BMW and Greer: A port far from any storms
No ocean-going vessel ever docks there but an inland port at Greer, South Carolina, has proved a perfect solution for BMW’s import and export parts shipping needs
In this story...
Perhaps the truest measure of efficiency and reliability in an automotive supply chain should be how soundly the logistics manager sleeps at night. On such a metric, Alfred Haas, department manager for material and transportation at BMW’s Greer, South Carolina, plant in the US must be getting more than his fair share of beauty sleep.
Haas, who oversees delivery assurance at one of the most productive car plants in the world, says his work-related sleepless nights have been virtually eliminated since the OEM started using an inland port near the plant, run by the South Carolina Ports Authority (SCPA) and serviced by a Norfolk Southern rail line that connects it to the port of Charleston.
“The operation works flawlessly and it has been a very successful project,” says Haas of the facility, which first began operations in the fourth quarter of 2013. “To me, a good partner understands your needs as a customer and how they can best support you. They understand how it works for you – and that’s what we’ve found through this partnership.”
Enhancing the supply chainPrior to the development of the inland port facility, BMW relied heavily on truck transport between its Greer plant, located within the Greenville-Spartanburg metropolitan area, and the port of Charleston, over 200 miles (320km) to the east. On any given day, BMW would receive around 50 truckloads of parts from the port, including engines and transmissions imported from Europe, and send back the same number with either finished vehicles or semi-knockdown kits (SKDs) for export.
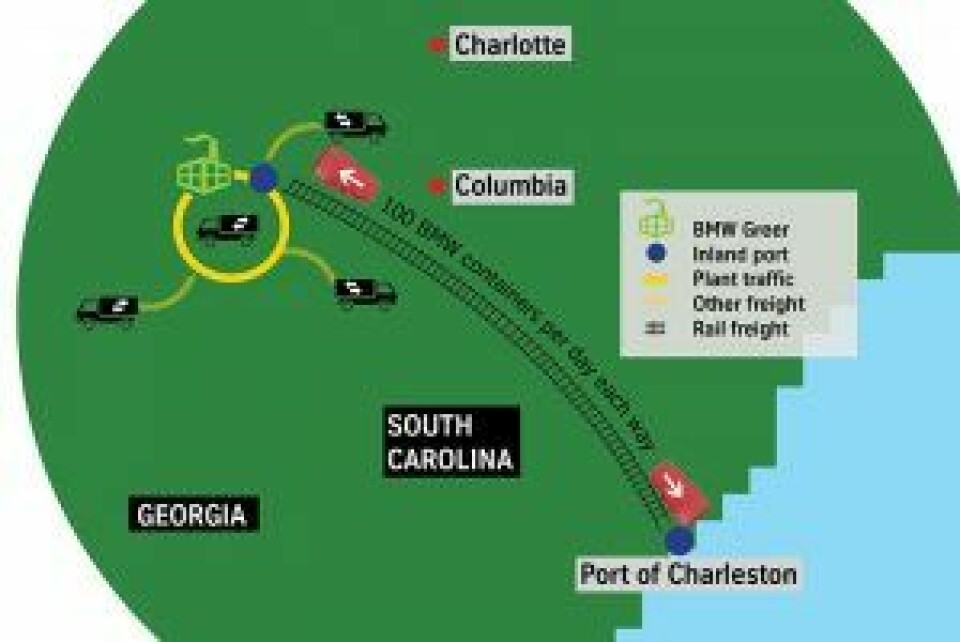
Inland port connections at BMW Greer – click to enlarge
That meant that, at the time, the plant was responsible for around 25,000 truck journeys a year, says Haas – a number that was set to rise significantly. Over the past three years, the Greer plant has become the largest BMW factory by volume in the world, with production rising from around 300,000 units per year to more than 400,000 of the BMW X3 and X5 Sports Activity Vehicle as well as the BMW X4 and X6 Sports Activity Coupe. The plant is also now preparing to build the X7, which will increase capacity to 450,000 units per year.
[sta_anchor id="1"]In assessing the logistics of its time-sensitive supply chain in South Carolina, BMW wanted to look at approaches that would eliminate the risks of highway congestion and reduce the potential for accidents, as well as sidestepping the issue of truck availability, says Haas. It also wanted to reduce the carbon footprint of its transport systems, he adds.
“The time was right,” says Haas about the move to establish the inland port in Greer. “BMW, Norfolk Southern and the port had a discussion about how we could move the freight from these trucks onto a railcar – especially since we are using rail to move our finished products. The biggest question was: how could we get our sea containers onto rail and to the plant?”
Using existing resourcesA workable answer to that question had been put in place nine years before the OEM even announced the plant’s construction, as it turned out. Back in 1983, SCPA had purchased a parcel of land in Greer for future use; by the time Norfolk Southern began the conversation with BMW in early 2012 about the possibility of moving trucked freight onto rail, SCPA president and chief executive Jim Newsome had already been thinking about possible uses for the site.
Newsome, who served as president of Hapag-Lloyd (America) before joining SCPA in September 2009, was no stranger to ocean container handling or to BMW’s operations at the port of Charleston. He had already taken steps a few years earlier, shortly after joining the port authority, to accommodate the carmaker’s needs at the port by relocating a terminal for outbound finished vehicles.
“BMW was growing and we had them in a footprint on our Union Pier that wasn’t going to be sufficient for the future. It would not have been able to handle their growth and they were very concerned about it,” he says. “We made a strategic decision to have Columbus Street serve as our main roll-on, roll-off terminal.
“The main thing that I was doing was making sure that we had the right home for the BMW manufactured vehicles,” he adds. “The move gave them certainty that they would have a terminal that would accommodate their growth.”

That Charleston facility now sees approximately 5,000 finished vehicles per week arriving via Norfolk Southern along a rail line that starts at the end of the BMW assembly line and testing centre in Greer. Of the 285,000 finished vehicles exported by the OEM from the plant during 2015, Charleston port was the point of departure for some 250,000 units.
Newsome says it was important to cater for BMW’s business for both parts in containers and vehicles. BMW is one of the largest exporters of vehicles to foreign markets from the US; it is also an important importer and exporter of components. So when Newsome heard about the plans being put together by BMW and Norfolk Southern to move containers onto rail, it was obvious that the Greer site, which is just three miles away from the BMW plant, could be the solution.
“I had started considering, in the back of my mind, what we were going to do with this property,” says Newsome. “When I got the phone call from Norfolk Southern, I was able to pretty quickly say to them that we were interested in building an inland port. The biggest discussion that ensued was we wanted to run the inland port, and run it as a port facility.”
[sta_anchor id="2"]Custom-designed logistics platformWhen Norfolk Southern agreed to SCPA’s operational concept and plans were developed with BMW as the inland port’s base customer, chief among the earliest challenges to be met were the economics of what stood as a short-haul rail run between Charleston and Greer. “Rail is typically considered a 500-mile application and we were looking at making it work for 200 miles,” says Newsome. “It was touch-and-go in that regard, but BMW was interested in the concept. And if you look at a supply chain, what it’s ultimately about is reliability. We were putting in measures that enhanced reliability and having their containers within three miles when they needed them, as opposed to 200 miles away at one of our port terminals, was attractive to BMW.”
"If you look at a supply chain, what it’s ultimately about is reliability. We were putting in measures that enhanced reliability and having their containers within three miles when they needed them, as opposed to 200 miles away at one of our port terminals, was attractive to BMW." - Jim Newsome, South Carolina Ports Authority
The key component for making the 200-mile run work, says Newsome, was the ability to access the overnight rail service that Norfolk Southern already had in place.
“If you look at the rail networks in this country, probably only 5% are high-density intermodal rail,” he says. “The rail network for [Norfolk Southern] in South Carolina happens to be right up Interstate 26 through Greer. So this was tapping into an existing rail network.”
That helped the parties involved to move quickly. From that first conversation in January 2012 between Newsome and the railway, it took around 20 months to put the facility into operation in October 2013. The port authority invested more than $50m while the railway spent about $7m to put track infrastructure in place, according to Newsome.
“I predicted that we would do 100,000 rail lifts at that facility within five years and we started with a base cargo of about 25,000,” he says. “Now, in our third year, we’ll do over 100,000 rail lifts.”
“It has been wildly successful,” Newsome adds. “I would love to tell you that it’s due to absolutely fantastic strategic management, but we had a certain amount of good fortune.”
[sta_anchor id="3"]Non-automotive freightPart of the planning for the Greer facility centred on the potential for bringing together automotive parts and non-automotive freight into the transport mix. As things have turned out, there have been plenty of opportunities to create more than enough inbound and backhaul freight on the line to prompt Norfolk Southern to put a dedicated train in place to provide a general service between the inland port and Charleston. The train, which is made up of around 5,000ft (1,525 metres) of railcars, now includes about 100 containers per day from BMW moving in each direction.
According to Jeffrey Heller, Norfolk Southern’s vice-president of intermodal and automotive marketing, the automotive industry, including parts and finished vehicles, accounts for around 10% of the railway’s total business. “It’s a major portion of our revenue and, to the extent where we can have an umbrella of multiple lines of business that can cater to the same customer, that’s a big benefit as well,” he says. “We work with the multilevels [for finished vehicles], but, if we can tie that in with the container transport, that works really well for us, especially if we can have it all in one location.”

The Greer inland port allowed Norfolk Southern to add containerised automotive freight to the extensive work it was already providing to BMW in hauling the carmaker’s finished vehicles to Charleston aboard its multilevel service. Meanwhile, Norfolk Southern and SCPA were able to market the Greer inland port hub to other industry verticals, creating more opportunities.
“We started off the train with existing BMW freight,” says Heller. “As part of our plan, we and the port developed a portfolio of business with companies in and around Spartanburg and Greer. We also worked with customers further away. We were able to move [other] business that was being trucked into the port over to the train as well. That made it possible to run the separate [dedicated] train, which is what we do today."
Today, more than half of the business that moves by train from Greer to Charleston and back again is non-BMW business, according to Heller. While the carmaker is at the core of the business, the logistics solution has been beneficial to multiple companies. “We had two goals: to cater to BMW, which was first and foremost; and to be an economic development generator in that part of the state,” he says.
A measure of successThe Greer inland port is not just a niche, low-scale operation. According to a study conducted in 2015 by research firm CBRE, it ranks among the top five such facilities in the US and it was described as the “up-and-comer” in the firm’s 2016 North American Inland Ports Logistics Annual Report. The CBRE report notes that rail volumes related to the inland port at Greer increased by 211% from 2014 to 2015; in March 2016 alone, it achieved more than 9,000 rail container lifts.
"[The inland port] had to design a system that could locate and deliver to the plant the sea containers that BMW identified in a 45-minute window. We do this every day – several times a day – and it works very well." - Alfred Haas, BMW
There have also been benefits beyond cost savings and supply chain efficiencies. By removing 25,000 truck journeys a year from the roads for BMW, the inland port has saved some 13,000 pounds (nearly 6,000 kilos) of CO² emissions.
“This is a great partnership and it just continues to grow. It couldn’t have happened without BMW and without Jim [Newsome]’s group at the port. We think the partnership between SCPA, Norfolk Southern and BMW is visionary,” says Heller. “[BMW has] a plan to grow with that plant, and we hope to grow with them over time.”
BMW’s history of success in South Carolina has led other OEMs to place a footprint in the state, with Volvo Cars and Mercedes-Benz Vans also set to build plants in the Charleston area. While neither Volvo nor Daimler will need the inland port infrastructure, they have both been in discussions with SCPA on designing efficiencies within their respective production operations that will use SCPA’s expertise in the movement and storage of sea containers.
Meanwhile, Newsome says he has received inquiries from other ports seeking inland facilities like the one at Greer.

Other carmakers and ports may have looked to BMW at Greer for similar models already. This year, for example, Kia started moving inbound parts imported through the port of Savannah, Georgia by rail to an inland terminal in Cordele, which will then be moved by truck to the carmaker’s plant in West Point.
Newsome’s wider vision for the inland port is also beginning to come into focus. “We had in mind that the facility would be a catalyst to make the Greer area more of a distribution hub for [sectors] other than automotive,” he says. “We said when we opened the inland port that it had the potential to be the convergence of four modes of transportation – truck, rail, water and air. And the Greenville-Spartanburg airport just landed two new air freight clients supporting the European automotive industry.”
[sta_anchor id="4"]The inland port doesn’t just give BMW greener, more reliable transport, but also more efficient storage and management of its sea containers. Prior to the construction of the inland port, trucked sea containers were kept at the BMW plant itself. As the Greer port was being developed just three miles from its plant, however, BMW worked with the port on building a warehouse adjacent to it. Now, it keeps its containers offsite at a leased 400,000 sq.ft (37,000 sq.m) storage facility and simply calls them in as required.
CenterPoint Properties built the warehouse and it is managed by third party logistics service provider Syncreon.

“The inland port gave us the opportunity to store our sea containers offsite and call on them in a just-in-time manner,” confirms Alfred Haas. “They had to design a system that could locate and deliver to the plant the sea containers that BMW identified in a 45-minute window. We do this every day – several times a day – and it works very well.”
The warehouse also serves as the platform where Syncreon packs semi-knockdown kits (SKD) for export to seven markets, including India, Egypt, Thailand and Russia. BMW ships about 100 sea containers per day for SKD assembly.
SCPA serves as an administrator for the free-trade zones in the state and the inland port at Greer also holds a free-trade zone status, which helps BMW handle and export material with less bureaucracy and lower costs.
Adopting this approach has opened up space within the plant, notes Haas. “It’s helped us to be more efficient inside the plant and we are able to use the space for expansion,” he says. “The port handles getting the sea containers unstacked, and we’ve had no issues with handling or damages.
“The port is open for us 24/7. They are very customer-oriented. So far, we have not had any interruptions at BMW.”
Is Haas, therefore, a logistics manager who sleeps very soundly at night? “Absolutely,” he confirms.