Meeting increasing demand for EVs in Europe depends on better battery supply
The increase in sales of low-emission vehicles in Europe has been a silver lining on an otherwise dark year for the automotive industry but there are still bottlenecks to tackle in the lithium battery chain if supply is to keep up with demand, writes Daniel Harrison
Carmakers are investing colossal sums of money into low and zero-emission powertrain technologies. Even before the coronavirus crisis infected the finances of most manufacturers the survival of many of them hinged upon a return on investment and a successful transition to electrification over the coming years.
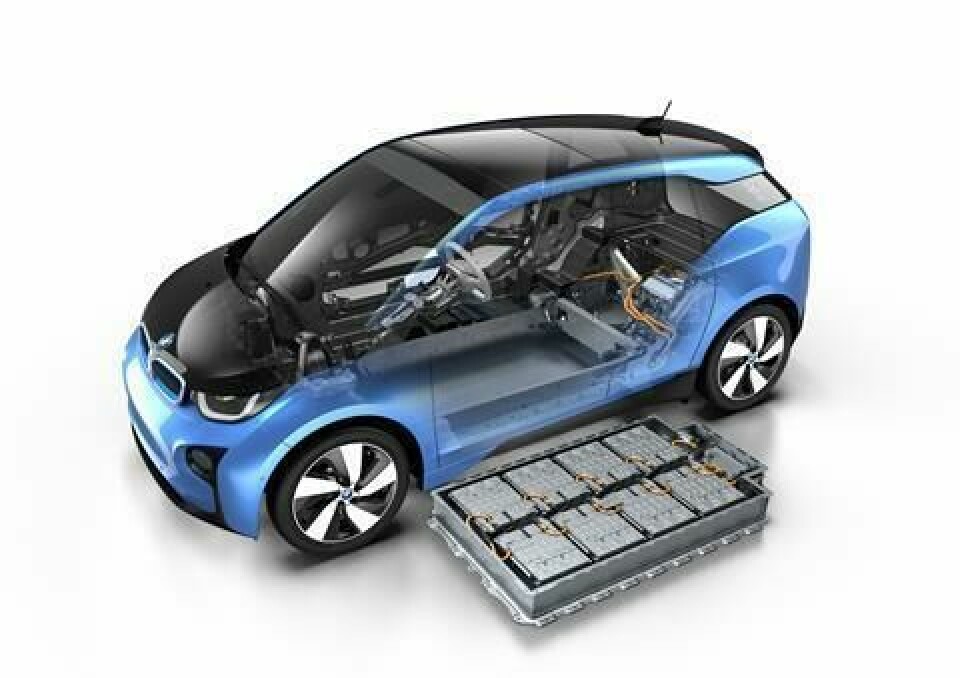
It has certainly been welcome news then that sales of low-emission vehicles have been among the few bright spots in a very challenging vehicle market in 2020. In Europe, in fact, the sales of electrically charged vehicles (ECVs), which include electric vehicles (EVs) and plug-in hybrid electric vehicles (PHEVs), jumped by over 40% year-on-year compared to the same period in 2019, whereas overall vehicle sales fell drastically by 38%.
However, while this is certainly good news for OEMs – and follows several years of high growth rates for EVs – the rise also brings challenges in the fast-developing lithium-ion battery supply chain. The supply of batteries has already struggled to keep up with the pace of change in recent years, with examples of OEMs having to stop or slow down production.
These bottlenecks have partly contributed to delays and longer waiting times for would-be EV and PHEV customers. Our research shows that in Europe, EVs typically take an average of 12 weeks to be delivered compared to around seven weeks for new factory orders of internal combustion engine (ICE) vehicles. In some cases, average wait times have stretched to 36 weeks, indicating a growing mismatch between demand and supply.
This is a clear indication of where effective supply chains are essential and why automotive manufacturers should consider them as a competitive advantage. The good news is that many OEMs are investing in and diversifying their production, sourcing and shipping of key EV components and products.
Accelerating the charge for EVs
The resilience of EV and PHEV sales amidst the crisis has been the result of multiple factors. A growing product offensive, spurred by stricter regulations, along with more powerful batteries have resulted in better technology and more choice for consumers.
Even before Covid-19, many governments had been offering a variety of tax incentives and premiums to purchase low-emission vehicles, along with measures to discourage higher-polluting vehicles such as low-emission and congestion zones in urban areas.
Now, of course, many governments have introduced further stimulus measures to encourage vehicle sales. In Europe, many national governments have tied such packages to purchases of low-emission vehicles, notably France, Spain, Germany and Italy. Carmakers have also been pushing an array of incentives and offers on price, financing and on products such as home charging equipment.
The result has been to bring down EV prices considerably, especially in price segments below €40,000 ($47,000), for which European incentives are generally higher.
Other impacts from the crisis might also be accelerating the shift to EVs. Consumer reluctance to use public transport especially in cities has encouraged more personal mobility, which may ultimately benefit low emission vehicles. The crisis may have even made customers more environmentally conscious.
These factors have played a role in making a vehicle such as the all-electric Renault Zoe a bestseller in 2020. Furthermore, the third generation Zoe was upgraded in 2019 with a new 52KwH battery and crucially this brings the range up to 245 miles (WLTP), which is comparable with the entry level Tesla Model 3. However, the Renault Zoe is £13,000 ($16,950) cheaper that the Tesla Model 3 and is now outselling the Tesla Model 3 in Europe.
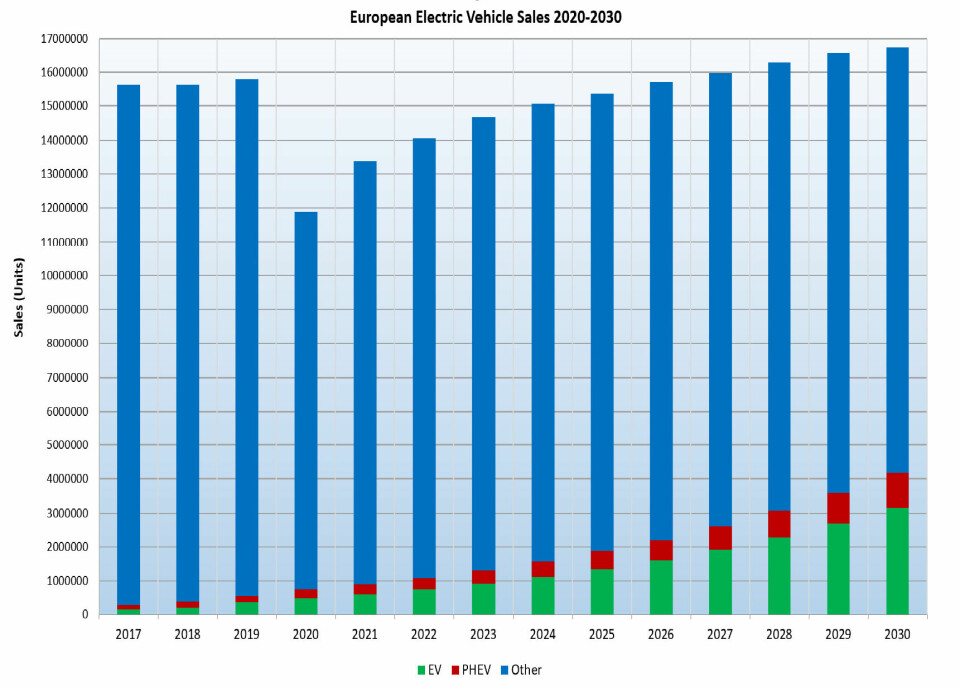
Sales forecast includes the EU, UK and EFTA.
Battery supply challenges
A key issue in sustaining this growth and maintaining market share, however, will be the battery supply chain. Even pre-crisis, battery supply chains were already struggling to meet demand. Earlier this year, Audi reported problems with its battery supply from LG Chem, while Mercedes-Benz were also reportedly experiencing problems.
Post-Covid, Tesla has reported battery shortages following long lockdowns. In fact, Tesla’s delay in restarting production is likely a contributing factor to lower sales of the Model 3.
Other production issues are also set to delay other electrified models. The new Nissan Qashqai, which is set to have a PHEV version, will see production and launch pushed back to next year at its plant in Sunderland, UK. Production and launch of the electric Jaguar XJ has also been delayed as a result of the crisis.
The supply chains for lithium-ion batteries and EVs are long and complicated. From the basic raw materials to assembled battery packs and finished vehicles there are unique dynamics and issues specific to region, and there are different companies specialising in each step of the value chain. As with any supply chain, EV battery supply is often only as strong as its weakest link.
For example, the raw minerals of cobalt, nickel, manganese and lithium are largely produced in very specific locations around the world and often subject to erratic supplies, not least as a result of political instability in those regions. Cobalt supply from the Democratic Republic of Congo is a good example. Cell manufacturers are reporting increasing shortages of raw materials, which is affecting supply.
Further downstream, the necessary anodes and cathodes are produced by a handful of specialist companies mainly in Asia.
Battery cell manufacture is also still dominated by the major Asian players in South Korea (including LG Chem and SK Innovation), China (BYD, CATL), and Japan (Panasonic). These leading cell manufacturers still make the majority of battery cells in Asia, which are then exported to OEMs for assembly into modules and packs before they are fitted onto OEM production line.
Regulation and localisation
This geography is further complicated by a variety of regulations around the transport and storage of lithium-ion batteries, which are classified as a dangerous good. This can lead to further challenges and delays in shipping; for example, restrictions on air cargo for dangerous goods makes it more difficult and expensive for manufacturers to expedite such parts at short notice.
That is why investment in regional battery production continues to grow, even as OEMs look to reduce cost and capital costs as a result of the crisis.
At low EV volumes, it has made economic sense to import battery cells rather than invest in local plants. As volumes grow, however, there has already been increasing localisation of battery plants in Europe and North America in an effort to make OEMs less reliant on battery cells sourced from Asia. For example, LG Chem has a new plant in Poland, CATL a new plant plant in Germany and Northvolt will build a joint venture plant with VW in Germany. SK Innovation is also building a second US plant in the state of Georgia. A host of other new battery players are also adding capacity.
There is also an increasing trend for OEMs to invest in battery plant joint ventures with cell suppliers, thus reducing investment costs and providing more stable supply of cells to OEMs. Tesla and Panasonic started with this model early on with the first gigafactory in Nevada. In Europe, Volkswagen’s partnership with Northvolt, and PSA Group’s JV with Saft – a division of French energy giant Total – are further examples. GM has partnered with LG Chem to build a large JV battery factory in Ohio.
Smaller players, meanwhile, such as startup EV manufacturer Fisker, are looking to form consortiums to achieve the same buying power for batteries as larger OEMs.
These are all important developments. However, building new battery plants can take three years or longer, and investment cycles cannot easily respond quickly to sudden increases in battery demand.
Battery components and raw materials, meanwhile, are also still likely to come from far-flung locations, indicating further bottlenecks will still be possible upstream.
Shift to multi-sourcing
This global supply volatility is why more OEMs are mitigating against battery supply bottlenecks by moving towards multi-sourcing of battery cells along with ‘regionalising’ their suppliers.
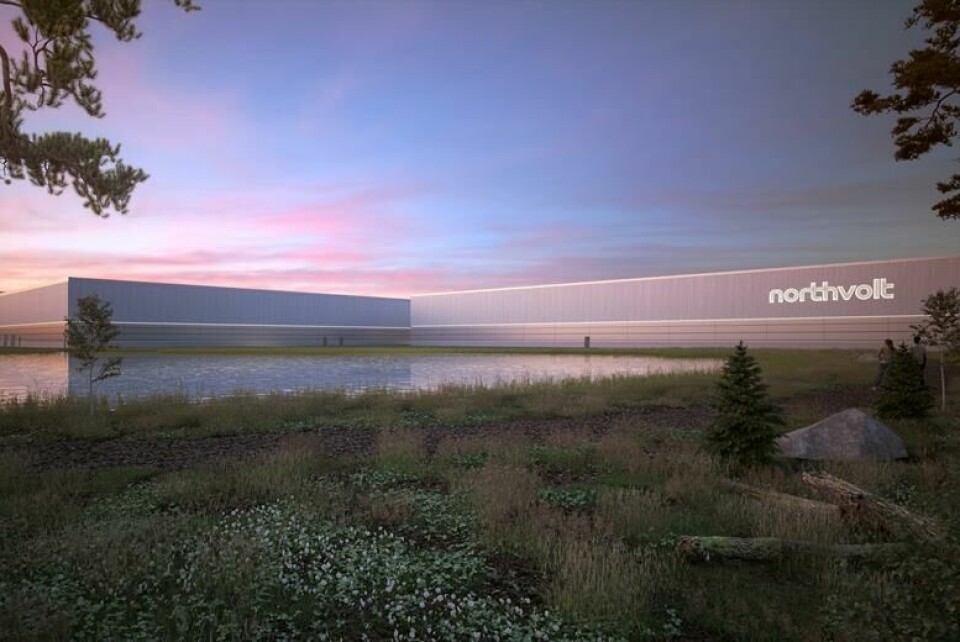
For example, Tesla used to use Panasonic battery cells exclusively, but now also uses LG Chem and CATL.
VW has expanded from just using Samsung SDI to sourcing from LG Chem, SKI and CATL across different regions. Likewise, Groupe PSA has shifted from using just LG Chem to also using CATL along with its joint venture with Total/Saft.
As a result of these developments, we expect to see huge growth and rapid change in the delivery routes for battery supply, both as more local sourcing of batteries is established and as OEMs supplement supply with additional sources.
The increasing complexity in trade will not only be for battery components. In some cases, manufacturers are looking to use global capacity to serve demand and bring EVs to market faster. A notable example this year is BMW using its joint venture production in China to build and export the new iX3 electric SUV across global markets, including back to Europe. While OEM expansion of EV capacity in China, Europe and North America is increasingly to supply regional markets, we expect increasing flows of vehicles based on demand.
The electrified future may not quite be here yet. But the Covid crisis is accelerating the change in many areas, with the supply chain set to see continuing transformation.
Daniel Harrison is automotive analyst at Automotive from Ultima Media. Join his presentation at Automotive Logistics and Supply Chain Live on Tuesday September 15th.