An aftermarket network rebuilt for rapid response at BMW
An interview with Wolfgang Baumann, vice-president of parts logistics management and responsible for the global supply of service parts for the BMW Group
The expansion in sales and model variety for the BMW Group over the past two decades has led to significantly higher demand in the aftermarket, with increasing complexity in the service parts supply chain. Around the turn of the 21st century, for example, BMW and Mini brands had around 165,000 different part numbers. By 2005 – the year the company opened a new central parts warehouse in Dingolfing, in the German state of Bavaria – the number had reached 240,000.
Today, the carmaker manages around 400,000 part numbers, with demand rising particularly in Asia and North America. BMW Group typically stores part types for 15 years or more, so the demands for space and transport across many regions are evident.
Key to managing these changes has been the Dynamics Centre in Dingolfing, which has served as the receiving and storage hub for nearly the entire assortment of BMW parts. Together with a number of satellite facilities that make up the Zentrale Teilauslieferung (ZTA), or central distribution centre, these operations deliver to BMW’s regional distribution centres (RDCs) around the world.
It is a highly effective network, with service parts availability at more than 95% for dealer orders. In many markets, that means dealers receive parts by overnight delivery; in some countries, including Germany, the UK and parts of the US and China, dealers receive up to three deliveries per day.
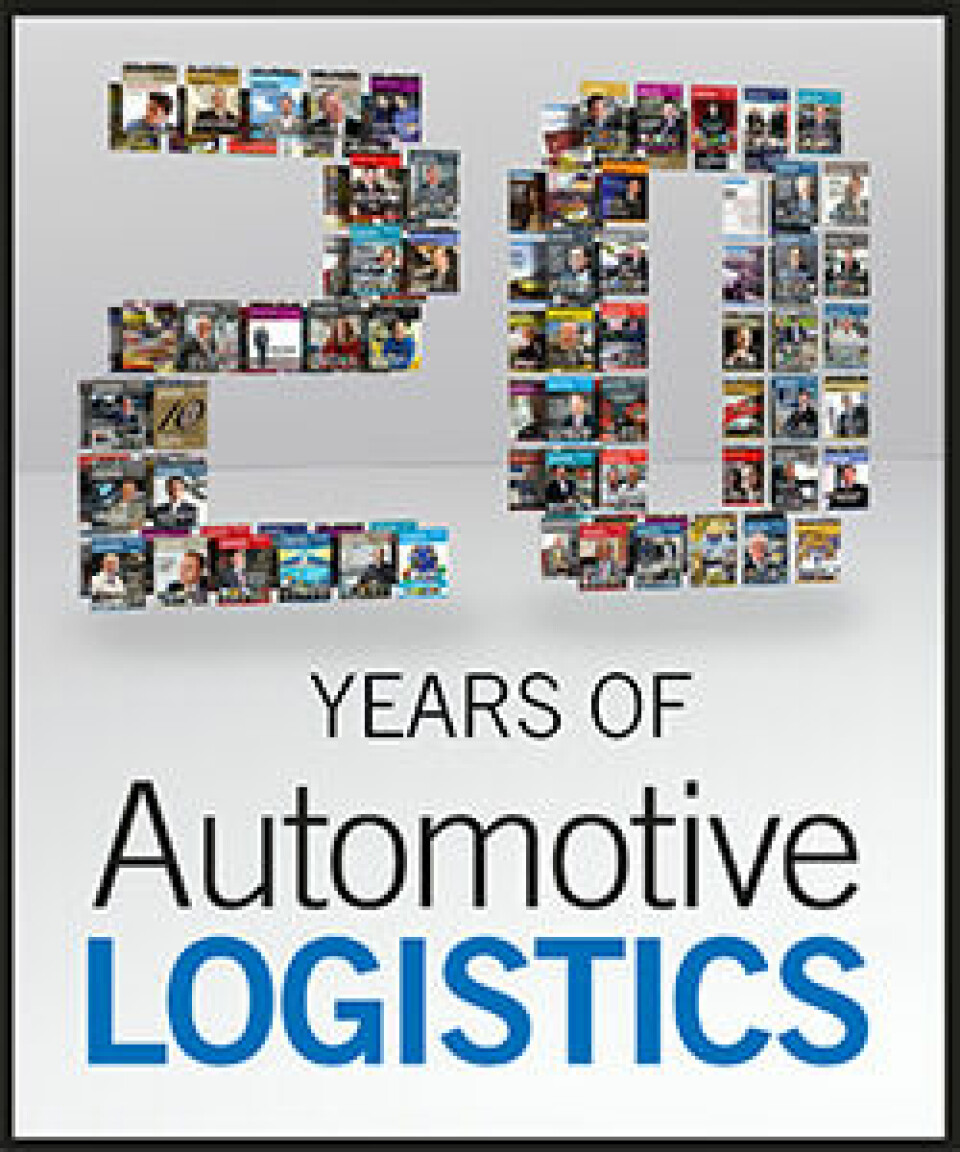
Click here to access more Automotive Logistics 20th anniversary features
Over the years, BMW has made upgrades to the ZTA and expanded its RDC network, notably in China. However, the strong growth, along with changes to supply and market geographies, left some facilities constrained and shipping routes redundant. As part numbers and storage requirements were growing at the Dynamics Centre, production at BMW’s adjacent manufacturing plant also rose substantially, with both facilities needing space to grow. Some inbound sourcing patterns have also required new approaches, including to avoid ‘parts tourism’, such as shipping North American or Chinese-built parts first to the ZTA in Germany, only for many to move back to RDCs in their country of origin.
In response, BMW’s aftermarket division has been restructuring and updating the ZTA and global RDC operations over the past two years, with a number of new facilities, increases in space and new strategies for parts distribution. Some warehouses have also been relocated closer to markets to reduce lead times and related costs.
According to Wolfgang Baumann, vice-president of parts logistics management and responsible for the global supply of service parts for the BMW Group, the objectives of the restructuring have been to create more customer-orientated supply chains, including reducing lead times where possible, as well as cutting costs and improving sustainability. For example, BMW has focused on reducing transport emissions per part transported, while new facilities have been built to low-energy standards, with higher levels of recycling and water reuse.
“Customer-focused logistics is closely linked to reducing delivery lead times, having more stable planning and providing higher parts availability and replenishment,” says Baumann, who joined BMW in 1985 and spent much of his career in sales planning before moving into service parts logistics in 2010. “We have set out to future-proof our operations.”
Improvements start at homeThis year, BMW and its logistics partners completed a significant update of the ZTA in Bavaria. “The changes were not only a matter of adding space but also of taking over more efficient locations,” says Baumann.

For example, the carmaker opened a new parts centre for the ZTA in Bruckberg, in Lower Bavaria, close to Munich airport, for rarely ordered parts. Bruckberg stores around two-thirds of total part numbers across contemporary and classic models, separating slow-movers from the Dynamics Centre in Dingolfing to better standardise systems, handling and storage. Baumann points out that the location close to the airport is also strategic; as low-demand parts, most orders are for individual customers, and around 90% are needed on an urgent basis, usually requiring air freight.
Another new ZTA facility is in Wallersdorf, which has a double function: around 49,000 sq.m are used for central goods receipt for suppliers of replacement parts and accessories, while a second, larger operation is for high-volume and fast-moving parts. While these items represent only around 3,500 part numbers, they are the most popular assortments, including wear-and-tear parts, oil filters and brake discs. This fast-moving parts operation covers around 178,000 sq.m and will soon include rail sidings to link into the carmaker’s train network in Germany.
Furthermore, BMW shifted an RDC operation out of the central warehouse to a 70,000 sq.m site in Kleinaitingen, close to Augsburg, which distributes parts to around 300 dealerships across southern Germany. According to Baumann, having both RDC and dealer distribution at the ZTA was something of a conflict because of the different picking, storage and IT requirements for each operation.
“Having them together was like a slaughterhouse having a sausage counter for passing customers,” he says. “Run separately, we can improve efficiency and reduce lead times.”
The new operations make up over 300,000 sq.m of new logistics space for ZTA-related operations, however the net expansion is less as some sites were closed or repurposed; for example, BMW transferred a 100,000 sq.m logistics centre at the Dynamics Centre to the Dingolfing plant for manufacturing activities.
Raising global coverageBeyond Bavaria, BMW is overhauling many RDC and warehouse locations. Over the past 18 months, Baumann or his colleagues have frequently donned hard hats or cut ribbons at ground-breaking and opening ceremonies, including in France, Slovakia, Russia, South Africa, Canada, Malaysia and Thailand. This past June, BMW opened a 57,000 sq.m new facility in Anseong, south of Seoul in South Korea. The RDC will help meet growing import demand in Korea and supply around 2m parts per year.
"Having [an RDC and dealer distribution facilities at the ZTA] was like a slaughterhouse having a sausage counter for passing customers. Run separately, we can improve efficiency and reduce lead times." - Wolfgang Baumann, BMW Group
Despite the global tour of construction sites and new warehouses, BMW has not expanded the total number of RDCs in its network by much, with total network locations increasing from 36 to 40 centres since 2005. There have been some new locations, including the carmaker’s fifth RDC in China, which opened last year in Shenyang close to its joint-venture plant with Brilliance, as well as Kleinaitingen in Bavaria. But in the last two years, there has been a net increase of only one RDC as other operations have been consolidated to improve transport links or create more sustainable operations. For example, BMW closed an RDC in Salzburg, which previously served the Austrian market, while it opened a new centre in Bratislava, Slovakia, that now covers Austria and eastern Europe.
In other cases, BMW has expanded RDCs or added new buildings. It is expanding its warehouse in Nazareth, Pennsylvania, which serves as lead parts distribution centre for other RDCs in the US. Earlier this year in Krefeld, in the north-west German state of North-Rhine Westphalia, BMW opened a new 31,500 sq.m greenfield warehouse in thetown of Rheinberg dedicated to storing large parts for distribution in the state and across Benelux. The warehouse complements an existing storage centre 30km away in Oppum, which is now dedicated to small parts such as windscreen wipers and screws.
While BMW’s total RDC network has stayed relatively constant, the carmaker has increased its customer reach through other facilities. For example, starting in 2010 in high-density markets in Germany, BMW opened smaller, local warehouses for fast-moving parts, known as dealer metro distribution centres (DMDCs), from which vans deliver same-day parts. It has since added DMDCs in markets including the UK, China and the US, where it has five covering half the market.
[mpu_ad]According to Baumann, while improvement of the network continues, there are no plans for new RDC or DMDC locations. However, the carmaker is considering the implications of the UK’s planned departure from the EU. For example, its RDC in Pineham, near Northampton, serves the entire country as well as the Republic of Ireland. If the UK leaves the European single market and customs union as its government says it will, it could be subject to tariffs and clearance checks with Ireland – which could potentially trigger a change in BMW’s parts distribution. “We’ll have to wait and see,” says Baumann.
Crossing continentsWhile much of BMW’s recent restructuring has focused on the ZTA and global RDCs, this year it also introduced a new type of facility to improve inbound supply. In late June, the carmaker opened the first phase of a ‘continental distribution centre’ (ConDC) in Spartanburg, South Carolina, close to its plant in Greer, to handle North America-sourced parts for regional distribution and eventually export, which will make it a unique service parts operation for BMW outside Germany.
The most obvious benefit of the US ConDC, as well as another planned later for Asia, will be to eliminate parts tourism for regional parts. According to Baumann, up to now all North American suppliers have shipped service parts to the ZTA in Dingolfing, meaning a share of parts must criss-cross the Atlantic Ocean before reaching one of BMW’s six RDCs in the US, or facilities in Canada and Mexico.
The ConDC is set to handle about 4,000 part numbers from 250 regional suppliers, a total expected to grow with rising X-series output in Greer and later Mexican production when BMW opens a new plant in San Luis Potosí. Suppliers that ship to the Greer plant will send a share of their shipments – often less than 1% – to the ConDC, where parts are inspected, repacked and sent to US RDCs. BMW expects to reduce inbound supplier lead times for US-sourced service parts by up to 80%. Repackaging parts at the centre rather than RDCs will also save space, time and labour.
Baumann points to further benefits from quality control operations, including verification of quantity and shipping errors, inspection for damage or faults, and packaging engineering. “By doing this quality control earlier, we pick up on errors much earlier than when we shipped the parts first to Germany, and we avoid shipping the fault onward,” he says. “Because we are handling a portion of parts that are shipped from the US to Dingolfing for global export, we are also able to identify problems before further shipments.”
For example, quality managers at the site recently discovered a fault on hoods (bonnets) that they were able to fix directly with the plant and its supplier. Operators at the ConDC also carry out a number of packaging processes, from applying protective film to windscreens to verifying and developing packaging materials and dunnage for new parts.

BMW is launching the Spartanburg ConDC in three phases. In phase one, with a floor space of 7,500 sq.m, it currently acts as a crossdock receiving American-sourced parts for US RDCs, without carrying inventory. In the second phase, set to take effect within the next two years, the ConDC will carry supplier inventory destined for the RDCs, and expand space in the warehouse to 11,000 sq.m. It will also increase coverage to include suppliers from Mexico and Canada.
In a third phase, which could see the operational area more than double, the ConDC will become the centralised export centre for North American-sourced service parts, shipping material to the ZTA in Germany, exchanging parts with the Asia ConDC and exporting globally. “That is our major objective, and what we have now is a precursor to that,” says Baumann. “The processes at the ConDC have been replicated from the ZTA.”
Baumann expects the third phase to begin by the end of the decade, by which time BMW will also have launched the Asia ConDC, the location of which is currently being decided. BMW already carries out some local supplier sourcing for Chinese spare parts at its RDC in Shanghai, but without the quality and inspection processes now done in Spartanburg. Parts sourced by the BMW Brilliance joint venture are already handled locally, but the Asia ConDC will be important for future parts exported globally.
BMW’s improvements have not only been about new facilities and locations. It has sought to improve IT and technology wherever possible at the ZTA, its RDCs and warehouses, including integrating all facilities into its SAP system, for example. Connecting the ConDC to its systems was a particularly complex collaboration across global and regional aftersales and logistics teams, with work still to be done for exports.
Next in the pipeline is a dealer inventory management system to support dealer ordering and stock management, which is planned for global rollout, says Baumann.
The carmaker is also interested in using technology to reduce errors and simplify operations where possible, such as in picking and packing parts in its warehouses for storage or dispatch. BMW has started testing scanner gloves for picking at the Dynamics Centre, for example, as well as trialling autonomous tugger trains along certain warehouse routes.

However, Baumann emphasises that customer focus is more important than high automation. In fact, equipment such as automated guided vehicles, robots or high-bay racking have played minimal roles in the recent warehouse restructuring, even if such technology is increasingly common in BMW’s production logistics. According to Thomas Kilimann, managing director at io-consultants, which has worked with BMW on redesigning the ZTA and RDCs, the carmaker has opted for a low level of automation in favour of flexibility, with more scope for human labour to manage volume peaks and troughs.
Baumann suggests worker-assisted technology is currently more beneficial to BMW’s services parts needs. He points to the end of quarters, bonus deadlines or other rush periods. “High-bay racking is hard to steer for speed. We have found more benefits by having more people to react, compared to fully autonomous operations,” he says.
That is not to say Baumann does not foresee significant changes in technology that will impact on logistics, particularly for vehicles themselves. For example, the telematics backbone in vehicles will increase data and communication, including on replacement parts. Likewise, BMW’s plans to increase its electric vehicle model range will introduce different parts and material to the supply chain, particularly around batteries. “We’re discussing the best way to maintain customer mobility with battery service,” he says.
But whether it is technological disruption or the political variety of change, Baumann is relaxed. His objective remains to serve customers, and that is what he believes the carmaker’s current investment in its service parts network reinforces. “BMW has been around for 100 years and I’m sure we will be here for another century,” he says. “For service parts, we’re supporting that with customer-driven logistics.”

According to Wolfgang Baumann, an important theme for BMW’s central parts supply is to increase rail transport between Europe and Asia, taking advantage of China’s ‘One Belt, One Road’ initiative aimed at strengthening trade links between China and other nations in Asia, Europe and Africa.
For nearly a decade, BMW has used rail services to move some production parts and kits from Germany to its joint-venture plant in Shenyang, in northern China. More recently, it has explored finished vehicle exports as well. Now, the mode is a growing focus for service parts.
“It’s a big advantage to move parts to China by train as it is more sustainable,” he says. “It reduces air freight, while turning a three-month ocean journey into three weeks. That would allow us to reduce safety stock in RDCs.”
While Baumann has sought to collaborate with production parts logistics on routes where possible, his team is also looking at destinations beyond BMW’s production plants. He reveals that BMW recently sent a container of aftermarket parts to South Korea by rail from Europe, which arrived “on time to the precise scheduled day”.
The carmaker’s new distribution centre near Seoul (pictured) will have a rail link ready by the time an express rail link between South Korea and Europe opens – due to be by 2019. Plans are also underway to trial shipments to Japan.