Battery supply chain could bottleneck in 2025, says analyst
The supply of lithium batteries for electric vehicle (EV) production could bottleneck from 2025 as demand for EVs outstrips the available capacity for battery production.
Mike Dean, automotive equity research analyst at Bloomberg Intelligence, told Automotive Logistics that while the semiconductor supply constraints are now beginning to ease, battery supply to meet demand will be the next problem.
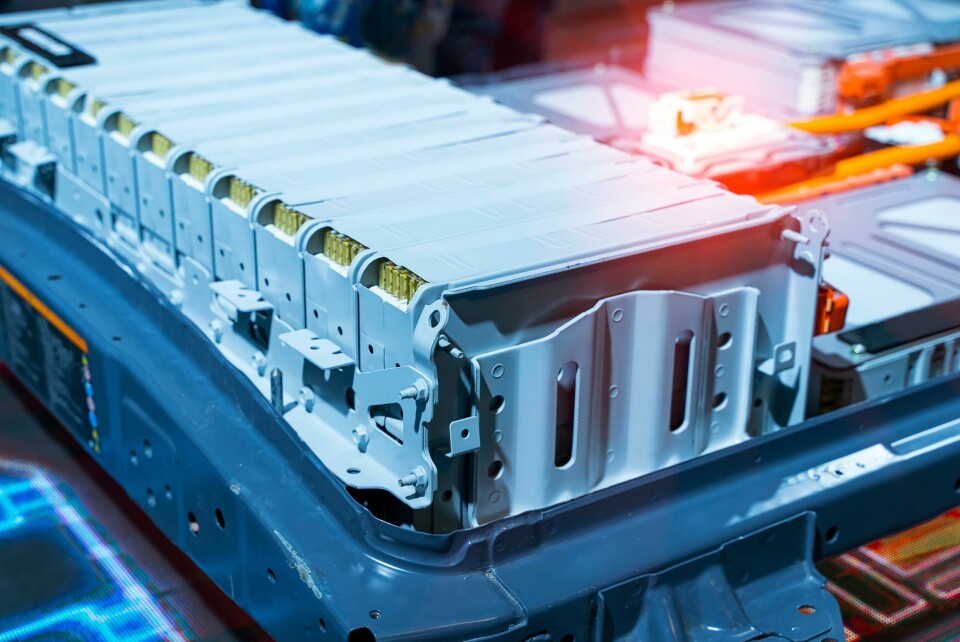
Growing demand from consumers along with government incentives are helping drive demand for EVs globally.
“Carmakers and their battery manufacturers are investing huge amounts on setting up new battery plants in Europe,” said Dean. “In the US, you’ve got President Biden’s Inflation Reduction Act (IRA), which is providing massive incentives to set up battery plants in North America, and there is a lot of talk about what is going to happen in the UK.”
Dean said more EV models are coming out from more brands over the next two or three years, supported by those incentives, adding that growth would start putting strain on battery production from 2025 as manufacturers struggled to meet demand. Given the short amount of time until then, he questioned whether it will be possible to build the infrastructure needed to solve the problem. “The question is, can all these factories be built on time, given there is so much demand,” he asked.
Lithium costs
On top of this, the lithium needed to make the batteries has risen in cost. “There has been a huge increase in the price of lithium recently,” he said, “and we don’t know whether there is enough lithium supply to satisfy the demand that we see coming through in 2024 or 2025, when all car companies have significant targets to sell more EVs globally.”
To tackle this, he said more vertical integration is needed within the industry. “Some companies are becoming more vertically integrated so we are seeing more parts in EVs being made in-house,” he said.
Along with inbound logistics problems, battery demand is set to cause issues in the second half of this year with finished vehicle logistics too. This will impact German automakers the most, because of their reliance on the Chinese market which is finally in post-pandemic recovery.
In recent years, German carmakers have earned a third of their profits from the Chinese market, but they are now falling behind in terms of exporting EVs to China. “For example, Volkswagen’s EV market share is 3% in China, compared to its ICE share which is about 15%,” Dean said. “There is concern that domestic brands are catching up, in terms of technology in EVs, but German car companies aren’t rolling out new EVs quickly enough to compete. Exports to China are going down, but the local production there is going up. That’s a trend we are seeing globally, exasperated by the shift to EV because of the huge weight of the batteries that they need.”