Warehouse excellence at Robert Bosch
Extensive research and testing of lean principles have elevated tier one supplier Robert Bosch’s warehousing practices alongside the highest OEM plant standards. The supplier is trying to replicate these lean standards globally
Few terms are used as ubiquitously throughout automotive production as ‘lean management’, a concept of continuous improvement and manufacturing efficiency derived mostly from the Toyota Production System (TPS). The tools associated with TPS and ‘lean’ – just-in-time, just-in-sequence delivery, kanban cards, supermarket storage areas, milkruns, and level ordering – are design features of most plants. Japanese words like kaizen for continuous improvement or heijunka for stable production flows have become embedded in the language of plants from the US, to Germany, Brazil, China and India.
Take the example of Robert Bosch, a major tier one supplier and distributor of service parts and products that include diesel systems, electronics and power tools. For more than a decade, Bosch has developed and implemented the Bosch Production System (BPS), an adapted version of TPS, in which key performance indicators (KPIs) and productivity at plants are measured rigorously, with operations standardised and constantly studied for process improvements.
The company provides thorough training in ‘lean’ from board level through plant managers and down to team leaders and line operators. For instance, there are six days of training just to define and understand concepts like ‘system-CIP’ – a method for mapping out the overall value stream and setting goals for each operation – and ‘point-CIP’, a data-driven tracking of processes with the goal of stabilising them.
Lean logistics is an obvious extension from plants. Indeed, when most logistics providers and manufacturers discuss their supply chains at conferences or in marketing slides, they describe material and products circulating with the steady rhythm of a pulsing heart, monitored for irregularities with the precision and care of a cardiologist.
However, research by Dr Kai Furmans, director of the Institute for Material Handling and Logistics (IFL) within the renowned Karlsruhe Institute of Technology (KIT) in Germany, shows that lean concepts have been slow to spread across the supply chain. Until recently, he has seen little evidence of it in warehousing, inventory management and especially in transport.
For Furmans, who worked in distribution and logistics at Bosch before joining the IFL, the biggest gaps are in setting standard processes and KPI tracking. He has seen few warehouses that use value-stream mapping, such as ‘system-CIP’, to break down each step of their operations and target ‘future states’, such as set unloading or packing times for given products. There is also a lack of systematic measurement of KPI deviations – the ‘point-CIP’ – to track progress and make adjustments.
“Part of this is a cultural failure of understanding, which existed also in the first ‘lean wave’ to hit the West in the early 1990s,” he says. “We focused a lot on the tools – be it JIT, kanban, etc – and less on the system behind ‘lean’. At Bosch, for example, we had continuous improvement workshops, but we hadn’t defined a future state where we wanted to go. Without that, you are not able to check deviations and you lose much of the power of ‘lean’.”
Reacting to KPIs
You might dismiss such criticism as academic, but Furmans has worked closely with Robert Bosch and his views are shared at high levels of its logistics management. Until earlier this year, Dr Helmut Wlcek was head of corporate logistics at the tier supplier, leading the central supply chain function across the company’s 280 plants. Wlcek, who has recently taken up a research position at KIT as director of the Karlsruhe Service Research Institute, agrees that, outside plant operations, logistics lags in lean processes. “Even the best companies in Germany for ‘lean’, such as Porsche, started really late to apply the principles to logistics outside the plants,” Wlcek says.
"[In the 1990s] Bosch had continuous improvement workshops, but we hadn’t defined a future state where we wanted to go. Without that you are not able to check deviations and you lose much of the power of ‘lean’"
- Dr Kai Furmans, Karlsruhe Institute of Technology
Like Furmans, Wlcek sees the biggest gaps in KPI measurement and reaction. While many warehouses use a large number of KPIs – too many in some cases, he says – they are not used to address root problems. He recalls one warehouse where management proudly showed him a wall with a list of the warehouse KPIs; nearby was another list of kaizen ideas from employees. Wlcek asked for the link between both sets; he was told there was none.
“That means that the management was not using the true potential of lean management,” he says. “In this case, they were just listing their problems and not finding root causes.
There are thousands of opportunities for improvement, but you should use your data to choose those that most impact your KPIs.”
From a gut feeling to proof of lean benefits
While Furmans and Wlcek had observational evidence that Bosch was missing productivity and performance improvements in its supply chain, it was not until a more co-ordinated and scientific study was done that the impact could really be measured and then addressed across the company.
Enter Payam Dehdari, who started at Bosch in 2008 and also did his PhD at KIT. As Dehdari explains, he and others had a “feeling in the belly” that there were big opportunities in the warehouses. Bosch, after all, has more than 800 warehouses across nearly 50 countries, which collectively cost several hundred million euros each year and are fundamental to maintaining flexible production and distribution. He and Wlcek had also visited operations where they saw true lean warehousing in action, including a Toyota parts distribution centre in Belgium, which operated with the timing and efficiency of a plant. They believed introducing a lean culture would have tremendous benefits, but they needed to prove to Bosch’s board that the investment would be worthwhile.
Dehdari worked with Bosch and KIT on a comprehensive ‘Warehouse Excellence’ study of the impacts that lean management training at warehouses would have on productivity. The study included 16 warehouses in eight countries spread across different Bosch divisions, including automotive, aftermarket and power tools. The varied warehouse operations included raw material, inbound factory supply and distribution. Similar to Bosch’s global makeup, the tier supplier managed half of the warehouses in-house, while logistics providers ran the other half. Separately, Dehdari established a control group of 56 warehouses of varied background and management with which to compare data.
Dehdari and Bosch developed a system to measure ‘lean maturity’ in the company’s warehouse operations (which included determining how well they carried out continuous improvement programmes) and also measured KPIs and productivity. In 2010, the first year of the study, data was collected in the first ten months without any actions taken in either warehouse group. At the end of the year, Bosch “empowered” the Warehouse Excellence group, in Dehdari’s words. This included an extensive set of training in lean processes and value-stream mapping, followed by consulting and workshops throughout the next year. The company then tracked lean maturity as well as KPIs and productivity in 2011, to compare the differences between those warehouses in which lean processes had been implemented and those where nothing specific had been done.
The results have since been published as a book and while there is far too much data and analysis to be effectively described here, the findings are compelling. Most importantly, the warehouses that improved their lean maturity showed a statistically significant increase in productivity, which was at least 10% higher than any productivity gains among warehouses in the control group. While Dehdari is careful to point out that he could not establish a mathematical link between an increase in lean maturity and productivity increases, the correlation was strong.
Dehdari reached conclusions that match what Furmans and Wlcek say about the importance of a lean system – particularly the focus on targeting a ‘future state’ for each process and then measuring outcomes and deviations frequently. “At the beginning of the project I also thought it was going to be about the lean tools, but by the end I understood that it is about systematically and analytically driving ‘lean’,” Dehdari says. “We have to underline ‘systematic’ and ‘analytical’ as they are so important.”
Getting lean from Stuttgart to Wuxi
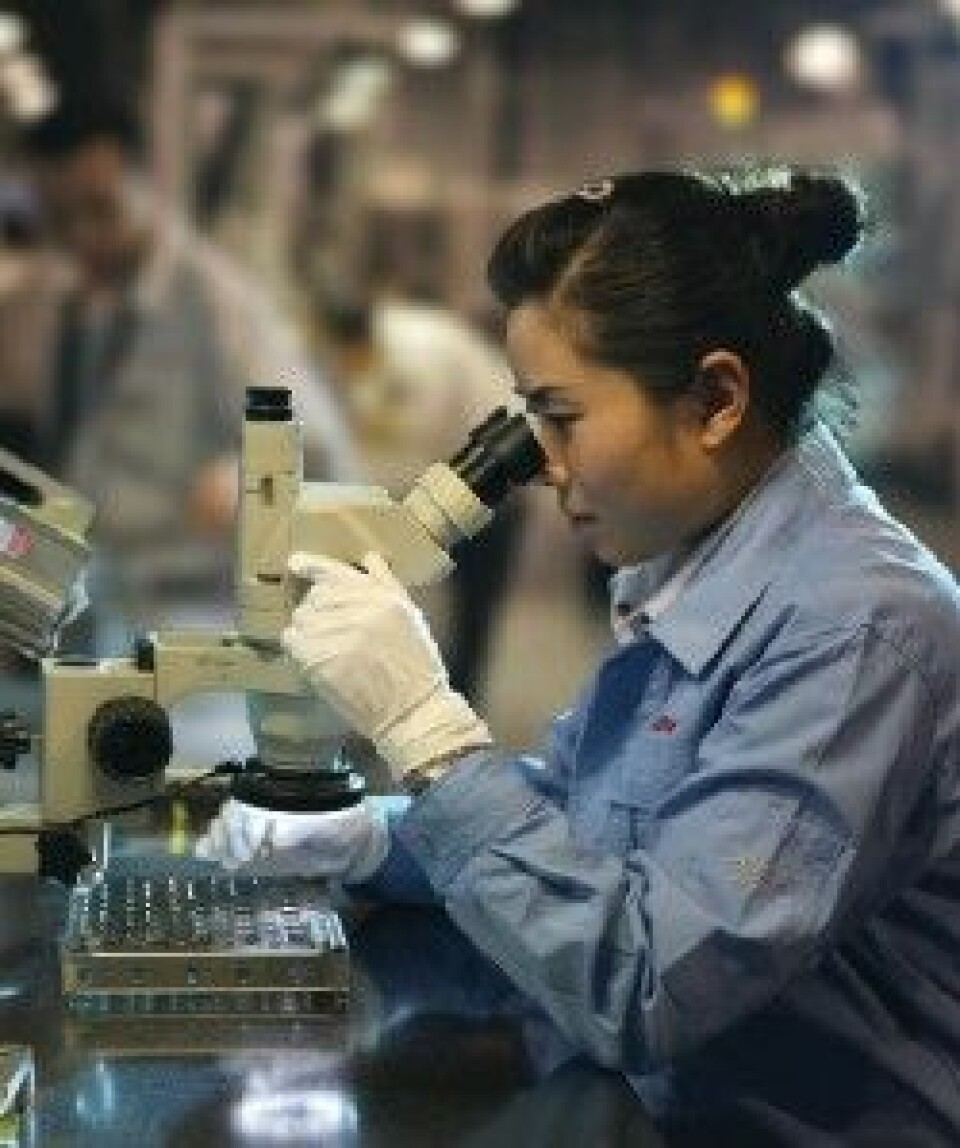
The Warehouse Excellence project validates the hypothesis that an investment in lean management and training increases productivity. This is the kind of calculus that pleases management and executive boards as much as academics. Following the project, Bosch’s corporate logistics department held a conference inviting warehouse leaders to present results to other representatives of Bosch’s global operations. Among those inspired from these findings to introduce lean management at his own warehouse was Dr Hans-Henning Töpper, vice-president of Bosch Automotive Diesel Systems, a joint venture for diesel engine components for the Chinese market based in Wuxi, west of Shanghai. The impact of introducing lean processes to the joint venture has been impressive (see case study).
While Töpper requested the project, Bosch is now coordinating a broader rollout of lean warehouse management. This is no loose and mushy target – the board of directors has approved it and Bosch is building up a consulting arm within its corporate logistics department to help lead and implement the project. Dehdari, having now gained his doctorate, has been part of this consulting team, which is set to become even larger, adding more senior managers and directors at both the central department at Bosch’s Stuttgart headquarters and in regional centres of competence.
Empowering ‘immature’ warehouses
According to Furmans, the potential for improvement in cost and operational performance is not just incremental. “It is huge,” he says, with double-digit productivity gains common. Furmans maintains that such improvements occur at warehouses that already meet the company’s criteria for costs and performance. “These were not what anyone would have considered ‘bad’ warehouses by any means,” he says.
Data from the project was encouraging in demonstrating how effective the ‘empowerment’ of lean management can be. For example, lean maturity tended to be higher initially at warehouses feeding production than at those for raw material or distribution, presumably because of proximity to lean operations at plants. The lean maturity of logistics provider-run warehouses also tended to be somewhat behind Bosch warehouses. However, it was these very types of warehouses that showed some of the biggest and most sustained improvements.
“When we took the second measurement after the empowerment of the Warehouse Excellence group, the production warehouses again showed small improvements,” says Furmans, “but the really big improvements came from those warehouses that kept the processes and ideas that they had learned, including non-production facilities and those managed by LSPs.”
Dehdari adds that the providers who showed the most gains tended to be medium-sized companies rather than larger ones, which he attributes to top management engagement at such companies, including chief executive officers who sometimes took up the ‘lean’ mantel. Furmans’s own research also shows that medium-sized companies have greater improvement potential, in part because of a willingness to share data. “These companies are not necessarily better than large ones, but they are more open to exposing their problems, which is the biggest step to improvement,” he says. He adds, however, that IFL is currently working with a very large German logistics company to create six lean training centres across the country.
"Even the best companies in Germany for ‘lean’, such as Porsche, started really late to apply the principles to logistics outside the plants"
- Dr Helmut Wlcek, Karlsrhue Service Research Institute
The potential to improve outsourced operations may be one of the most important findings of the project. While Bosch has many in-house warehouses, the view from its corporate logistic department is that warehousing should be the core competence of logistics providers. While the company tries to eliminate as many storage locations as possible, demands for flexible production and quick delivery mean that warehouses, particularly outsourced operations, remain strategic. In China, for example, Bosch Automotive Diesel Systems is rolling out a network of regional distribution centres to serve critical customers, all of which will be run by providers.
According to Dehdari, some logistics providers are making progress; several have warehouses with higher lean maturity than Bosch’s own, although most have a long way to go, he admits. In the long run, Dehdari envisions providers being as good as, or better than Bosch and other manufacturers in such areas. “It is no secret. Bosch wants service providers to see ‘lean’ as a core competence and eventually to teach us,” he says. “Currently a higher percentage of our providers are far away from our own levels, and we want to close this gap.”
What does ‘lean’ mean for outsourced warehouses?
Applying lean processes across a vast network of warehouses requires both central support from Bosch’s logistics and competence centres as well as local management reinforcement. For Diesel Systems in Wuxi, Bosch sent consultants from Germany for a week every month for six consecutive months, supplemented with weekly two-hour tele-conferences to control and monitor the process. “My entire logistics team, including the department manager, section manager and team leader, shared 100% of their working time with the consultants to help collect the open points and close them,” says Töpper.
Bosch set up a ‘war room’ in Wuxi dedicated to the lean activities. When the consultants were in China, they assessed data and processes. For the three weeks in between, the local team had to implement new processes or reconstruct others. “We needed considerable support in the beginning, but now my team is able to run this project by itself,” Töpper says.
Bosch hopes such success can be replicated across hundreds of warehouses, with logistics providers as willing to commit to the process as the diesel joint venture in China has been. Töpper admits his company has not yet applied lean standards to outsourced warehouses, instead requiring annual price reductions that leave the methods to the providers, but he admits his team will have to look more closely at outsourced sites in future.
"Bosch wants service providers to see ‘lean’ as a core competence and eventually to teach us. Currently a higher percentage of our providers are far away from our own levels"
- Payam Dehdari, Robert Bosch
Furmans, Wlcek and Dehdari agree that it can be complicated to bring lean principles to outsourced sites. Some logistics providers might be hesitant to commit time and resources to the training and many warehouses are used for multiple clients, each with different standards and requirements. Even more fundamentally, some providers might see the systematic elimination of waste as a threat to their own businesses. However, Furmans believes that providers interested in long-term relationships should embrace ‘lean’ as a means to maintain or gain further contracts. “Over a long-term relationship, there should be an expectation to improve productivity as a provider to your customer,” he says.

Providers who complain that their contracts are too short to invest in lean improvement also do not impress Wlcek, who still consults for Bosch. “Such an excuse would be valid only if the provider thought it had no chance of continuing business with Bosch,” he says. “While I wouldn’t invest in large equipment that wouldn’t pay off in time, investing in business quality and processes has clear benefits.”
Wlcek’s research on labour management also subverts some traditional ideas about ‘lean’ that might otherwise put off service providers, including that it requires a largely fixed workforce. He points out that while Bosch’s in-house warehouses use mainly permanent employees, logistics providers tends to operate with many temporary employees – in some cases up to 80-90% of the workforce, including even team leaders.
Wlcek accepts that in those extreme examples, lean training is difficult. However, he sees scope for operations with many temporary workers to still gain high lean maturity, perhaps with as much as 50-70% of operational staff being temporary, as long as management and team leaders are permanent.
“Lean standards help you to instruct people much faster, which in turn allows you to work with a higher number of temps,” he says.
While there may be contract terms and supplier relations to finesse, the findings of the Warehouse Excellence studies and further research on the benefits of ‘lean’ would seem to bode well for providers. The productivity improvements save costs, while lean training can help retain management and keep labour flexible, including in regions like China where staff turnover is high. Dehdari believes that ‘lean’ drives benefit sharing between customer and providers. “Both sides have to invest first, but then this helps to drive providers’ operations more efficiently,” he says.
While bringing ‘lean’ to warehouses is a long-term project for Bosch, there is also potential to roll out these processes to trucking, where Furmans and Wlcek believe lean maturity is lowest. Technology will play a role; Wlcek is researching ways to improve transport time windows and administrative processes across deliveries, including further use of consumer smartphone applications (rather than clunky and expensive industrial equipment), telematics and sensors in packaging. He is even reasearching driverless trucks.
As with warehousing, the big wins will come from changing the mindset of managers and companies. Both researchers feel that if top management is committed to the benefits of a highly data-driven analysis, then it should be no more impossible to convince truckers of its benefits than it has been warehouse operators.