VW Group brings North American facilities into digital production strategy
Technological advancement means software is now central to vehicle architecture and operation, but that same digital technology is now also being applied to the building of those vehicles at VW.
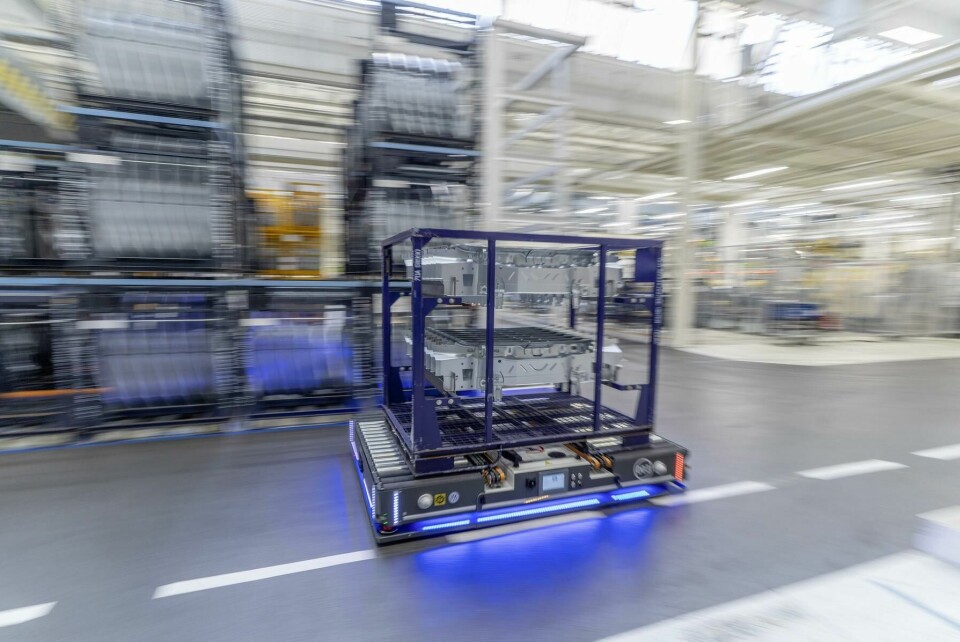
The German carmaker is rolling out digital manufacturing on a global scale and has recently pledged to invest $1 billion in the technology across its North American production network between now and 2025. It is the latest stage in a global transformation of its manufacturing process first announced with Amazon Web Services and Siemens in 2019.
Cloud-based industrial software, new intelligent robotics and artificial intelligence (AI) are set to be rolled out in factories across the region.
Johan de Nysschen, chief operating officer at VW Group of America, said digital technology will inevitably reshape the future landscape for manufacturing and North America is part of the eventual global digital network. The strategy is to not just digitalise core products but apply digital technology throughout the manufacturing process, including in production, design and development, as well as in supporting in-plant logistics.
Productivity and personnel gains
The explicit aim of this project is a 30% increase in productivity and to lay the foundations for digital manufacturing jobs in the future, promising to alleviate the more repetitive and labour-intensive tasks associated with vehicle making. Such a move will enable staff to focus on more valuable and personally enriching tasks, leading to an expansion in individual opportunities, and a more efficient and safer workplace overall, according to VW.
Since the initiative was first announced, the company said it wanted to connect North American plants in Chattanooga in the US, and Puebla and Silao, in Mexico. By the end of 2021, they will become the first Volkswagen plants outside Europe to be linked up to the Industrial Cloud. Eighteen plants in Europe have already been networked.
The Chattanooga site, in Tennessee, which currently manufactures the Volkswagen Atlas and Atlas Cross Sport SUV, alongside the Volkswagen Passat sedan, will become the nucleus for electric vehicle (EV) production in North America. In addition, Puebla builds the Tiguan, Jetta and upcoming Taos SUV, and the Silao plant makes engines for Volkswagen and Audi vehicles.
Industrial cloud
Volkswagen’s digitalisation strategy aims to connect those factories through a cloud-based industrial IT platform called the Industrial Cloud.
Susanne Lehmann, senior director production at Volkswagen de México, said the carmaker is developing tools to help manage manufacturing performance, control inventory and maintain visibility down a virtual pipeline to understand supplier performance and track production.
The scope of the Industrial Cloud includes VW’s suppliers, something the company said distinguishes it from competitors in both approach and scale. It is designed to encompass the entire worldwide supply chain involving 1,500 suppliers and partner companies at around 30,000 locations.
According to de Nysschen, those suppliers will have full transparency of customer needs and demands, which in turn lowers costs because suppliers can plan for capacity, invest in production equipment, and synchronise operations to meet supply and demand in real time.
The cloud technology enables a level of collaboration not hitherto available. It bridges all stages of model development, from a fully virtual design process to predictive pricing and purchasing, as well as being applied to advanced manufacturing and logistics planning. Digitalisation of processes will be a “game-changer” in how Volkswagen conducts business worldwide, said de Nysschen.
The development of apps is central to this process, according to the carmaker. The apps are available at a company-specific app store to all Volkswagen plants for downloading and implementation. This helps the company streamline the internal production process as well as improve transparency with partners, said the company.