Planning BMW’s logistics in the factoryverse
Assembly and logistics planners at BMW’s Plant Spartanburg are designing layouts and operations in the virtual world, with real-time visibility of how changes would impact production and worker movements.
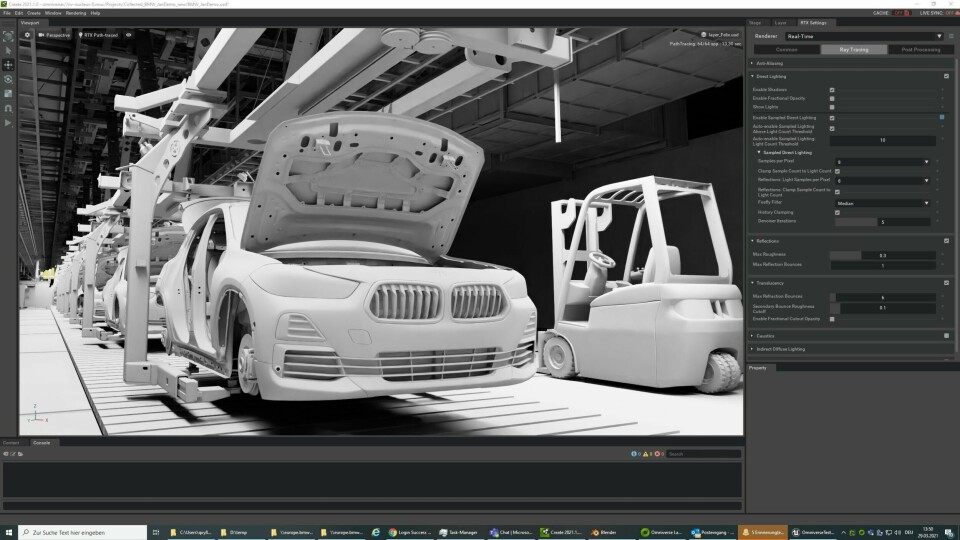
BMW planners can see the impact of layout and process changes in real time
‘Performing while transforming’ BMW's logistics in Spartanburg: Special series
-
‘Performing while transforming’ BMW's logistics in Spartanburg: Special series
-
Red Sofa Interview: Material control is BMW's next frontier for AI at Plant Spartanburg
-
Planning BMW’s logistics in the factoryverse
-
Material mission impossible: digital control of BMW’s inbound logistics
-
BMW rides the path of logistics automation
-
From South Carolina to the world of BMW, with love
In preparing BMW’s Spartanburg, South Carolina plant for new model and electric vehicle production, the carmaker’s logistics team will be able to design material flow and parts handling processes in a more dynamic way than ever before. BMW has worked with 3D scanning specialist NavVis to digitally scan its worldwide factories, capturing detailed data points across facilities. It has also partnered with computing and graphics specialist Nvidia to input this data into its Omniverse tool to create an entirely virtual landscape of plants, which uses AI to help plan and predict impacts from changes in layout or operations.
At the Spartanburg plant, BMW continues to update this virtual view even as it expands the factory. Omniverse is already accessible at a new training centre that BMW opened at the campus in late 2022, which is designed to train staff on new technologies and processes. Logistics and assembly planners can enter production halls across any global plant and walk through to inspect operations based on actual data points. “It’s basically like Google Street View inside of our facilities,” says John Mitchell, structural digital specialist at BMW Manufacturing Co.
The tool, which has been enhanced for BMW and is referred to internally as ‘Factoryverse’, allows planners to make virtual changes to layout and line structures within a facility. The programme creates animations based on the 3D scans and other information, including model, parts and equipment information. Assembly and logistics planners can test in real time how changes to structures will impact line-side delivery, worker movements and subassemblies.
According to Mitchell, the carmaker is integrating a programme that will help it plan the full material flow, including racking, tugger train and other line-side deliveries, as well as simulate worker actions such as walking distances between the rack and car.
“With AI built into the software, the movements are animated, which really helps us to understand how our people need to move. That’s important because we are not trying to hit a standing target, but one that moves at the pace of our takt times.”
John Mitchell, BMW Manufacturing
“The way we we’ve done it in the past would have been static, but now with the AI built into the software, the movements are animated, which really helps us to understand how our people need to move,” he says. “That’s important because we are not trying to hit a standing target, but one that moves at the pace of our takt times. It gives the ability to optimise and make adjustments that would reduce footsteps, which are changes we would otherwise have had to make later on the shop floor.”
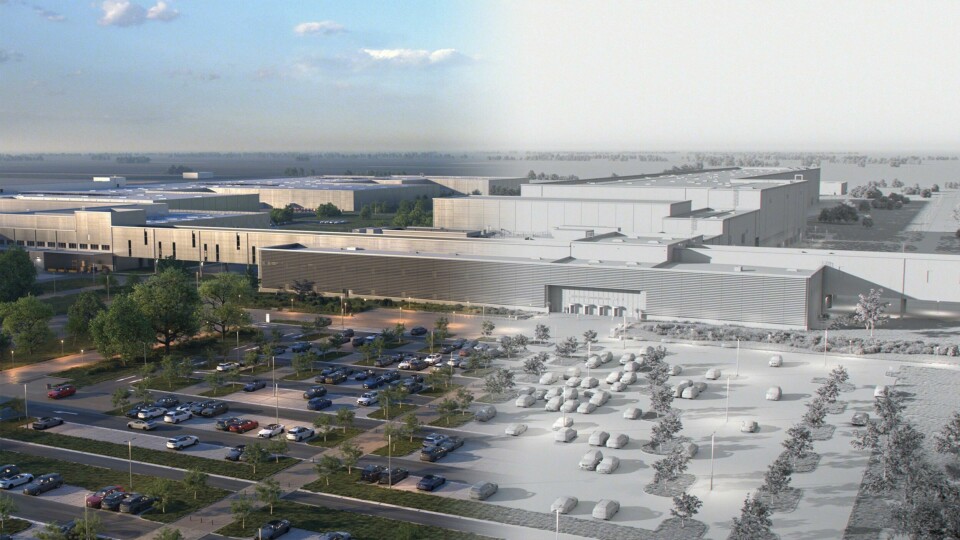
Plant Spartanburg has been fully digitised in the factoryverse, and planners are already assessing changes to Hall 52 for EV production
The factoryverse already includes a view of Hall 52, the assembly centre that BMW is expanding to build its new electric vehicle. The virtual view includes the planned dimensions of the assembly hall and expanded logistics centre, and planners have begun to add the new equipment to the digital twin, such as the overhead rail lines, carriers and pre-commissioning loops. It gives them the opportunity to check spacing and determine layouts to improve and even catch unexpected design issues.
“When we started to look at the simulation, we noticed that the rail line ran very close to the wall, which wouldn’t leave enough room for a carrier,” says Mitchell. “We were able to show this to the engineers so that they could redesign the loop before any of it was built.”
For Oliver Bilstein, vice-president of production control, logistics and material control at BMW Manufacturing Co, being able to plan this far in advance is a key advantage across facility planning, logistics and production design. “And with AI, it will give us the chance to make more improvements long before we start production,” he says.