, some outsourced to third party logistics providers, and some that are owned or handled by private distributors or other Toyota sales companies that are part of the North American network, but outside NAPO’s scope.
Along with the Hebron and Ontario parts centres, NAPO directly operates nine PDCs within the US. According to Swartz, keeping these major operations in-house is a priority for Toyota, especially when it comes to applying the Toyota Production System (TPS) and its processes. “A kaizen activity in a small facility may not impact the overall North American cost model, but to do so at our large parts centres has a big impact,” he says. “We really prefer to have our own associates.”
It is by that strategic reasoning that Toyota also has 3PL-run warehouses, and is about to add more. Currently, a small PDC is outsourced to a provider in Dallas, Texas for Lexus customers in the region. For Toyota and Scion vehicles, private distributor Gulf States Toyota (GST) is responsible for sales and parts service in Texas, Oklahoma, Mississippi, Louisiana and Arkansas, and so NAPO delivers parts to GST in Houston, but does not own or control operations beyond that.
The situation is somewhat similar in the south-east, where Southeast Toyota (SET) sells Toyota and Scion vehicles and parts in Alabama, Florida, Georgia and the Carolinas. Again, NAPO delivers parts to SET in Jacksonville, which has its own warehouse and distribution. However, NAPO has used SET as a quasi-3PL to manage its Lexus PDC in Jacksonville. This situation is changing, however. In the first quarter of 2016, NAPO will open two of its own warehouses for Lexus in Atlanta, Georgia and Orlando, Florida, both of which will be run by a 3PL.

“SET is a great partner, but they need space to grow and NAPO is going to take advantage of getting closer to [Lexus] customers,” says Swartz. He points to opportunities to decrease lead times and add more same-day delivery services in the region, especially out of Atlanta.
Even in the PDC operations that NAPO contracts to a 3PL, the warehouses are dedicated to Toyota. The carmaker owns the lease to avoid any risk that the provider could leave the space at short notice, while NAPO uses its own warehouse management system (WMS) and order systems. The 3PL, meanwhile, provides labour and equipment. “We went back and forth a lot on using our systems or those of providers, but in the end we believe that keeping the same system helps maintain our processes and inventory control,” says Swartz.
There are a number of other distributors in North America or NAPO’s territory: it delivers parts to depots in Toronto and Vancouver, Canada, at which points Toyota Canada Inc (TCI) has full handling and distribution responsibility; NAPO also ships to Servco, a private distributor in Hawaii, Guam, Saipan, and American Samoa.
Finally, TMS owns PDCs in Mexico City and in San Juan, Puerto Rico, which are operated by direct subsidiary companies but under close oversight by NAPO.
Despite the lack of central oversight in the distributor locations, Swartz says their collaboration with NAPO is strong. “We have great relationships and the distributors operate in a similar way to the way that we do,” he says.
"[The Ontario parts centre] was completely new for Toyota, it was not a duplicate, so we had to start from nothing and visualise everything " - Fletcher Davidson, Toyota
The network could expand further, depending on Toyota’s future strategy for production in Mexico. It is widely known that the carmaker had considered a Mexico plant in the past, and later this year it will use Mazda’s plant in Salamanca to build a new model. Were Toyota to eventually add a full-scale production site in Mexico, it could require more warehouse and distribution activities in the country.
[sam_ad id=6 codes='true']If that were to happen, Swartz says that NAPO would have responsibility for new facilities and routes.
“We already have a lot of suppliers in Mexico, and have supply routes that move into and out of Mexico,” he says. “Depending on if Toyota were to build a new plant, we could absorb new flows into our existing infrastructure or, if we need to, establish something new in that area.”
Managing space for part volume and size
With the exception of the two new PDCs planned for the south-east, Toyota has used primarily the same warehouse footprint since it opened up its facility in Mexico City in 2006, and this despite a significant rise in part numbers, sales and complexity in North America. What’s more, Toyota’s overall inventory levels are actually lower than they were a decade ago, says Swartz.
One of the most significant changes in recent years has been the growth in North American sourcing, says corporate manager Mamie Warrick. A decade ago, 65% of the service parts that NAPO distributed were from Japan (or consolidated there), with 35% from North America; today, that proportion has exactly reversed. That has impacted transport routes plus space and handling in the main part centres. The PCK in Hebron, for example, which is the primary warehouse for North American-built parts, is now running on two shifts and has frequently added overtime hours.
The PCC in Ontario, with some space freed up thanks to fewer imports from Japan, has increased its handling of North American-built parts, particularly from suppliers in Texas and Mexico, says John Ngo, assistant operations manager at the warehouse. “The Texas suppliers used to go over to PCK, but [Ontario] was able to absorb most of that because we have the capacity,” he says.

Growing vertically
Another trend that is impacting warehouse space is the growing size and dimensions of parts, particularly frame and body parts like hoods/bonnets and bumper covers, which follow the size of vehicles. To manage these changes and make sure that packing and storing processes are still appropriate, the major part centres have dedicated analysis teams who are responsible for storage and positioning parts. According to NAPCC national manager Don Thill, these teams apply their findings internally and also report them to NAPO headquarters so that they might be applied across PDCs.
Examples of such changes include storing bumper covers in the ‘car position’ to reduce the potential for damage, which has now also been applied to all of the PDCs, according to Loren Silbert, operations manager at the Los Angeles PDC. “We now store these items in the same way they would be positioned on a vehicle, which both reduces damage and allows some nesting to improve density,” Loren says. “Previously these were in U-shape boxes that took up a lot more space.”
A similar change was applied several years ago for windshields. Such parts were previously stored in corrugated boxes, for which the choice was either to use one per box, which meant poor shipping density, or to put multiple screens in a package, which increased the chance of damaging multiple parts. Today, each windshield is packed individually in transparent wrapping, which increases pack density and promotes safer handling. “Today we are treating the windshields like an egg,” says Silbert. “You know it is an egg, so you treat it like an egg and are more careful, while it also takes up much less space.”
Perhaps the most important breakthrough in organising inventory space at the warehouse has been improvement in storage racking and picking equipment, says Neil Swartz. For example, narrow-aisle storage is now standard for larger, bulk items across most warehouses, with ‘order picker’ forklifts that can reach up to 25ft (8 metres) to store, pick and pack parts. In the past, items out of reach would have required workers to use a separate piece of equipment to replenish the primary location or retrieve parts stored in what was called ‘reserves’.

“The biggest change we have made at our PDCs is to take advantage of vertical space,” says Swartz. “We had a lot of reserves because of the way the buildings were designed. But as we established the parts centres in California and Kentucky, we were able to reduce lead times, allowing us to save floor space and have more space for primary picking.”
Processes are replicated at parts distribution centres, which have also benefitted from similar applications in racking, storage and forklifts. Stocking stations are ordered by part size and speed of demand, while fast-moving, ‘bin’ parts are sorted by hand stations with minimal bending or reaching; large items rise toward the ceiling on the high rack shelving. Parts that arrive at PDCs are sorted from their returnable packaging into ‘put-away batches’ that match the storage positions for faster unloading.
“A key element of TPS is to standardise batches, which we achieve by doing sortation for both small and large parts,” says corporate manager Mike Schober.
Furthermore, Toyota has recently completed the rollout of a WMS across all its parts and distribution centres. The system includes handheld scanning of inventory to keep track of its position in storage cages, which has helped to improve shipping accuracy and visibility of all parts across the network.
“The WMS was a win,” says Don Thill. “It has really helped to have all the facilities around the country on the same management system to support processes. The integrity of our inventory has never been higher.”

NAPCC – foundation of a vision
Together with its counterpart in Kentucky, the North American Parts Center California is the ‘shock absorber’ in Toyota’s supply chain. But as well as being the receiving point for part numbers from Japan, Mexico and western US suppliers, the facility has also played a founding role in shaping NAPO’s operations and culture.
While Toyota began to set up its distribution centres decades ago, the opening of the PCC in October 1996 changed the dynamics of the operation. According to Fletcher Davidson, who designed many of NAPO’s systems and network, the PCC changed the rhythm of operations into one of daily ordering, planning and shipping.
The warehouse was also an entirely new operation, as Japan’s service parts supply chain has a different character, made up of a dense network of small distribution centres delivering to dealers several times per day. US geography required teams to develop and adapt to local conditions, says Davidson, who is today group vice-president of the product support division.
“Ontario was completely new for Toyota, it was not a duplicate, so we had to start from nothing and visualise everything,” adds Davidson. “There was a lot of training to understand the new system and daily planning processes, but also kaizen teams to make improvements.”
Several years later, in 2001, the Ontario experience allowed Toyota to replicate much of this learning in building the Kentucky parts centre, says Neil Swartz. Today, while the PCK is a larger warehouse (see data below), the PCC remains a benchmark in standards and quality for Toyota.
The decline in Japan-sourced parts has freed up some capacity at the warehouse, however the PCC still has more than 185,000 unique parts and 35,000 order lines per day. The PCC has also come to play a more important role as Toyota’s exports beyond the US increase, shipping containers not only to Canada, Mexico and Puerto Rico, but also to countries in the Middle East, Europe, and the Pacific Islands. Most exports beyond North America move from the PCC to the parts centre in Hebron for consolidation and onward shipping to global destinations in Asia, Europe and Africa.
LAPDC – new efficiency
Established in 1972, the Los Angeles Parts Distribution Center is one of the oldest in Toyota’s network and it remains the company’s largest PDC by volume of parts shipped. Located within the campus of the current TMS headquarters in Torrance, California (Los Angeles County), the LAPDC serves Toyota’s largest sales market in the country across 134 dealers in southern California, Arizona and southern Nevada. The closest dealer is literally a few minutes’ drive down the road and the furthest is more than 550 miles (880km) in Sierra Vista, Arizona.

The PDC is a good example of the efficiency and ergonomic measures which Toyota has applied across its PDCs, many of them originating in the larger part centres. The LAPDC benefited from a specific ‘rejuvenation’ project between 2009-2013, which Toyota carried out without stopping operations. For example, parts are now stored in relation to their frequency, with 80% of the most picked and handled parts kept in the so-called ‘golden zone’ shelves, which require minimal bending or reaching.
Other safety features have now been applied, including ergonomic flooring in the fast-moving parts area, where most worker movements take place. During its rejuvenation, Toyota installed ‘gravity flow racks’ at the LAPDC with rollers to help move heavier parts in totes faster, including brake pads; with this equipment, parts are loaded from the back of the rack using powered equipment, and pulled from the front to allow ‘first-in, first out’ (FIFO) access.
“Usually you see FIFO more in manufacturing plants than in warehouses, but we have done it for fast moving, heavier parts to improve safety,” says Loren Silbert.
Workers who pick these parts on foot at the front of the rack for dealer orders are also separated from powered equipment that is used on the other side. It’s a system that is not currently found across NAPO but which the Los Angeles centre applied as a storage and handling improvement during its rejuvenation project.
There is also a somewhat similar FIFO process – but using a different kind of powered equipment – for hybrid batteries, which must be carefully monitored because they have a specific shelf life.
The warehouse has made progress on hitting its quality and kaizen targets. This past financial year it has made a 14% reduction in shipping errors compared to last year, recording just one error for every 1,400 lines shipped. It has also reduced denials – when dealers are incorrectly told a part is in stock – by 15%.
Same-day service via remote drop-off has been rolled out to 68 dealers across five available routes (plus a Monday only drop-off in Las Vegas). ‘Will call’ parts pickup is available to a further 12 dealers. For some customers, parts can now be available within 3-4 hours from order to receipt.