No light at the end of the tunnel
The German rail network is in dire need of restoration but now that work is finally going ahead carmakers are facing a decade of disruption and delay to the movement of parts and finished vehicles
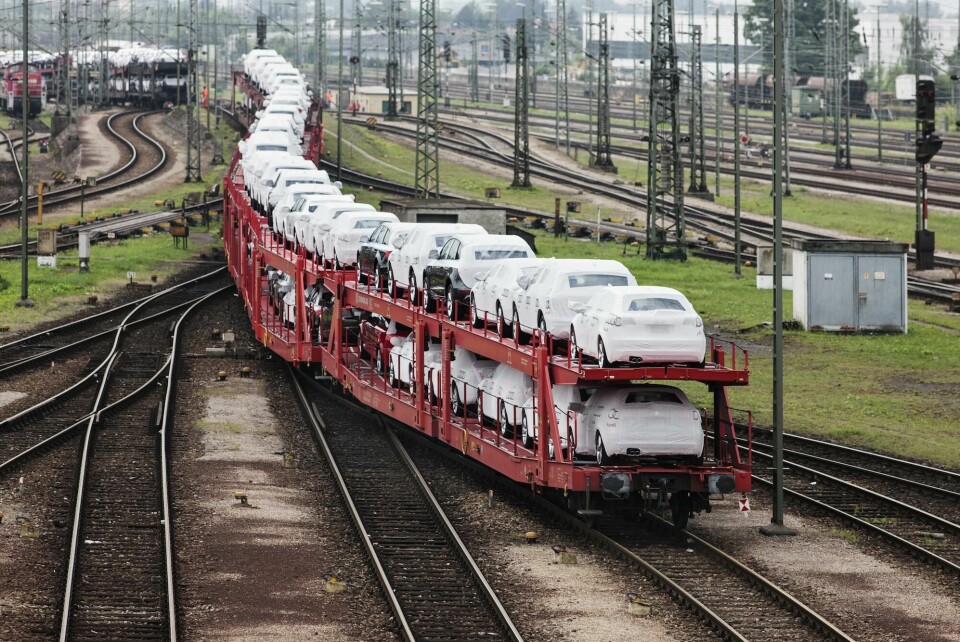
Extensive renovation work on the German rail network, which began in 2022, is disrupting the movement of freight and has reduced available capacity for goods movements by more than a third.
In 2022, Germany’s national railway company Deutsche Bahn (DB) announced a planned to upgrade 1,800km of its rail track, along with 140 bridges and 800 stations. Along with federal and regional governments in Germany, DB is investing €13.6 billion ($14.5 billion) in the work. The investment is aimed at increasing capacity and efficiency, and digitalising the network.
The efforts to improve the network also ties in with DB’s stated goal of growing the modal share of rail freight transport from 18% in the early 2020s to 25% by 2030, equivalent to around 13m fewer truck journeys per year on German roads. For the foreseeable future, however, it is having the opposite effect and that is putting additional pressure on a trucking sector struggling with its own shortage of assets and drivers.
The disruption comes at a time when carmakers are working hard to deliver cars after the disruption to supply and production caused by Covid, the consequent semiconductor shortage and the war in Ukraine. The disruption is also hampering efforts by European carmakers to shift more of their automotive parts and finished vehicle movements onto rail and thereby cut pollution.
Failure to deliver
At the same time as the network disruption, carmakers are facing a capacity shortage for finished vehicle movements because of a lack of rail wagons. Older equipment was scrapped during the Covid pandemic and has yet to be replaced. There has also been a reduction in the availability of traction for the finished vehicle sector. The pandemic also saw a reduction in labour from which the industry is still trying to recover and there have been further problems caused by the priority given to rail shipments of military equipment and energy (including coal).
According to a briefing paper on the capacity crisis in Europe issued last October by the Association of European Vehicle Logistics (ECG), a combination of these factors has resulted in a shortage of rail capacity of between 35-40% in Germany, with estimates that the shortage is equivalent to 500+ trains a day. That has made rail a much less reliable mode of transport, according to ECG.
“[The] European Commission very good at promoting use of rail [and] modal shift, eg. Shift2Rail, but [it has] almost completely failed to deliver on infrastructure and progress towards a single market for rail,” says the ECG briefing paper.
It is a dilemma that cannot be solved in the short term, as Deutsche Bahn’s CEO Richard Lutz has already stated, because investment in construction and the repair of Germany’s rail infrastructure is well overdue. The rail provider maintains it is trying everything to minimise the negative effects on transport companies and customers in passenger and freight transport, but there is no getting around the fact that the network in Germany needs to be renovated to deal with the growing demand.
Now government and industry are investing €100 billion package of construction and reconstruction that spans the next decade. As much as 50% of the track in Germany could need replacing and the overall project will involve 1,000 major construction works, closing lines for six weeks or more at a time and forcing rail companies to divert services over longer routes.
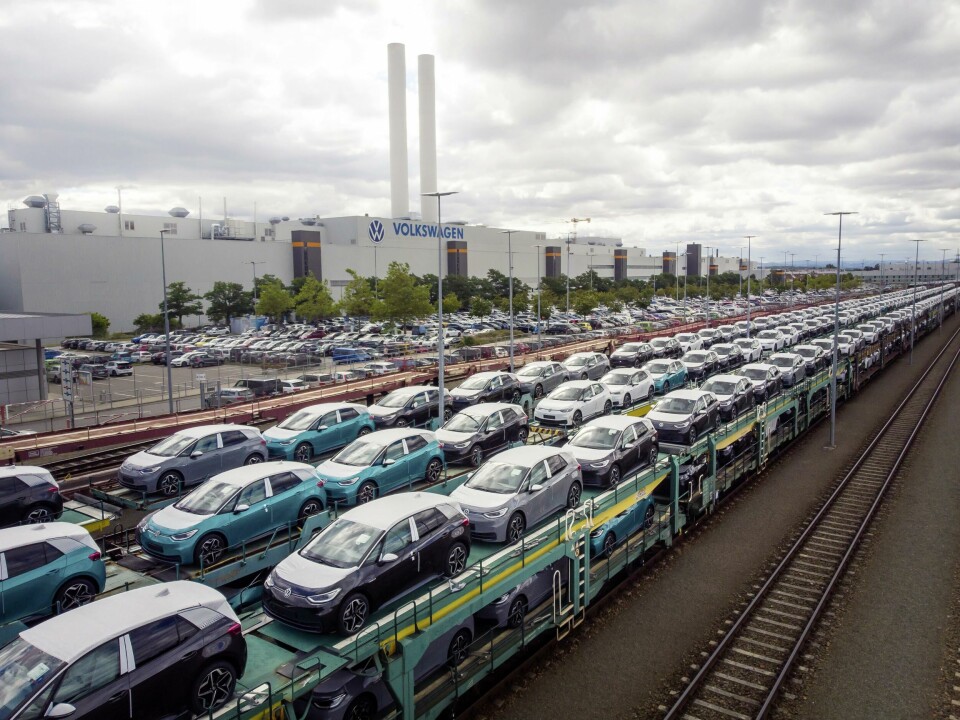
Cross-border coordination
For carmakers in Germany that is not good news for either inbound parts supply or finished vehicle moves.
“The construction and repair work in the German rail network, and the availability of locomotives and wagons occasionally leads to restrictions in the transport of vehicles and parts at Opel,” says a spokesperson for the carmaker, part of the Stellantis group of carmakers.
That is also the view at VW Group, which has seen severe restrictions on the rail network because of the construction works, a situation it recognises as being there for years to come. While the carmaker recognises the necessity for maintenance for a sturdy rail network, it says the work should be better coordinated, especially for cross-border traffic.
However, that is not the only problem. “In addition to the construction sites, there are also increasing bottlenecks for drivers of locomotives, especially at the European state railways,” says VW Group’s spokesperson. “In particular, classic single wagon transport in the finished vehicle sector, has been reduced since mid-2022.”
Fortunately, for the movement of finished vehicles, there has been enough flexible capacity built up by the private sector over the last 10 years to absorb the loss in single wagon traffic, according to VW. The carmaker is also bundling volumes in its external compounds to form block trains.
However, there is also inbound freight to consider and VW Group is just one carmaker in Europe aiming to move more inbound freight by rail, including battery materials, by rail.
Restrictions by road
At the same time that the rail network is compromised, there is a lack of capacity on the roads in Europe, making it harder to find alternative delivery options for automotive goods.
“Due to the ongoing pandemic, the geopolitical situation and the resulting absence of drivers from freight forwarders, there are delays in deliveries [by road],” says Opel.
That situation is also recognised by VW Group. “Corona[virus] and semiconductor restrictions had an impact on the logistics service providers,” says the carmaker’s spokesperson. “As a result, capacities of freight forwarders are limited as well. The truck capacity was reduced in the transport market for finished vehicles.”
As a short-term solution VW Group is chartering trucks in the network to reduce the impact of transport restrictions.
Meanwhile, Opel is offering dealers the option of collecting their vehicles from designated compounds.
“Dealers can now pick up ordered vehicles themselves from… intermediate storage facilities so that they can be
handed over to our customers in a timely manner,” said Opel’s spokesperson. “Collection by retailers is one way of improving the current delivery situation in Germany.”
Road-based transport providers need longer-term contracts and better volume forecasts to justify investment in new equipment and recruit labour, something that is now being recognised by carmakers.
Intermodal collaboration
While volatility continues on the rail network carmakers are looking at intermodal contingencies, even given the various restrictions on the road haulage of finished vehicles in Europe.
“We believe that a smart combination of rail and road is a sensible approach in which the modes of transport are used according to their respective advantages [and] we follow this approach with FBU [fully built units] and material,” says VW Group’s spokesperson. The carmaker is intent on that combination being sustainable, using rail powered by green energy on long distance routes and for shorter distances using electric trucks.
As well as new bundling concepts VW is taking a long-term approach to strengthen collaboration and partnerships with its transport providers.
While contingency options exist, the disruption and capacity constraints are affecting lead times for the delivery of vehicles. VW Group says that while it is taking all appropriate measures to avoid or reduce the impact of the disruption on its supply and distribution network, delays at the nodes or on routes in the network cannot be avoided.
“A flat rate time cannot be called, it is always dependent on the respective transport corridor and the alternative routes that are available,” says its spokesperson.
VW Group says that external to its own efforts, the ongoing construction needs to be better coordinated and that more locomotives are put into action with a proportional recruitment effort made to gain more train drivers. The carmaker also wants to see greater reliability in traction and an expansion of transshipment capacity to facilitate greater intermodal flexibility.