Europe’s EV forecast has dropped – and here’s what it means for the supply chain
As Europe’s EV transition hits regulatory and market speedbumps, automakers face tough decisions on where and how to adapt operations for the EV supply chain. From battery traceability to shifting trade flows and affordability pressures, supply chain strategies are being re-engineered in real-time.
Europe’s EV supply chain is in full recalibration. Amid regulatory shifts, global trade tensions and evolving consumer demand, the region’s automotive leaders are facing some difficult strategic choices.
Building on the themes of localisation and the strategic repositioning of Europe’s EV manufacturing base explored in Automotive Logistics’ previous analysis, this follow-up draws on insights from the 2025 Automotive Logistics & Supply Chain Europe conference and takes a deeper look at one of the most critical and dynamic areas underpinning the transformation: battery materials and the supply chains that support them.
From pressure to pause
In early 2025, the European Commission’s Strategic Dialogue proposed easing the timeline for CO2 fleet compliance. The revised framework allows automotive manufacturers to average emissions targets over three years – 93.6g/km for passenger cars and 153.9g/km for vans – rather than meeting annual thresholds. This policy shift provides some short-term breathing space but introduces fresh complexity for long-term planning.
On May 6, the European Parliament voted to fast-track the proposal, aiming to accelerate its adoption and offer regulatory certainty to manufacturers. However, the proposal still requires formal approval from EU member states before it can take effect.
For automotive supply chains, this potential policy pivot means adjusting launch schedules, rethinking volume forecasts and aligning logistics capacity with a more gradual – but still inevitable – transition to BEVs.
As Matthias Schmidt, European automotive analyst at Schmidt Automotive Research, noted at the 2025 Automotive Logistics & Supply Chain Europe conference: “The European market is heavily built on a regulatory framework… and the recent dilution gives OEMs an opening to prioritise higher-margin ICE models in the short term.”
Schmidt Automotive Research shared its BEV market forecast for Western Europe – down from 22.2% to 21.5% – in its January edition of the “European electric car market intelligence report 2025”, following the European Commission’s regulatory proposal.
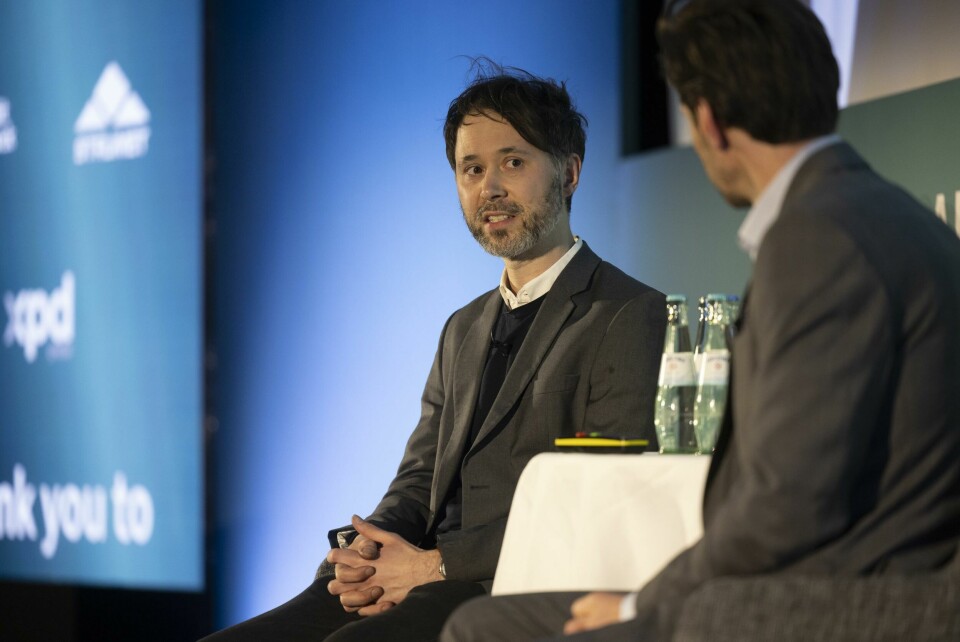
Commenting on the EU’s revised CO2 compliance rules, Schmidt said: “The European market is heavily built on a regulatory framework… and the recent dilution gives OEMs an opening to prioritise higher-margin ICE models in the short term.”
For many automotive logistics planners, a dip in future BEV volumes may translate to temporarily reduced demand for specialist battery transport and EV-specific infrastructure, however, this delay does not eliminate long-term pressure. OEMs remain tied to investment and product development cycles that were anchored in earlier, more stringent regulatory timelines. For example, the Volkswagen Group is delivering BEVs based on 2024 orders, maintaining 18-20% BEV mixes that help reduce its fleet-wide CO2 emissions, according to Schmidt Automotive Research.
Even as near-term volumes fluctuate, the flow of batteries, charging infrastructure and regulatory documentation is expected to grow. Electrification strategies remain active across major OEMs in Europe, including BMW, VW, Stellantis and Changan Automobile, underscoring the continued need for supply chain readiness.
As Henner Lehne, vice-president of global vehicle forecasting, automotive, at S&P Global Mobility, highlighted at the same conference: “It’s not just about the vehicle. The vehicles are coming – but the infrastructure, supply chain costs and regulatory frameworks are the big blockers and need to evolve in parallel.”
Market movement
Proposals of regulatory easing has coincided with a notable shift in BEV market dynamics. In January 2025, Tesla’s share of Western Europe’s BEV segment fell to 14.4%, down from a year earlier, following a 46% drop in year-on-year volumes, according to the report from Schmidt Automotive Research. The report attributes this decline to several compounding factors including the “facelift” of the Model Y delaying consumer purchases, the loss of environmental subsidies – particularly in Germany – and ongoing reputational challenges linked to Tesla’s leadership.
Meanwhile, the Volkswagen Group strengthened its position, capturing 28% of the region’s BEV market.
Beyond the headline players, Chinese OEMs are responding to regulatory conditions with an adaptive playbook. Europe, long a net exporter of vehicles, is becoming a net importer, driven by inbound flows of BEVs and hybrids from Chinese brands like BYD and MG. Analyst Schmidt highlighted this reversal: “We’re seeing Chinese manufacturers delivering more non-BEVs than BEVs across Europe… It’s a tariff workaround, but it’s also about flexibility.”
In response to EU anti-subsidy tariffs targeting Chinese-made BEVs, some brands have pivoted to hybrid or ICE models to preserve market access. The UK, which opted not to mirror EU tariffs post-Brexit, has emerged as a preferential entry point – though right-hand-drive production remains a constraint.
Lehne offered a long-term view of Chinese manufacturers’ positioning: “The Chinese… don’t have a two-year strategy, it’s a ten-year strategy. Step-by-step, they’ll push into Europe with smart, affordable models.”
This signals a sustained challenge for European OEMs – not just in pricing, but in product design, speed to market and digital integration. This evolving competition landscape will also require careful balancing of inventory forecasting, capacity management and sourcing strategy. Diversified portfolios and regionally adaptive logistics will be essential in staying resilient amid these unpredictable flows.
Material matters
The EUs updated battery regulations are also setting a new bar for traceability, material sourcing, recycling and transport. As highlighted by Aleksej Krükov, general manager of overseas service EMEA at CATL, during the Automotive Logistics & Supply Chain Europe 2025 conference, automotive battery regulatory framework is one of the most complex in the world: “Battery waste, extended producer responsibility, traceability, recycled content… it’s not just about transport; it’s about designing end-to-end systems.”
These measures aim to reduce reliance on imported raw materials and establish a circular value chain within Europe. For automotive logistics operators, this means managing not only the forward flow of components but also complex reverse logistics for battery collection, storage and recycling.
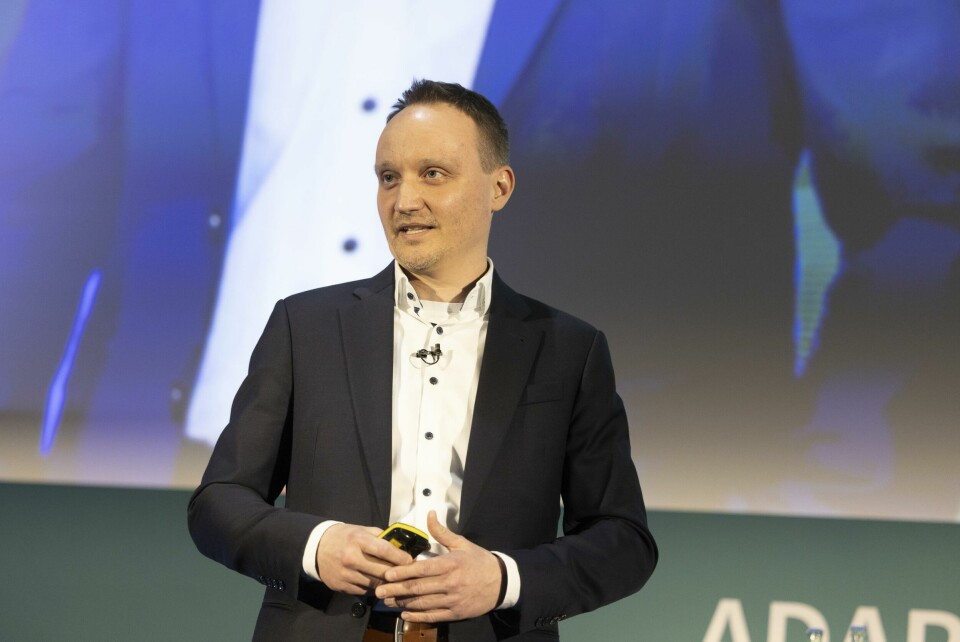
Emphasising the EU’s evolving battery regulations, Krükov said: ’It’s not just about transport – it’s about designing end-to-end systems that handle everything from sourcing to recycling.”
Cross-border transport within the EU poses an additional challenge. As Krükov noted, varying national regulations for handling dangerous goods make it especially difficult to move damaged or end-of-life batteries – raising both administrative and safety concerns.
“Transporting new batteries is already regulated, but moving defective or end-of-life batteries increases the complexity to the highest level,” he said.
Packaging is another overlooked but critical issue in the battery supply chain. Philip Bittermann, editor-in-chief of Neue Verpackung – sister publication to Automotive Logistics – drew attention to the waste and inefficiencies in traditional materials during a dedicated packaging workshop at the conference.
“Just one part [of the packaging] can generate 20-30% of a vehicle’s total packaging waste,” Bittermann explained. “Expanded polystyrene is bulky and non-recyclable. Switching to polypropylene means you can reuse the packaging.”
This insight underscores a broader shift toward modular, reusable packaging solutions – particularly for high-density items like lithium-ion cells. Highlighted in the workshop, OEMs are now deploying standardised outer battery packs capable of carrying over 400kg, reducing packaging waste while improving handling efficiency across modes.
Affordability and demand
Affordability of BEVs remains a core tension. Lehne observed that while battery costs are dropping (LFP packs now under $100/kWh), infrastructure and financing remain major barriers: “Interest rates haven’t dropped as expected. Financing a car is still expensive.”
To soften that impact, VW has proposed socially targeted leasing programmes to make EVs accessible to lower-income households. However, this sits against a backdrop of OEMs also extending ICE line-ups to preserve margins in the face of softening BEV demand.
In parallel, Chinese OEMs continue to gain ground with lower-cost, feature-rich BEV – particularly in cost-sensitive markets. These competitive dynamics are pushing both Western and Chinese automakers to reevaluate their sourcing and localisation strategies. Schmidt Automotive Research projects that Chinese brands could capture up to 12% of Western Europe’s BEV market by 2027, aided by localisation efforts such as BYD’s plant in Hungary and Geely’s planned European assembly expansion.
This has led analysts to more broadly suggest that for automotive supply chain and logistics leaders, the implications are significant. Affordability pressure is likely to increase demand for small-segment BEVs, many of which may be produced in low-cost European locations or imported via tariff-optimised routes. Logistics strategies must therefore anticipate a growing mix of intra-European transport, more frequent smaller-batch vehicle flows, and the need for highly cost-efficient battery and component distribution models.
Moreover, affordability is influencing investment in charging infrastructure. Slower EV adoption can delay or redistribute charging network rollout – altering installation logistics, parts delivery patterns, and the timing of support services across different regions.
Regulatory policy remains in flux for Europe’s battery supply chain. The midterm review of the EU’s 2030 and 2035 CO2 targets has been brought forward to 2025. Data gathered during 2024 and early this year will influence not just vehicle development strategies but the infrastructure planning and logistics investment timelines that support them.