GM, Nissan on FVL strategy

Engineering FVL: An ounce of prevention is worth a pound of cure
Engineering finished vehicle logistics has become a lot more complex and maintaining quality from factory to dealer forecourt depends on communication and transparency, according to speakers from GM and Nissan at this year’s FVL North America conference.
Engineering an outbound supply chain to deliver different vehicle types across different modes and global markets is an ever-more complex job. Keeping an eye on quality, safety, cost and delivery depends on strong partnerships between carmakers and their carriers. That in turn depends on greater transparency through improved communication and a sharper analysis of delivery touchpoints and multimodal network performance with the latest digital technology. That technology, however, needs to be in the right hands. It is a tool for talented employees, not a substitute for them.
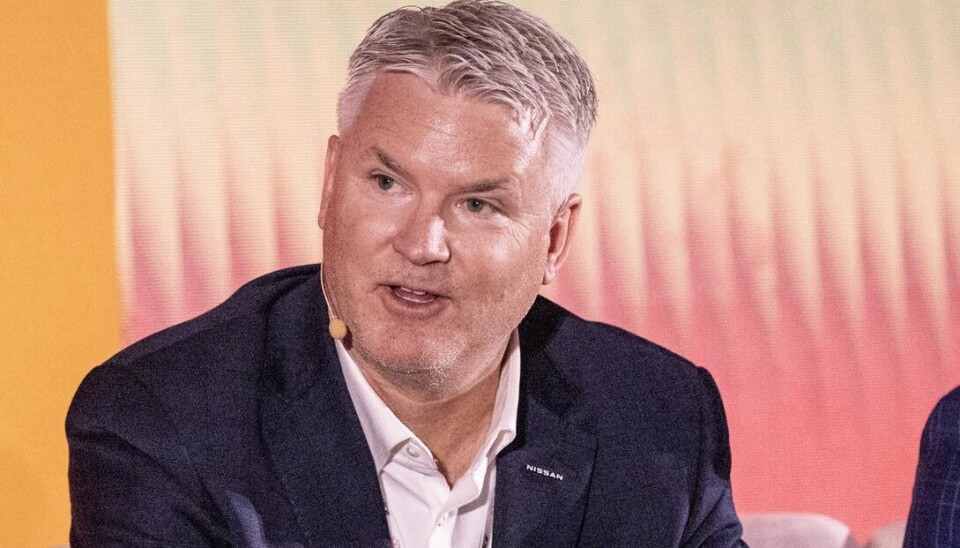
At Nissan, gaining more transparency in outbound logistics starts with communication, according to Ben Shain, senior manager of vehicle logistics at Nissan North America, who was speaking at this year’s Finished Vehicle Logistics North America conference in California. Nissan North America has enhanced the six-month, face-to-face business plan reviews it has with its 19 carriers. Those reviews look at performance and where there are any gaps in quality. “We expect the carriers to come with solutions [and] we expect them to collaborate with us and explain where the gaps exist,” said Shain.
Nissan also reviews where it might be creating problems and where it is supporting, or not supporting, carriers. This internal communication includes a quarterly webinar in which the carmaker goes through procedures for safety, quality, cost and delivery, as well as discussing new model launches and key changes in process and procedure, according to Shain.
Handing off the baton
Nissan sends its carriers information on what vehicles are in the pipeline on a daily basis but in a recent survey of those carriers the carmaker discovered that a number of carriers were unaware of the information sent or not processing it. In response, Nissan began working closely with each of the carriers that had exceptions with the aim of improving forecasts. Nissan is now measuring its forecast accuracy. What the carmaker identified through this review of forecast accuracy is that its projected ETAs on vehicle delivery are based on the time a vehicle ships from a port, plant or railhead but it was not including network performance and where holdups could occur. Key to Nissan’s outbound logistics planning is accurate visibility on the delivery network in combination with the vehicle pipeline and communicating the forecast with its carriers.
“We want the resources to be headed toward the volume when we are ready to ship,” said Shain. “It is like running a relay, handing off the baton is a problem if the next person is standing still. That is what we have been working on to improve the performance.”
Nissan is working on the quality of its delivery to the dealers, factoring in adjustments and identifying potential bottlenecks to ensure vehicles are delivered in a more timely fashion. Shain said Nissan was also taking a close look at vessel bunching and where it can smooth that out.
Bridging the silos
A more comprehensive view of finished vehicle operations based on better communication requires carmakers to look across departmental silos. GM is looking at that both within its own operations and with external partners supporting quality, claims and repair processes.
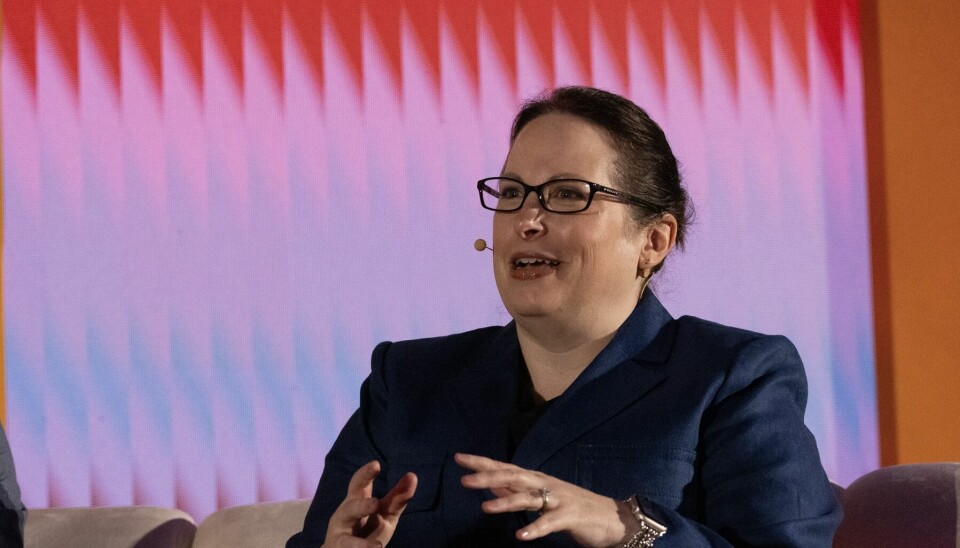
“The quality team at GM is working on streamlining that… and has made cross-functional team proposals, identifying where we could do this better,” said Amy Paulsen, director of finished vehicle logistics. That was very well received and we are working on that project currently.”
Paulsen said that because of the sheer size of GM (and the time it has taken to grow in complexity) there are multiple external players involved in its quality, documentation, claims and repairs processing. Growth at GM has come with fragmentation and Paulsen pointed out that there are four different internal teams involved in its quality adjudication and claims management process. GM is now looking at reformatting the process end-to-end. That starts studying the stakeholders involved and a cross-silo approach to identify where GM can streamline processes. “All of those players play a critical role and they are not ones we can assume internally,” she said.
At the same time, GM is working on getting internal stakeholder alignment across quality and build, vehicle delivery, and for the dealer and customer experience. “It is a new endeavour for us to make sure that everybody is aligned on what quality means and how we are going to deliver it together, eliminate the conflict and make the process go faster,” said Paulsen.
GM is looking at how it can deploy the latest technology to make data transfer seamless and visible to all parties in real time so it can identify and resolve any disputes as they pertain to the claims process. However, Paulsen was also keen to point out that technology would not be taking jobs away from the workforce, stressing the human factor and how it is GM’s employees that design the strategy and deployment of digital tools, and spot the trends in damage and repair. “It is humans that brainstorm and strategise how to make the overall quality process better,” she said. “I don’t see AI and machine learning (ML) taking over those functions any time soon.
Data for dialogue
It is a similar situation at Nissan North America and Todd Myers, director of finished vehicle logistics, said that constant communication and sharing information is fundamental to the carmaker’s relationship with its partners, something that is supported by technology. “You can provide multiple scenarios to your partner, whereas in the past you were just giving a single option,” he said, adding that greater visibility meant more scenarios for consideration. “You are going to have a lot more dialogue and this is going to provide stability to your operation,” he continued. “You can have longer-term relationships and longer-term contracts, to the point where they get more ingrained and truly become a longer-term partner.”
Technology is also helping Nissan visualise its network and better analyse where performance can be improved, according to Todd Myers. Fewer miles travelled means less logistics expenditure. Myers said the technology available today has increased the velocity at which network optimisations can be generated and provides the logistics planner with more scenarios to analyse.
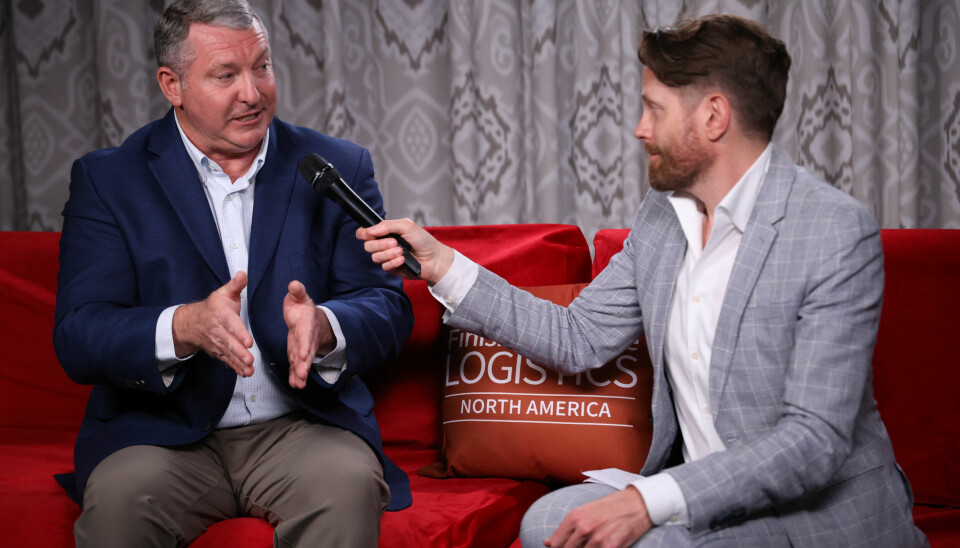
Nissan has recently completed an extensive optimisation pilot that ran for around six months aimed at improving vehicle haulaway. The pilot showed up just how complex finished vehicle logistics is, notably when vehicle output is optimised for manufacturing. The carmaker looked at consumer demand and married it to a standard nine-vehicle car hauler to try and pre-emptively schedule units coming off the production line based on destination enabling a carrier to pick up a full load of vehicles and get on the road more quickly.
“What happens today is that planning is not considered and production runs on manufacturing optimisation [so] you get scattered groups of units,” said Myers, adding that it leads to disparity and delays in vehicles ready to ship. “Considering the planning aspect allows you to batch those units better.”
However, including the vehicle planning based on a nine-car hauler and the destination in the algorithm was extremely complicated and showed enormous amounts of constraint. Myers said the complexity of the problem needs to be revaluated into outbound supply chain planning and that has to include vehicles that are taken off line for one reason or another. The sequence according to which a vehicle starts on the assembly line is not guaranteed to be the sequence it finishes in.
“The carrier is waiting on that unit but even though they have been given visibility in the pipeline, they may not actually get the unit for five or six days,” says Myers. The opportunity to improve antiquated load planning is there but Myers recognised that it is going to take some smart people to figure it out by using the latest technology and analysing a lot of data. That is going to be an in-house optimisation of the process to identify where the constraints are and how to solve them.
“There is a saying where I come from: an ounce of prevention is worth a pound of cure. You get ahead on the planning side and you can solve so many problems on the finished vehicle logistics side,” said Myers.
Amending for electric
One of the main developments affecting quality management and outbound supply chain planning is the growth in the movement of battery electric vehicles (BEVs). By the end of 2024 GM had a robust BEV portfolio in place, including the GMC Hummer EV and the Cadillac IQ – “beautiful but very large and heavy EVs”, according to Paulsen. The impact on quality and load factor mean that GM had to work closely with its road and rail logistics providers.
“The team did a lot of tactical work with our rail partners, including what is the best way to chock them [ending up with six chocks to secure the vehicles],” said Paulsen. There were also trailer modifications to make for road haulage. “These new EVs are in a way a class by themselves so that took a lot of prework,” she said.
Thomas Shannon, finished vehicle operations manager, Ports and Logistics EV, at GM pointed out that vehicle density per trailer is dropping significantly because of larger BEVs. “[Last year] was a huge launch year for use with EVs, I think we had six major launches,” he said. “During those launches we had a ton of cross-functional teams, from quality, engineering and safety, and we all worked well together; our voices were heard, so are hoping we can move forward with these lessons learned and really help ourselves from a logistics end.”
Premium BEVs that sell quickly has put a new focus on quick claims resolution of claims and accurate documentation. Paulsen said this is another area where GM is researching digital technology to ensure it has an end-to-end chain of evidence internal to the business.
“Where we fail in the claims process is usually where there is a gap, where information is missing or a process was dropped,” said Paulsen. “We are really looking at how we streamline that using technology, using platforms that guide and document the quality process through the different milestones, so that we don’t have that fallout.”
Analysing the complexity
One other crucial factor in vehicle logistics engineering and planning is the increased handling involved in a more complex distribution network and one that is increasingly its inclusion of BEVs. Outbound logistics planners are keen to miminise touches as a means to control cost regardless of the powertrain.
“At the end of the day everything we do across safety, quality, delivery – all of those things ultimately have to equate to some cost for the business,” said Nissan North America’s Myers. “Fundamentally with my partners and my carriers, we have to execute on all of them to the best of our capability. Understanding the kind of the thing that governs us is where we land on a cost per unit standpoint.”

Myers said this applies to the entire finished vehicle logistics system from taking ownership of the vehicle to getting it to the dealer quickly, robustly and following Nissan processes.
Complexity in outbound logistics is encouraging Nissan to work differently with its partners and to look at different tools for analytics, according to Ben Shain. That includes a data visualisation tool called Tableau. Considering delivery performance and the balancing of cost-per-unit versus total landed cost, Nissan has been working on improving its ‘day zero’ – the first day on which a finished vehicle is available for shipment and the first 96 hours of operations.
“It was insightful to see [in a three-month set of data] the number of VINs at a given ramp that would be grounded and available at 10 o’clock in the morning,” said Shain, adding how that compared to other that were not available until 8 o’clock in the evening with no chance of being delivered.
Nissan met with its Class One railroad partners and shared data specific to each of the their ramps. Shain said that with really good performing ramps the emphasis was on maintaining that performance with only minor schedule tweaks if necessary. However, in examples where the train schedule and unload was timely but the transmissions were not it was important to make the Class One railroads aware of that and try to move solve it.
“We want it to be early as possible so the carrier can get that day zero or maybe even a second turn,” said Shain. “We are trying to focus on our free cash, we want the railroads to be able to use their railheads with multiple OEMs, and we want the carriers to benefit from driver utilisation from the equipment and hours of service. It is really a three-way win.”
Merits of mobile charging
At GM, Paulsen is bringing some nimble start-up thinking to the complex outbound network from her experience working at Tesla, Byton and Rivian.
“One key point is taking control of our own destiny, which is a very start-up mindset, [including] in terms of the mobile charging,” she said. “Where the market isn’t meeting the functional requirement we have to fill that gap.”
New electric vehicle programmes and production is not slowing down while outbound logistics planners find an answer to the increased demand for charging infrastructure. Mobile charging has saved GM’s bacon, according to Paulsen.
“It has enabled us to dramatically reduce the number of ‘bricked’ vehicles we have at various vehicle distribution centres [VDCs], and our rail partners are very grateful that we have this solution,” she said. While not a long-term solution there is always going to be a place for mobile charging, according to Paulsen, because the network is always going to be shifting.
“Long term, where we have fixed locations – plants, VDCs that are high volume for us – there should be a more permanent infrastructure in place,” she said. Currently, however, the lead time on a transformer from Asia is 18 months and it takes as long to get the agreements and permits in place from the local utility company. There is also the financial investment to consider and the fact there may not be sufficient electric generation in the grid to keep up with demand. “Those are all longer-term problems to solve but that should be the goal,” said Paulsen.
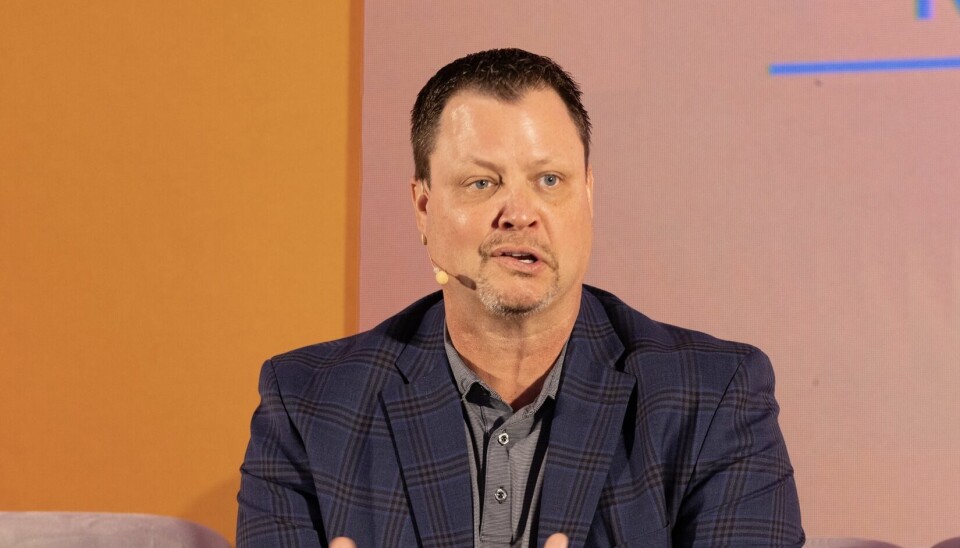
Toward that GM is getting creative with how it manages the charging and Paulsen said the company is starting to see some consistency with standards. Thomas Shannon, who has been leading on those standards, said that GM had partnered with multiple mobile charging companies. “It is one of the things we kicked off early in 2024 when we started our launches,” he said. “We quickly realised that we did not have the infrastructure that we need at our manufacturing facilities. It was quite eye-opening and scary [finding out] what we were supposed to do about the vehicles.”
Having multiple mobile charging partners has worked out well for GM and Shannon said that, regardless of the administration in government, BEVs are here to stay. The industry needs to move forward as a whole and carmakers and their partners need to look at how they can support each other in that area.
Trade and tariffs
Government policy is also having an impact on vehicle volume flows in terms of trade and tariffs. Currently, the smooth flow of volumes by road and rail are being hampered by political and legislative factors at home in the US and abroad, including the impact of shifting tariff legislation on vehicle releases and movement across borders.
“Unfortunately, with all of the disruption that continues to occur in the market we are constantly having to adjust to abnormal conditions, and it results in storage lots and different processes, but you ultimately have to have the discipline to bring that stuff home,” said Nissan’s Myers.
That discipline includes taking a strategic and tactical approach to operations and preparing for the “capacity bubble” that could occur (depending on the duration) when pent up volumes begin to move again and carmakers are looking for capacity, including for cross border rail from Mexico into the US.
That is something that GM is also feeling, according to Paulsen, and tariffs have further challenged a vehicle logistics process that has traditionally lacked creative thinking.
“Tariffs are on, tariffs are off, tariffs are back on – if you are the railroad how do you react to that?” asked Paulsen, adding that it was equally difficult from the OEM side. Again, managing this situation comes down to better transparency through communication with logistics partners.
“We have started to have very transparent communication, telling them as soon as we know that something is changing [and admitting] we can’t make any promises but we are in this together,” she said. “We have had some very creative ideas in terms of circulating carflow and new places to store cars, so if there is a disruption we can bring that back online very quickly.”
What is clear from both GM and Nissan is that communication is key. Data needs to be shared between OEMs and partners to make better decisions on outbound vehicle delivery planning and for the benefit of the overall finished vehicle logistics network, including for electric vehicles.