Turning the tide at Toyota
Christopher Ludwig meets Nancy Davies and discovers someobe unfazed by the challenges the last few years have thrown at Toyota’s finished vehicle distribution in the US, and who has big plans for streamlining the company’s already slick operations.
In April 2008 Nancy Davies became vice president of Toyota Logistics Services (TLS), the subsidiary of Toyota Motor Sales (TMS) responsible in the US for vehicle logistics, processing and accessories. At the time, she inherited a distribution network that had handled or processed a record 2.8m cars across Toyota, Lexus and Scion in the US and Canada in 2007. What followed, of course, have been three of the most tumultuous years in the company’s history.
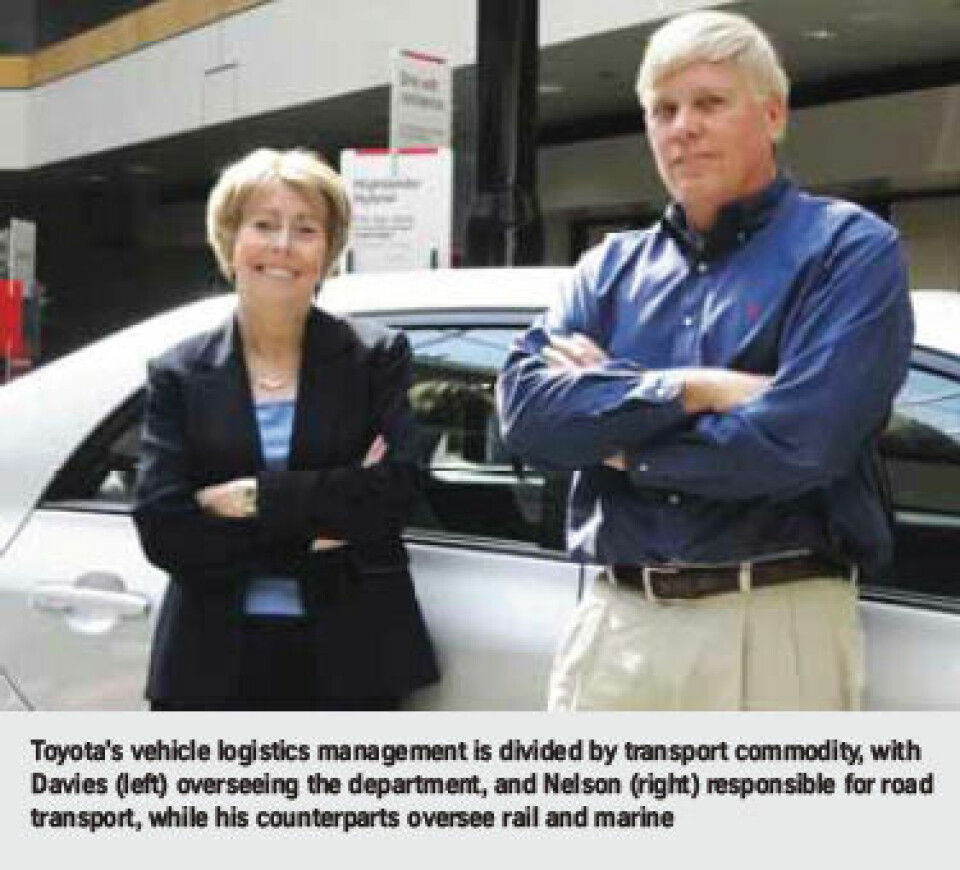
The market collapse of 2008 and 2009 wasn’t easy for any company, as the industry dropped 30%. But while Toyota outperformed some of its domestic rivals during the recession, its subsequent recall crises have caused aftershocks that held its sales back from recovery in 2010, following almost a fullmonth shutdown of sales and production during January that year to service recalled vehicles. As a result, 2010 sales of Toyota, Lexus and Scion in the US were 1.76m units, about flat with 2009 (and still about 30% off the 2007 peak), while the industry grew 10%. A strong yen also continues to take a deep bite into profits for Japanese imports, which make up about 33% of Toyota’s sales in the US.
The last few years were difficult for many reasons,” says Davies. “But, we’ve learned a lot and have increased focus.” While the recent difficulties were well outside the control of logistics, they nevertheless had a significant impact on TLS. The port and distribution network had to absorb the effects of the economic downturn, which at one point led to a large overstock of vehicles (although numbers were still lower than competitors). A network that had been primed to grow to 3m vehicles per year in the US has instead needed to adjust to handling two-thirds that amount. And for the recall, TLS had to redirect vehicles in the supply chain and carry out the necessary updates at distribution centres.
But today, from the TLS offices at Toyota’s sprawling and sunny campus in Torrance, California, both the recent pain and the subsequent hope for revival are palpable. While TMS avoided wide-scale redundancies during the downturn, on February 1st the company announced a voluntary exit package for operational-level managers in Torrance to align staff with future needs. Another recall was announced in February to address any possible remaining issues with floormats. But there are also signs that Toyota has turned a corner. Sales are growing again, forecasted to rise as the market improves and the recall recedes from headlines. In February, TMS sales were up nearly 42% year on year, the largest annual increase in 11 years. Even in 2010, the company maintained its lead as the top-selling retail brand, while Lexus has shown particularly strong growth. On the day I visit, the campus is humming with the announcement that a US government probe, conducted by the National Highway Traffic Safety Administration and NASA engineers, had found no evidence of electronic flaws in Toyota’s vehicles.
Meanwhile, Davies points to several projects that will make 2011 an important year for TLS, with ten new or updated products, including the new Prius V, Lexus CT and Scion iQ. In the autumn, Toyota will open its latest plant near Tulepo, Mississippi, where TLS is currently working with the manufacturing arm to develop the processing area.

While sales are far from prior peaks, speaking with the Toyota team reveals a company focused on improving processesboth internally and at an industry level, including reinforcing its relationship with vendors. “The industry used to operate in individual silos, and now we are trying to look more at an enterprise level to make our decisions,” says Mike Nelson, national manager, highway logistics.
He and Davies point to an initiative called ‘Total Route Management’, which actively brings together the TLS managers and logistics providers involved across transport modes for any route, to get both a full view on cost and lead time. “Total Route Management is a big effort to make sure that all of our managers are working together so that when we plan new routes or make changes, we look at the upstream and downstream impact and don’t make decisions in isolation,” says Davies.
Other improvements at the company include a supply chain initiative in which TLS is working on providing more accurate estimated arrival times (ETA) for dealers by improving the IT links and scheduling for TLS vehicle processing and accessory services. The company will also launch a new transport management and freight audit system this year with better visibility for carriers.
Doing it in-house
The central TLS team in Torrance is larger and more extensive than the vehicle logistics teams at other carmakers, owing both to Toyota’s size and the scope of its in-house responsibilities. TLS comprises two main parts: the transport of vehicles from port or plant to dealers, as well as the processing and the installation of options and accessories. Management is divided between field operations and planning, with commodity managers for different transport modes. Contracting and negotiations are handled by TLS together with Toyota’s purchasing arm. A separate team, working closely with TLS, handles distribution and sales planning.
Toyota is unique among most brands in North America in that it carries out the physical processing and accessory work with TLS staff at most of its vehicle distribution centres at ports or marshalling yards at plants. The exceptions are at the port of Benecia, California, where Toyota uses a 3PL, and the port of Jacksonville, where its distributor in the region, Southeast Toyota (SET), has its own processing company. Most carmakers either outsource this work to providers or else leave it to the dealers, with some exceptions, such as Mercedes-Benz or a Glovis subsidiary on behalf of Hyundai and Kia (see Glovis feature on p32). But Toyota stands out for its scale and level of control.
TLS also owns Toyota Transport, an in-house car haulier with a fleet of about 100 trucks. Toyota Transport delivers about 20% of the market for Toyota, primarily to the West Coast. The trucks for the fleet are leased from Penske, which carries out all maintenance work, while TLS does the planning, routing and employs the drivers.
The use of an in-house carrier gives Toyota several levels of flexibility, especially when truck capacity gets tight. The carrier also serves as a learning laboratory for Toyota’s understanding of the car haul market’s cost and operations. For example, TLS piloted the use of soft tie lashing for several years at Toyota Transport before rolling it out to carriers. Similar initiatives are currently being tested at Toyota Transport and the TLS distribution centres for the ETA project. “It is a lot easier to run pilots with your own associates than with outside vendors,” says Davies.
The US distribution network
But while it has in-house assets, TLS still relies heavily on vendors to service its network of 30 facilities including plants, ports and rail yards. Besides handling domestic distribution and export from Toyota’s US plants, it also handles US distribution from Toyota’s two plants in Canada, as well as from its plant in Baja California, Mexico.
In 2010 TLS handled the import and distribution of more than 500,000 Japanese imports (which doesn’t include imports handled by SET at Jacksonville), a slight increase from 2009 but well off the 1m imports in 2008. Overall, Toyota imports a third of the vehicles that it sells in the US from Japan (a balance that will shift when Corolla production begins at the new plant). The imports are processed through VDCs at five ports: Portland, Oregon; Benecia and Long Beach, California; Newark, New Jersey and Jacksonville, Florida.
As mentioned, SET takes vehicles from Jacksonville as one of two remaining independent distributors for Toyota and Scion in the US. SET handles five states in the southeast for sales as well as distribution, for which it has its own trucking company. The second distributor is Gulf States Toyota (GST), based in Houston and serving five states in the Gulf including Texas; GST also distributes cars with its own trucking company. In both regions TLS’s responsibility ends at the rail yard or port. The exception is Lexus, which has no independent distributors in the US, leaving TLS responsible up to the dealer, although it works with GST and SET in both cases for the transport.
TLS moved 1.2m vehicles by road in 2010. It has ten carriers under contract, with about 60-70% of the volume handled by unionised, Teamster carriers, according to Nelson. That is a proportion similar to the carrier base for General Motors, Ford and Chrysler, most of whom have told this magazine in the past that their road carriers are around 70% union carriers. Other transplants tend to use fewer union truckers. “Our union carriers do a great job for us, as do the others,” says Nelson. “While we are not making any immediate changes, we are monitoring performance and cost.” TLS employees at the ports that do the handling and processing are also union workers.
For rail, Toyota remains a formidable player, moving 1.3m vehicles this way in 2010. TLS works with all of the Class 1 railways. According to Davies, TLS models distribution from its ports and plants on a basis of moving 70% by rail, with the ratio varying by location or vehicle allocation.

Improving ETA accuracy
The ETA initiative will be an important step for TLS in 2011. Davies admits that dealers currently don’t have much faith in the arrival dates they receive from TLS, and that a survey revealed they would be satisfied with an accurate two-day window. “Improving that ETA is made up of several parts,” she says. “One is related to IT and how well we can communicate information between our manufacturing, vehicle logistics and our dealers.
“The second part is in our processing activities at our own facilities. Our VDC managers run the ports and work closely with planning, marine and accessory groups to schedule processing flow.”
The issue that Davies raises here is a familiar one to many carriers involved in moving cars as they come through port processing operations. Often, even if carriers have precise information on when a ship arrives and will be unloaded, the accessories and modification that the processor may be doing can cause variables for when the car will actually be dispatched to the final customer.
Building trust in release times for ports therefore means TLS needs the necessary accessories and allocation data in advance so that it can schedule cars through the shop based on dealer destinations. That scheduling, likewise, could be shared with carriers, allowing them to build loads and allocate their fleets with a lower risk of waiting. “As TLS continues to standardise and improve its processes and scheduling at our facilities, we are able to give trucking companies or the railroads more accurate information,” Davies says.
Of course, for the proper scheduling of vehicle processing to have a positive impact downstream, Toyota needs to count on an effective system of tracking freight and communicating potential delays or changes across its supply chain vendors. TLS has several separate IT systems for this process, including one used at the VDCs for parts ordering and scheduling, one used to determine the ETA for dealers, and finally one for its transport network.
All three systems are seeing updates, but by far the largest work, according to Davies, is being done on the transport system. For the past two years Toyota has been working on implementing a new Oracle-based system for routing and freight payments called Toyota Transportation Management System (TTMS), which is set to launch this summer. Among its important features will be its ability to get automated, accurate information to hauliers earlier.
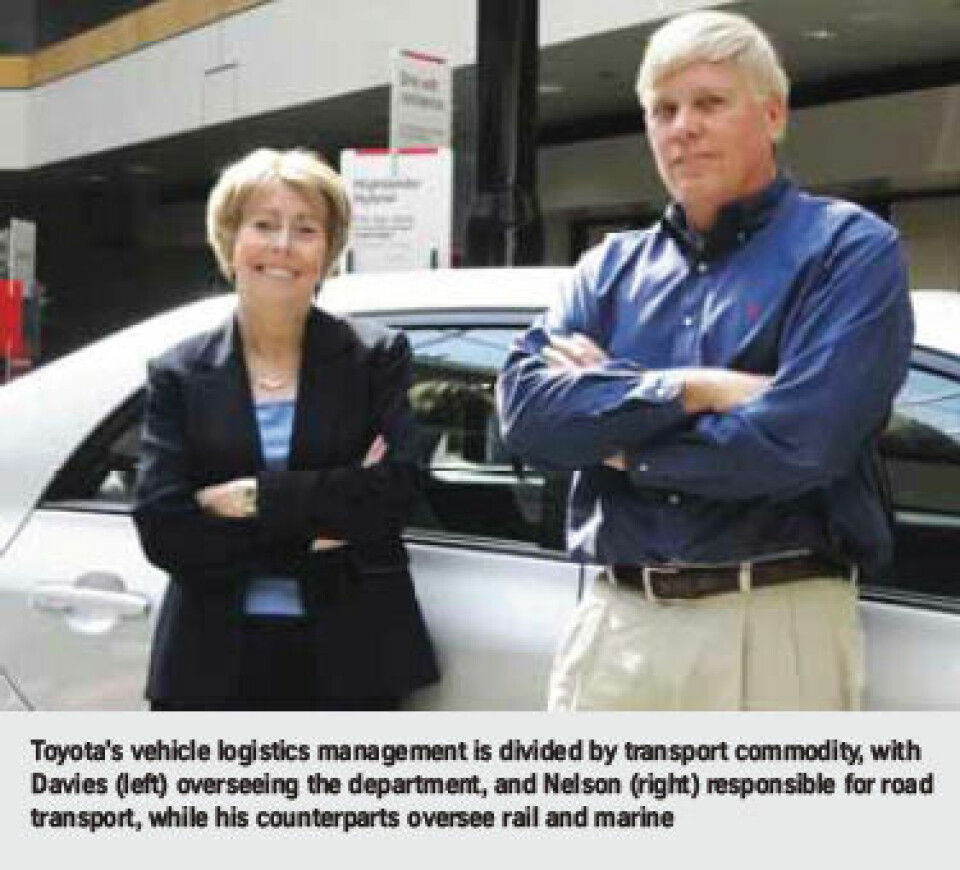
The new system, which will replace several legacy systems, will also give Toyota more automation in functions such as freight invoices and fuel surcharges. Crucially, it will allow flexibility in carrier selection from any given port or plant to any dealer base. For the first time, TLS will have the ability to rate its traffic based on the cubic size of the transported vehicles, allowing for a tiered rate for vehicles that range in size from the compact Yaris to the large Tundra pickup truck. Currently, carriers are charged either a single rate or at best a blended rate, according to Nelson.
Keeping an eye on capacity
Among the question marks facing the vehicle logistics industry in North America for 2011 continues to be the availability of drivers and truck capacity. While most agree that the industry has begun to see signs of driver shortage, and that capacity could become an issue, opinion is divided over whether that is likely to happen anytime soon. Nelson believes that the current levels of capacity are adequate with the exception of some congestion in the northeast, however he believes that the current network could get shaken should the market surpass 13m vehicles. The industry lost some 4,000-5,000 trucks during the downturn, and Nelson does not believe they can come back quickly. “If the economy jumps, then the industry could be in a lot of trouble from a capacity standpoint,” says Nelson. Other looming threats to capacity and the driver shortage are regulatory issues whose outcomes are still pending. Among them is the Comprehensive Safety Analysis (CSA) 2010, which would target safety issues, including better monitoring of carriers and drivers. While the industry largely supports CSA 2010, there is concern that a sudden implementation will result in more drivers leaving the industry.
Toyota is also awaiting the outcome of the hours of service (HOS) proposal, which could limit the hours of consecutive driving from around 11 to 10. Various versions of the HOS have been debated since 2005, though an outcome is expected in the first quarter of 2011. “We are keeping a close eye on these potential measures as they could affect the industry if they restrict the current operating efficiencies of our carriers,” says Nelson.
On the rail side, a large number of wagons (railcars, as they are called in the US) were put into storage during the downturn, but TLS believes that there is generally enough capacity for the market. “However there is some concern about the balance between bi-level railcars [for trucks and SUVs] and tri-levels [for passenger cars], as consumer demand shifts,” says Davies. “For years the industry was short of bi-levels, but now we may be in need of more tri-levels.”
Future projects
With the pending increase in North American production, and the ongoing strength of the yen, Toyota’s US production is not only slated to rise for the domestic market but also for overseas. In 2010, TLS handled the export of around 40,000 vehicles from the US, while the future target for the company is 200,000, according to Davies, with the potential to grow in South America, Russia, Australia as well as South Korea following the recent free trade negotiations with the US. That change means more direct interaction and negotiation with shipping lines, something that TLS already does with a small export team that works as part of its maritime transport unit and together with TMS’s international division. Another ongoing project is related to tracking and limiting carbon emissions in the outbound supply chain, which Toyota tracks across all transport modes on a monthly basis. Toyota is also one of the most active participators in the US environmental body’s voluntary programme Smartway, which encourages carriers to reduce emissions by certain techniques such as limiting idling to monitoring tyre pressure. Toyota is the only carmaker that is a Smartway-certified shipper, and it uses 100% Smartway carriers.
Nelson also reveals that Toyota has participated in meetings with industry groups to consider a wider standard for tracking carbon emissions across all carmaker networks. Steve Jones, managing director of Vehnet, who helped developed the carbon calculator for the European Association of Vehicle Logistics (ECG), has recently met with several groups to discuss a cross-sector analysis that would have the benefit of identifying potential backhauls. Nelson says the proposals are under consideration.
Turning to growth again
For Davies, of course, the main challenge of her tenure at the head of TLS has been in managing three years of declining or stagnant sales. It is a measure of her team’s success that TLS is broadly pleased with the performance levels of providers during the downturn and the early recovery. “As the industry starts to recover and providers bring back people and equipment it has been a struggle to get back to optimal service levels, but overall our partners have done a great job,” she says. But now, for a nice change, Davies is looking forward to the difficulties of growth, including the capacity shortages, should they occur. “If the market goes up to 13.5m or 14m unexpectedly, we will be faced with a capacity problem, but it will be a good problem to have,” she says.