CATL powers ahead with a regional, sustainable supply chain strategy
With a new carbon-neutral gigafactory in China, and a plant set to start production this year in Germany, the Chinese battery cell producer is scaling its production and logistics to create secure and sustainable battery supply.
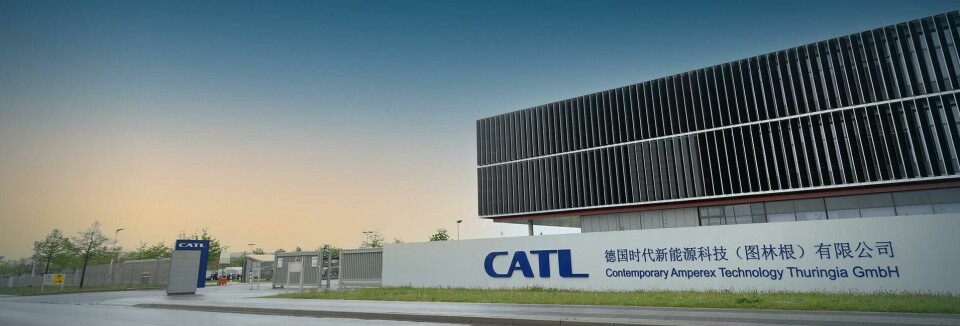
As OEMs increase electric vehicle production to keep up with surging demand, pressure continues to grow on lithium-ion battery manufacturing, including as a result of rising material prices and uncertainties over the Russia-Ukraine crisis. In response, carmakers and battery cell producers are investing to further develop new technology, vertically integrate their supply chains, as well as investing in more sustainable and regional production.
It is an industry in fast transition, and several key players are growing at a staggering pace. Among them is China’s Contemporary Amperex Technology Limited, or CATL, which is already one of the world’s leading lithium-ion battery cell manufacturing companies with supply agreements across many of the world’s major OEMs in China including BMW, Daimler, Renault, Nissan, Stellantis, Tesla and Volkswagen Group, as well as Chinese brands including GAC, Dongfeng and Geely.
CATL has ten battery gigafactories planned worldwide, mainly in China, however it is set to open a European battery plant this year in Erfurt, in the eastern state of Thuringia, Germany; it is also eying investments in North America. The company has been partnering further with upstream material providers to gain more control of its supply chain as well. It’s rolling out new designs as well for its batteries, including a cell-to-pack design that will provide greater energy density as well as manufacturing and supply chain advantages.
Charging ahead sustainably
CATL continues to invest significantly in China, both in production capacity and in sustainable manufacturing and logistics. It has recently launched a new plant in Yibin, Sichuan, which has been officially granted a zero carbon PAS 2060 certification. This certification is an important signal for the direction of travel for CATL specifically and for the wider industry, as the company aims to achieve this status across all its plants.
“The battery is a critical component of global efforts towards carbon neutrality; therefore, its zero-carbon production will further promote the sustainable development of the whole world,” a spokesperson for CATL told Automotive Logistics.
The wider context is that whilst electric vehicle ‘tailpipe’ emissions are zero, the energy used in manufacturing the EV, especially in the initial battery manufacture and sourcing, are considerably higher than for an equivalent ICE vehicle. To be genuinely ‘green’ and carbon neutral will require zero carbon manufacturing and significant changes to battery production and logistics.
From a battery perspective that mean eliminating emissions from sourcing and production of raw materials, processing, cell manufacturing, pack assembly, in-vehicle use and end of life recycling. “Zero carbon at the manufacturing process is just our first step towards our carbon neutrality goals,” admitted CATL, as significant efforts will be required to decarbonise the full lifecycle of batteries.
The underlying presumption around zero carbon manufacturing is that it costs more than a ‘conventional’ polluting plant to setup and is difficult to achieve. Over a longer period, however zero carbon plants will amortise costs thanks to the use of renewable energy. At CATL, the battery maker points to the use of both renewable energy, such as hydropower, at its Yibin plant, as well as leveraging innovations in its manufacturing and logistics processes.
“We managed to achieve zero carbon through green manufacturing, green energy management, green transportation and logistics,” said the CATL spokesperson. “Supported by a smart plant management system that features real-time date monitoring of equipment operation and advanced algorithms, we are able to calculate each equipment’s operating parameters with the lowest total energy consumption of the system and thus work out the best energy solution.”
Furthermore, electric and driverless logistics vehicles such as electric forklifts are widely used in production, according to the company.
Ultimately, CATL acknowledged that the “green premium” of zero-carbon factories would be increasingly visible as the global industry chain turns to low carbon development. “[That] will turn will give positive feedback to zero-carbon factories,” according to the company, suggesting such sustainability strategies will help to make such products more attractive to customers.
“We managed to achieve zero carbon through green manufacturing, green energy management, green transportation and logistics. Supported by a smart plant management system that features real-time date monitoring of equipment operation and advanced algorithms, we are able to calculate each equipment’s operating parameters with the lowest total energy consumption of the system and thus work out the best energy solution.”
CATL
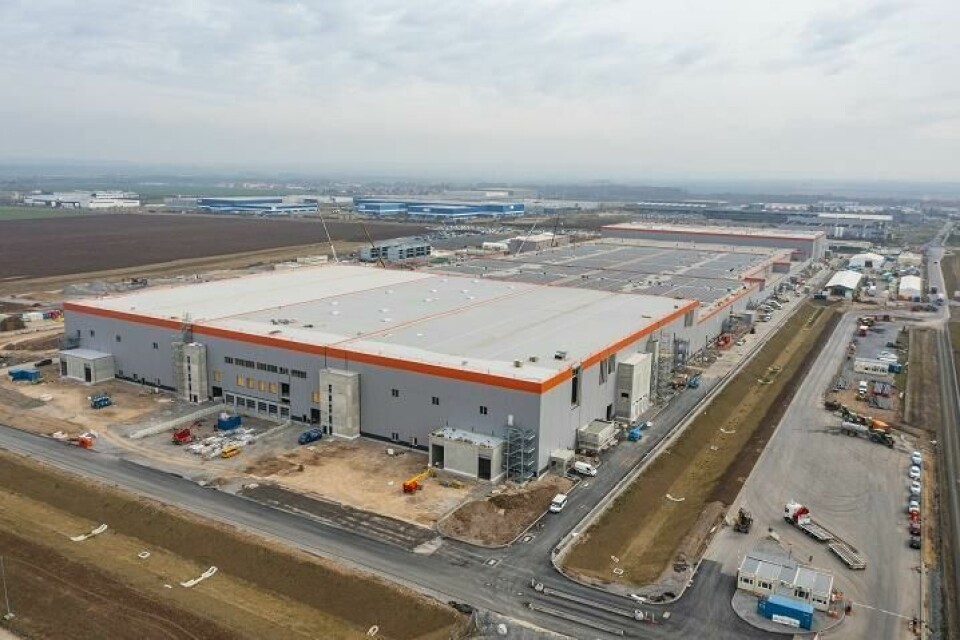
CATL goes giga in Germany
CATL is furthering this strategy in Europe with the opening of its plant in Erfurt, in the eastern state of Thuringia, Germany, which has just gained approval to build batteries and is expected to start production later in 2022. The plant will play a key role in expanding CATL’s global footprint and serving major European carmakers, including BMW, with which it has a significant supply agreement.
Tesla, a customer of CATL’s in China, has also just opened a plant for vehicles and batteries outside Berlin, and could become a future customer in Germany.
CATL is entering production in the European market at a time when regulators at the EU and member state level are focused on regionalising more of the battery value chain.
The EU’s forthcoming Battery Regulations are intended to drive the climate mitigation agenda and reach net zero targets across all manufacturing sectors, including requirements for sustainable materials and regional supply. The EU Parliament’s Environment Committee position on battery regulation went even further than the European Commission’s original proposal. While the Battery Regulations are likely to be negotiated further ahead of ratification by member states, they are likely to pass into law, establishing a set of rules across the entire battery product lifecycle for the first time.
As Europe winds down its legacy ICE production, the economic impact upon skilled automotive jobs could be substantial. The battery supply chain, on the other hand, offers huge growth potential for jobs and the economy. Europe cannot compete on price with imported batteries from Asia, however it can compete on regulation and environmental standards. By requiring all batteries sold into the EU to meet strict environmental standards, including rules of origin, European based battery manufacturers can compete on more of a level playing field.
The new battery regulations are likely to become a benchmark for the global battery industry, with CATL confirming that it would pursue carbon neutrality beyond the requirements of any region. “We are taking the initiative to achieve carbon neutrality for all of our products instead of trying to meet the requirements of certain customers or regions. “
Supply chain security
The push to create more sustainable, regional supply chains dovetails with other strategic priorities for OEMs and battery producers, namely around supply security and resilience. The Covid-19 pandemic, semiconductor shortages and Russia-Ukraine conflict have caused ongoing disruption to critical raw materials, components and supply routes. These capacity issues have contributed to a growing waiting list and lead times for the delivery of EVs.
Such constraints not only prevent OEMs from reaching their individual emission targets but they put the entire industry’s transition to electrification in jeopardy. CATL observed that a stable and orderly supply chain “is in the best interest of all players in the industry, and we hope that all players in the industry chain work together to promote a coordinated and steady development of the industry for the long-term goal of global carbon neutrality.”
In response, more EV carmakers and suppliers in Europe or North America are aiming to become less reliant on battery imports, which manufacturers source overwhelmingly from Asian cell suppliers. In Europe the import rate is as high as 90%, according to Recharge, the association of European battery manufacturers. (View the recent Automotive Evolution Livestream on battery production from AMS, a sister publication to Automotive Logistics.)
To ensure the security of its own supply chain, CATL points to measures including investing in upstream suppliers to secure supply, enhancing battery recycling and reuse of metals, as well as long-term supply agreements with upstream suppliers.
Localising the battery chain will help improve supply chain security and resilience. There is a move away from single sourcing of key components towards more flexible multi-sourcing, where viable, of those critical components. Transporting heavy battery modules is costly and further expands carbon footprints and increases risk as well, not least as shipping such batteries require special certifications and equipment thanks to status as dangerous goods.
The result will be more localisation of battery cell factories to where the pack integration and OEM vehicle assembly takes place.
Battery technology innovation
Along with manufacturing and sustainability, CATL is investing in new battery technologies. Battery capacity, energy density, weight, safety, reliability, price and charging performance are all areas under constant development. The major area that many industry observers are hoping for is technological advances that can bring battery prices down to below $100 per KWh, which is widely considered the point where EVs can achieve price parity with ICEs.
There are many technological approaches including driving down the costs through economies of scale, increased automation, refining battery chemistries and through cell-to-pack innovations. At CATL, innovation in battery cell and pack technology is a key area. The company has launched its third-generation cell-to-pack (CTP) – known as the Qilin Battery internally at the company – which aims to replace battery cell modules with a more efficient pack design.
“With the same chemical system and the same pack size, Qilin can deliver 13% more power than the 4680 battery,” said the company. “Meanwhile, CTP is also able to achieve cost-effectiveness by combining different chemical systems.”
The company is responding to ongoing range anxiety among consumers, as well as reactions to worries over battery fires, especially through improvements in thermal management of batteries.
“To address consumers’ range anxiety and safety concerns at the same time, we have been committed to the safety design of high energy density systems. Following the mass production of the 8-series products featuring no thermal propagation in 2020, the no thermal propagation technology with a higher energy density of 1,000km will also be mass-produced in 2023.”
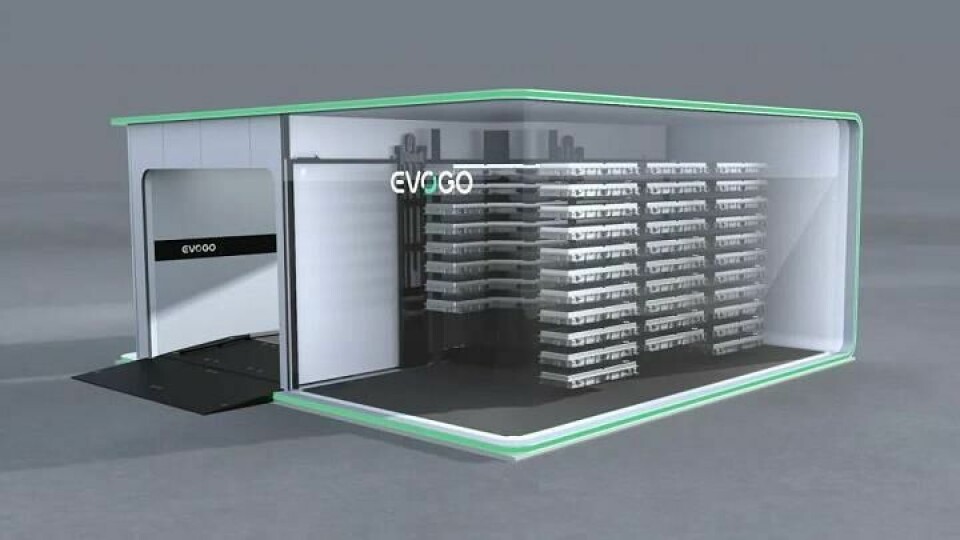
Battery swaps could help right size packs
To counter consumer concerns around EV range anxiety and charging times, some OEMs and battery companies are offering battery swapping, especially in China. Battery swapping not only removes the need to wait for charging but can protect residual values of the vehicle compared to when (fixed) battery performance deteriorates. Older EVs could also benefit from the latest advances in EV battery capacity, density and performance.
CATL has launched its EVOGO battery swap solution, which separates vehicle and batteries. According to the company, it helps customers to save costs on the initial purchase cost of electric vehicles, and to choose the number of battery blocks to swap according to actual needs of battery use.
This approach is interesting, as the conventional wisdom has been that everyone wants the largest highest capacity battery with the longest possible range. But that’s not always the case. If a consumer knows that they only have a 50km commute each day, and can easily charge daily, then carrying an unnecessarily large battery around makes the vehicle less efficient – and makes the initial purchase price prohibitive. The Honda-e, with just a 220km range, was developed with such a philosophy to reduce the weight, improve the driving performance and keep the cost down and make the price more affordable. Being able to select the size of battery capacity necessary for individual needs or a specific journey is a perfectly logical approach.
Vertical supply chains
Notable in CATL’s response to this situation is the move away from industry specialisation, which has been the norm in the automotive industry, towards deeper ‘vertical integration’ in its R&D, manufacturing and supply chain. Many battery manufacturers and OEMs have started developing long-term supply agreements or even partnerships with upstream raw material providers such as lithium, nickel, cobalt and manganese to ensure security of supply. Furthermore, they are making agreements with multiple suppliers to move away from single sourcing where feasible.
Tesla and VW are beginning to develop their own in-house battery cell production in part because of future supply chain concerns, with more large OEMs set to gradually follow suit as they increasingly see battery manufacturing and supply chain superiority as a competitive advantage. Such a shift will point to an interesting mix of collaboration and competition between OEMs and battery cell producers such as CATL. In the medium term, however, it’s clear that EV manufacturers will depend significantly on the technology, production and sustainability criteria of these battery experts.